
13 minute read
Mobile Brake Testing
CVST staff will soon have six of the new Mobile Roller Brake Test units in service around New Zealand.
Brake testing goes mobile
By Dave McLeod
New CVST mobile roller brake testers will improve road safety and reduce the risk of a serious injury or death on our roads as a result of a heavy vehicle brake failure.
BEGINNING JUNE, NZ POLICE COMMERCIAL VEHICLE SAFETY
teams (CVST) will be able to identify brake failures anytime, anywhere thanks to six new BM20200 mobile roller brake testers (MRBTs) being rolled out nationwide.
CVST Acting Inspector Lex Soepnel told NZ Truck and Driver; “New Zealand road toll stats are a lot higher than the rest of the world and one of the points that has come out of the ‘Road to Zero’ campaign is the need for safer vehicles on the road, particularly commercial vehicles.
“We want the vehicles on the road to be safe - there’s no compromise, and as you’d appreciate, brakes are a very important safety device.”
To emphasise the point, Soepnel says that during the research stage they used the Paengaroa CVSC (as it’s the only location that currently has a CVST operated roller brake test machine) and between 2018 and 2021 they tested 2500 trucks with 67% failing the test!
“Now bear in mind this is a fixed ‘in-ground’ test at the station there [not a mobile one], so it’s known there’s a safety centre there, and we were still getting a 67% failure rate,” Soepnel says.
He says the results prompted them to go mobile.
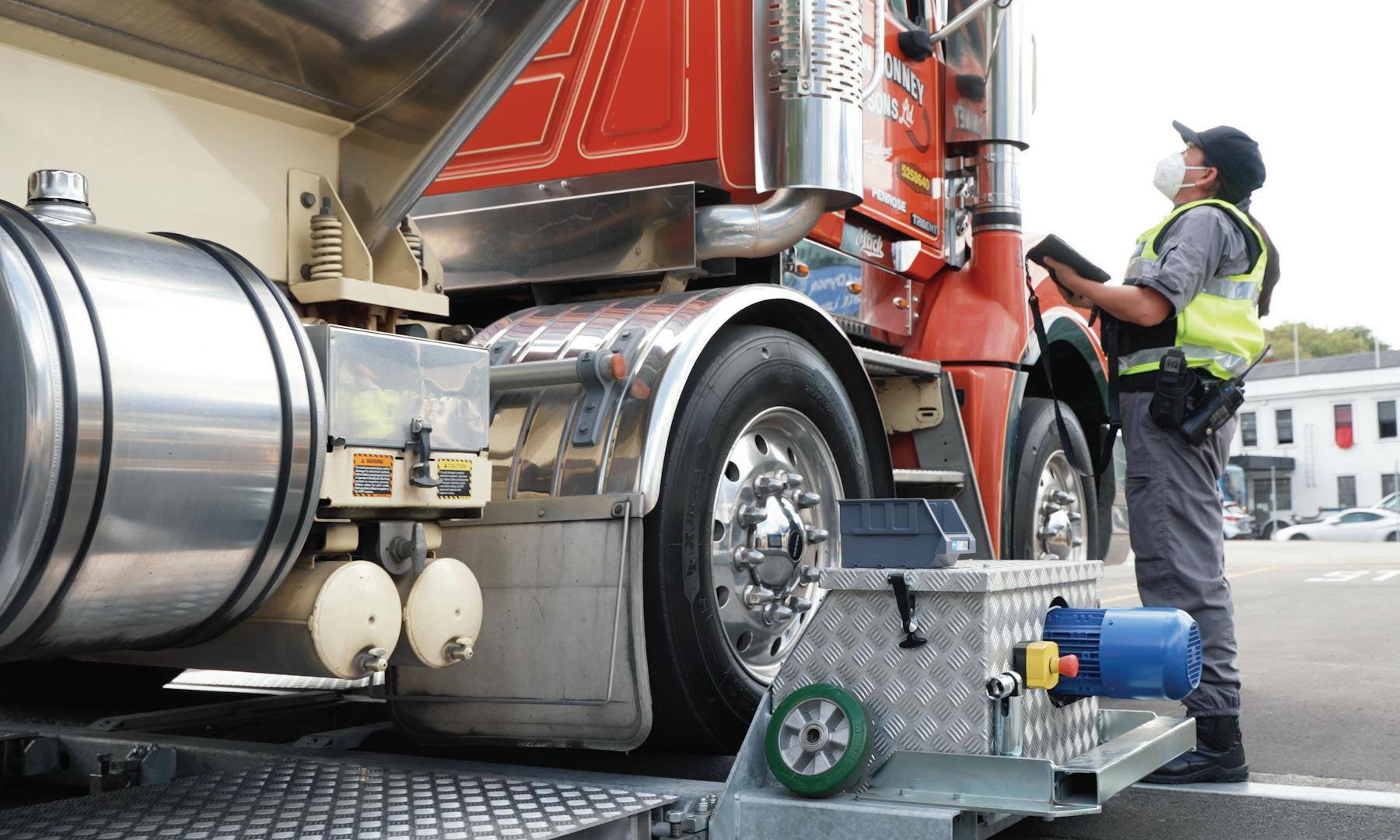
The rollers are set up 160mm above the ground, differing from the machines in the testing station which have bigger diameter rollers, but delivering the same results.
