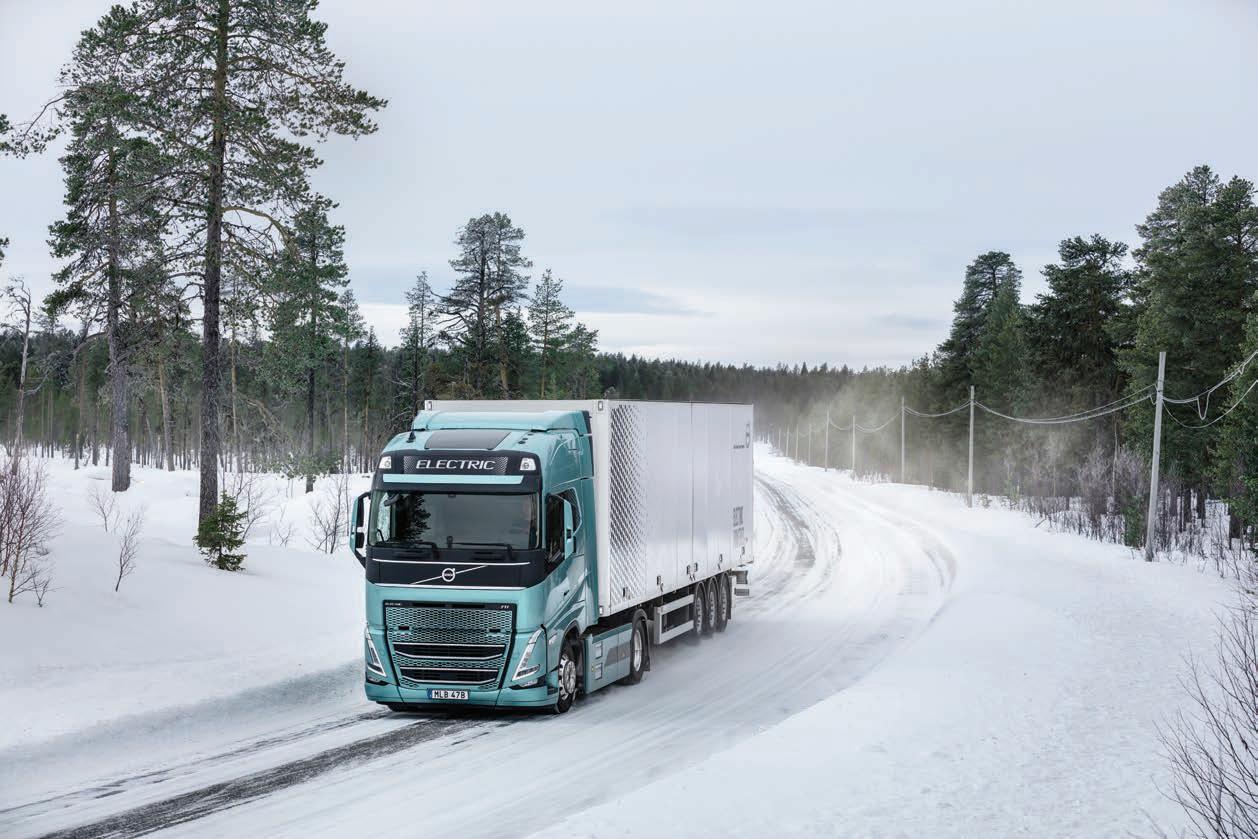
8 minute read
Volvo Gets a Grip
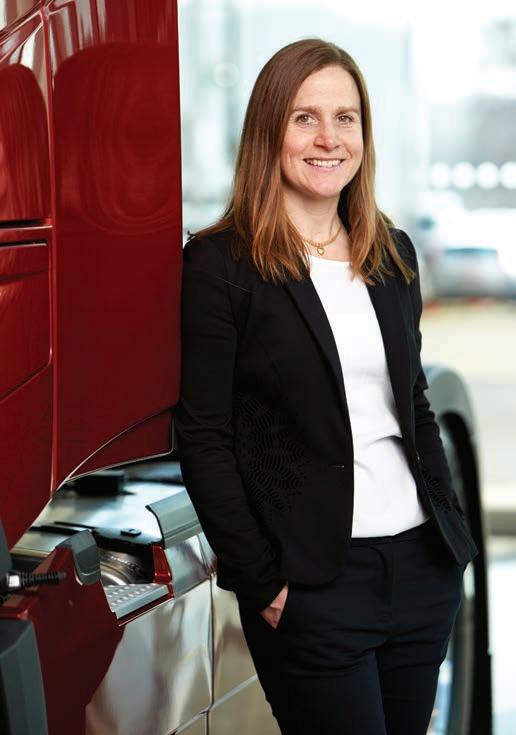
Anna Wrige Berling, Traffic & Product safety director at Volvo Trucks, says electric drive technologies will offer big safety and performance improvements in slippery gravel conditions. the risk for jack-knifing and oversteering when driving unloaded.
