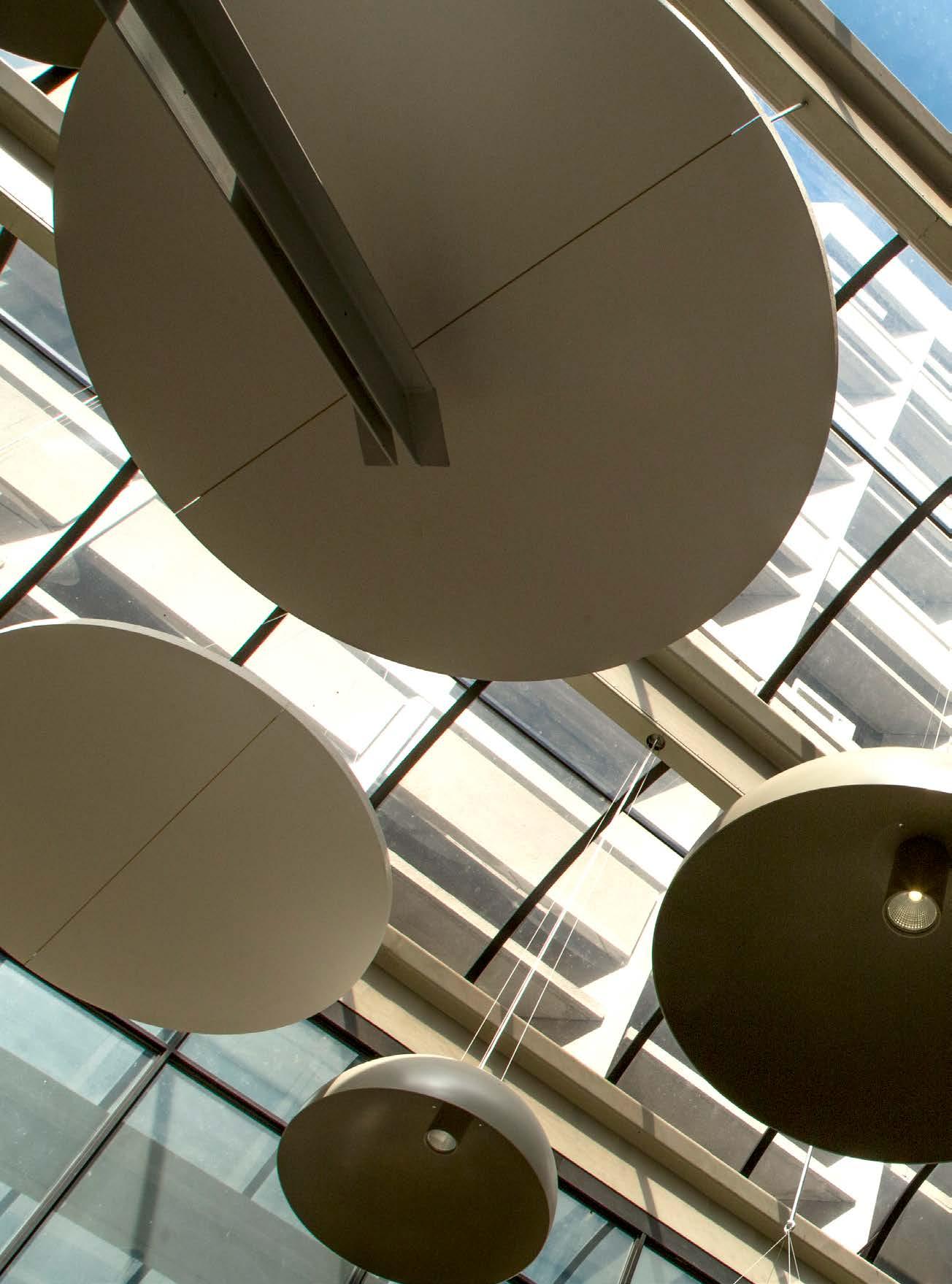
10 minute read
TAKING “MEASURE, MONITOR, MANAGE” TO THE NEXT LEVEL
Taking “MEASURE, MONITOR, MANAGE”
to the next level
Advertisement
The headquarters for the Western Cape Department of Transport and Public Works is the first public sector building to achieve a 4-Star Green Star Existing Building Performance v1 rating with GBCSA. This flagship project boasts several innovative features.
