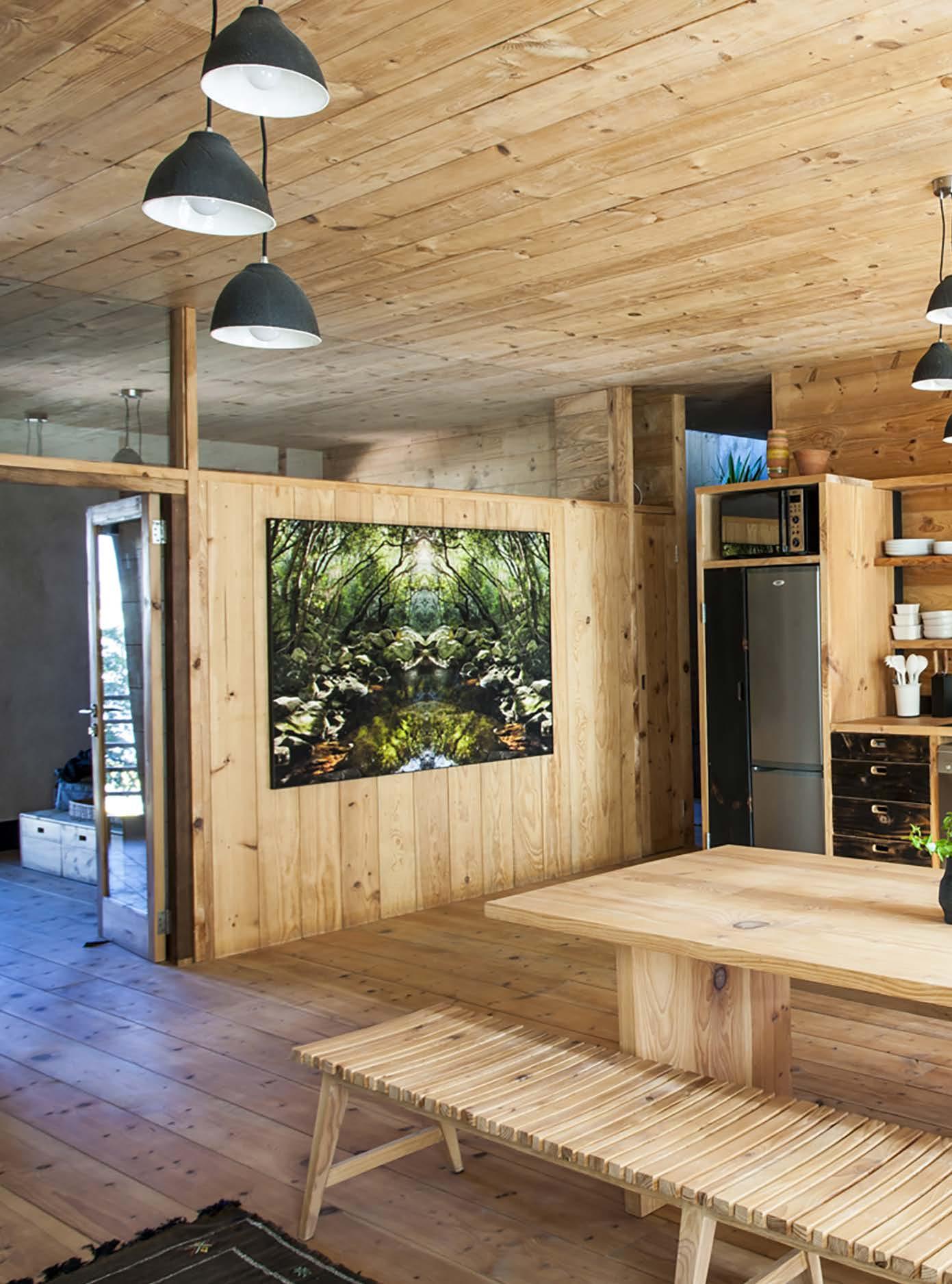
10 minute read
OPINION PIECE HEMP IS WHERE THE HEART IS
HEMP
IS WHERE THE HOME IS
Advertisement
It is estimated that the hemp industry will create 25 000 new jobs and be worth an estimated R10-billion by 2025. +Impact speaks to Wolf from Wolf & Wolf Architects about its hemp house built in the Bo-Kaap and how hemp has the potential to change the face of the building industry.