“With Active Grip Control we are giving our drivers further improved ability to traverse difficult roads and terrain – even during the most challenging of conditions. This is a unique function that Volvo Group has protected by patents,” Anna Wrige Berling explains.
Improvements can also be seen when braking, as the function can be used for controlled regenerative braking without going into ABS. This increases efficiency, since more time is spent in regeneration, allowing for a smoother braking experience.
The Active Grip Control feature will be available on the heavy-duty Volvo FH, Volvo FM and Volvo FMX Electric trucks, that are used for regional haul and construction operations. A version of the feature will also be available on trucks with a diesel or LNG driveline.
Volvo Trucks already has a range of six all-electric trucks designed to cover a wide variety of different transport assignments.
Its FH, FM and FMX Electric models are heavy-duty trucks with a gross combination weight of 44 tonnes. Sales are ongoing in Europe and production will start in the second half of 2022.
Serial production in Europe of the Volvo FL and Volvo FE Electric, for city distribution and refuse handling, started in 2019 and sales of the Volvo VNR Electric for North America began in December 2020.
The pace of development in the electric truck sector is reflected in the launch of an enhanced VNR Electric
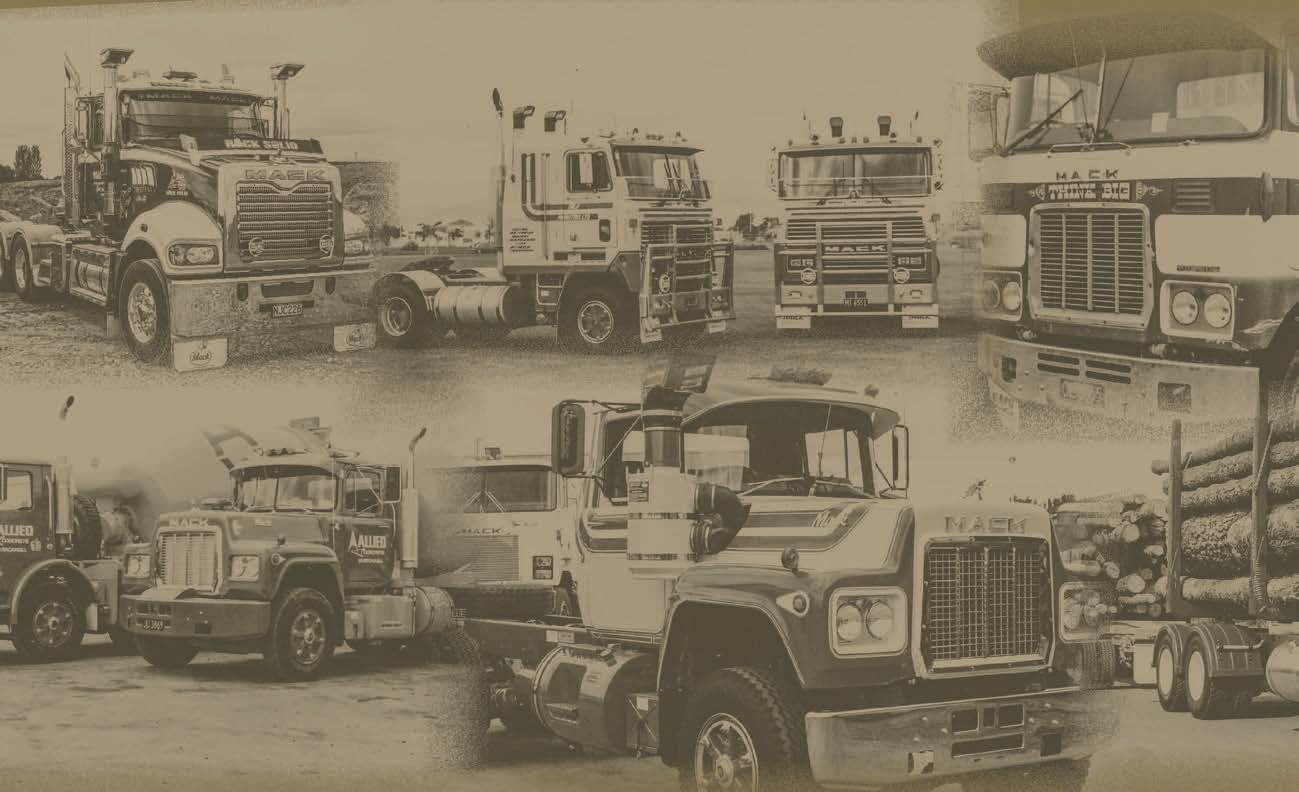
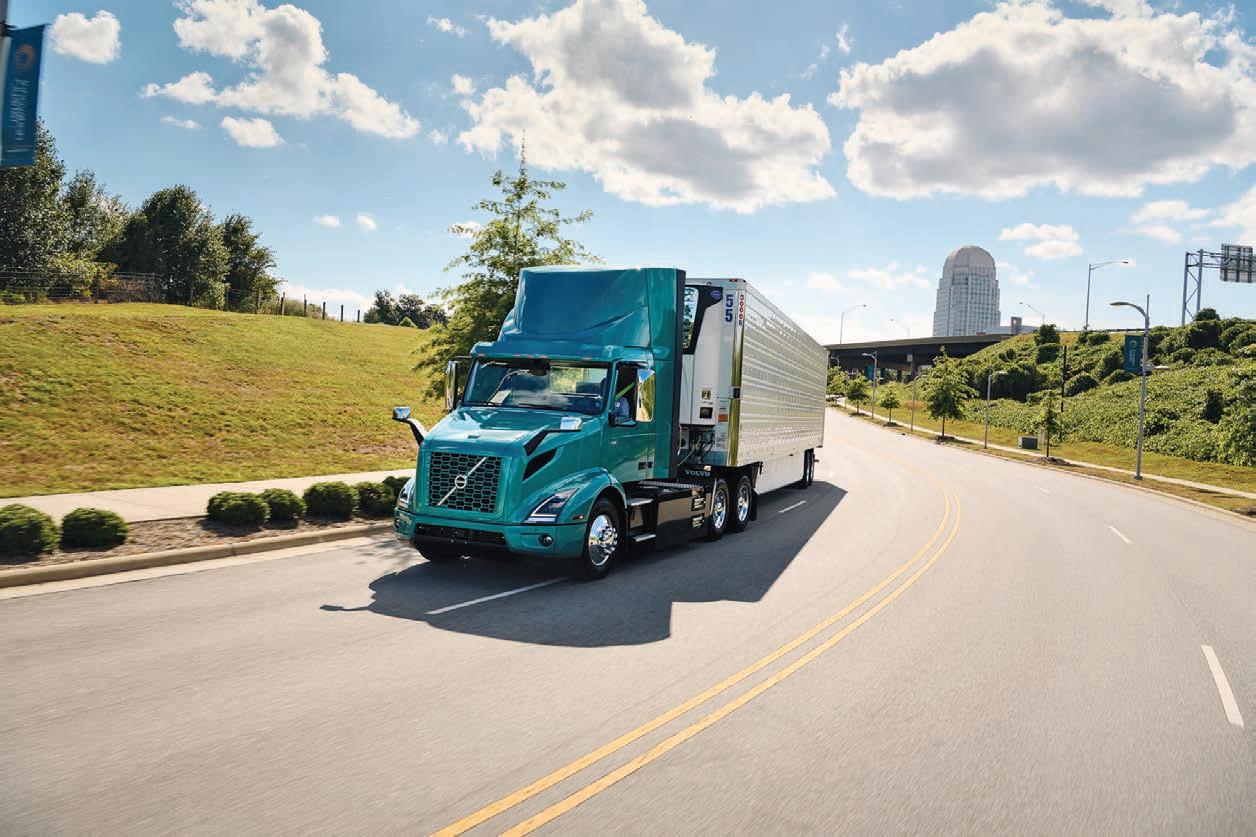
1972 - 2022 50 GOLDEN YEARS OF KIWI TRUCKING.
A second generation version of the Volvo VNR Electric has increased battery capacity and now boasts an estimated range of 440 kilometres.
Volvo Trucks’ global target is for electric models to account for half of all the trucks it sells by 2030.
1972 - 2022
which offers a significant increase in battery capacity and range.
New battery options achieving an 85% increase in range along with faster charging capability are features of the second generation VNR Electric announced recently. In the gen-two specification, the VNR Electric now boasts an estimated range of 440 kilometres.
The first generation VNR Electric had an operating range of up to 240km. Increased energy storage (now up to 565kWh) along with an improved battery design and a new six battery package option are delivering the improved performance.
The new Volvo VNR Electric also reduces the required charging time. The increased 250kW charging capability allows an 80% charge in 90 minutes for the six-battery package, and 60 minutes for the four-battery version.
“It is a testament to Volvo Trucks’ leadership in a continuously evolving industry that we are bringing Truck & Driver | 91
the enhanced version of our VNR Electric to the market only a year after sales of the VNR Electric first started,” said Peter Voorhoeve, President, Volvo Trucks North America. Production of the enhanced Volvo VNR Electric will start in Q2 2022 in the company’s New River Valley plant in Virginia, which is the exclusive producer of all Volvo trucks in North America. Globally, Volvo Trucks has set the target that electric models will account for half of all Volvo trucks sold by 2030. “We are determined to lead the transformation of the transport industry,” says Roger Alm, President Volvo Trucks. “In only eight years’ time, our goal is that half of our global truck sales are electric. The interest among customers is high, and it’s quickly becoming a competitive advantage for transporters to be able to offer electric, sustainable transports. That is very encouraging,” T&D Register your interest to bring your Mack to our huge anniversary truck show. 22 October 2022, Manfeild Park, Feilding. 50years.macktrucks.co.nz 50 GOLDEN YEARS OF KIWI TRUCKING.
After gaining good experience with a Volvo FE Electric (above), Unicon is now taking the next big step towards emission-free distribution with plans to order 11 FM Electric (below) trucks for concrete work.
Volvo’s concrete plan
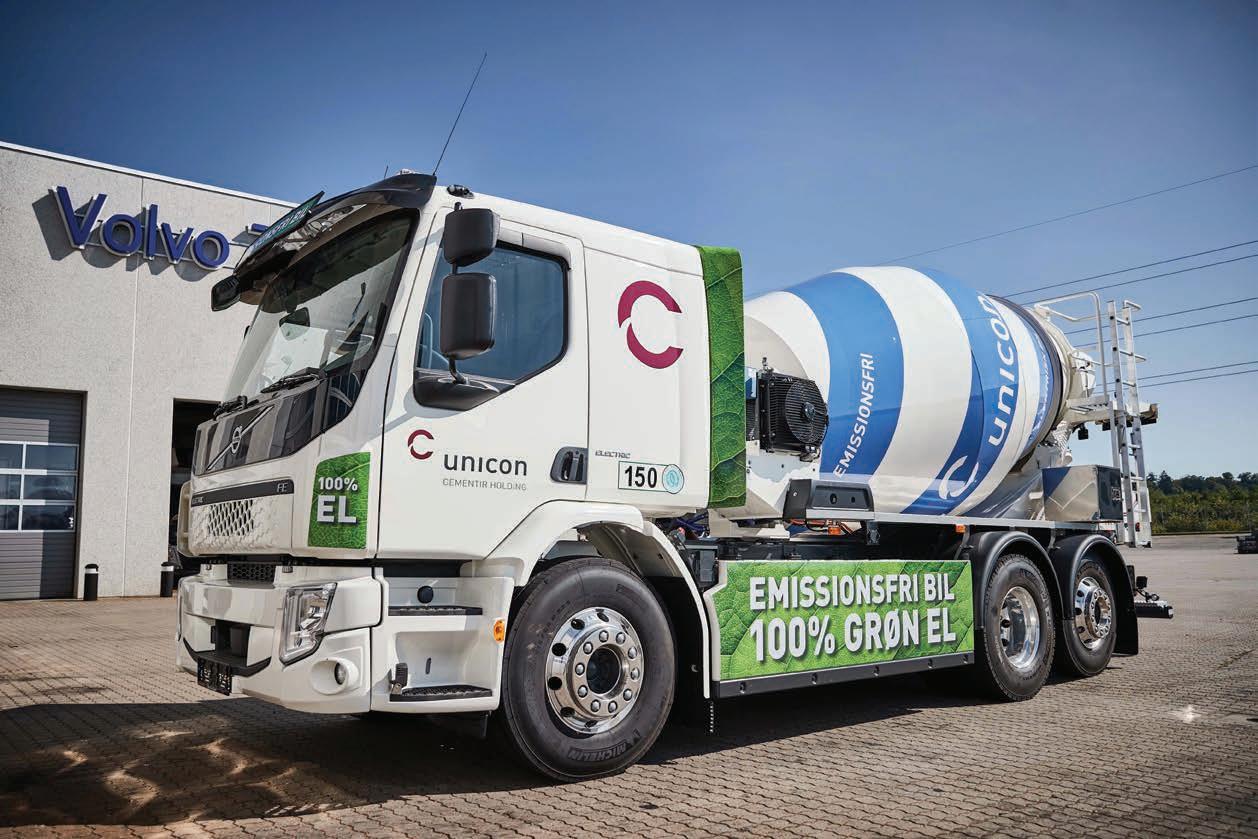
VOLVO TRUCKS IS TEAMING UP WITH A DANISH CONCRETE FIRM
to overcome one of the more difficult applications for electric trucks.
Concrete mixers present a considerable challenge for electrification because of the heavy loads and mixing demands.
Unicon, the largest producer and supplier of ready-mixed concrete in Denmark, has announced plans to order 11 Volvo FM Electric trucks that will be converted to truck mixers and operate in Denmark.
It’s the largest private single order to date for electric trucks that will run on Danish roads. The trucks will start being delivered at the end of 2022.
In addition, Unicon and Volvo Trucks have agreed on a long-term collaboration that aims to develop and implement complete truck and body electric solutions for the sustainable distribution of ready-mixed concrete.
“With this major order and ambitious collaboration agreement, we are putting tangible actions behind our CO2 emission targets for our distribution,” says Christian Elleby, Supply Chain and Procurement director at Unicon.
“This clearly underlines our role as a frontrunner for the construction industry in both Denmark and worldwide. We are very much looking forward to this collaboration with Volvo Trucks, which gives us unique opportunities to jointly develop the right complete truck and body electric solutions for our distribution.”
Peter Ericson, managing director of Volvo Trucks in Denmark, says that because heavy vehicles for the concrete industry are among the most difficult to electrify, the company expects to learn a lot from this collaboration.
“With these agreements, we are taking important steps in expanding fossil-free distribution solutions to the concrete industry, where electrification of heavy vehicles has been a very difficult challenge due to the heavy loads and continuous mixing demands,” says Ericson.
“We are pleased to have Unicon on board as a strategic partner and we expect a lot of learning and development as a result of the collaboration for the benefit of an entire industry.”
Unicon believes that electric truck mixers offer the most obvious technology for achieving ambitious sustainability goals. This applies both in relation to supporting emission-free distribution of readymixed concrete and for creating a better and even safer working environment on construction sites.
“With the new electric truck mixers, we are ready to support the requirements for emission-free construction sites in Denmark, which we see from the City of Copenhagen, as well as an increasing number of contractors and builders,” Elleby says.
Unicon is Denmark’s oldest and largest producer and supplier of ready-mixed concrete with 35 factories producing about 1 million cubic meters of concrete annually.
It operates a fleet of 195 trucks and has defined a target to reduce CO2 emissions from its fleet by 30 percent in 2025 compared to 2019 and has a clear strategy to make its fleet of truck mixers emission-free in 2035. T&D

New home for TransDiesel
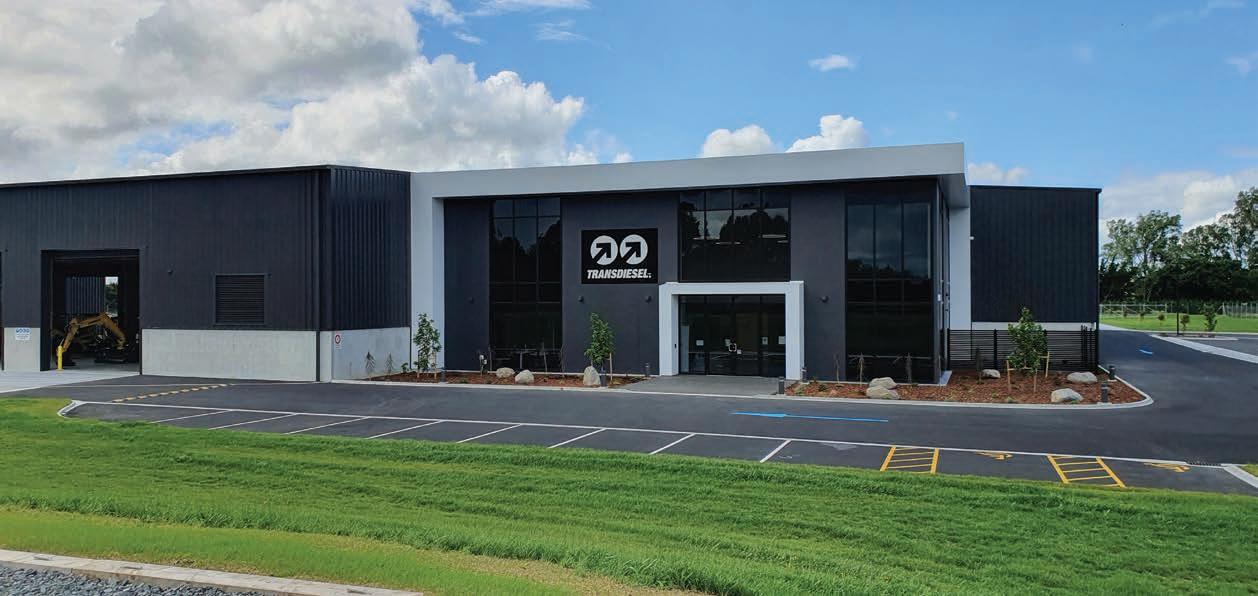
SPURRED BY THE DEVELOPMENT OF THE WAIKATO
Expressway, Hautapu is becoming an increasingly vital transport industry and manufacturing hub.
