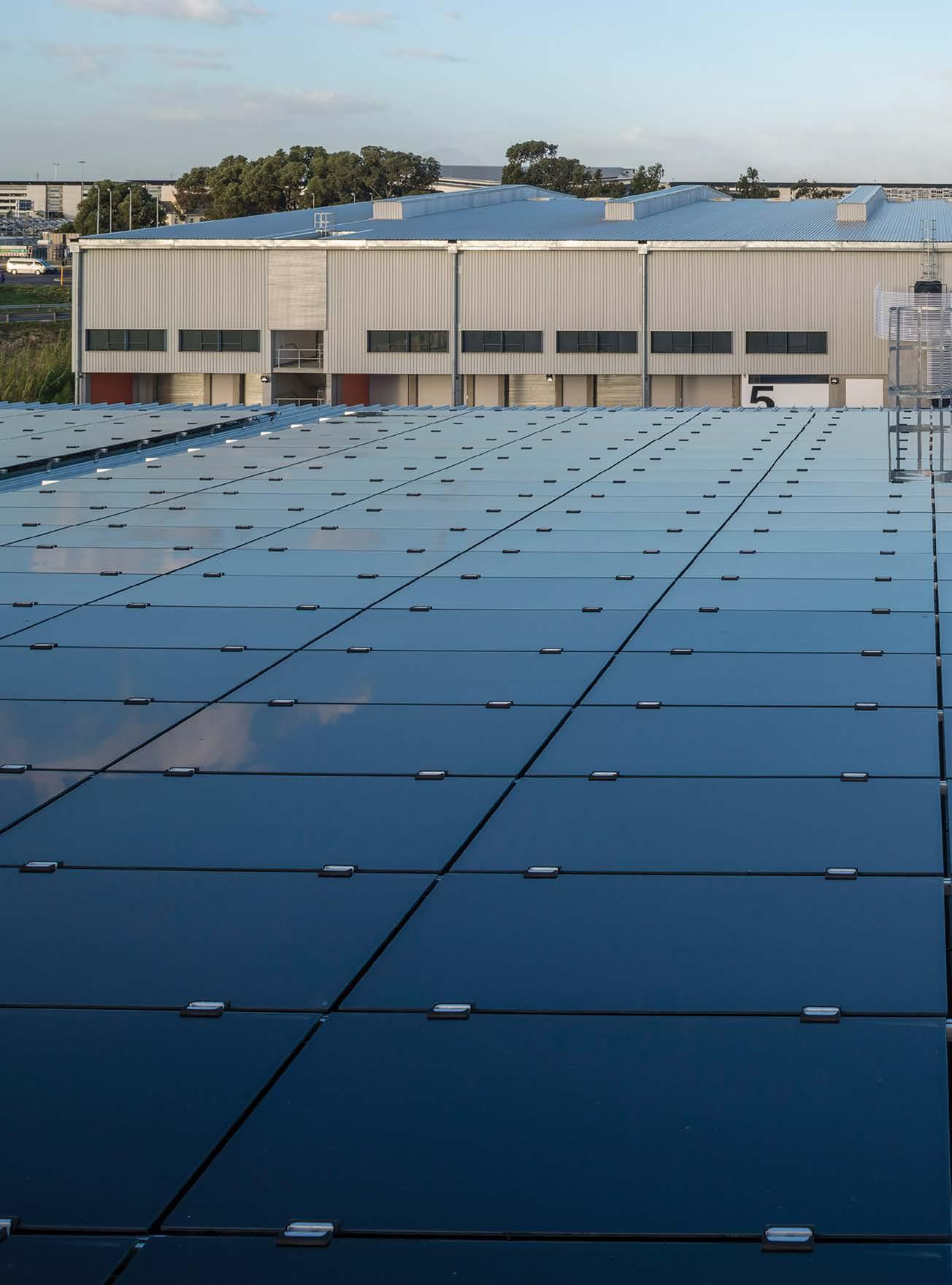
12 minute read
IT’S INDUSTRIAL PROPERTIES’ TIME TO SHINE The GBCSA’s Existing Building Performance rating tool has been customised for industrial buildings
It’s industrial properties’
TIME TO SHINE
Advertisement
Industrious and thriving local economic activities are bound together by the network of buildings near and far. GBCSA’s wildly successful Existing Building Performance rating tool has been customised for industrial buildings, potentially decreasing the cost of doing business and increasing the economic benefits across the sector.