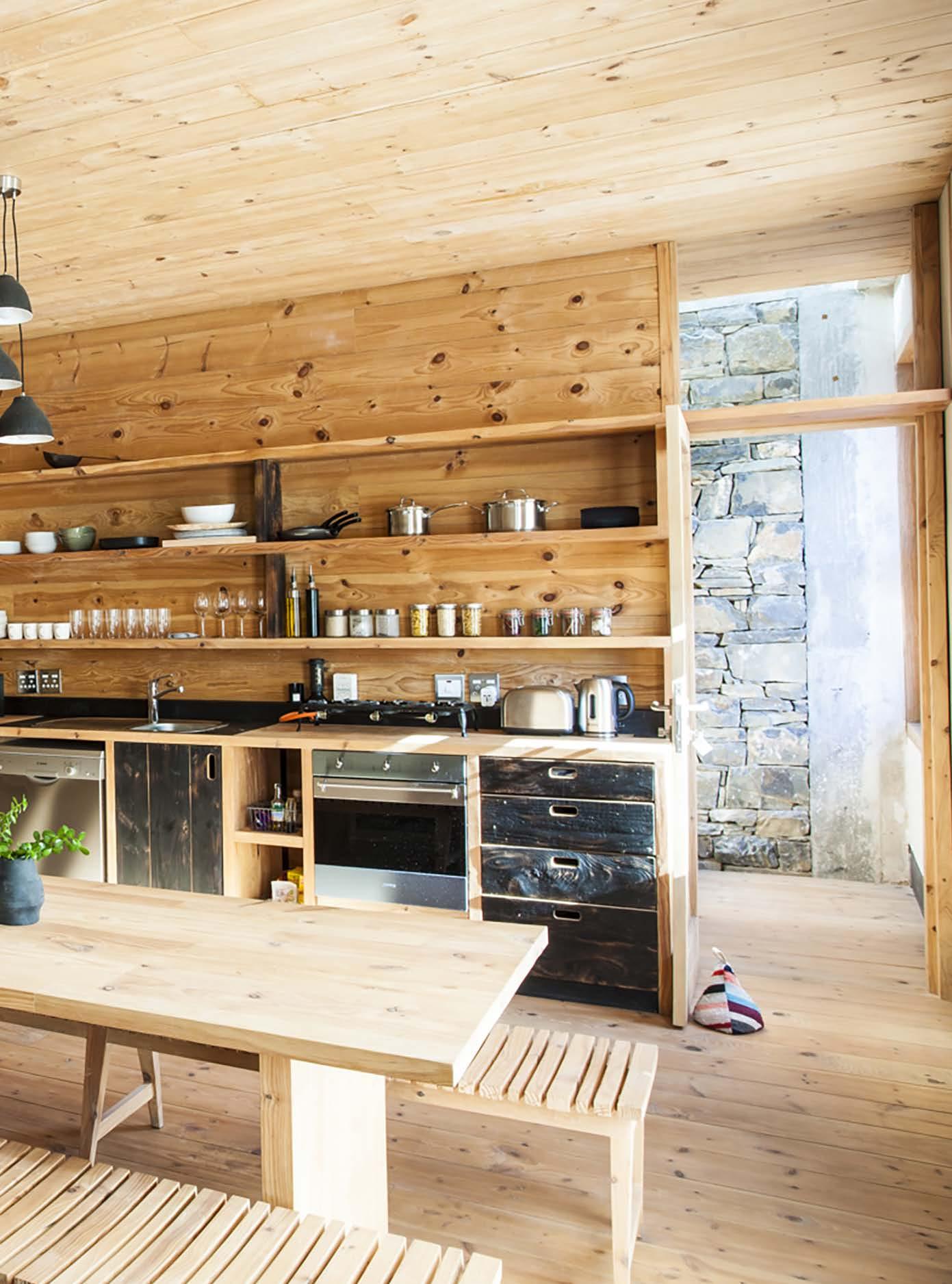
WORDS Robbie Stammers
Wolf of Wolf and Wolf Architects has designed and facilitated almost all of the Western Cape’s hemp building projects to date, starting with The House that Hemp Built in Noordhoek that was built for South Africa’s foremost hemp expert, Tony Budden, from Hemporium, in 2011.
Following this project was the hemp house in the BoKaap. The double-story Bo-Kaap hemp house was built using a timber and concrete structure with Hempcrete infill. Over 50% of the hemp was sourced locally from hemp cultivation research projects. This work forms an important landmark on a journey towards refining the combined use of timber and industrial hemp.
Set within the culturally and historically sensitive Bo-Kaap, this project explores the use of timber, clay and lime plasters focusing on energy efficiency and the reduction of the carbon footprint of the building. The home has a built-in water catchment, a bio-digester in the basement and a green house on the roof with the potential for an aquaponic system. The design succeeds in addressing the street in a historically appropriate way while offering a contemporary interior space.
