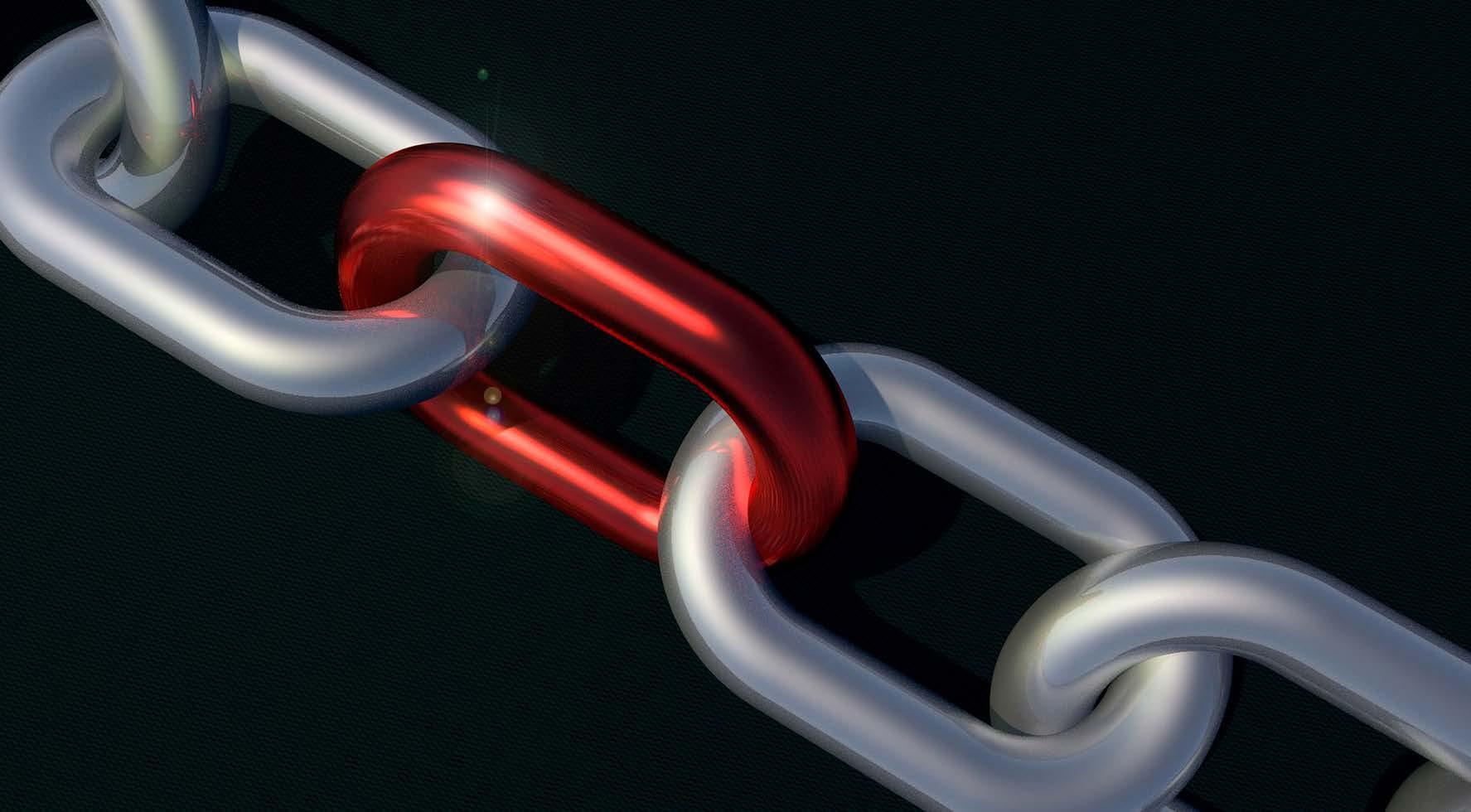
10 minute read
VALUE CHAINS
BUILDING RESILIENCE
IN MANUFACTURING AND SUPPLY CHAINS
Advertisement
Covid-19 is severely disrupting manufacturing value chains, with grave consequences for the global economy. The pandemic has surfaced significant questions about near- to medium-term supply chain resilience.
BY KEARNEY CONSULTING
While traditionally global value chains have been designed around optimising for cost-competitiveness, Covid-19 further underlines the need for companies to orient the design toward “risk-competitiveness”. Certainly, global supply chains have been knocked – and recovered – before, for example from the disruptions associated with past crises such as the 2003 outbreak of SARS, the 2008 financial crisis, or the 2011 Fukushima nuclear disaster. But this time, as it became apparent very quickly, is different.
First, the emergency is a global one. Unlike SARS, Covid-19 spread to all continents and more than 180 countries in the space of only a few months, too quickly for effective mitigating or remedial action. As such, it created a global demand shock.
Secondly, previous crises have typically been concentrated in particular geographies or targeted specific sectors, but Covid-19 affected all major economies. Six of the top 10 world economies in terms of manufacturing value add are also among the hardest hit by the disease (Figure 1).
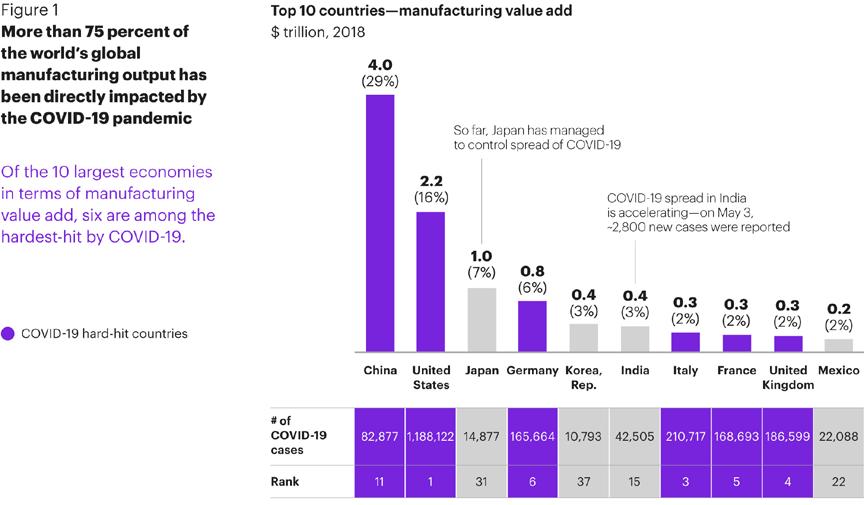
Figure 1. More than 75% of the world’s global manufacturing output has been directly impacted by the pandemic. The colour purple in the graph denotes Covid-19 hard-hit countries. (Sources: The World Bank, Kearney Analysis)
Figure 2: Covid-19 has significantly disrupted supply chain operations. Purple denotes Covid-19 hard-hit countries. (Source: Kearney Covid-19 survey as of 10 April).
Thirdly, the nature of trade between countries, in which the international flow of goods as a percentage of global GDP has steadily increased during the past 50 years, is now highly interdependent. The level of disruption has been amplified, and recovery will take longer. The scale, complexity, and urgency of the situation means that no single body can tackle it in isolation. If industries are to ensure business continuity, protect employees, and shore up supply systems for the future, they will need to find new approaches, share knowledge, and work together like never before.
Recognising this, in collaboration with the World Economic Forum Kearney surveyed more than 400 senior operations and supply chain C-suite executives to codify the current economic impact on value chains, share perspectives on the immediate response to the crisis, and identify the strategies that will be needed to prosper post-Covid-19.
The analysis confirms the level of disruption that has overwhelmed supply chain operations: more than 80% of respondents indicated that Covid has significantly disrupted their own setup, with small businesses the hardest hit (Figure 2).
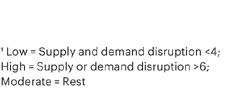

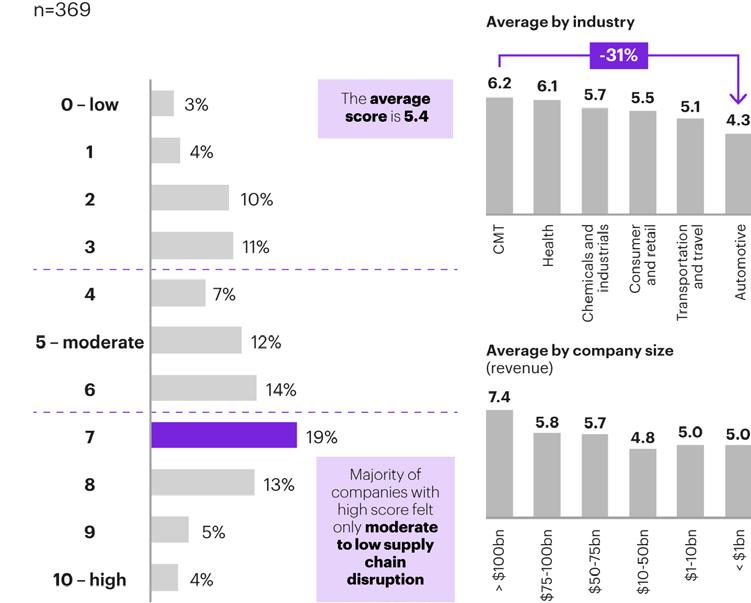
Figure 3. Supply chains have only moderately adapted to the crisis, with automotive facing the biggest challenges. Larger companies’ supply chains adapted better, especially companies with revenues greater than US$50-billion.
When asked to score how much the virus was disrupting their sources of demand, for example changes in key markets or consumer behaviour, and then their supply network, including suppliers and manufacturing centres, respondents gave an average result of 7 out of 10 (Figure 3).
Three stages of activity will be needed to help supply chains back onto a more secure, durable footing.
1. React: immediate actions to ensure business continuity
Taking care of employees was the number one priority for respondents, and a few active measures to protect both physical wellbeing and mental health have been put in place, such as the use of personal protective equipment (PPE), restrictions on employee contact in the workplace, switching employees to working from home, and travel restrictions (Figure 4). None of the 300+ respondents said they hadn’t taken any steps to protect employees.
Companies are also supporting suppliers, customers, and society at large. Suppliers have been given a helping hand in various ways, from advances or premium payments to guaranteed purchase promises. Many firms have repurposed their production lines to produce masks, ventilators, and other much-needed goods; turned to new types of transportation; or prioritised orders for vulnerable customers.
Employee protection
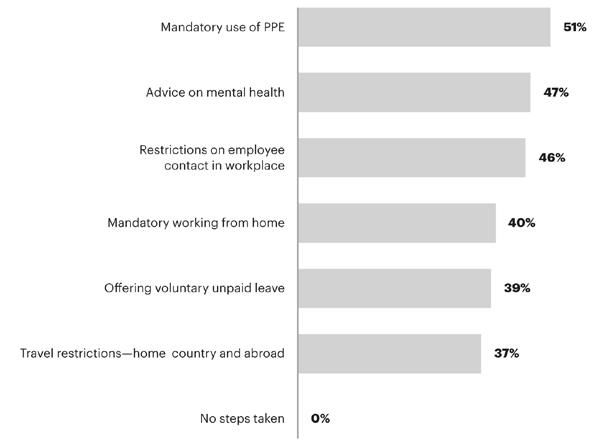
Source: Kearney, COVID-19 survey (as of April 10)
Figure 4: Companies are actively taking measures to protect employee wellbeing.
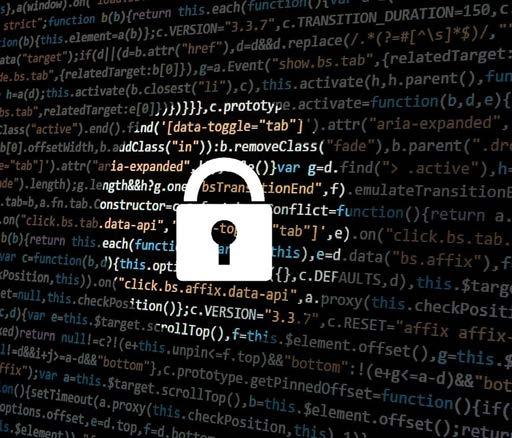

Figure 5: Leading companies are taking action to mitigate impact on customers. Nine out of 369 surveyed companies had not taken any action to support customers.

One area that could improve significantly however is adapting delivery methods to ensure minimal human contact: only 40% of respondents had put these measures in place (Figures 5 and 6).
“We see many companies sharing intellectual property – for example, 3D/CAD design files – to allow other companies to also produce ‘their’
products to ensure sufficient supply of high-demand goods.” - Chief commercial officer, technology company

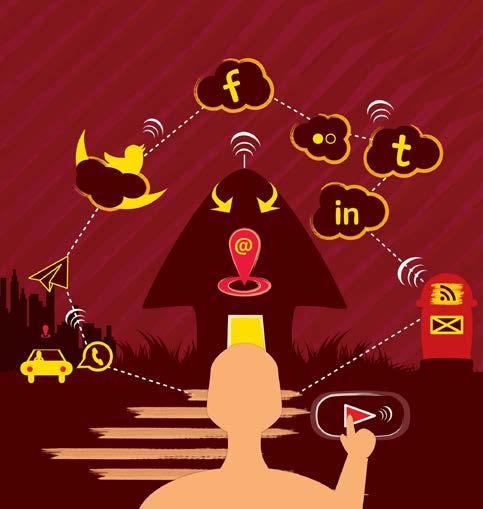
2. Recover: strategic longer-term initiatives to increase resilience
Current supply chain configurations are seen as ineffective. Fortyseven percent of executives surveyed indicated a need to overhaul manufacturing and supply network to increase future resilience. Supply chains are too long, too complicated, and too often exposed to tier-2 and tier-3 supplier vulnerabilities in a single source supply. Each of these factors adds risk, especially in a crisis. Businesses are starting to shift their focus away from cost and toward being risk-competitive instead.
To make their supply chains more effective in the medium term, businesses are looking to reduce complexity, increase their use of local suppliers and manufacturing capacities, and diversify their supply base to protect supply (Figure 7).
Business leaders also noted the role that advanced technologies such as artificial intelligence, data analytics, 3D imaging, and additive manufacturing played as a crucial way of arming themselves to face the future and adapt to potential disruptions in supply and demand. This presents a huge opportunity, as the companies who are already making most use of high-tech tools are demonstrably able to adapt their supply chains in the face of Covid-19 better than those that don’t.
“Technology and digitalisation enable end-to-end visibility across the supply chain. Having this visibility – ideally in real time – is key to proactively run risk analyses and react fast when a crisis hits. We
are currently accelerating multiple initiatives in this area.” - Head of procurement, healthcare company
Key changes to supply chain setup
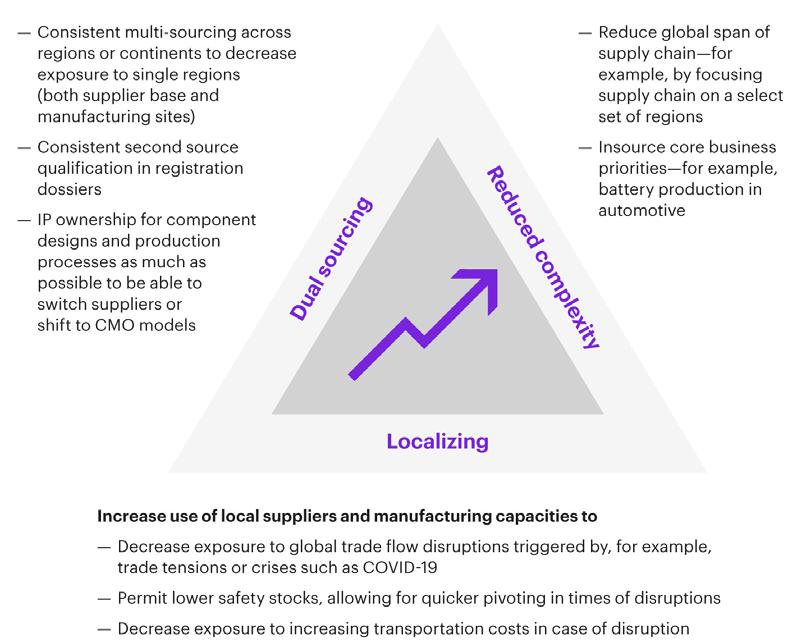
Figure 7: Dual sourcing, reduced complexity and localising are the three key changes that executives are evaluating. The three levers are highly interdependent (for example, dual sourcing often implies increased complexity). Safety stocks and resources in supply chain departments will be rammed up.
Unsurprisingly, the ability to adapt to changing demand and manage risk better are two of the top priorities for businesses coming out of Covid19, especially in areas with highly complex supply chains, such as industrials, healthcare, and automotive (Figure 8). As for future operating models, remote working is here to stay, with an average of 20% of businesses across sectors considering permanent work-from-home solutions. A shift toward decentralisation is expected, enabling organisations to be more flexible and make decisions quickly.
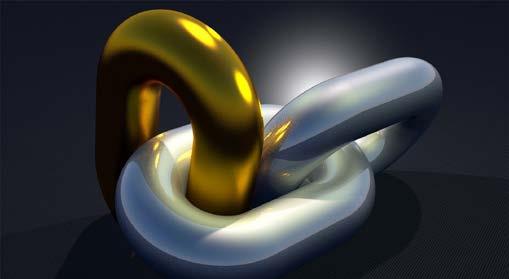
Because we’re better together.

Figure 8: Upskilling people and having a consistent riskmanagement system in place are key to ensure higher resilience. Changes to the operating model must cover all four dimensions to ensure smooth implementations. Covid has changed our ways of working, which makes changes to the operating model inevitable.
Relationships will also change. Many companies supported their suppliers throughout the pandemic, deepening the bonds between them. These vital connections are perceived as an important way to secure supply during turbulent times. New collaboration models are also on the table. Within and across industries, organisations have come together to share practices, come up with new solutions, and keep elements of the economy moving. Not every business will survive, and like other periods of financial difficultly, consolidation may follow.
3. Reinvent: key imperatives to adapt to potential “forever” changes
With widespread disruption already present due to emerging technologies, climate change, and geopolitical tensions, it’s clear that the pandemic is acting as an accelerator. Businesses will need to consider five key imperatives if they’re to succeed in the long term: 1. Be rapid response ready. The crisis has forced a change in consumer preferences by removing most in-person contact. Existing trends toward personalisation and sustainable shopping mean it’s likely that manufacturing and supply systems will need to be able to adapt to further changes in behaviour. Becoming more sensitive to demand through increased use of technology and data analytics will be crucial. 2. Adopt high-tech habits. Companies best placed to adapt during the crisis were those that were able to make use of advanced technologies. This will only take on more importance as further developments emerge. For example, additive manufacturing makes it possible for goods to be produced directly in the setting where they’re most needed, while automation and advanced robotics are increasing production flexibility and making it easier to switch products across manufacturing locations. All of this points to a shift toward distribution and manufacturing, rather than the other way around. 3. Think global, act global. At the height of the crisis, some supply shortages were caused by lack of capacity. By coordinating logistics within and across global value chains and using new technologies to enable much better visibility across the entire ecosystem, similar headaches could be avoided. Connecting other applications such as blockchain and IoT sensors together could also speed things up, for example by reducing customs clearance time.
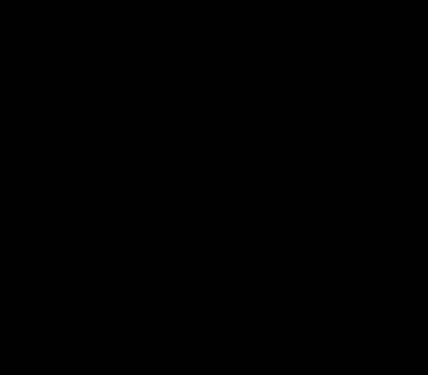
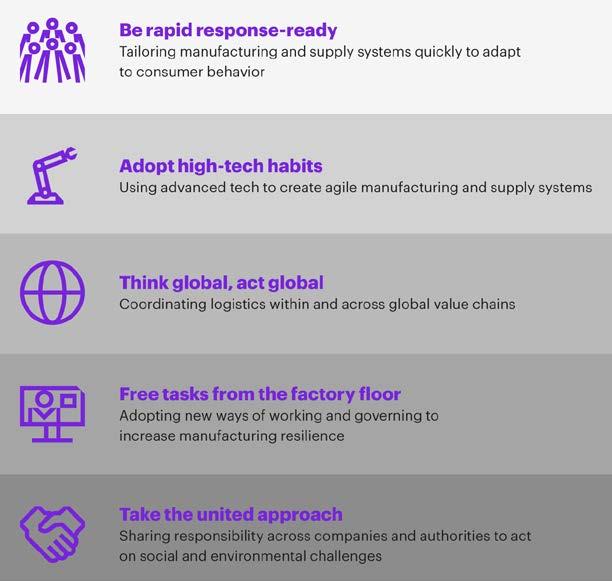
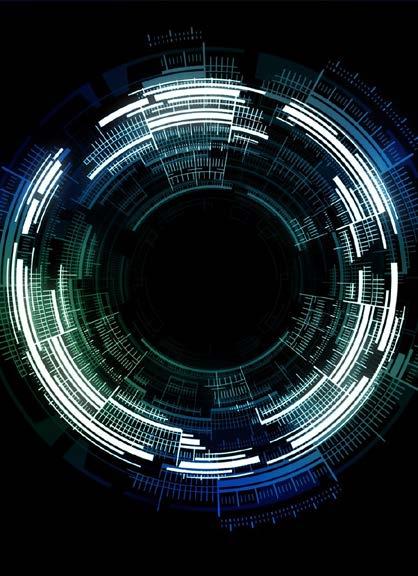
Figure 9: New imperatives will emerge from Covid-19, posing significant challenges and opportunities for businesses.
4. Free tasks from day-to-day operations. Although home working has been adopted at breakneck speed out of necessity in many organisations, the shift needed to make it a success is as much psychological as it is physical. While executives reported a certain level of cultural resistance to remote working, becoming equipped to cope with potential future disruption, like successive waves of Covid-19 or outbreaks of other infectious disease, is of vital importance. Virtual and augmented reality could provide the means to enable key tasks or carry out employee training from outside the factory. 5. Take the united approach. Fighting Covid-19 has driven new levels of collaboration, for example speeding up the delivery of medical and essential supplies and getting temporary clinics and hospital facilities set up to operate in record time. This experience could be used and adapted as we attempt to tackle other challenges such as climate change. While this has been a global crisis, it is not a crisis of globalisation. By working together, stakeholders can influence the changes and take the actions needed to bring about the bestpossible solution to navigate the new global scenario (Figure 9).
If the pandemic has taught us anything, it’s that when we are truly put to the test, we are capable of astonishing achievements. Hospitals can be built in a few days. Entire operating models can change. And collectively, we can do what matters most. By continuing to collaborate, a manufacturing and supply system can be built that’s more robust than ever. Because we’re better together. Article courtesy: kearney.com
READ REPORT
THOUGHT [ECO]NOMY
greeneconomy/report recycle
HOW TO REBOUND STRONGER
FROM COVID-19 | Resilience in manufacturing and supply systems
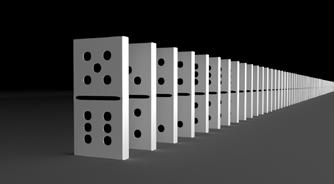
| White paper produced by Kearney Consulting and the World Economic
Forum [April 2020]