WORDS Alan Cameron IMAGES Growthpoint
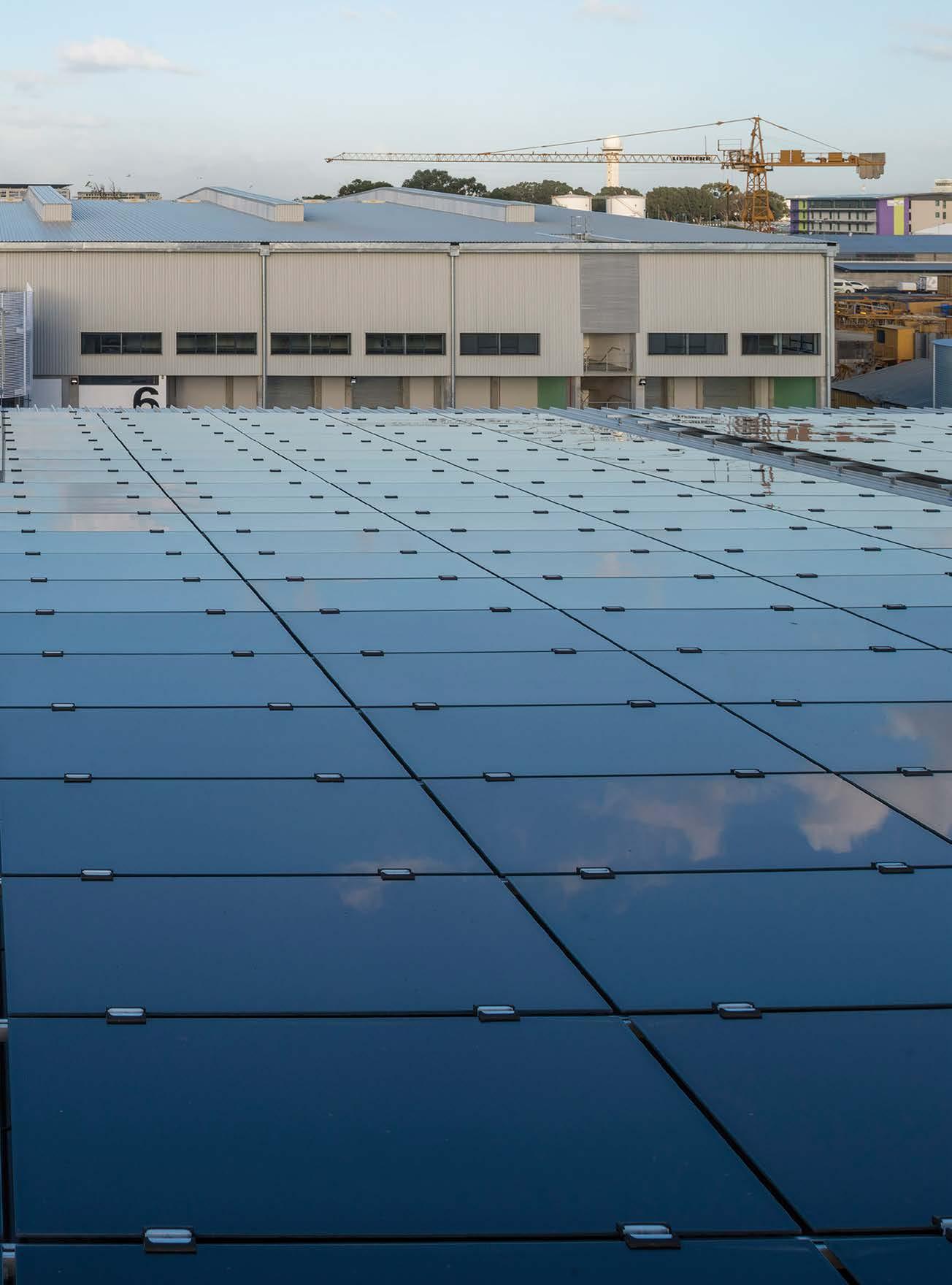
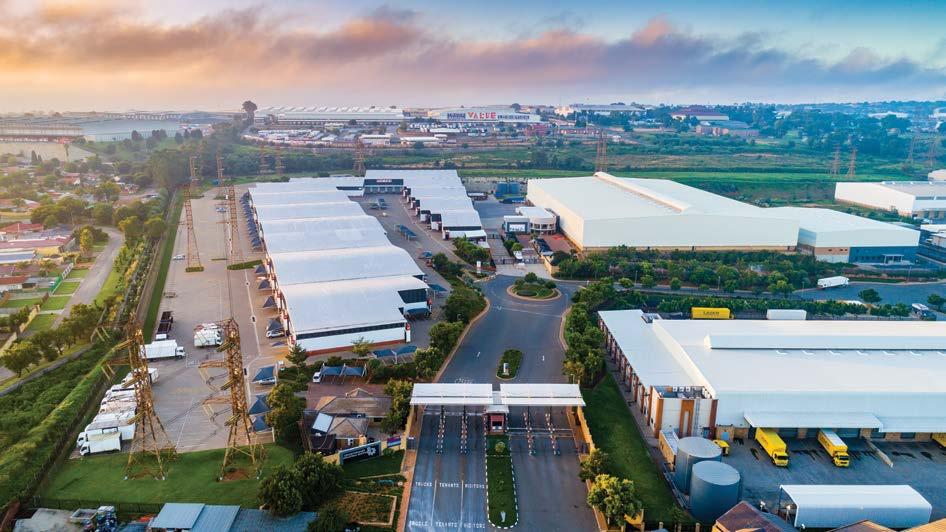
Regional and national economies are tied together by value chains strengthened by a robust network of industrial buildings. These are the sites of industrious enterprise; they generate work and can massively multiply job opportunities. Enabling these buildings to shelter often-fragile economic activity against the storms of global warming and rising business costs has never been so important.
A significant cost-saving in any business asset helps to make it more adaptive to future pressure, and mitigating the rising costs of energy, water, waste and emissions in industrial complexes follows the proven successes in commercial and residential sectors.
The GBCSA board gave a directive that the standard EBP tool should be specifically customised for existing industrial buildings to become the EBP Custom Industrial Pilot rating tool in December 2020 and is headed up
internally by GBCSA technical manager, Jenni Lombard. The tool is a custom version of the established EBP tool credited with greening the commercial sector.