“We pride ourselves on being strong advocates for the hemp industry in South Africa and are leaders in hemp construction nationally. Having built and been involved in several hemp-built homes and, more recently, larger building projects, we understand the benefits and limitations of this material. The benefits to personal and environmental health are substantial,” explains Wolf.
GREEN BUILDING
Hempcrete is an energy-efficient, low-impact, watersmart building material that offers a better carbon footprint than other home building materials. An alternative to cement blocks, which are very energyintensive, hempcrete can be an integral part of home building, using just enough energy to keep its occupants warm in the winter and cool in the summer.
Hempcrete is made from hemp mixed with a formulated lime binder and water; it does not require heat to produce. This material can be formed to fit between the studs of a house as hempcrete or as bricks, blocks or panels set between a timber, steel or concrete structural system. Because it is less dense than regular clay or cement blocks, it reduces the load on the structure of the building.
Hemp can also be used like stucco to protect the outside walls of new and existing homes from moisture.
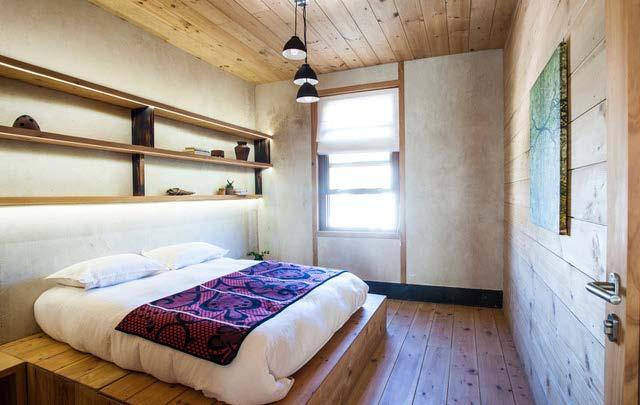
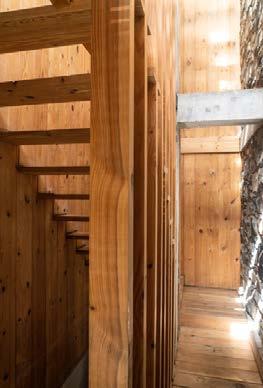
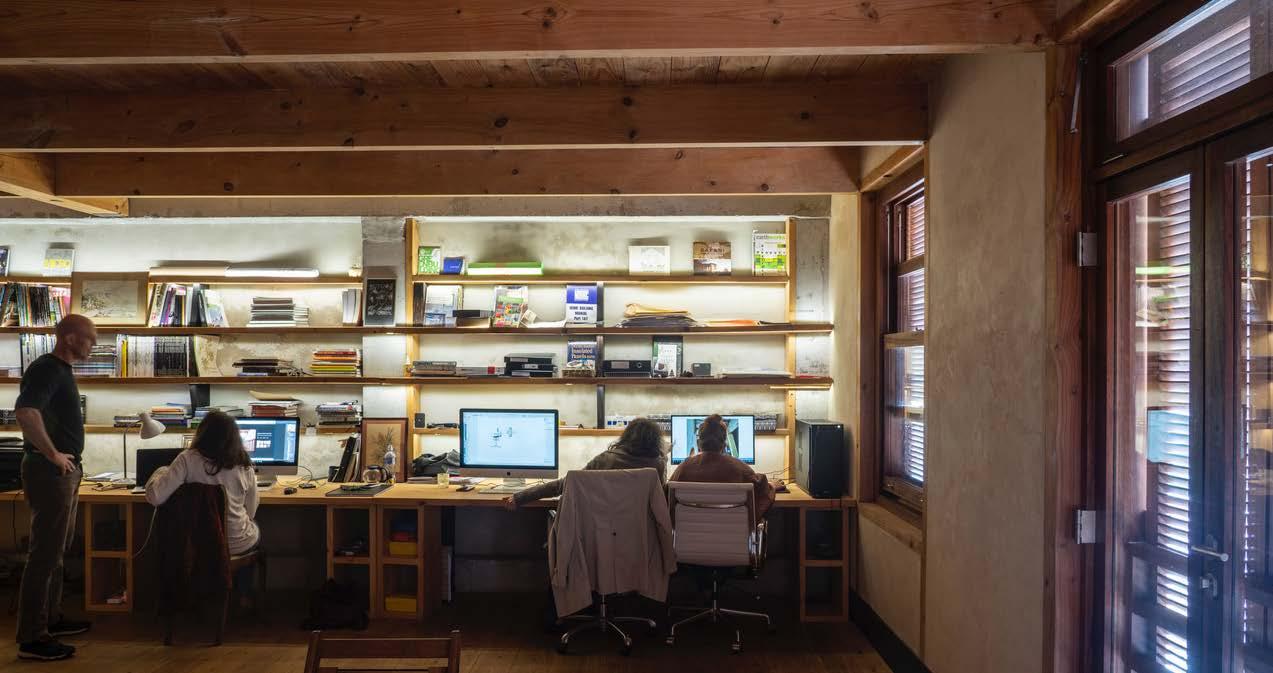
Top Left: Bedroom showing hemp walls.