“Places like the deep South or far North, or East to West, some of the vehicles there, the only time their brakes get tested or possibly maintained is when they go for their Certificate of Fitness.”
Soepnel says that although COFs are thorough, it’s the time between them is often the issue.
“Many COFs are on a six-monthly basis, and what we’re finding is that a lot of vehicles are lacking in maintenance or failing COFs largely due to brakes. You must remember that some of these vehicles do a considerable amount of mileage between COF checks.”
Soepnel believes that the solution lies with testing the brakes on the road and hence the introduction of MRBTs. And as it turns out, this is not the first time NZ Police has ventured down this road.
Brett Higgins, National Equipment Manager from the successful tender supplier Sulco Tools and Equipment explains.
“Previously, the police had four mobile brake testers in trailers with a dedicated tow vehicle that had a generator inside. They tested roadside around the country.”
However, Higgins understands that with the introduction of the 2006 Industry Operator Rating System and the introduction of the Heavy Vehicle Brake Rule (where they went from unladen brake testing to laden during COF B brake testing) they decided to do away with them.
“But in 2020/21 they [NZ CVST] went to tender for the supply of six new roller brake testers. The tender requirement was for a mobile roller brake tester to work roadside that had the capacity to test fully laden vehicles,” recalls Higgins
“It needed to be in a self-contained trailer with the generator and [an overall] weight around 3000kg. It needed to be able to be set up with just two people and be ready for operation within 15 to 20 minutes of arrival to site.”
Soepnel says; “What we’re doing with the roller brake machines is trying to meet that safety need by testing brakes, particularly in heavy motor vehicles, on the go. This will complement the ‘Road to Zero’ programme plus it will also complement the Waka Kotahi ‘Weigh Right’ scheme where they are designing and building more commercial vehicle safety
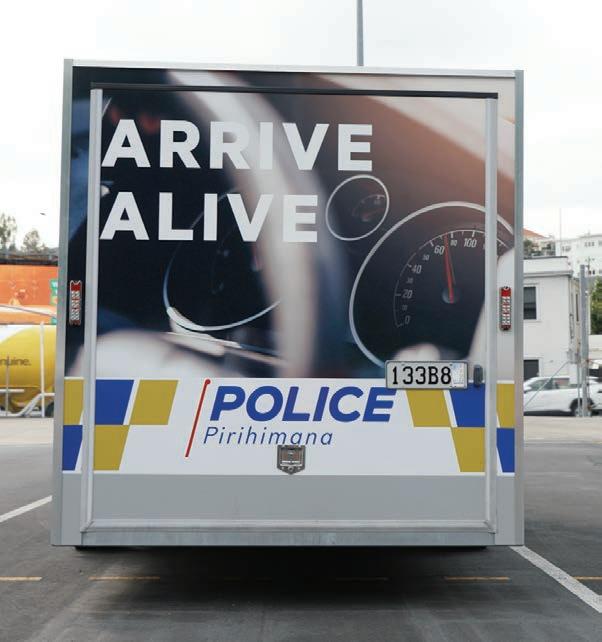
centres around the country.”
Admittedly, these seem like quite hefty requirements, but Higgins, the veteran brake testing supplier, and his company Sulco Tools and Equipment came through with the solution.
“I’ve been with Sulco for 38 years and I’ve been involved in the installation of over 800 roller brake testers in all of New Zealand dating back to 1995,” says Higgins.
Sulco is New Zealand’s largest established supplier of roller brake testers for the car and heavy transport industry.
“Our brake testers are installed in 90% plus of the car and truck vehicle testing centres. We introduced load simulation into brake testing in New Zealand, and we have a bespoke, purposebuilt, mobile roller brake tester that’s capable of testing cars, vans, four-wheel drives and heavy vehicles - trucks, trailers, b-trains, buses, whatever, to a COF-B standard.”
Higgins says mobile brake testing is not new to New Zealand, in fact there’s over 50 in service today for doing either VCAs, COF-B’s, general diagnostic work, or pre-COF brake testing in workshops. Sulco’s clients include the police, vehicle testing stations, fleets, and corporate truck service workshops.
The CVST model (BM20200) is a perfect solution for the job required. Imported from BM Autoteknik in Denmark, it’s equipped with special ramps before and after the brake tester to ensure that the axles being tested are level for accuracy of weight scale reading. Set up roadside it can perform unladen and fully laden tests.
Higgins says that the trailers have been supplied locally by Pinto Trailers and are based on the design of a car transporter.
“It’s a great big box. The trailer tilts and the roller brake tester rolls out of the back. It’s attached to an electrical and mechanical winch so you can release it a bit like launching a boat at the boat ramp and then you can wind it back in. It’s got a generator with PC and printer for recording and capturing the results.”
He adds that it’s also supplied with a wireless hand-held tablet display to display results and remote control for the officer to communicate with the driver.
“It’s a stand-alone system. It’s not talking to big brother. It’s just there to be able to capture brake test results and print them out for each vehicle. A copy is available at the end of the test if the driver asks for it.”
Higgins describes a brake test machine is simply a torque gauge.
“It’s an electronic torque roller bed that’s measuring the torque output of the wheels on the rollers and displaying brake force in Deca Newtons (DaN).”
It performs the equivalent of a COF-B brake test, in a controlled environment, irrespective of weather or terrain conditions.
“It’s set up the same way, to record the same results as if you were presenting your vehicle at the testing station,” says Higgins.
“The only difference is that the roller speed is slower than the machines in the testing stations and that’s purely to do with the motor gear ratio because the rollers are set up 160mm above the ground and the machines in the testing station have bigger diameter rollers, therefore a different roller testbed.
“But irrespective of roller diameter, the mobile RBT can still measure the same torque output because we have a middle roller that’s measuring the wheel speed, and as the brake brings the vehicle to a lock its sensors will shut down the machine safely without any risk or damage to the tyres.”

The BM20200 MRBT system can cope with any shape, diameter and width of tyre and with a full range of suspension and braking systems.
The system works irrespective of brake manufacturer, mechanical or air suspension, and on both ABS and non-ABS vehicles.
“It can deal with any shape, size or diameter or width of the tyre, be it a Mini Minor, a dual set of wheels, super singles or just steering axles, even including Unimogs from the army, with the big knobbly tyres,” says Higgins.
He is adamant that there’s no deviation or no alteration of readings.
“So effectively they’re doing a COF-B equivalent brake test at the side of the road using presented weight. We record the results, and a printout is available. The police officer is looking to make sure that the vehicle is safe, it’s all about safety.”
Higgins says that the key to a successful roadside test is braking nice and slowly to the braking range is measured from low application through to lock.
He confirms that as per Waka Kotahi requirements, Sulco has a nationwide network of third-party servicing and calibration IQPs (Independent Qualified Personnel) and that the machines, weight scales and transducers are calibrated on an annual basis.
“I’m very proud of what we’ve achieved for the NZ Police, NZTA and the transport industry,” Higgins says.
“I’ve been heavily involved with the NZTA and the testing stations and over the years the methods used for testing vehicles within COF-B and roadside are very fair and reasonable tests when compared to other international countries’ testing standards. And these BM20200 mobile brake testing machines are being used by roadside policing authorities around the world.”
Soepnel agrees. “We did have a look at other models, but we found the BM20200 was best suited for our conditions. I have contacted several police forces around the globe that are using them, including Greenland, Denmark, Australia and a couple of others and they have indicated that they are reliable, robust machines.”
The BM20200’s edge roller can test axles up to 16-tonne, which Soepnel says is well in excess of New Zealand’s legal limits of only 8200kgs per axle and are extremely accurate when it comes to reporting failures.
“On the steering axles, if there’s more than 30% imbalance [if one wheel has a brake working and the other one doesn’t] the vehicle could be issued a non-operation order,” says Soepnel.
“And if we’re looking at the braking efficiency of a normal axle, say a drive axle on a truck, if it’s less than 50% braking efficiency then that would be a failure too.”
He explains further. “If you have a series of axles and some are over and some are under, we look at the total braking efficiency of the full unit. So, let’s say it’s a 50-tonne with nine axles, all those nine totalled up together must have more than 50% braking efficiency.”
Higgins goes into further detail. “What are they looking for is ‘do we have brakes? Do we have a brake imbalance between the left and right wheel? Because anything over 30% is a failure.
“And do we have brake force efficiency? Brake Force efficiency is equal to brake force left plus right wheel divided by axle weight. Here we’re looking for a minimum of 50% efficiency for the service foot brake for each axle. In other words, does it have enough braking to bring the vehicle combination to a stop in a safe manner according to the NZTA braking requirements. Park brakes are also tested.”
Soepnel says the MRBT procedure doesn’t necessarily take any longer than a normal Level 3 or Level 5 check and it will depend on the faults found [if any].
“It only takes about 30 seconds to check once it’s up on the roller machines, so it doesn’t take very long, and it won’t add on any extra time to their journeys. No more than at Level 3 or Level 5. In actual fact, the brake test machine will be a Level 6 check which will encompass a Level 5 or Level 3 as well.”
Soepnel says that as of right now they’ve taken possession of two units and that they’re training their VSOs (vehicle safety officers) on how to use them.
“We have a third one just waiting for the livery on the trailer. But soon there will be six units spread out across the country, one for each CVST area [of which there are four], and the other

The system is designed to be operated by two CVST officers and will see brake testing carried out in more remote areas.
two will probably be floating.
“They are towed by a ute so they can go anywhere, anytime. We are very flexible, there’s no set plan as to where they are going to go, but every area will have one assigned to them.”
He says that at the moment all the CVSCs are essentially on State Highways, so the advantage with these mobile brake machines is that they can go to more remote rural areas.
Soepnel is excited about this new safety addition.
“I think it is a very positive step forward. The vehicles are getting heavier, I mean we’ve got 62/68-tonne out there on the highways - this way we’re going to know that at least their brakes work.”
He says that there are more trucks on the road and there’s also a delay in new trucks arriving which means that a lot of the older trucks are on the road longer.
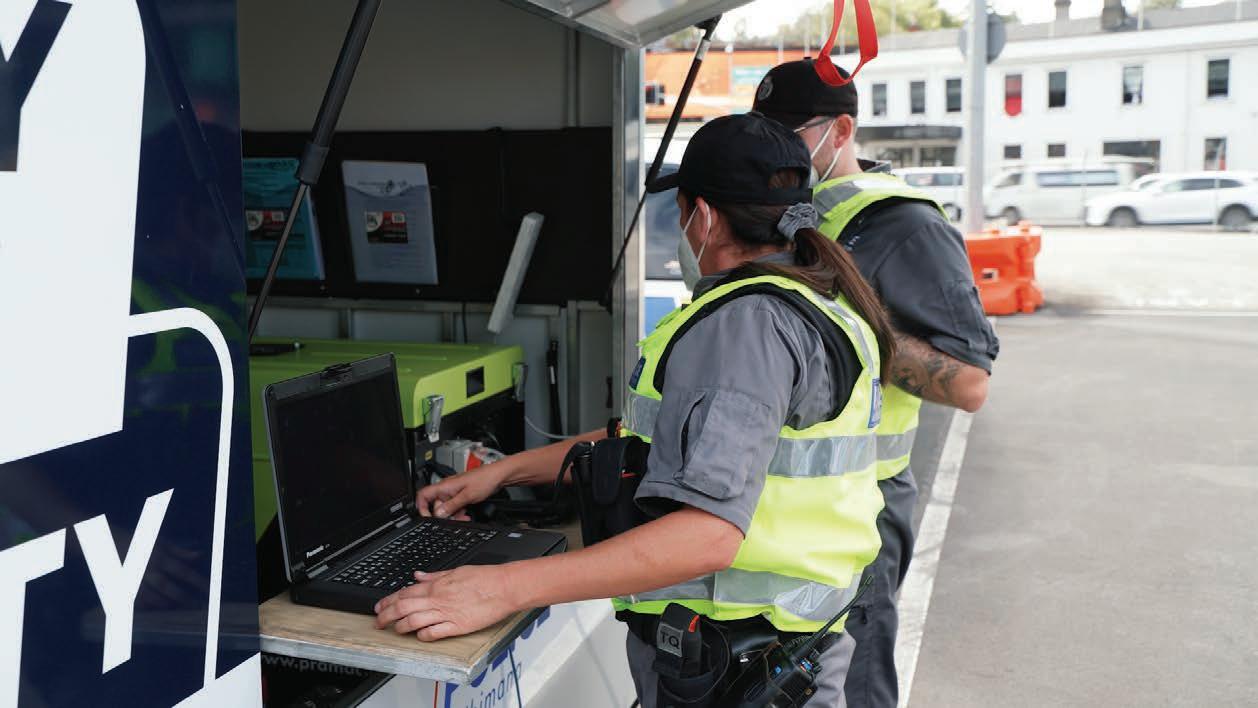
The big thing Soepnel wants to point out is that they’re in a partnership.
“We can’t do road safety by ourselves. This is a combined programme where we’re working with Waka Kotahi. These brake machines complement their whole road safety programme.
“And we’re working with industry to try to get the road safer. Part of that ‘commercially’ for them is to get a level playing field in terms of vehicle upkeep and maintenance (such as worn tyres and unadjusted brakes) and therefore rates.”
You’d think that there would be pushback from the operators, but Soepnel says no.
“At this stage we have had good feedback from both drivers and operators. They’ve all been informed that these machines are coming, and several operators have taken a proactive stance on it and actually installed roller brake machines in their own workshops, so they can regularly test them when they are doing day-to-day maintenance.”
He says that they have received several [victimised] complaints in the past from operators going past Paengaroa and being the ‘only place in the country that are being brake tested’.
“They don’t consider the playing field to be level as such, but now it is.”
Higgins adds; “This is a good thing. Possibly some people will think this is just revenue collecting but what I can say is that we did some roadside testing prior to winning the tender and let’s just say eyebrows were raised at the condition of brakes on some of the vehicles.”
Higgins says that he’s a great believer of ‘test don’t guess’.
“If you test, you’re in possession of the facts and if you’ve got a problem wheel that’s not braking correctly you’ve got the opportunity to fix it. And then retest the brake to make sure that it is working.
“What a lot of people don’t realise is that if you have a low braking axle or wheel in a combination, not only is it unsafe but then all the other wheels have to work harder. So, it is actually costing big bucks because you’re potentially wearing out those wheels and axles quicker than if everything was working as it was designed, in unison.”
Higgins says working brakes will save money and give operators longer intervals between service. “Like anything if you do it right first time then it always saves you money,” he says.
Soepnel says the introduction of MRBT units is all about safety.
“We see this is a big step forward because a lot of the vehicles are not getting tested regularly and as times get tougher, maintenance goes by the board. So obviously there’s a lot of brakes out there that are not up to scratch,” he says.
“I think at the end of the day we can’t do this ‘Road to Zero’ by ourselves. We need the cooperation of the industry, the public and our partner agencies, it’s a joint effort. We want drivers to go to work and come home safe at the end of the night.
“A lot of crashes are not caused by heavy commercial vehicles. However, a truck with good brakes, stopping 3-metres quicker in the event of an incident could make a huge difference,” says Soepnel. T&D