This iteration of the tool holds the same potential for industrial properties, says Grahame Cruickshanks, head of sustainability and utilities at Growthpoint Properties. As a founding member of the GBCSA, and committed advocate for a more sustainable built environment, Growthpoint Properties came on board to sponsor the EBP Custom Industrial tool development.
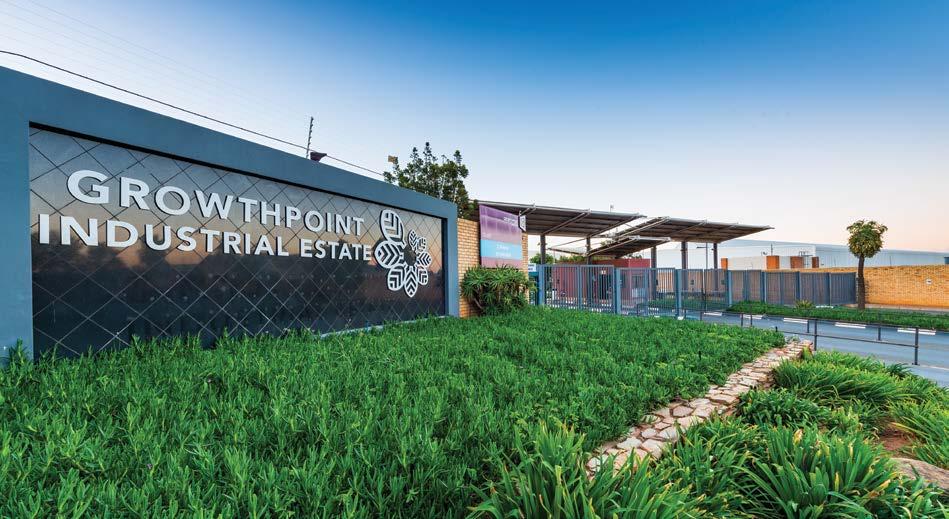
Situated within the bustling node of Meadowdale, Germiston, Growthpoint Industrial Estate (above and below) provides easy highway access and is close to O.R. Tambo International Airport.
With a portfolio of assets in South Africa, spanning all three traditional property sectors (office, industrial and retail), Growthpoint notes that the GBCSA Energy Water Performance (EWP) benchmarking tool, which is integrated into the EBP tool gives property owners a grassroots understanding of the property’s efficiencies and costs, and a tree-top perspective on sustainability and financial products, especially as lenders increasingly invest in programmes characterised by environmental, social and governance (ESG) criteria.
