Sustainability update 2022
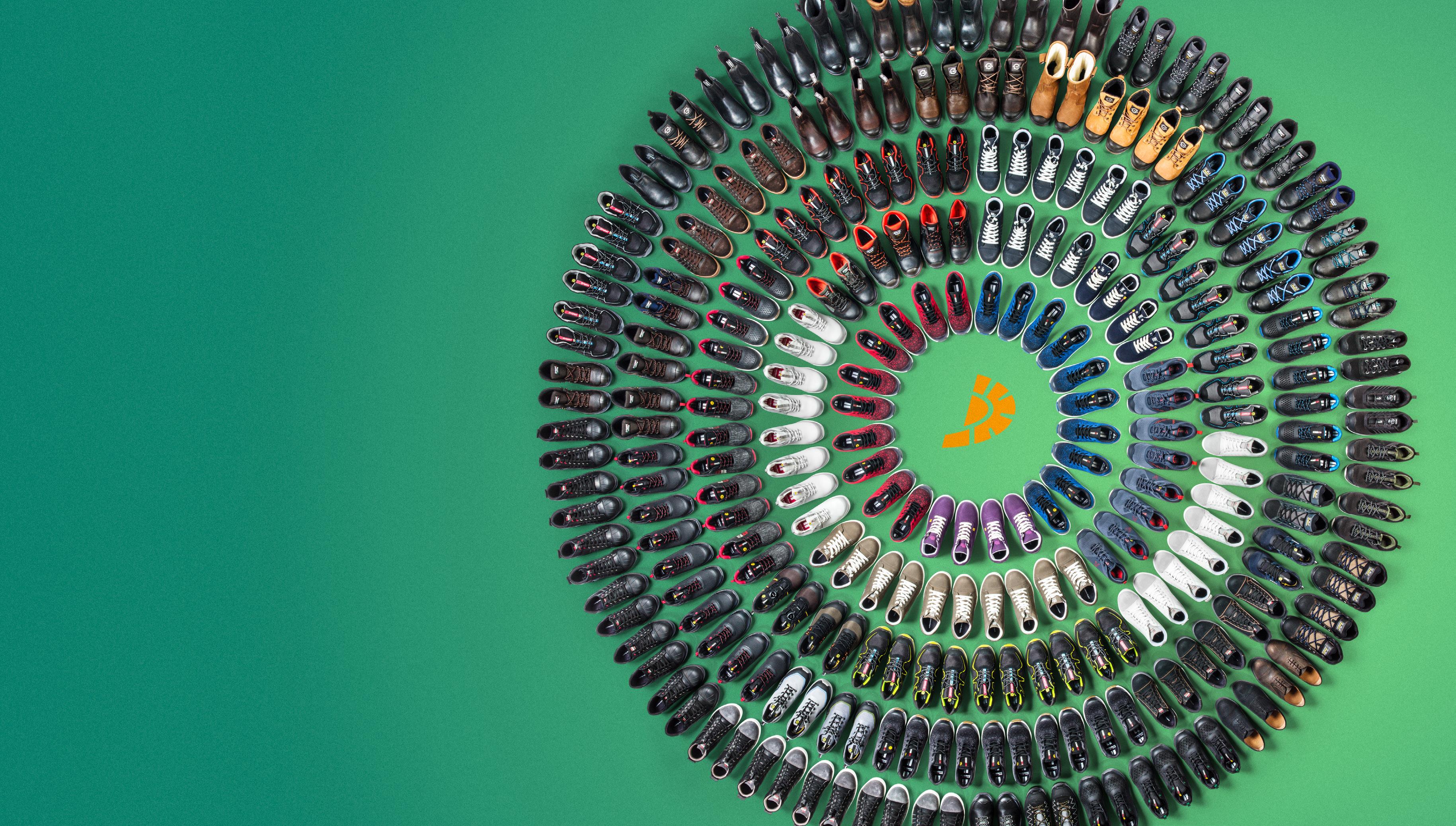
About this update
Last year, Allshoes Safety Footwear published its first comprehensive sustainability report detailing all sustainability initiatives up to and including 2021. In the document before you now, we provide an update on the progress Allshoes has made in 2022. This way, we make our steps transparent to the outside world and also keep a close watch on them ourselves.
We provide a comprehensive report one year and an update the next. This will keep you adequately informed of our progress and plans, and allows us to devote even more time and energy to making Allshoes more sustainable.