Recently finding a new home just to the east of Cambridge is TransDiesel, a leading supplier of construction equipment, diesel engines and transmissions to the heavy-machinery industry.
TransDiesel has opened a new national distribution centre at 219 Peake Road, Hautapu. Located adjacent to the Waikato Expressway, the new facility takes advantage of the location to enhance the service offered to customers throughout the country.
“The new hub represents a significant investment in all-new infrastructure at a greenfields site and demonstrates our ongoing commitment to our customers,” says Mike McKessar, TransDiesel CEO.
“It offers multiple benefits to our clients and will enable many associated positive flow-ons, ranging from improved customer service, enhanced satisfaction thanks to shorter wait-times as well as employment for local residents.
“All of the new construction has been done with environmental considerations in mind, with the new facility showcasing a number of sustainability-oriented features.”
The new facility will provide a consistent supply chain solution by relocating product to a more cost-competitive in-house solution, in turn enabling better controls and stock management.
The recently upgraded Waikato Expressway runs past the national distribution centre’s front door and, with 80% of the freight originating from the Auckland port, will enable TransDiesel to offer national coverage in a timely manner.
Furthermore, the additional space and the central location will give the facility the added advantage of being able to use the new infrastructure investment being made around the Tauranga port upgrades.
Among the first inventory items to arrive was 500,000 litres of Shell products and in coming months, 2,600-plus pallet spaces in the warehouse will be utilised as the new facility comes online.
“There will be three warehouse staff to start the process and there will be additional employees required to keep pace with future growth,” McKessar says.
“From a TransDiesel perspective, the number of employees in the region has now risen to six technicians. I am sure this number will climb as demand for products increases alongside sales and market growth.”
The distribution centre sits on a four-hectare sire and boasts 170m of road frontage, making it easily recognisable from the Waikato Expressway. Further expansion is possible with an extra hectare of land available onsite for development as and when required.
TransDiesel has placed sustainability initiatives to the fore at the new location.
Rain water is harvested from the roof and collected in five 30,000-litre tanks. These tanks, operating in conjunction with a bore water supply, will enable the facility to be self-sustaining for water and will be the primary method of water use onsite.
A clever waste water system under the ground will manage the stormwater in an environmentally effective way, and after the filtration process the water can be used through the facility operations.
An innovative Kingspan warm roofing system also assists the building to manage seasonal variations, helping keep employees warm in winter by retaining heat within the building and cool in summer by reducing the solar gain.
LED interior lighting is another feature used to reduce running costs which are estimated at 70% less than a traditional high-bay light system. T&D
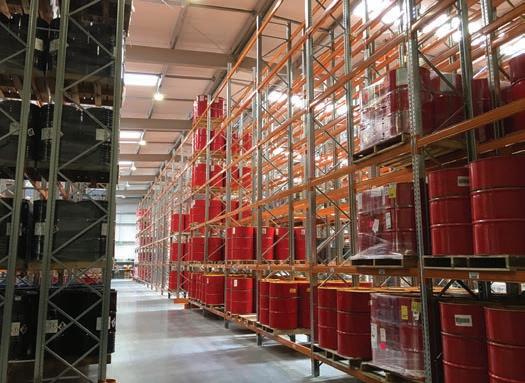
The new distribution centre at Hautapu will house 500,000 litres of Shell products.