“In the last two to three years investors have begun assessing ESG reports and metrics closely to evaluate the bankability of investments. Long-term returns are being linked to ESG performance, with better ESG metrics making a good investment great,” Cruickshanks notes. “Many tenants have ESG targets linked to their ESG strategies. This applies especially to listed and multi-
Growthpoint’s Greenfield Industrial Park in Cape Town was awarded South Africa’s first ever Green Star rating for an industrial property. It received a 4-Star Green Star Custom Industrial As-Built certification from GBCSA. Setting new benchmarks for sustainability in the South African industrial sector, Greenfield achieved full scores for energy efficiency for its rating. It will be a key pilot project for net-zero energy buildings in the country, because the base building (excluding tenant loads) produces as much of its own energy as is consumed by it over the course of a year.
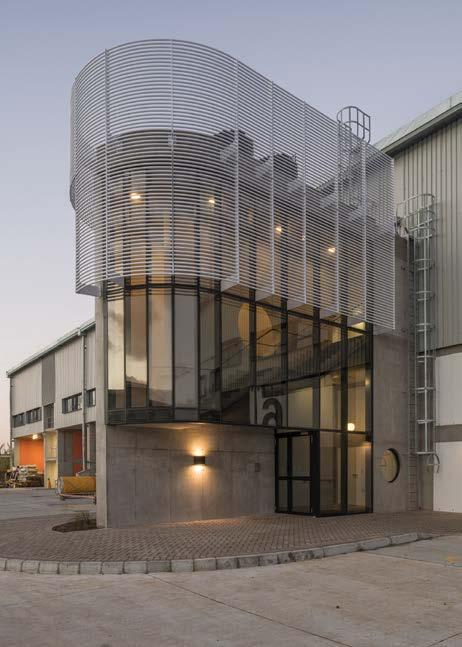
WHAT’S DIFFERENT?
The EBP Custom Industrial pilot rating tool follows the same structure as the current Green Star – EBP v1 tool, but with adaptions and benchmarks specific to the industrial sector. The differences property owners can expect to see are:
• Credits that are better aligned with the varied kinds of industrial building typologies. With respect to energy and water, benchmarks have been put forward for specific sub-categories such as distribution centres, warehousing, light manufacturing and workshops. All energy and water usage is included within the benchmarking process, with certain conditions set out for the exclusion of unusually large process loads.
• A new Energy and Water Benchmark Framework
that can be used when following benchmarking operational performance for the industrial sub-
categories. This has been developed from a dataset collected specifically from existing industrial buildings and will perform the function of providing a simplified industry benchmark, but one that has taken some normalising factors into account. Existing operational performance data was contributed by major REITS, analysed by the appointed sustainability consultants and new benchmarking parameters were set to form this framework. “The significance is that it will tangibly support industry by offering a standardised methodology for analysing energy and water performance data both for comparisons (that is, to compare apples with apples) as well as in offering indicative benchmarks based on primary data that has been collected,” adds Smit.
• Credits that support property owners and tenants working together at improving assets. As with the EBP v1 tool, property owners can address some credits without necessarily involving tenants. However, for many of the credits relating to building management practices such as waste management, green cleaning and so on, it will be necessary to have the tenant commit to implementing such procedures. “The custom tool incentivises increased engagement with tenants. We believe that this will be critical not only in the success of the tool but also has huge potential knock-on effects into tenant processes,” says Retief.
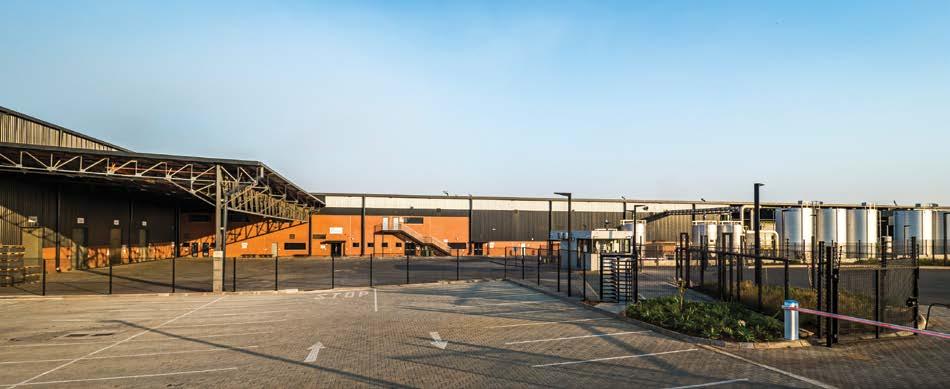
The Wadestone Industrial Park in Wadeville, Germiston.