This update is about the period from 1 January 2022 to December 31, 2022
Do you have any questions or comments on this report? Do not hesitate to contact us through sustainability@allshoes.eu
Check out the 2021 sustainability report on our website!
allshoes-safety-footwear
allshoes.eu
In 2025... Allshoes has a fully circular product range
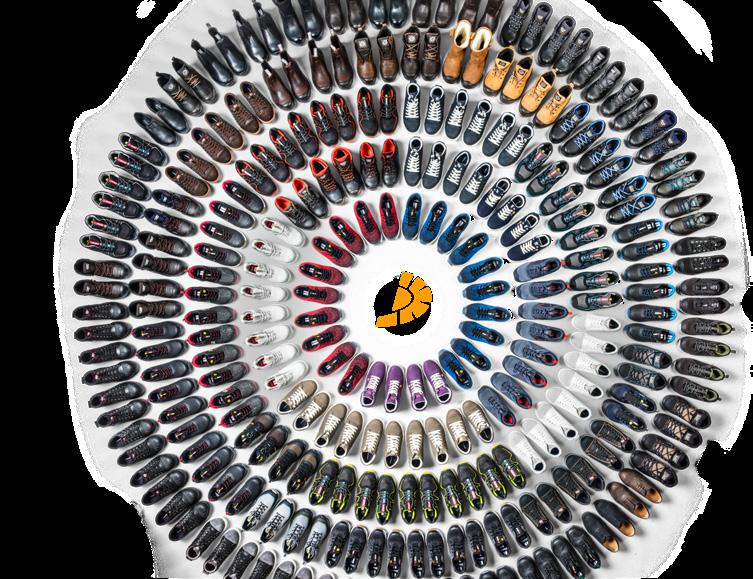
Allshoes
Great Place to Work
... Allshoes has a transparent supply chain
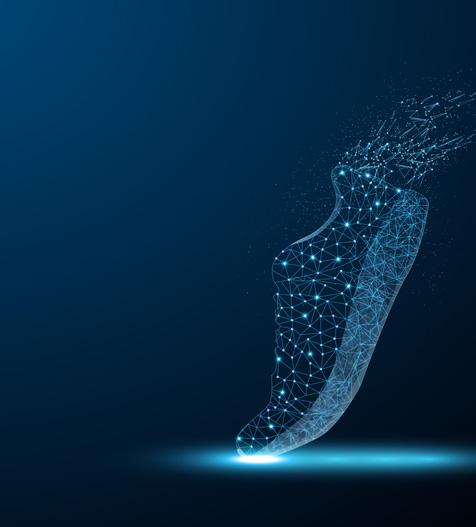
... Allshoes is a climate neutral organization
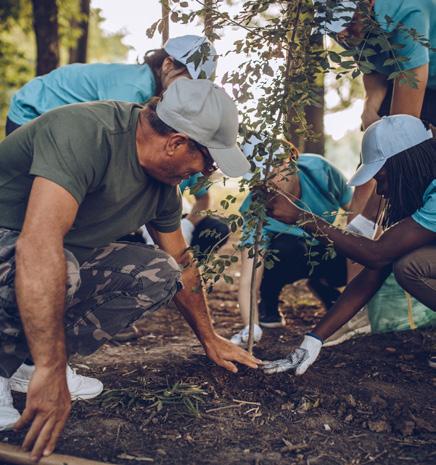
Life Cycle Assessment
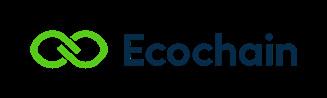
LCAs are the basis for more sustainable choices in the design process
>750.000 pairs sold
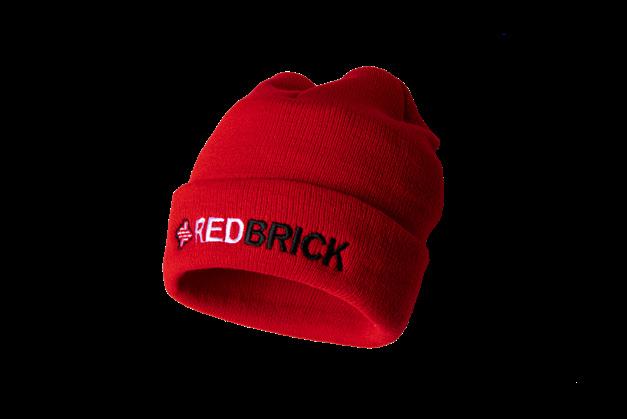
*
>50% in 6 new models