WORDS Marlinée Fouché IMAGES Western Cape Government
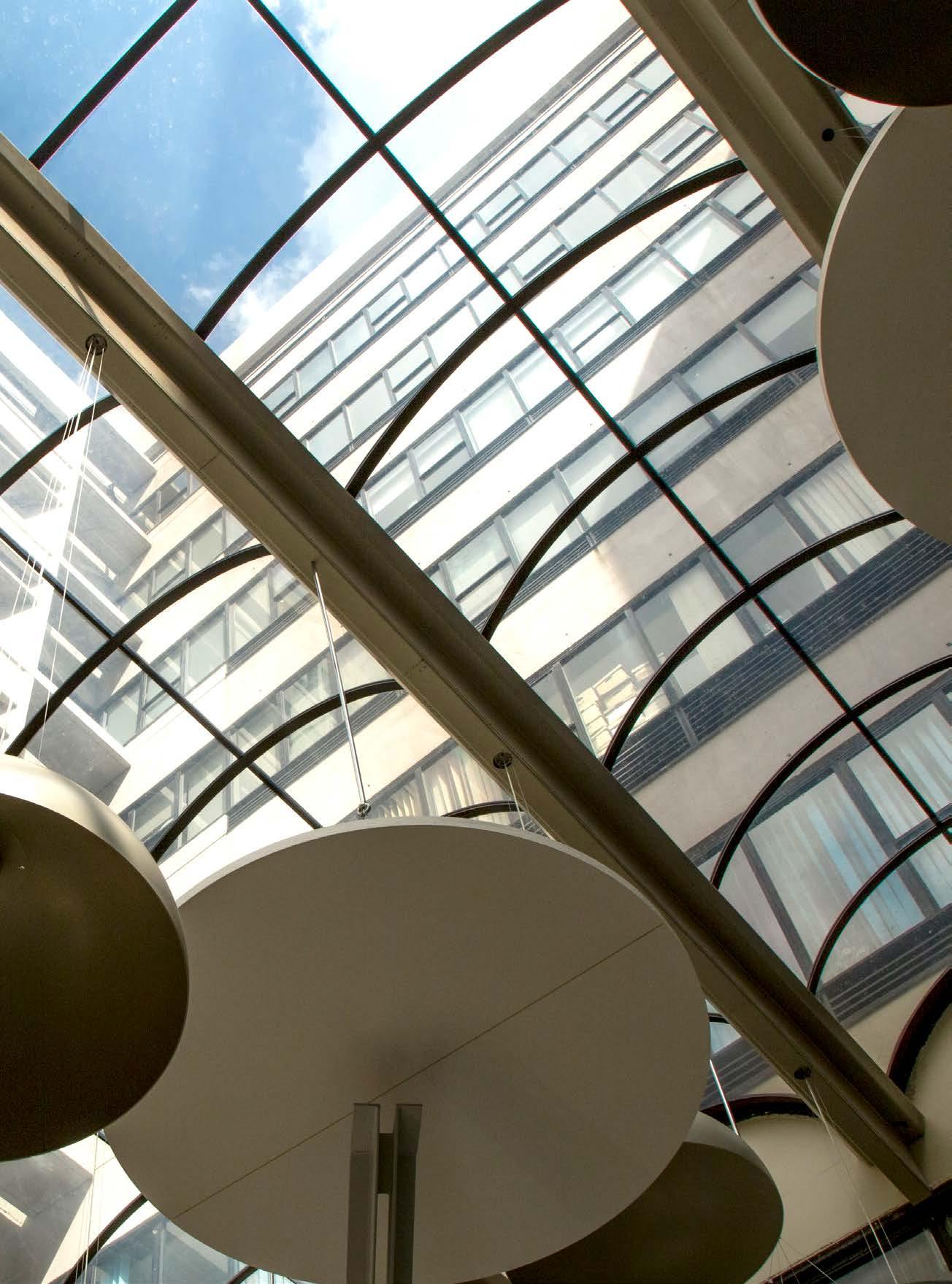
PROJECT NUTSHELL
Location: Cape Town CBD Green Star rating: 4-Star Green Star rating, Existing Building Performance v1 Type of building: Public sector Project dates: Certified June 2022 Project size: 13 905m² total gross floor area
Number 9 Dorp Street is a renowned modernist building in the City landscape. These buildings are typically modern, in that they employ a level of horizontally clean white façades, floor-toceiling glazing which offers views of the South African landscape, ribbon windows etc and are typically harder to renovate for greater efficiencies.