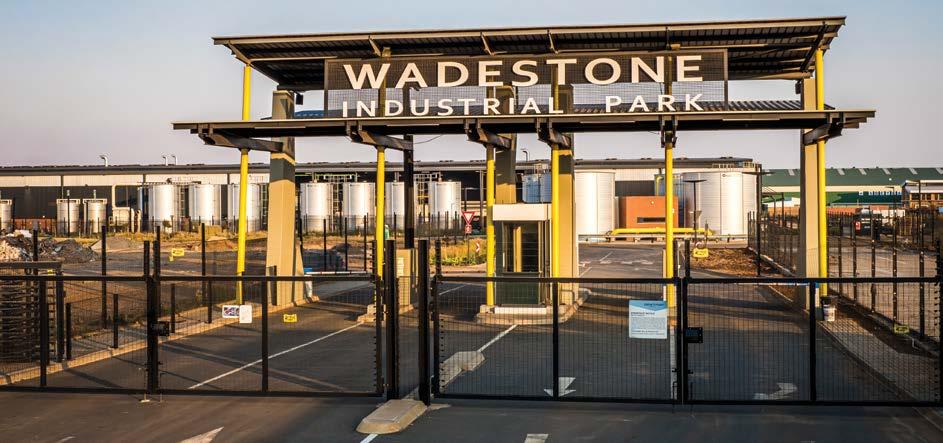
The Wadestone Industrial Park in Wadeville, Germiston.
national companies and occupying a Green Star certified building makes a positive contribution to many company ESG strategies and targets.” Cruickshanks is confident that the industrial construction sector will take the opportunity to improve their assets through certification.
“One of the key successes of the Green Star EBP rating tool in the commercial office sector is the inclusion of green building rating as an enhancement to total return on investment as well as property values. Green-rated property portfolios also comply with many investor ESG requirements adding further value in the form of investor attractiveness. The widespread application of the Green Star EBP rating tool to P and A-Grade commercial office buildings has supported the adoption of green building in the majority of listed and many unlisted property portfolios as a must-have,” Cruickshanks says.
JUSTIFYING INVESTMENTS
The demand for an industrial version of the tool reached a tipping point in December 2020, despite the thenpresent reality of the Covid-19 pandemic. The validation of Growthpoint’s investment was quickly achieved as the industrial sector outperformed other property classes during, and in many cases after, the pandemic. It grew with the increased use of warehousing and distribution services used by on-demand logistics companies and was also flexible enough to accommodate tenants down-sizing. The non-speculative nature of industrial tenancies and developments also helped the sector to deliver to investors, the Rode Report on SA Property Market 2022:2 notes.
The GBCSA’s existing Green Star – EBP tool is aimed at rewarding buildings that are managed sustainably well, can demonstrate good operational performance over a measured period and that contribute towards better quality spaces for tenants. “When the original EBP tool was developed, it endeavoured to take as many building typologies as possible into account, but there were nonetheless limitations, and, in reality, it has largely been applied to the commercial office segment of the market,” explains GBCSA head of technical, Georgina Smit.
The customisation process was adopted to ensure that GBCSA can offer market standardised guidelines
for energy and water benchmarking of industrial buildings, as this did not exist in the South African property market. Furthermore, nuances around industrial building ownership needed to be slightly reconsidered within the tool to better serve the market. For example, many single tenancies operate on triple net leases which places a lot of the operational decision-making with the tenant and not the landlord.
The industrial typology is an interesting one because the sector itself is quite varied, with sub-categories including distribution centres, warehousing, light-manufacturing, workshops and more, comments Francois Retief from Sow and Reap who along with Imbue Sustainability assisted with the tool customisation. Also, because the leasing structures place more responsibility on the tenant than the property owner, issues of sustainability in the building are often neglected as they are seen as secondary to the industrial activities themselves, or responsibility is unclear between owners and occupiers. “As such, it is important to create a framework which allows for landlords and tenants to work together at improving the assets,” adds Retief.