371 collection points
recycled material
*weight-based
CFA operational in 6 countries
for used safety shoes through the Circular Footwear Alliance
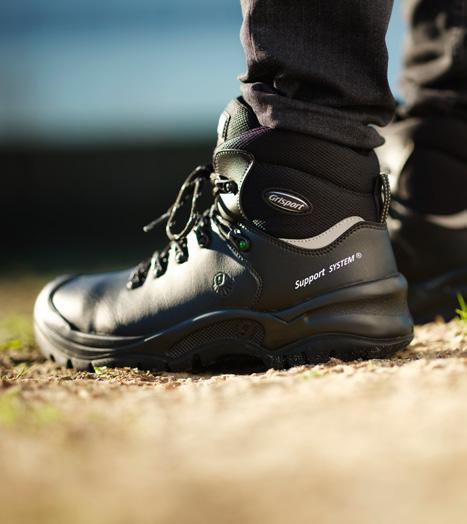
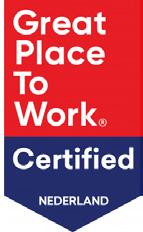
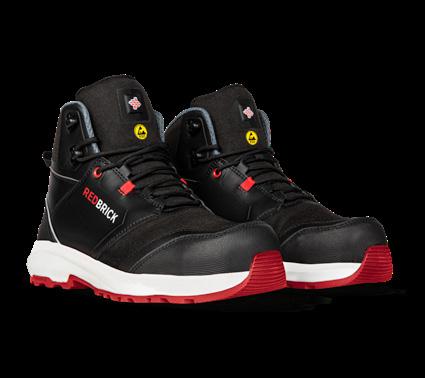
No leather in new designs
SUPPORTING PEOPLE
Prototype Smart Safety Shoe
New shoe box designs with 60% ink reduction and made of FSCcertified cardboard
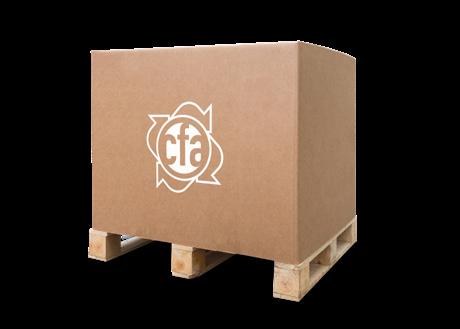
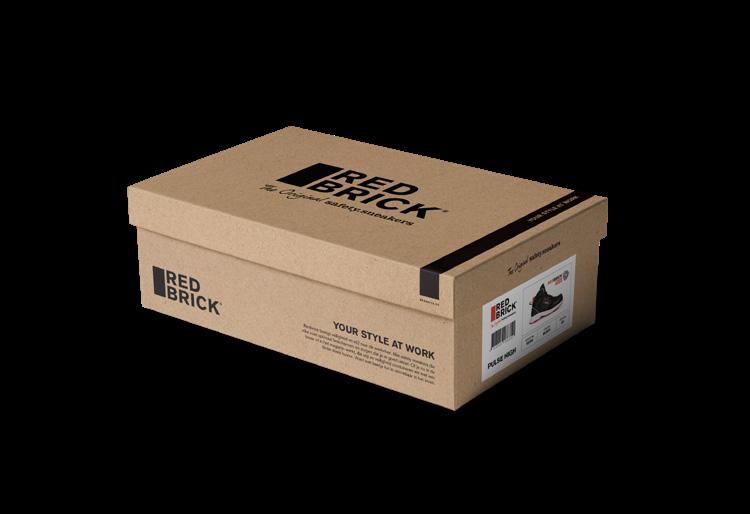
10.540 pairs of used safety shoes collected in 2022 through the Circular Footwear Alliance
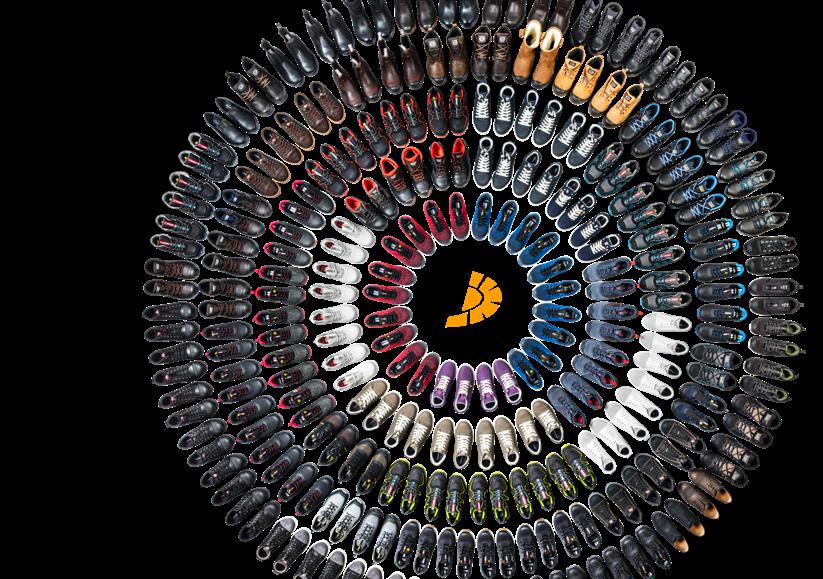
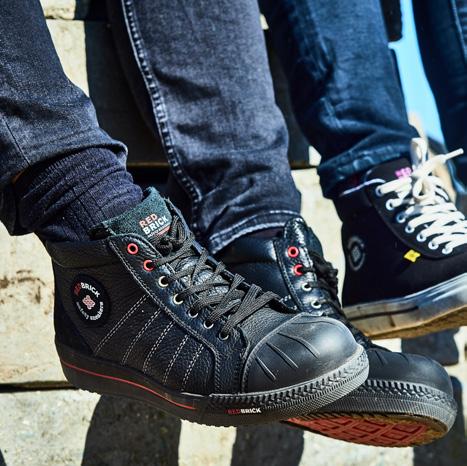
>400 pairs of shoes & 1000 hats donated
785 trees
planted through the United Packaging Forest initiative