Initially a guinea pig for sustainability projects, 9 Dorp Street can now be considered one of the pioneers for performance-based sustainability in the public sector – not only because of its physical sustainability features, but also for ingraining a culture of sustainable practices among employees and other government officials.
The working environment in the building, situated close to parliament and the central train station in Cape Town, is constantly adapted with this principle in mind. “There’s sort of a freshness to it,” says in-house accredited professional (AP), Karl-Robert Gloeck. “As you step out of the lobby, you can already see the perimeter windows where the natural light comes in. A lot of the areas are open-plan and with single corridor access. More employees can be accommodated on a single floor, and that reduced the overall footprint as far as accommodating government staff within the CBD.” The concrete brise soleil elements on the building façade help mitigate unnecessary heat gain, and the upgraded airchilled HVAC systems ensure user comfort is maintained, altogether creating a light and airy feel for all spaces on the modernised floors.
Desk space has been optimised, light sensors were installed, and shelves are mostly limited to a height of 1.4 metres, allowing natural light to reach throughout the floor.
Kode says there’s more to the process than meets the eye. “It’s part of the journey of becoming an employer of choice, to attract the best people to do the best job for the people and citizens of the province. At the same time, you are reducing water and electricity as well as the cost of thereof to the taxpayer.”
This nine-storey office block incorporates various sustainability initiatives in line with the Existing Building Performance v1 certification tool. The most notable of which, according to Gloeck, concern water usage, the building monitoring system as well as the property efficiency report.
“There are 32 electrical meters, one of which is connected to the solar PV panels, and there are nine water meters and a groundwater meter,” says Gloeck. “Essentially, these allow for monthly reports to be issued to the general infrastructure directorate for capturing and monitoring, and there’s a display of energy and water usage for the building in the foyer. Users entering the building are able to read the measurements.” This allows for accurate performance measurement concerning energy and water, which can be compared month on month, season on season and year on year.” Energy usage, for example, is metered per floor, which means that comparisons can be made to identify where improvements can be made.

Visitors to the building are welcomed in an open, light space.
The headquarters for the Western Cape Department of Transport and Public Works.

The threat of day zero in 2017 ushered in a drastic review of the approach to water management, so it comes as no surprise that this was one of the highest-scoring categories. “There were a lot of drastic interventions, including waterless urinals and low-flow fittings for many of the bathroom taps. The water meters are tuned to a level where they detect even minor leaks early on.”
Along with this, there are two bigger intercessions: replacing the water-cooled chillers for the HVAC with air-cooled chillers, and a groundwater system in the second basement. Kode says a lot of work has been done historically, and the dual plumbing system, which now supplies 95% of the water requirements for the building’s ablutions, is one of them. It was part of the original building design, but because no one was thinking about water scarcity back then, it was only recommissioned more recently: “Now we are using a lot of free basement water that would otherwise have been discharged into the municipal stormwater system.” The water is UV-filtered, and then distributed for toilet flushing, without cost or potable municipal water consumption. “That accounted for about 40% of the water use in 2019/2020,” says Gloeck.
Measuring, monitoring and managing is of primary concern at 9 Dorp Street, an approach epitomised by the yearly Property Efficiency Report, which scored the building a point in the innovation category. “Last year we published our tenth edition,” says Kode. “This document reports on the office portfolio of every building greater than a thousand square meters. Then we can set targets and benchmark ourselves against similar buildings in the private sector.”