Better-managed and better-performing green industrial buildings have great potential to decrease energy and water consumption, as well as reduce waste-to-landfill production. Furthermore, warehousing and distribution centre types of buildings have the capacity to generate more energy than the building demands, enabling them to be exporters of energy.
Plenty of roof space and large hard surfaces make industrial properties well suited to achieving efficiencies in power and water. Beyond stacking solar PV on these large roofs, the electrical load is low for warehousing, logistics and distribution centres as it is mostly required for lighting. And this draw is dialled right down in those properties that have their natural lighting design done correctly, says Retief. Examples can be seen when natural
lighting is allowed through vertical façade elements and vertical roof light. By starting the sustainability journey on the architects’ drawing board not only does the building take full advantage of natural lighting but it also requires minimal additional lighting. And besides being extremely efficient, motion sensors can dim and switch off lights automatically when there is no activity.
To the question of the benefits of the added complexity of quashing artificial lighting requirements through passive design, and if it is worth it when lighting is a seemingly low expense. Consider then the frequent double-digit annualised increase that power costs present each year for the lifetime of the building, as well as the present unreliability of state electricity supply. Beyond the impact on the environment, the business security that uninterrupted, convenient use of a facility designed for optimal use increases the attractiveness of the premises for its users, who before signing the lease will consider in minute detail how the premises aligns with their business needs.
Reducing the need for other municipal services such as potable water use and solid waste collection dovetails into this too. Harvesting grey and waste-water runoff is often a simpler matter at industrial properties with the long straight lines typical of rectilinear properties. Reticulating this water for toilet flushing, landscape irrigation or even washing of vehicles contributes to mitigating an ongoing cost. Effective on-site waste separation and recycling outsourced to a wastemanagement contractor with the ability to collect and account for it, further contributes to the growing ESG metrics for owners and tenants.
“Industrial buildings, such as warehouses, manufacturing plants and logistics facilities play a key role in the smooth running of national and regional economies. It’s vital that these assets are future-proofed for the impacts of a changing climate and the rising costs of energy, water, waste and emissions, as well as delivering other benefits for their tenants,” explains Errol Taylor, head of asset management: industrial at Growthpoint.
THE ROUTE TO CERTIFICATION
“Smaller property owners could leverage opportunities where the inherent building design lends itself to an EBP rating. Many of these features are already included in a building specification and if the building is well operated it means less of a leap to certification,” notes Cruickshanks.
The route to certification will include an accredited Green Star consultant evaluating energy and water performance through 12 months of utility accounts, assessing the site and engaging with occupants. Discussing how building occupants can utilise efficient design and proactive behaviour to take advantage of environmental and social stewardship opportunities enables the certification to water the seed germinated through certification to establish a thriving legacy.
Taylor anticipates that over time the new tool will demonstrate that Green Star – EBP Custom Industrial certified buildings outperform non-certified industrial buildings against ESG criteria and financial returns on investment. Smit concludes: “GBCSA hopes to support the market transformation of the industrial sector, in the same way it supported the journey of the commercial office space, with this tool. We are also hoping to embark on a journey of continuous energy and water data collection to refine benchmarks for future iterations of the EBP tool.”
Energy efficiency is at the core of the Mount Edgecombe Business Park. Motionsensing warehouse lights can be set to 50% or 100% and change with the quality of outdoor light which streams into the bright, airy buildings through the clever use of translucent polycarbonate sheeting.
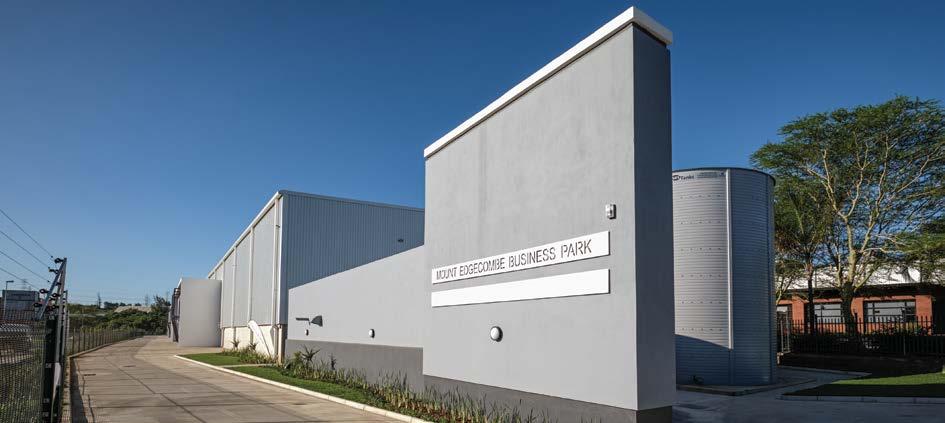
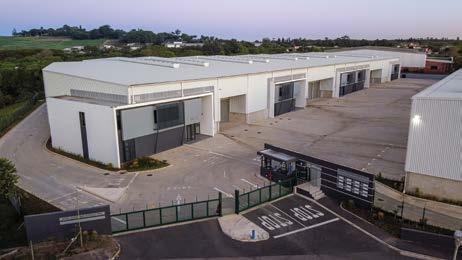

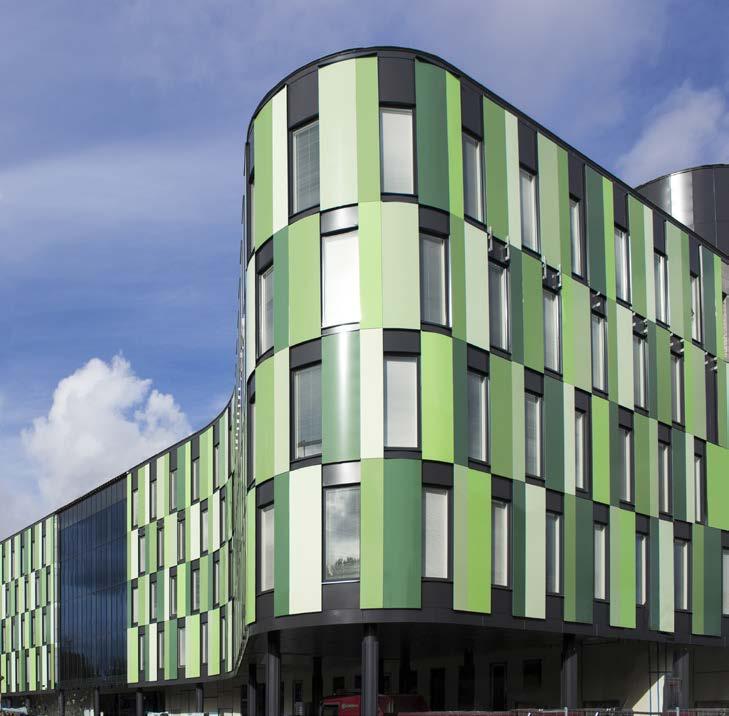

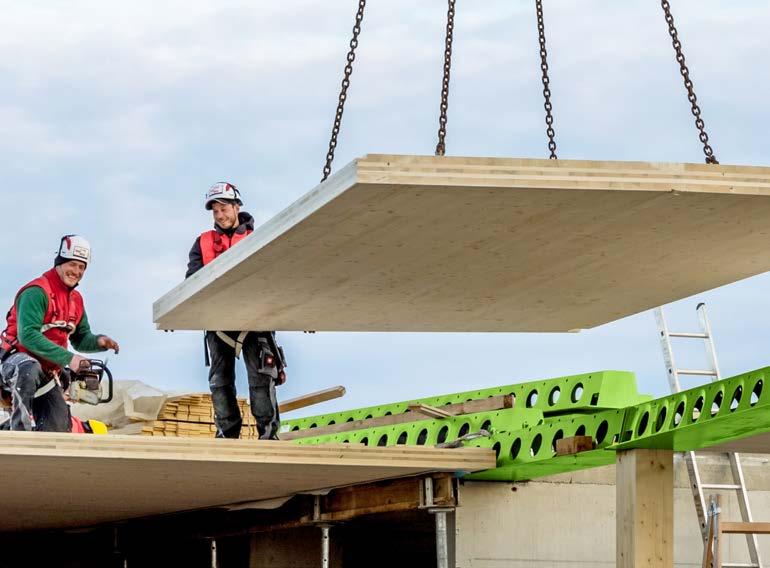
Peikko are Forerunners.
What does that mean?
• A rich heritage: Peikko was originally founded under the name of Teräspeikko by Jalo Paananen.
Now Peikko is owned by the second and third generations of the family – continuing the work. • Independence: Manufacturing operations in 12 countries, we can guarantee safe, standardised and quality production. • Innovations: Our products have shaped the construction industry and some of Peikko’s innovations still hold their ground as industry standards to this day. • Being an inspiration to others: Thanks to our constant innovation, our products get copied a lot, but we take it as a compliment. • Shaping the future: We constantly keep up-to-date with the latest trends in the industry and take part in standardisation work globally to make the construction industry faster, safer and more efficient.
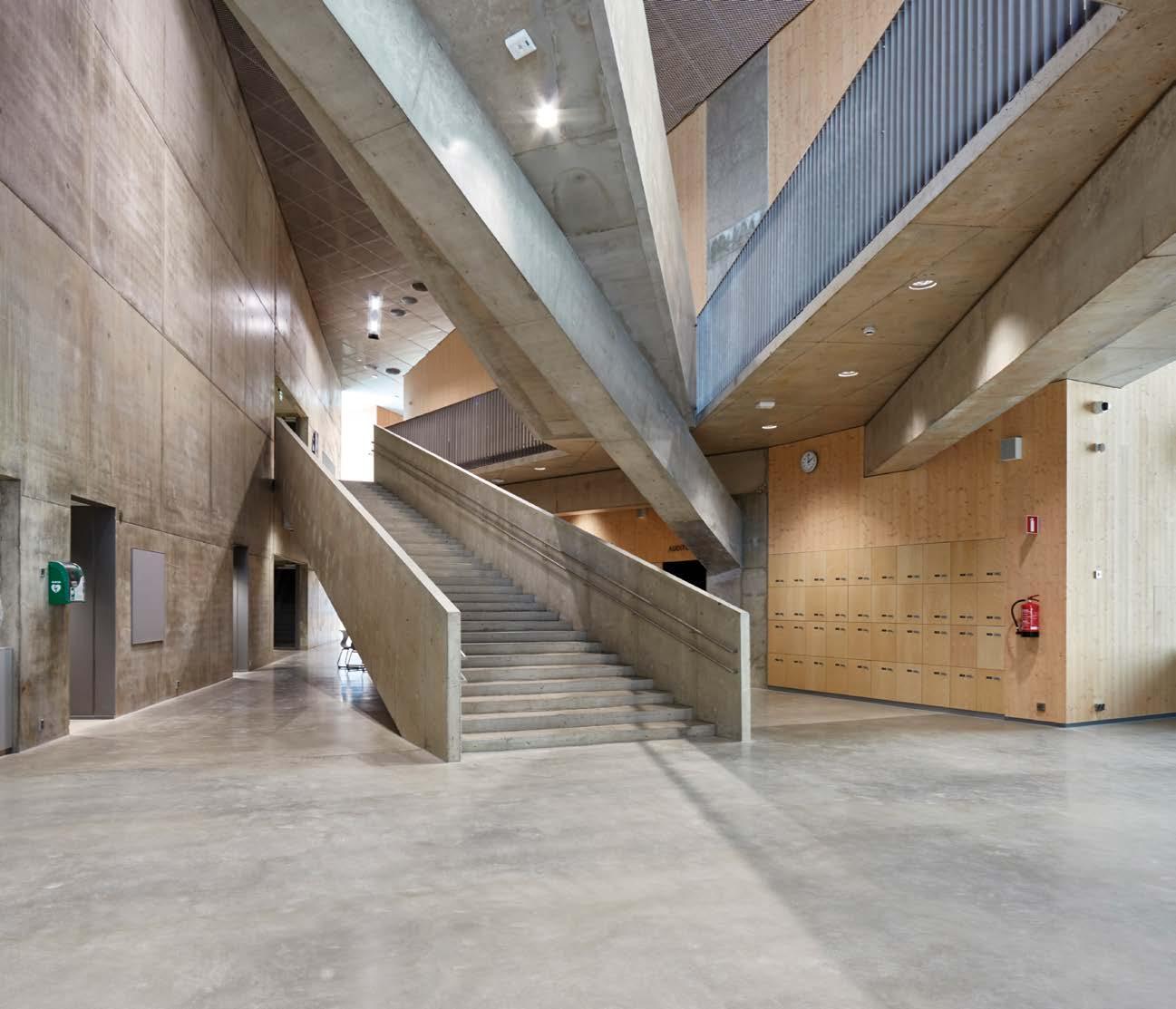
Peikko South Africa (Pty) Ltd
values
As a family-owned company, our roots are in customer-oriented innovations. We have a strong set of values that guide the way we work and interact with others.
For Additional Information:
Managing Director: Daniel.Petrov@Peikko.com Project Engineer: Winston.Visser@Peikko.com