Partners we collaborate with: Ecochain, Ecoreview, MVO Nederland and Transparency Pledge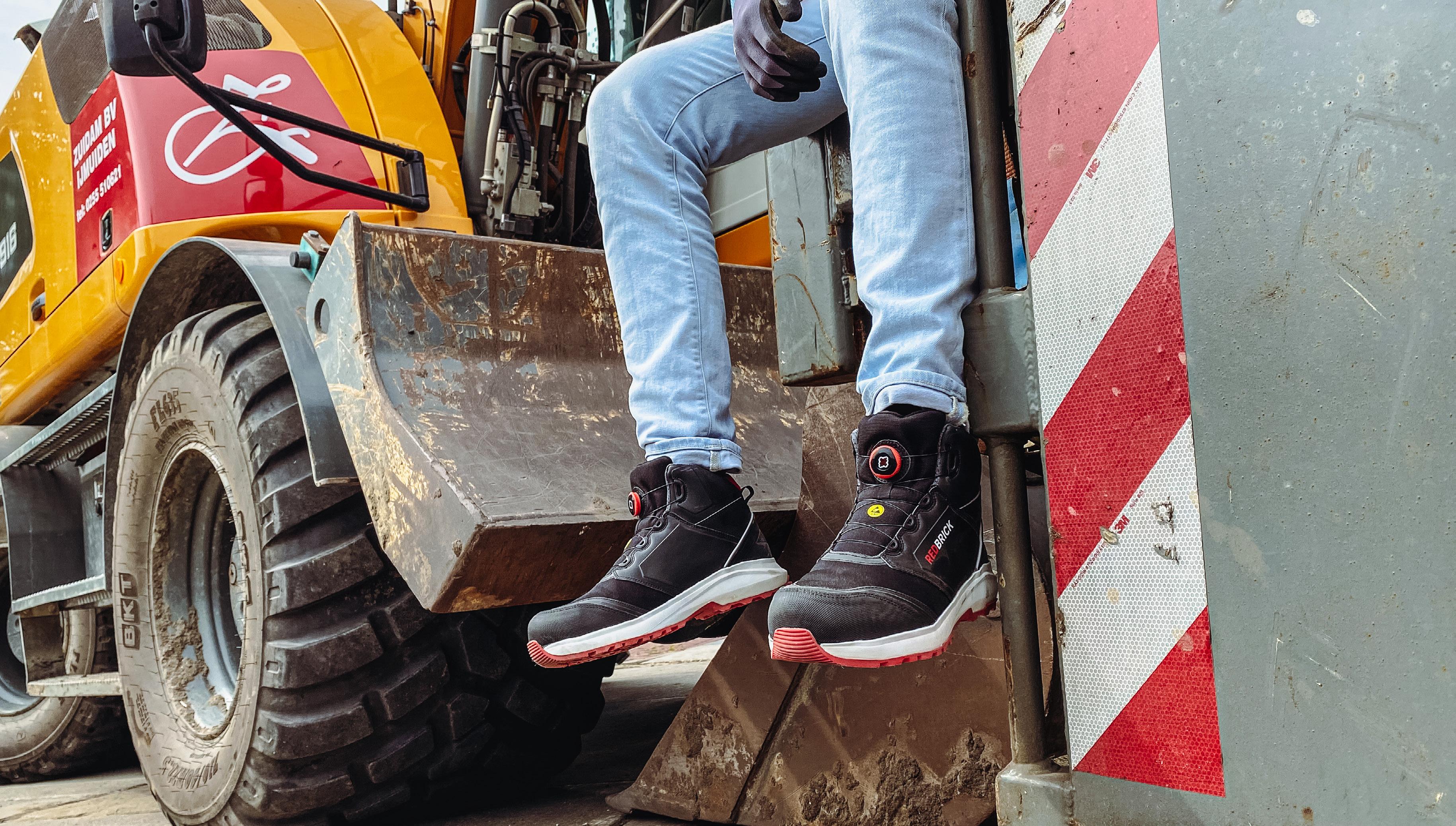
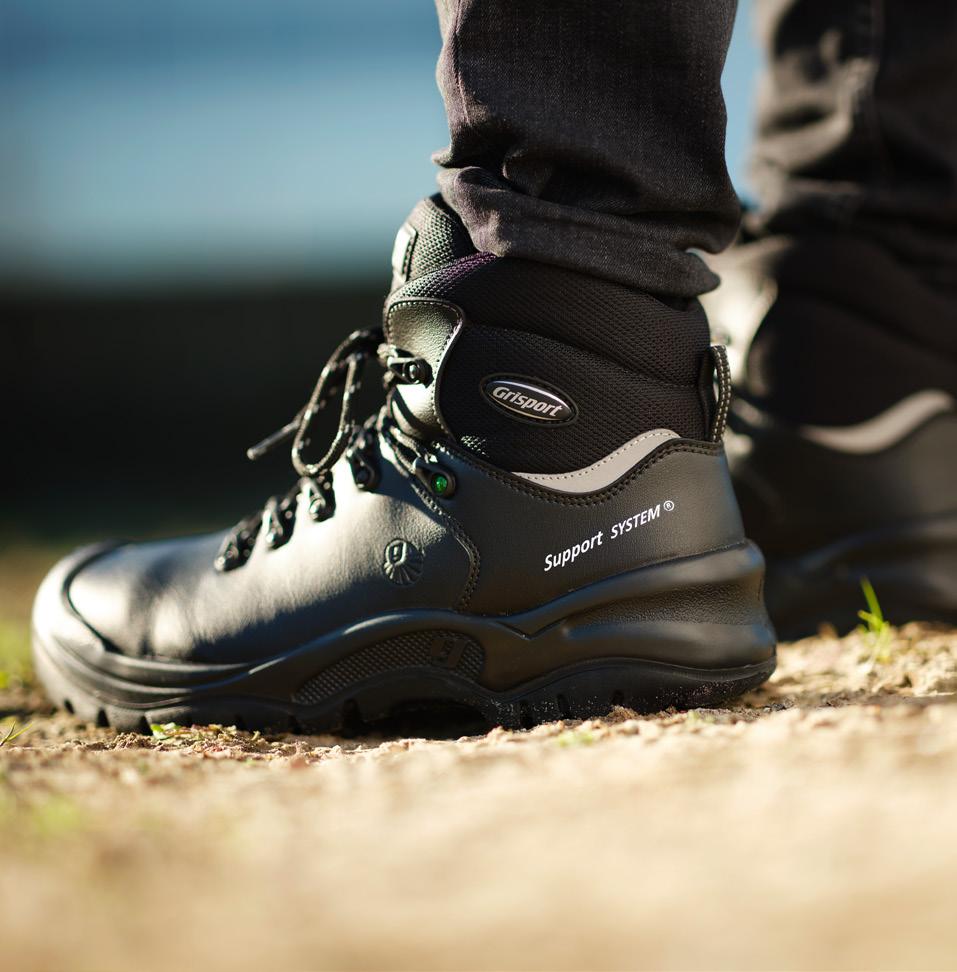
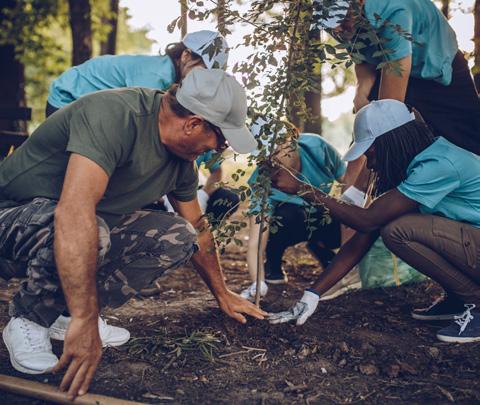
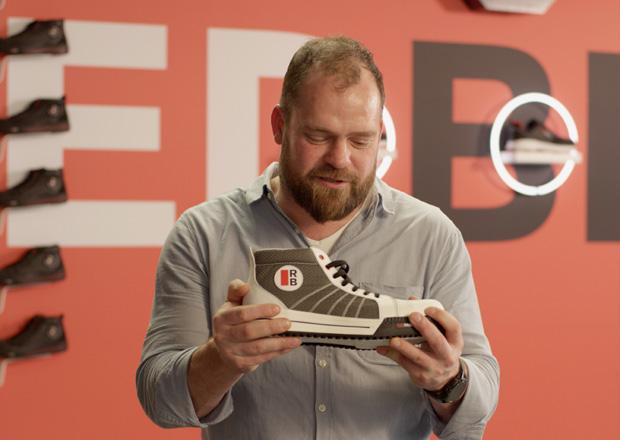
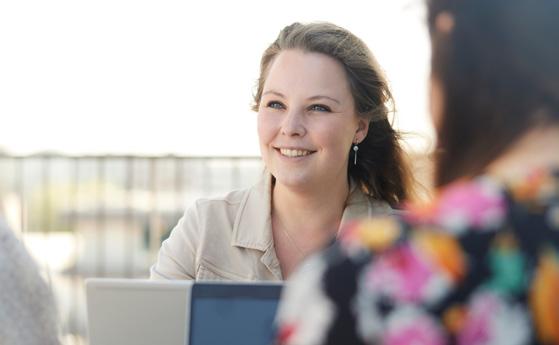
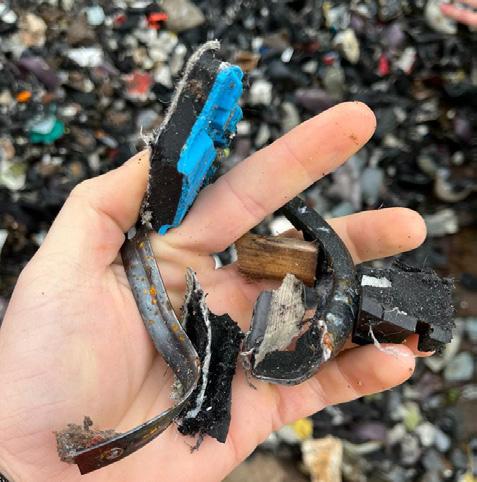
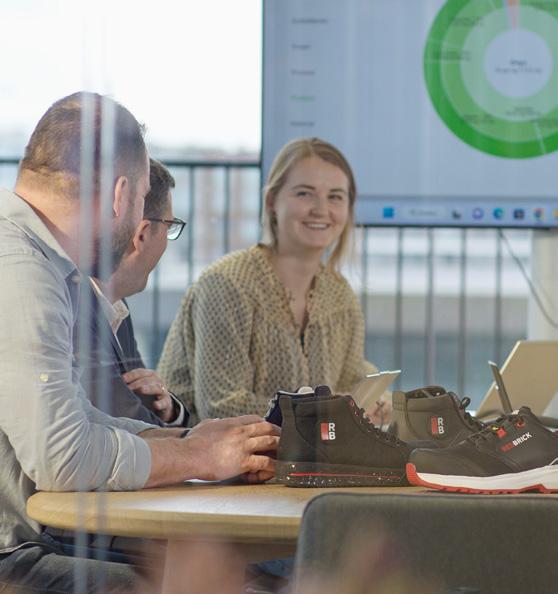
The drive to be sustainable
Last year, we published our very first sustainability report. A report in which we proudly demonstrated how Allshoes is making a positive impact when it comes to circularity, CO2 reduction and a responsible supply chain. In the report, we talked about how we want to be a climate-neutral organisation by 2025 and we highlighted the projects we have implemented and will be implementing in the future. The steps we envisioned for 2022 have certainly been taken. Some at a much faster pace than I could have ever imagined.