Top Right: Stairs upto the apartment in the Bokaap hemp house.
Bottom: Wolf & Wolf office.
Bokaap hemp house seen from above, showing greenhouse and roof garden.

As a vapour-permeable material, it can absorb water when it’s raining and then expel it when the sun is shining. This is a huge advantage because, for many building materials, moisture problems can lead to mould and rot.
Hemp takes carbon out of the air and therefore has lower embodied energy. Hempcrete absorbs more carbon than it emits during its manufacture, making it carbon negative. To put that into perspective: one cubic metre of hempcrete will sequester approximately 110kg of carbon from the atmosphere.
An average-sized house would be built using around 50 cubic metres of hempcrete for the walls, meaning that an average hempcrete house would lock up 5.5 tons of carbon for the lifetime of the building. This compares to a more standard new house of a similar size, in which the walls would be likely to emit 48 tons of carbon into the atmosphere. This is a saving of 53.5 tons of carbon for every house built. It is clear to see that the carbon balance is not even close and that, notwithstanding slight variations in calculation methodology, building with hempcrete can significantly reduce carbon emissions, making it a more sustainable building material.
Hempcrete’s ability to save carbon does not stop there. Hempcrete is an insulative walling material and has two crucial attributes in its favour to reduce carbon emissions and save on energy bills – the qualities of moisture management and thermal mass. Largely overlooked by building regulations, these attributes mean that hempcrete buildings require less energy to keep occupants warm and comfortable.
HOUSE OF STRAW
“Our commitment to hemp is based on environmental as well as economic factors. In the context of South Africa, where we have both the suitable climate as well as large amounts of open land, industrial hemp could be cultivated and harvested in abundance with relative ease. It grows quickly, requires little water and has no pesticides or herbicides as it is inherently pest resistant, so its cultivation can be completely toxin-free. In fact, it can even contribute to the Phytoremediation of previously contaminated soils,” says Wolf. “Considering that hemp can also be used to create organic, durable and comfortable textiles, pressed for highly nutritional non-psychoactive oil, used in cosmetics and even processed to create an alternative to plastic, the cultivation of industrial hemp has the potential to substantially grow our local economy and provide sustainable and dignified jobs.
“Afrimat-Hemp is making hemp blocks locally. They are currently using hemp imported by The Hemporium. We anticipate that the hemp licenses will be issued around October 2021. This will make blocks more affordable. Afrimat-hemp has developed a hempcrete mix and hemp-lime plasters suitable for new and heritage restoration work. They are also developing light weight hemp pre-fabricated panels for rapid construction and insulation work.”
Of all the plant fibres used in construction, hemp boasts several characteristics that make it superior from both the ecological perspective and the economic one. With most conventional wall construction techniques, you can expect to find multiple layers of different

Rendering of “Mickey’s Lighthouse” a project that Green Home, Wolf & Wolf and Hemporium are currently fundraising for.
materials, each performing only one specific function. For example, a steel- or timber-framed structure with a composite wall system requires an insulation layer, a vapour barrier layer, a breather membrane and a sheathing layer, as well as the finishing cladding, to name a few. A hempcrete wall can perform all of these functions itself and, due to the reduced number of connection points between these materials, a more air-tight envelope can be achieved.
THE GIFT THAT KEEPS ON GIVING
“Hemp construction can be straightforward and lowtech. It can create a whole new industry and job pool, which is particularly relevant in our South African context. This is the reason hemp is our material of choice for non-load bearing elements,” adds Wolf.
In 2015, Greenhome, Wolf and Wolf Architects and Hemporium joined forces to build a hemp extension to Yiza Ekahaya. Yiza Ekhaya is a soup kitchen in the informal settlement of Khayelitsha in Cape Town and feeds and cares for over 250 people daily. This same team are currently fundraising for a further extension to Yiza Ekhaya, called “Mickey’s Lighthouse”, a three-storey hemp soup kitchen and safe house for young girls.
https://www.givengain.com/c/yizaekhaya/
Wolf and Wolf Architects are currently working on a 12-story building in the Cape Town CBD where they use hemp for the internal walls due to their good acoustic and thermal properties. Due to hemp being so light, they reduce the loading on the foundations and have a fantastic carbon footprint. The building will house a Hemporium retail store on the ground floor.
“In the last three months, we have noticed an increase in the interest in hemp construction from four large architectural firms and developers seeking a way to create carbon neutral or negative buildings,” Wolf concludes.
POIGNANT FACTORS ABOUT HEMP
Very lightweight. Microbe- and insect-resistant. 100% biodegradable as it is fully organic. Excellent sound insulation properties. Sustainable to grow, harvest and process. Mould and rot resistant. Hemp absorbs moisture; one square metre of hemp can absorb up to 14 litres of water. It has excellent thermal insulation values and good thermal mass – well above regulation standard, leading to substantial energy savings compared with conventional building technologies. Unlike most other building materials, it is simultaneously breathable and inherently airtight. As a vapour-permeable building envelope, it regulates internal relative humidity, eliminating condensation on internal faces. It can be a zero-waste material, as previously used hempcrete can be reused and added to new mixes.
Hempcrete is a carbon-negative material, meaning that it sequesters CO2 from the atmosphere. About 108kg of CO2 can be locked away as biomass per cubic metre of hempcrete for the lifespan of the building. Hempcrete is currently in the process of getting SABS approval and an Agrément certificate. The blocks do have a two-hour fire rating for nonload bearing walls.
FUTURE AFRICA: Developing African Science Leadership
A Pan-African research centre
The design brief called for an environment that would facilitate and enhance trans-disciplinary research within the African context, where collective research has a strong focus on science leadership development.
WORDS André Eksteen, project director, Earthworld Architects
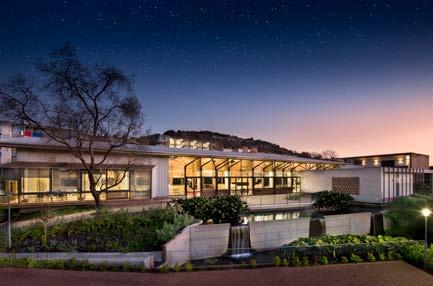
Future Africa was to provide an integrated live-/ work environment for post-doctorate students from all cultures and backgrounds, fostering fellowship, understanding and collaboration among the vast diversity of cultures and disciplines on our continent. The re-imagining of this typology called for centralised spaces for interaction, facilitating collaboration and cultural interaction.
FUTURE FACILITIES
• 280 one-, two-, and three-bedroom living units • Central hall (Future Africa hub) • Research commons • Conference facility: • 250-seater auditorium • Two 50-seater multi-purpose rooms • Six break-away rooms linked to the auditorium: doubling up as translation booths
Future Africa is not only about place (locality) or space (building). It is about the contribution a building can make to the ecology in which it is developed.
CONCEPTS EXPLORED
1. Adaptability
• Systems and tectonics were deliberately disentangled to allow for parallel off-site manufacture and on-site assembly • Levels of permanence can be read in the tectonics • Timber was used for the tertiary systems • This open building allows for adaptive re-use and re-cycling, as well as more inclusive contracting
2. Regenerative design / catalytic development
• Breaking the buildings down in clearly defined elements offers the potential of outsourcing manufacture to small- and micro-enterprises • Design to allow for the establishment of new industries and micro-enterprises that can be funded by community banking • Informal systems in the developing communities already exist; if these can be augmented with quality control and moderation, a new sphere of democratised industrialisation will be established
3. Democratisation of building
• Opening the building industry up to allow for small- and micro-enterprises to participate in large projects is key to the project • The level of ownership by contractors resulted in pride and a sense of accomplishment; traits lost to our industry since labour became a commodity
4. Parallel vs linear value / supply chains
• Local skills were curated rather than using established, imported building systems • Materials sourced directly from or close to site • Integrating the production of the various manufacturers negated the need for linear value chains by material being handled only once
5. Systems thinking / inter-connectedness
• The building is central to a system where people are key • Integration of the local economy, ecology and landscape were critical • The project and the impact during construction is just as important as the final product
The landscape design forms part of the system by re-introducing 56 orphan crops and allowing foraging to explore alternative cuisines and creative interaction around new tastes, textures and colours. CASE STUDY
EARTHWORLD ARCHITECTS
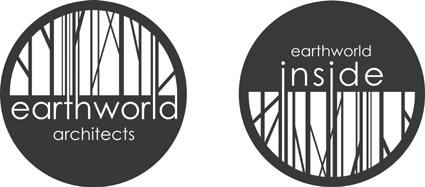