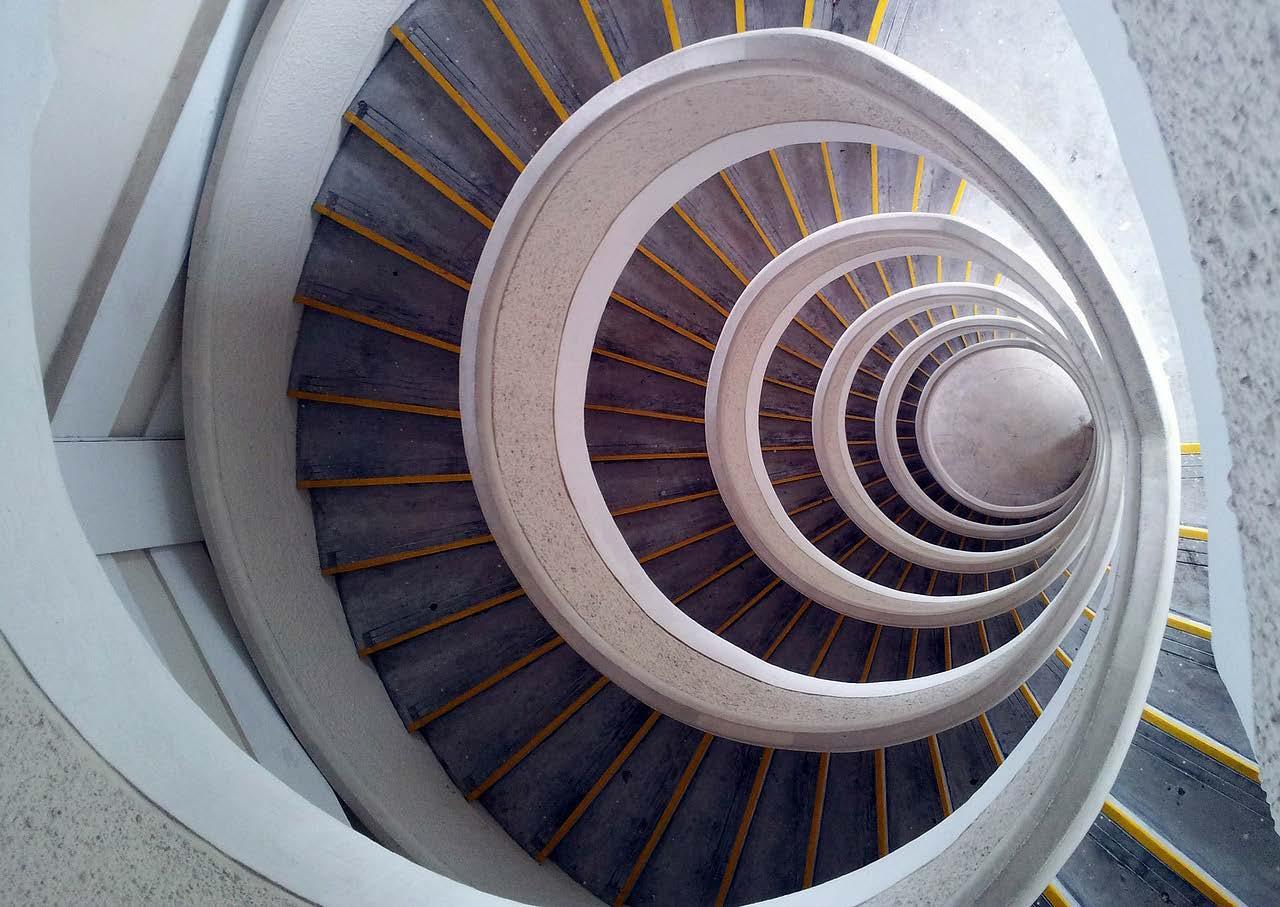
8 minute read
CONSTRUCTION
CIRCULAR ECONOMY IN CONSTRUCTION
Geopolymers as a low-carbon cement alternative
Advertisement
Social and mainstream media are all doom and gloom about mankind’s inability to transition to a low-carbon economy and mitigate the effects of climate change on the planet. Our economic development over the last century has been based on a very linear model of take-make-dispose and the drive now is to embrace the principles of circularity in the hope of a greener and more sustainable future.
BY CHRIS WHYTE, AFRICAN CIRCULAR ECONOMY NETWORK (ACEN)
Cement as a single sector contributes some 8% of all global emissions contributing to global warming and the built environment is said to contribute 39% of global emissions. The cement industry is doing a huge amount of work currently to reduce the carbon emissions of their product addressing greener alternative fuels for their kilns; harvesting their waste heat; reducing the clinker to cement ratios and deploying CO2 capture and storage technologies.
There is another option, and it is not cement. Geopolymer technology offers an alternative, using problematic waste streams like fly ash, blast furnace slag and selected mine tailing waste and offers engineering advantages over conventional materials. Geopolymer technology is not a new phenomenon globally and in his quest for low-carbon alternatives the author has engaged with American and European scientist developing geopolymer materials. However, South Africa has one of the foremost material science engineers pioneering its development in Cyril Attwell from Arc Innovations in Gauteng.
One cubic metre of concrete has a carbon footprint of 350kg of CO2, making this staple material in the construction industry one of the biggest
Construction of the wind turbine bases at Khobab Wind Farm.
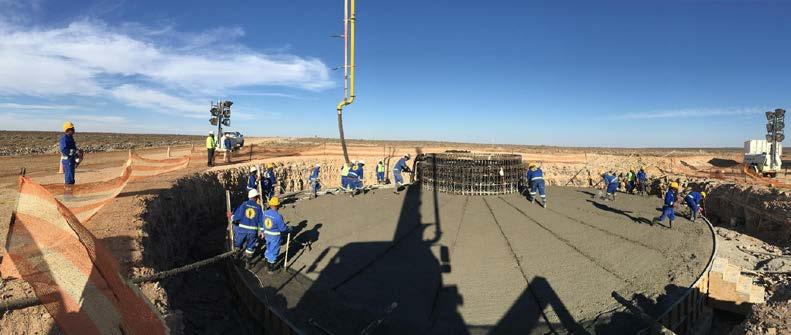
contributors to greenhouse gases in the world. Attwell is one ardent scientist looking to turn concrete’s bad rap around, exploring ways to take the material from grey to green. The development, commercialisation, and ultimately the use of hybrid cement technology provides for a far more sustainable and environmentally responsible process with the potential to replace traditional and widely used cement. Hybrids are a type of inorganic polymer that can be formed at room temperature by using industrial waste or by-products as source materials to form a solid binder that looks like and performs a similar function to normal cement.
Hybrid binders can be used in applications to replace cement fully or partially with important environmental, technical, and notably, cost benefits – including an 80-90% reduction in CO2 emissions and improved resistance to fire and aggressive chemicals. Hybrid cement is made from aluminium and silicon, instead of calcium and silicon. The sources of aluminium in nature are not present as carbonates and therefore, when made active for use as cement, do not release vast quantities of CO2. By marrying this knowledge of construction and construction materials with innovative concrete technology, there is a viable alternative in a changing environment that is competitively priced and has significantly lower impact on the environment than the traditional, price-sensitive and commoditised products currently available.
While in continual development, the application of geopolymers is currently available at a commercial scale and has proven itself in multiple infrastructure projects across the country since 2006 and won several awards in recognition of its contributions to emission and cost reductions while meeting or exceeding engineering requirements. Many would be familiar with the project applications, but perhaps not aware of the role of geopolymers in their success. • The Gautrain project used ARC technology to significantly reduce the originally estimated cement content of 344 000 tons to 210 000 tons with the replacement of pulverised fuel ash (PFA). • The 32-storey Portside Tower in Cape Town is the largest alkaliactivated concrete structure in the world and the first building in South
Africa using up to 85% cement replacement with slag. This delivered significant savings in cost while achieving high durability co-efficient for chloride and oxygen permeability indexes. This application assisted
Portside in achieving a 5-Star Green Star rating with GBCSA. • 102 Rivonia in Sandton (2013) is first skyscraper in South Africa with cement replacement with PFA in excess of 38%. Most of the concrete batched on site utilised cement replacement values of 64% cement with PFA with significant increases in durability, strength and aesthetics achieved. 4-Star Green Star Rating with GBCSA. • At the Loeriesfontein Wind Farm (2015), standard concrete uses up to 95% cement replacement with a reduction in carbon footprint of concrete (more than 70%). This is the first high-fatigue structure in the world constructed with 100% cement replacement. • The Majuba Power Station ash dam changed stabilisation layers to reduce carbon footprints by 85%, reduction of costs by 34% using waste and by-products within 10kms of the project to replace 90% of the cement (reuse of waste and by-products into product of approximately 350 000t). • New Denmark Coal Mine is the first application of affordable mine support in a coal mine using long-line technology. A reduction of 80% carbon footprint was realised by using by-products and wastes with a cost reduction of approximately 40%, making mine support for coal mines feasible. • Kangnas and Perdekraal East Wind Farm’s foundations used a 70% replacement of cement.
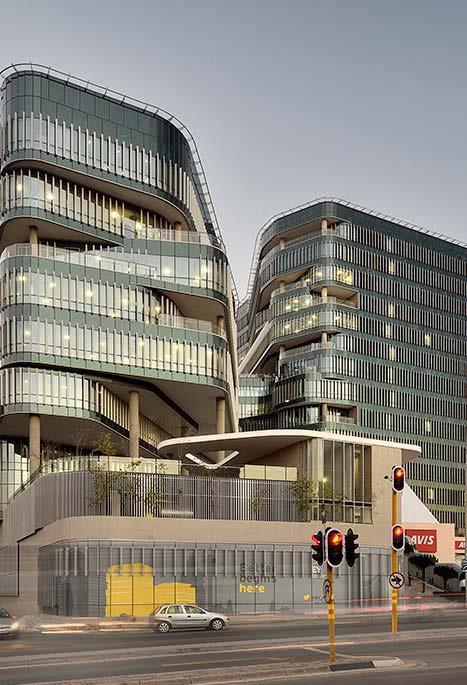
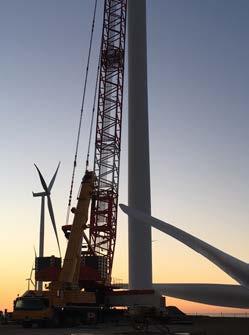
102 Rivonia in Sandton.
• At the Khobab Wind Farm, a four-star eco-product label has been awarded for the low-cement concrete used to build the wind turbine bases achieved by substituting cement with ground granulated blast furnace slag (GGBFS) or fly ash from the steel works at Saldanha Bay.
The average carbon footprint on the bases at the Khobab Wind Farm was 90.7kg.CO2/m³. The average carbon footprint for a standard 30MPa readymix concrete base is from 290 to 340kg.CO2/m³. Eco Standard also commended the use of recycled water in this application in the water scarce region. These projects represent a fraction of infrastructure in South Africa and the uptake of geopolymers has been slow while the country landfills hundreds of millions of tons of ash and slag to the detriment of the environment. The problem is an absence of national standards covering the use of geopolymers, and consulting engineers are reluctant to sign off on projects using materials that do not meet current national standards because of the high risk involved if the material fails.
One cubic metre of concrete has a carbon footprint of 350kg of CO2, making this staple material in the construction industry one of the biggest contributors to greenhouse gases in the world.
While we wait for standards to be adopted, this does not mean there is no more that can be done in South Africa. The opportunity for substitution of ingredients to make concrete, rather than cement/clinker, are where gains can be made. Here, cement replacement is becoming more common. This provides massive carbon offsets, significant cost benefits, options for using recycled water, landfill diversion benefits of problematic waste streams and associated negative environmental impacts, improved resistance to fire and aggressive chemicals, and a host of other benefits.
We need to make changes to national standards, material specifications, as well as procurement and supply chain policies to drive the uptake of alternative low-carbon alternatives to meet this country’s international obligations to driving a low-carbon economy through the Paris Climate Agreement and UNFCCC. The fact that South Africa has world-leading scientists in these fields means that we should be leading the race.
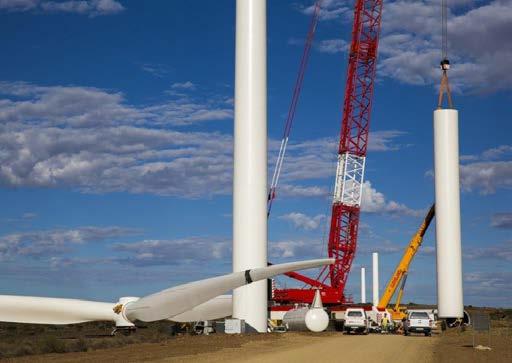
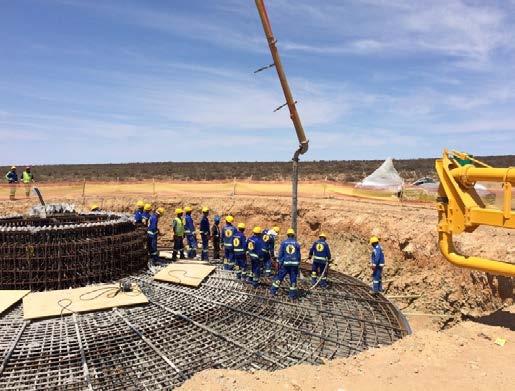
Loeriesfontein Wind Farm is the first high-fatigue structure in the world that will be constructed with 100% cement replacement.
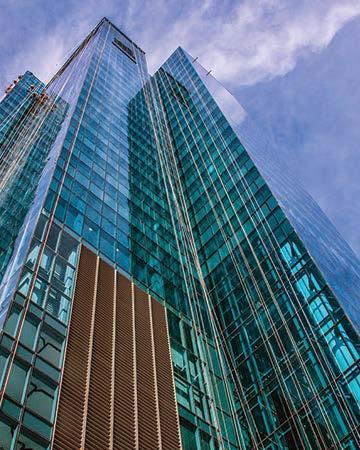
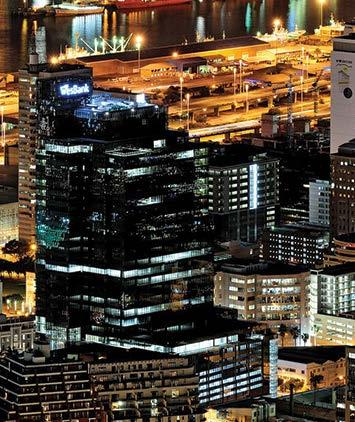
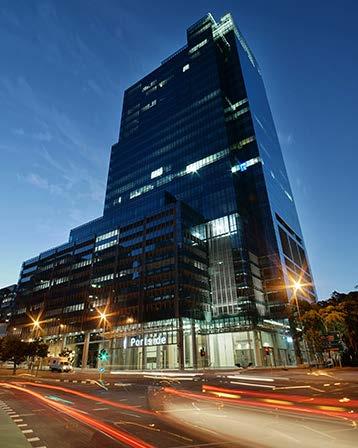
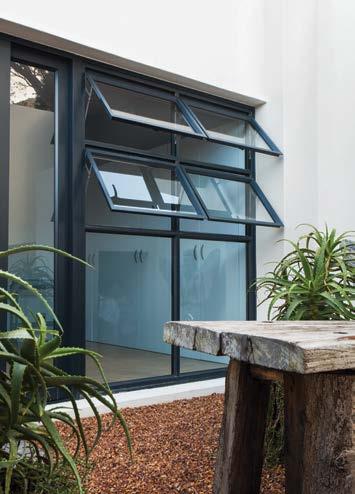
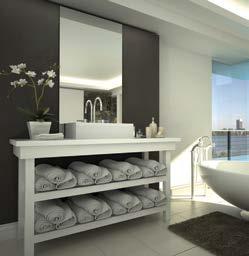
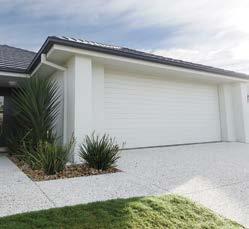
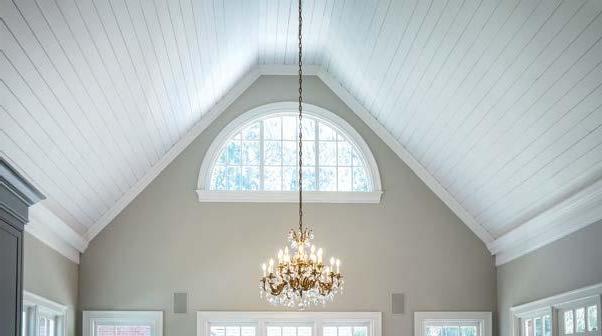
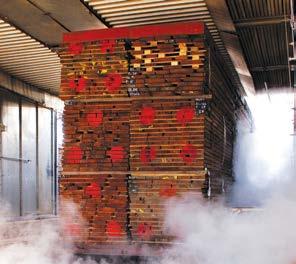
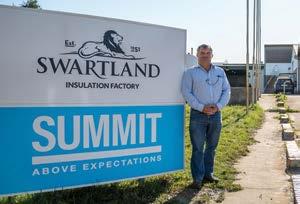
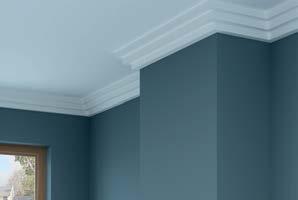
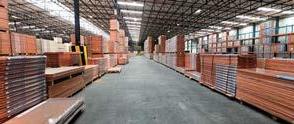

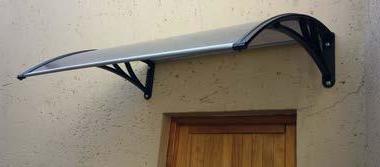
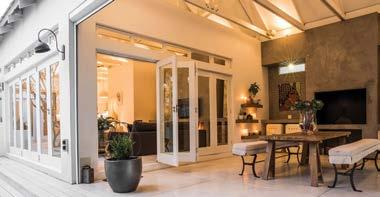
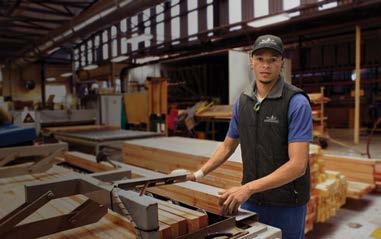
70 years of building together.
In the last 70 years, the Swartland Group has become one of the largest suppliers of quality products to the building industry.
Our national distribution footprint comprises two Swartland and seven SBS depots, and more than 42 000m² of warehouse space, situated in all major centres in South Africa.
Our class-leading products include wood and aluminium windows and doors, PAR timber, skirtings, fi nishes, manufactured products, cornices, garage doors and automation, and most recently, XPS insulation board.
Staying at the forefront of technology, design, and production effi ciency, our ongoing research and development drive continuous improvement and our exciting expansion into new categories.
Our customer promise ‘Experience Quality’ is not just a slogan. It’s our commitment to holding ourselves to the highest standards, and to ensuring that every experience with us is a quality one.
Quality doesn’t only apply to our products, it’s infused in every facet of our business, from our admin staff to our service teams.
We encourage our people to look past their computer, their production lines and know that they’re part of a greater mission to deliver quality to the homes of millions of South Africans.
CERTIFIED