According to Gloeck, it’s a one-of-a-kind publication in South Africa. “It reviews the performance and resource usage of applicable buildings in the portfolio by capturing and recording their energy and water usage, space efficiency and other performance metrics, and there’s quite a substantial framework for comparison for energy and water usage.” Instead of only having access to information on the last year or two, APs can now see a decade’s worth of comparative data. “The improvements have been quite staggering. There was a reduction in 57% of the energy usage for 9 Dorp Street from 2013 to 2021, and a remarkable 97% reduction in the use of water for the same period.”
One aspect that sets this certification apart – and contributed to yet another innovation point – is the Western Cape government’s attempt to “grow their own timber”. The eight APs that certified 9 Dorp Street, formed
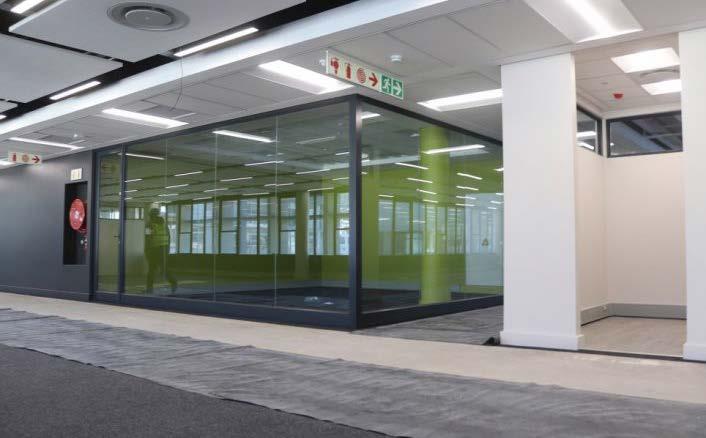


Partitions and storage space in the open plan office is mostly limited to a height of 1.4 metres to create an airy feel.
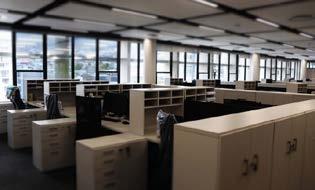
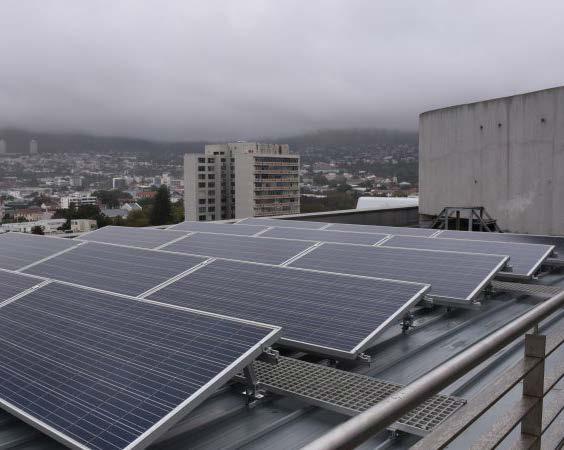
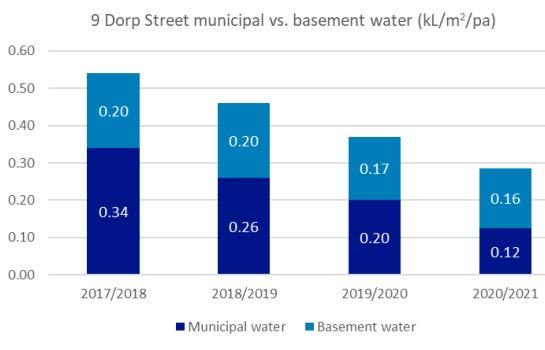
The threat of day zero in 2017, ushered in a drastic review of the approach to water management, including the utilisation of basement water for the building.
part of 54 Public Works officials who were trained as APs under GBCSA’s Existing Building Performance tool. The team of eight formed a task team, that initially used 9 Dorp Street as a case study and then through to simulated registration and certification of the building – with the goal to do the actual certification of the building after completing their training.
This team, consisting of engineers, immovable asset management professionals and architects in the public sector, allowed for a substantive approach to the process. Gloeck, a chief architect in the Chief Directorate Health Infrastructure, played a leading role in the certification process. He is particularly proud of this. “We’re all in the accommodation and infrastructure implementation sphere, building hospitals, schools and clinics, upskilling internal staff and managing various property issues; this was an opportunity to address a different challenge. These are steps working towards our goals of becoming a net-zero government by 2050 to align with the national mandate, and to foster an understanding of what needs to be done, to reach a point where the province’s buildings are recognised as sustainable.”