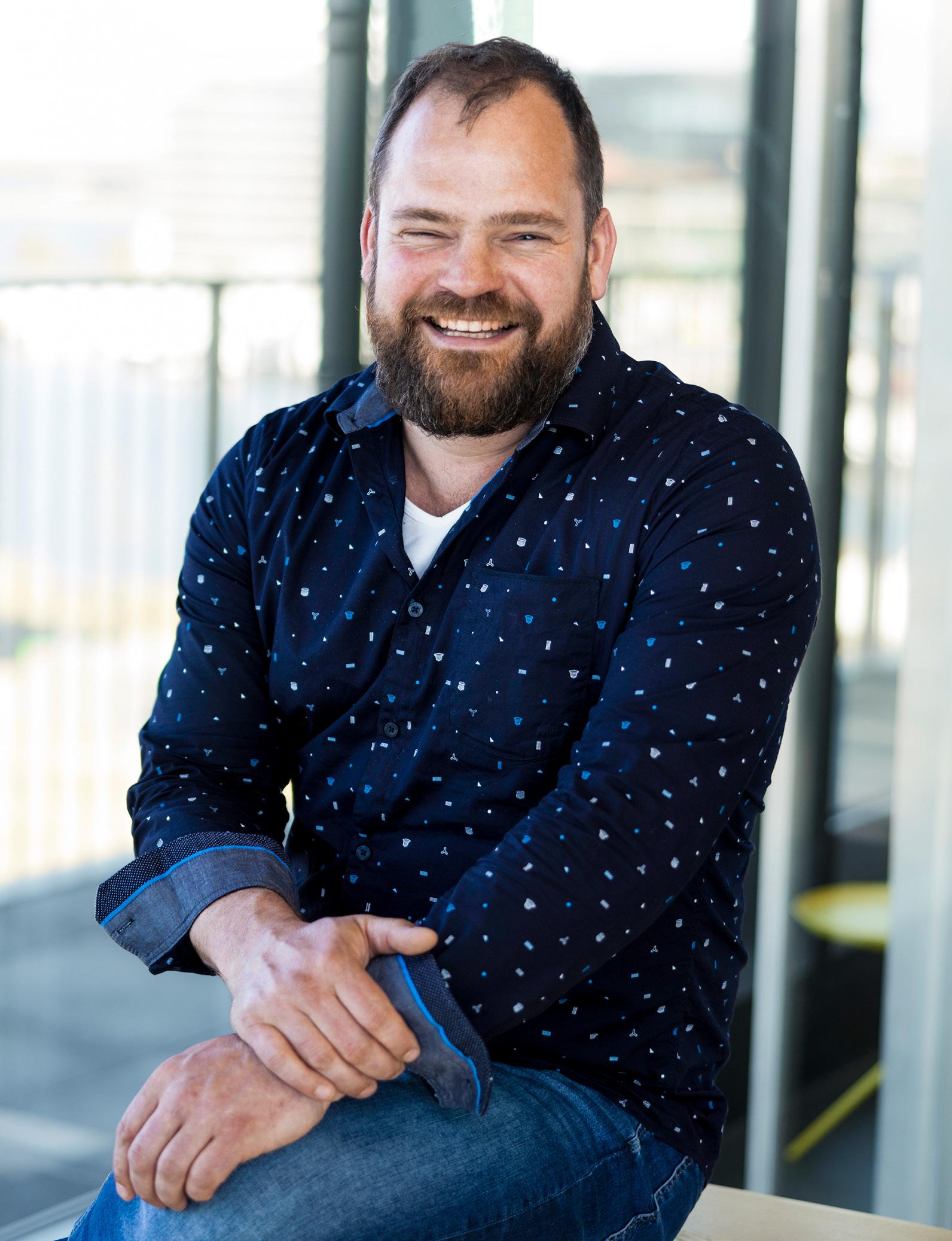
In 2022, our core values of team spirit, courage and perseverance were heavily called upon. Not just at Allshoes, but throughout our entire supply chain. The war in Ukraine, which caused and is causing great social and human suffering, has created a huge shortage of energy and raw materials. Some of our suppliers were hit hard by those raw material shortages. Thanks to our partnership with these suppliers and flexibility across the organisation, we never failed to deliver to our customers.
The current global situation called for vigorous action. We already knew that we wanted – and needed – to work in a different way. And going back to an ‘economy as usual’ was not an option. Especially if you want to contribute to a sustainable economy for the benefit of our earth and life on it, now and in the future. The high energy prices and scarcity of materials meant that we had to be even more flexible, innovative, and change our way of thinking. This was true for our suppliers as well. Remaining steadfast and sticking to our sustainable trajectory turned out to be crucial. Trying to protect our current business model is no longer an option. Our flexibility, innovation and perseverance resulted in six new safety shoes with over 50%weight-based* recycled material. A huge step in the market toward a circular safety shoe!
The drive to be sustainable is in Allshoes’ DNA. It is reflected in both the work and personal lives of our employees. From the sustainability to the marketing department. From facility (we drive electric and have vegetarian lunches) to our warehouses. We don’t want to ‘do’ sustainability, we are sustainable. And we back up the results with validated facts and figures that we share transparently.
I am proud that we have accomplished so much this past year. Proud of the teamwork within Allshoes and with our suppliers, and proud of our customers. In fact, among our customers, we observe an increasing awareness of the importance of sustainability. Sustainable initiatives, such as the Circular Footwear Alliance, are being embraced by them.
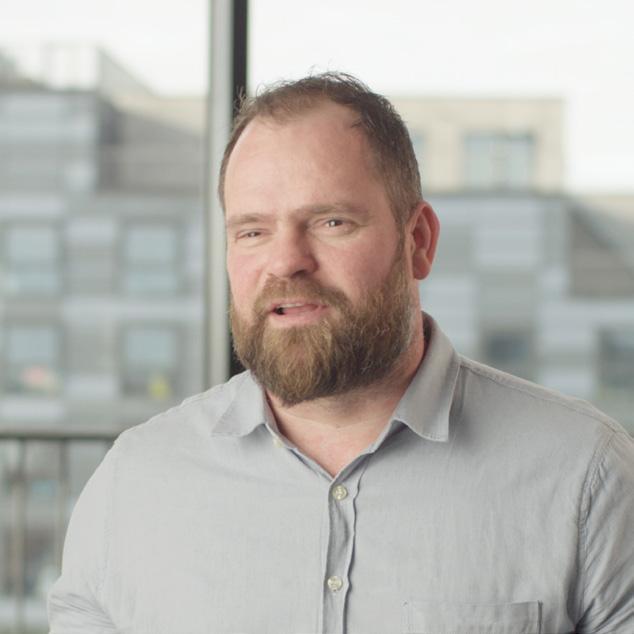
We do not know where we will be by the end of 2023. But I’m sure we will continue to take many exciting steps this year to reach our goal of a fully circular range by 2025.
Jan Arts Manager Operations, Sustainability & Innovation

“If we want to take care of our planet and the life on it, going back to the ‘economy as usual’ is not an option anymore.”
Jan Arts
MANAGER OPERATIONS, SUSTAINABILITY & INNOVATION*Weight-based means that the percentage of recycled materials are measured based on the total weight of the safety shoe. For this calculation, all components of a safety shoe are carefully cut and weighed by the supplier.
Our supply chain partners talking about sustainability
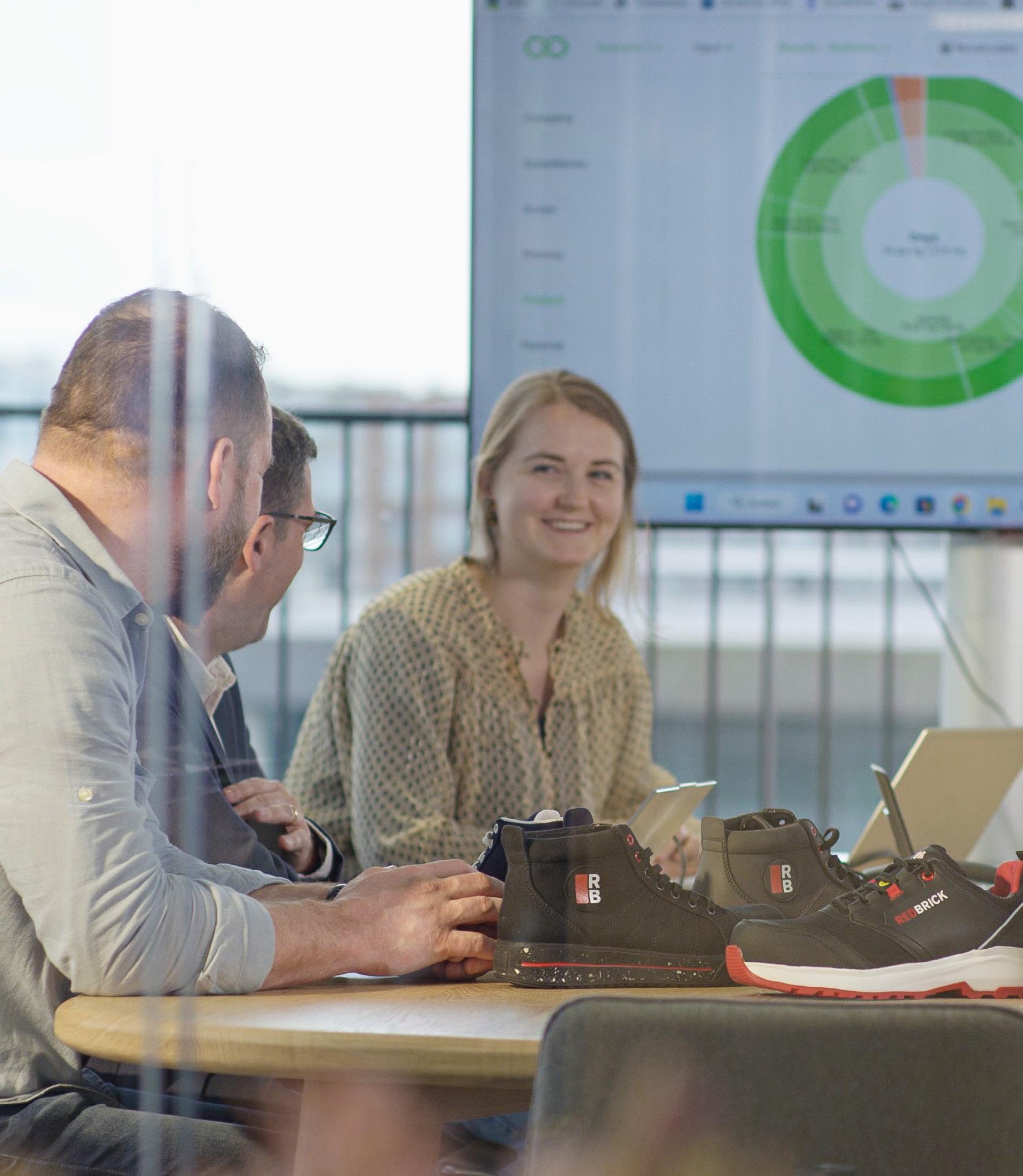
Within Allshoes we are proud to be a driving force for sustainability. In the fight against climate change and the increasing pressure on our material resources, it is important to not only focus on individual actions, but also on the entire supply chain. From the raw materials for safety shoes to the end-of-life a product: every part of our supply chain makes an impact on the environment and our planet. