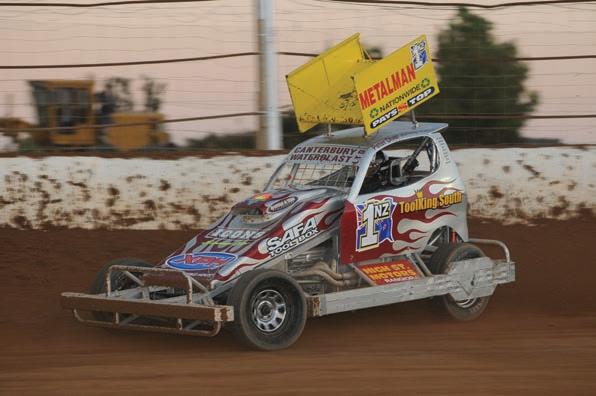
11 minute read
Reintroduction of RUC discount the right decision
Transporting New Zealand
welcomes the Government’s decision to extend the Transport Support Package, including reinstatement of the 36% RUC discount.
by Nick Leggett Chief Executive Ia Ara Aotearoa Transporting New Zealand
The Transport Support Package has been absolutely critical to help reduce costs for road transport operators and keep rising consumer prices in check, which is why Ia Ara Aotearoa Transporting New Zealand ran a campaign over summer to have it extended.
The Treasury estimated that the combined impacts of the Transport Support Package reduced headline inflation by 0.5% in the June 2022 quarter so the impact of the policy right across the economy is pretty significant.
Middle- and lower-income New Zealand families are already up against it with annual inflation sitting at 7.2% and a 11.3% year-on-year increase in food prices (which includes a rise in fruit and vegetables of over 23%). The removal of the RUC discount would have come right at a time when these communities could least afford it, particularly as transport operators have no choice but to pass increased input costs on.
I’m not sure many New Zealanders actually understand the costs associated with RUC. Transporting New Zealand publicly released figures back in January that showed a 45+ tonne truck and trailer travelling 100,000 km per year would pay an additional $21,000 if the RUC discount was removed.
Transporting New Zealand has strongly recommended to Government that the Transport Support Package remains until inflation falls below 6% and we are glad new Prime Minister Hipkins has at least pushed the current extension out until the end of June. The discounts can’t last forever but with domestic inflation forecasts remaining high through 2023, not to mention a General Election in October, it is hard to believe that the Government won’t extend them beyond the current June expiry.
Trucks carry 93% of freight and the industry is the semiconductor of the New Zealand economy, so this decision will provide considerable transport price relief for a period to come. That will assist all Kiwis.
Roadside drug testing is here!
From March 11 Police will have the power to conduct saliva-based roadside drug tests on any driver, similar to how they currently conduct random alcohol breath tests.
The change is a result of the passage through Parliament of the Land Transport (Drug Driving) Amendment Bill and means that roadside drug testing is to be another critical tool in the Police’s toolbelt to improve safety on our roads. It is also something that Transporting New Zealand and the road transport industry has long called for.
The oral fluid testing that will be used on the roadside takes only a few minutes to achieve a result and can detect the most common impairing drugs used in New Zealand including cannabis, methamphetamine, benzodiazepines, ecstasy and cocaine.
A driver who fails two consecutive oral fluid tests will be liable for an infringement penalty, including demerit points, a fine and a temporary prohibition from driving. Dispute the results of this and failure of the subsequent blood test could result in criminal charges depending on the level and number of drugs detected and their combination with alcohol.
Of course, there will be those that say this testing is a step too far and an infringement on liberties but drugged driving is a massive problem in New Zealand, and in my opinion must be treated exactly the same as drunk driving. In both 2020 and 2019 over 100 people were killed in crashes where a driver was found to have a level of drugs in their system. That is nearly one out of every three people who died on our roads in that time and fully justifies the move to introduce roadside drug testing.
For truck drivers who spend their working lives on our roads, workplace drug testing is a well-established means of helping to ensure their own and the public’s safety. Industry best practice is for truck drivers to undergo three forms of testing – pre-employment, random during their employment, and post any kind of incident on the road or in the workplace. However, up until now, other road users haven’t been subject to any testing outside the standard impairment test, and that only takes place when police already suspect a driver is under the influence.
The Government must be congratulated for doing the right thing here. The new law provides far better balance in the way we treat the use of drugs on our roads and seeks to protect all road users, whether they be professional drivers or mum, dad and the kids. We should all look forward to its effective implementation.
REASONS FOR SETTING UP COMPANIES CAN BE AS VARIED as the companies themselves – to commercialise a great idea, be able to dictate your own destiny, fill a perceived gap in the market, or follow a lifelong passion.
Malcolm Ngatai has an even simpler explanation for his journey. The owner of Christchurch underground services firm Suck It Up explains why he began in business 10 years ago: “It was to finance my stock car racing. I did it on wages and salary for a long time, maxxing out my credit card every season and spending the winter paying it off. It was painfully obvious I needed something more.”
At the time Malcolm had been managing Canterbury Waterblast Ltd, a company he had worked with since leaving school 24 years before. Choosing the somewhat esoteric world of drain clearing as opposed to more conventional careers was mainly down to happenstance, he reckons: “I wanted to leave school, but my mother said I couldn’t leave without a job. A friend of a friend worked for Canterbury Waterblast and arranged a job for me.
“I was with them for 20 years. Then the Clark family that owned the company wanted to sell up, and it was bought by the Peter Diver group in 2006. I should have bought it myself, but I didn’t think I was quite ready to take on a business. In the event, Divers needed someone to manage the operation, so I stepped up.”
A core part of Canterbury Waterblast’s operations was the high-pressure water clearing of blocked drains and pipes. In the aftermath of the Christchurch earthquakes the demand for such services rocketed. As Malcolm comments: “We had what we thought was enough work before the earthquakes, but in the time following we went from a hundred calls a week to around a thousand. It was a crazy time.”
Demand for specialised vacuum trucks to carry out this sort of work was immense, and Malcolm took the opportunity to source a couple of units, which he dry-hired back to the company. In turn, the trucks formed the foundation of his own company when a couple of years later he made the call to go it alone.
From that modest beginning the firm has grown rapidly, until now the fleet numbers around 30 vehicles, ranging from Nissan Condor-based vacuum loading trucks with a capacity of 3000 litres to a Mercedes-Benz Actros 3248 air-vacuum unit, the last word in sophisticated material removal.
As well as handling jobs direct from the public, the company contracts to the Hurunui and Waimakariri District councils as well as several large contracting companies.
Where it’s not uncommon for a conventional transport operation to have more trucks than drivers, simply because of a difficulty in hiring staff, the vehicle/ratio imbalance with Suck It Up (nearly two to one) is more a reflection of the wide variety of jobs undertaken, each task requiring specialised equipment.
Consequently, you can visit the company’s yard to the north of Christchurch any time during a working day and find maybe a dozen trucks parked up, and nobody else on site except Malcolm, general manager Doug Knight and fleet manager Chris Walding.
This doesn’t mean the trucks on site are idle, just that they’re not needed for the jobs being handled at the moment. As Doug puts it, they’re simply seen as “plant transportation devices”. Depending on the length of each job, a driver could be in and out of the yard three or four times a day, using a different truck each time.
As well as the vacuum loading units that are used to clear blocked drains, empty sludge pits, do spill recovery or to clean up surface flooding, the fleet also includes hydro excavation vehicles. These use high-pressure water nozzles for trench excavation, eating rapidly through earth yet able to work carefully around existing underground services like sewer lines, power cables and fibre optic ducts without damaging them.
As Malcolm explains: “With so many other underground services, if you’re using a digger there’s always the risk of ripping them out of the ground. With the hydro method you can just dig smoothly around them and continue on with the trench.”
An even more advanced variation of the hydro approach uses extremely high air pressure to grind away not only earth but stones as well, yet because the pressure extends only a few millimetres past the delivery nozzles is ideal for working around the roots of protected trees or in areas where the integrity of other underground services cannot be compromised.
An added benefit of the air-vac approach is that the extracted soil, being dry, can be used as backfill, whereas with hydro excavation the water/soil slurry has to be taken way for disposal elsewhere.
Some of the hydro units have an inbuilt recycling function where the solids are filtered out of the water and then compressed, leaving the water to be used again. As Doug Knight explains, a recycling truck could fill up from a stream or municipal supply in the morning and be able to work nearly a full day before the need for a refill or the onboard volume being too limited by the compressed solids.
With the appropriate nozzles, high pressure water is used for clearing blocked drains and cutting through tree roots as well as above-ground water blasting and surface cleaning.
Throw in CCTV drain inspection, an advanced vacuum street sweeper and tipper trucks for spoil removal, and you have what Suck It Ups feels is a one stop shop for customers. The company is also a local agent for the English-built Harben diaphragm fluid pumps, which offer pressures in the 5000psiplus range.
This sort of technology doesn’t come cheap, so it’s not a great surprise to find that the trucks themselves are the least of the company’s outlay when setting up a new unit. In fact, as Doug explains, because they cover small distances in the course of a year, they’re almost invariably bought secondhand as a cab-chassis and fitted out with the specialist gear (vacuum units, pressure pumps, tanks and associated hydraulics) called for by the job.
Among the larger vehicles, ex-Fonterra Scanias have been the preferred option. With a typical 700,000km up, they still have years of reliable service ahead at the distances they’ll be travelling.
Above: Site cleanup is another task regularly carried out by the firm.
Opposite page: Malcolm Ngatai with Mustang, site security patrol, noisy visitor greeter and all-round sook.
Below: Malcolm reckons he started up his company mainly to finance a speedway competition career, one headlined by winning the 2009 NZ Super Stock title.
The cost comparison truck to gear can be marked, Doug says: “The trucks – even the big ones – might cost us no more than $50,000, On the other side of that equation, the plant they’re outfitted with – water pumps, vacuum units, hydraulics – is new and top end, and accounts for the bulk of the setup costs. It’s not unusual to have a truck fitted with several hundred thousand dollars of plant. High pressure water pumps alone can be $40,000, and some of our units are fitted with two.
“For the big trucks we have tended to try to standardise with the Scanias, though in the past couple of years we have also picked up a couple of Mercs and a Volvo. One of the Mercs was the air vacuum unit we sourced second-hand from the UK. Were we to commission one of these new it would cost around 1.3 million dollars and involve a six-month wait. As it was, we got it into service, with quite a lot of new equipment fitted here, for less than half that.
“Setting up new trucks is done substantially in-house, though we use specialists for the likes of the hydraulic work. As much as we can we try for uniformity of brands in pumps and vacuum units and the like. We’ve made plenty of mistakes over the years, but I feel we’re getting close to a formula that works.”
Working on the setup of newcomers to the fleet ensures fleet manager Chis Walding’s job doesn’t lack variety, for every project is essentially a custom one.
The work can be challenging, Chris admits: “You can wander out to No.8, the Volvo, and you can pull separate workshop manuals for the engine, the transmission, the main pump, the waterblast pumps, the hydraulic drive motors...but not how the whole system is plumbed and wired up. Apart from the air-vac unit every job is totally custom.
“As a result there often isn’t a clear direction. If you’re blazing trails, by definition there isn’t a trail to follow, so it doesn’t always go perfectly to plan. Then it’s a matter of licking the wounds, regrouping and trying again tomorrow.
“When I started my career I didn’t see myself ending up in hydro. Truth be told I wanted to be a tractor mechanic, but not having come from an agricultural background I struggled a bit with the application of some of the equipment, so opted instead for road transport for my trade course.
“I was lucky in that the company where I did my time, Heavy Transport Specialists, was a small, four-person operation that handled everything that came along. As a result you quickly got a wide experience of different makes and systems.
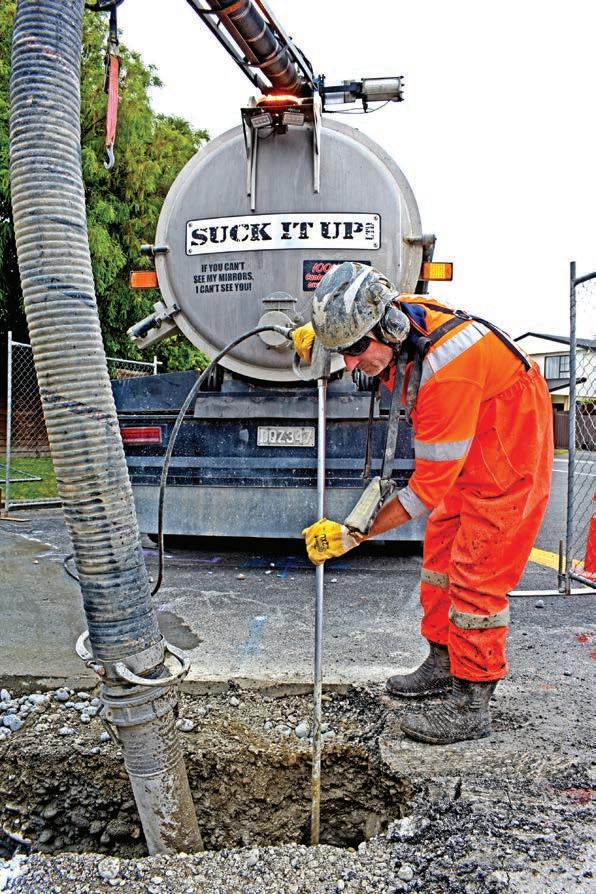
“And to be fair, I knew what I was getting into when I started here three years ago. I had worked with another company in a similar field for three or four years and had already helped Malcolm with some of his gear, and it grew from that.”
The company’s management/admin structure couldn’t be leaner, comprising just Malcolm and Doug, working out of a Portacabin on a site whose most substantial other building is the 200 square metre workshop. Forget your elegant front office, receptionist and support staff. If Malcolm’s around you’ll be vociferously greeted by Mustang, his biscuit-seeking chocolate labrador; if not, it’s just Doug, and a succession of drivers sticking their heads through the door for their next assignment.
Doug’s nerve centre is a large whiteboard marked off around a fortnight ahead with assignments for the various trucks. Queries for potential jobs are colour-coded to the side before a time and vehicle is locked in.
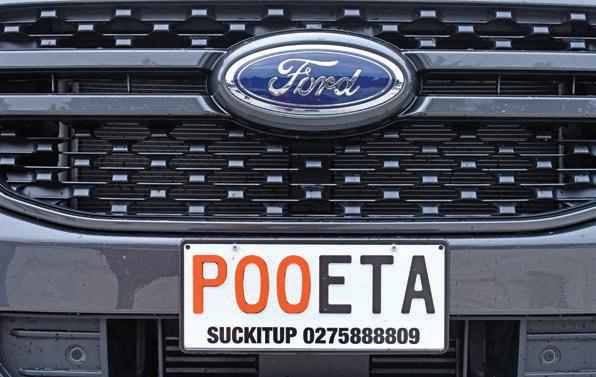
The system is basic, but effective, and depends heavily on Doug’s planning skills. From a personal perspective, he says, he finds the work exciting and challenging: “Mal and I complement one another, he hates the office stuff, and that’s more my strength.”
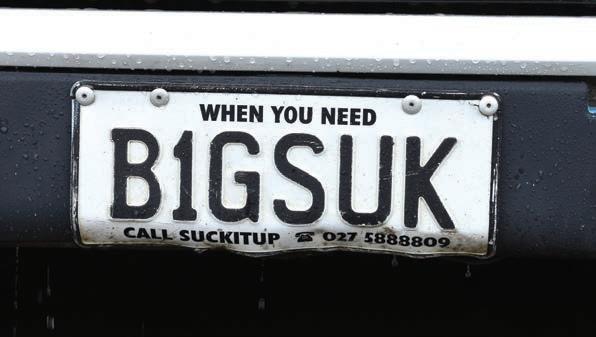
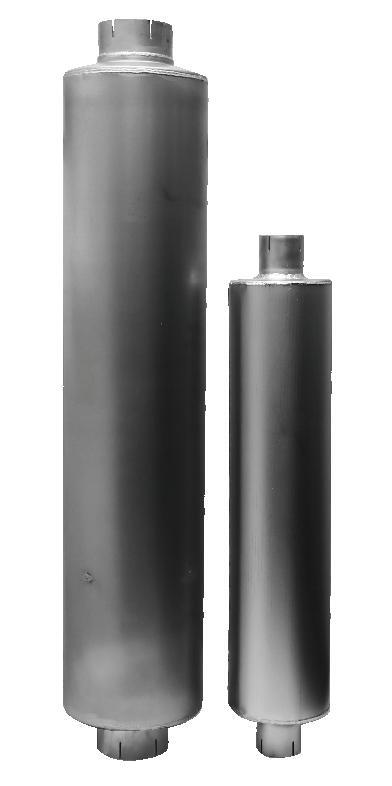
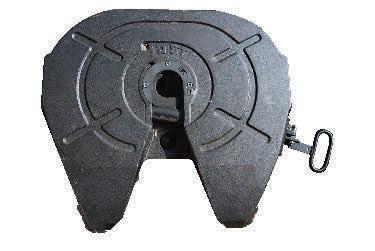
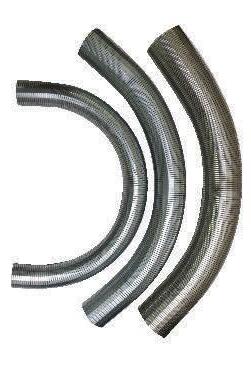
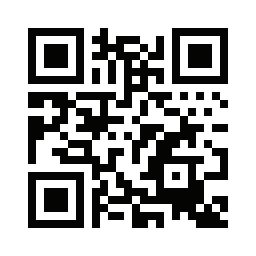

For his part, Malcom’s mobile number is the one used for 24/7 emergency calls, and though the staff are rostered on after-hours standby, if needed he will also front up in a truck, at night or during business hours.
Excavation units range in size. Some have onboard filters and compactors for the slurry, so the water can be recycled, while one unit uses high-pressure air for sensitive jobs. Its spoil, being dray, can also be used for back-filling.
The company only moved to its current location a few months ago, so the site’s still very much a work in progress. Coincidentally, it’s a bare kilometre cross country from Mal’s home speedway track of Woodford Glen. A clear insight to his staff relations attitude can be gleaned from the 160 square metre staff recreation building that’s being developed alongside the workshop. Using largely recycled materials, the project’s as yet in its