Modernisation is part of the journey to attract the best people for the job.
This is exactly what the Western Cape government wants to achieve, says Kode. “We are endeavouring to develop awareness in the realm of sustainability by investing in our people. They might not necessarily all take part in the certification training or directly be involved in the process, but it enables them to see the impact more broadly through the buildings they interact with, which has a ripple effect through the organisation and communities.
Plans are underway to vertify two more of the Western Cape Government’s office buildings in the city centre, and it is expected that they will receive their ratings early in 2024.
XPOD AND BIOBUILD™ - A BUILDING METHODOLOGY FOR A BETTER ENVIRONMENT
Through the use of recyclable materials, the core intention is maintained, to provide an ecological building alternative that is accessible, and affordable.

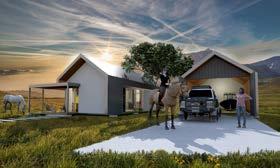
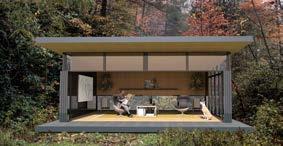
To understand how green the xPod designs and BioBuild™ materials are, you would be forgiven in thinking that it is all just context – but, on the contrary, the reality is very different.
In South Africa, between 5 million and 8 million tonnes of construction waste are generated annually. Only a small fraction is reused or recycled. The result is that a large amount of waste is disposed of in landfills, which are rapidly reaching capacity in many places. The literature suggests that as much as 30% of the material delivered to a construction site ends up as waste. Concrete and other cementitious materials were most frequently cited, followed by bricks. Wood, plastic and cement bags, formwork and sand were also mentioned. The two most prevalent reasons cited for the causes of waste were the lack of skill of labourers and contractors, and poor supervision. Other reasons include poor material handling, negligence, speed of execution, design changes, poor management and planning, and the standard work process. Construction workers sometimes did incorrect work, leaving waste after the incorrect work was demolished. (The Conversation, 5 October 2022)
The impact of buildings and construction on the environment is astounding, with the built environment currently accounting for 20% of the world’s water usage and 40% of its electricity. There is great significance in the fact that green buildings can reduce global carbon emissions by up to a third. South Africa is on its way to becoming one of the global leaders in green building.
The xPod off-site fabrication and manufacturing solutions are extremely beneficial to this environment, in that the central feature of all our models and designs is that they are non-invasive and seek to leave the natural topography untouched.
We have emphasised that wood waste is one of the largest portions of the waste stream generated from construction and demolition activities and the lack of sustainable usage for the disposal of the material. Hence the incorporation of BioBuild™ panels in the xPod designs.
BioBuild™ consists of an ingenious combination of mineralised woodchips and cement, which provides a unique ecological and economical alternative to traditional building materials. This is due to the ease/speed of installation and modular design capability, as well as providing various insulation and acoustic properties. With our core materials consisting of recycled wood waste and cement, we have created a fully sustainable green building alternative that we feel is a direct replacement for brick & mortar.
BioBuild’s eco-friendly production contributes to the reduction of CO₂ emissions in the manufacturing process and offers a sustainable solution for the recycling of wood waste. BioBuild™ offers an alternative that assists in the preservation of energy and natural resources during the construction process and throughout a structure’s life cycle.
The structural frame was designed to avoid the need for any cut and fill excavation, to preserve the natural conditions, topography and existing flora. Since all units are premanufactured, on-site waste and site establishment processes are kept to a minimum. The design philosophy allows for the integration of PV systems, incorporating water harvesting systems, as well as various waste disposal options. Since the implementation relies on an installation methodology as opposed to a construction methodology, all logistics and process-supporting activities are vastly streamlined.
The xPod and BioBuild™ building methodology intends on creating a healthier and sustainable living environment by reducing the carbon footprint of infrastructure through the use of recyclable materials, while maintaining the core intention to provide an ecological building alternative that is accessible, and affordable.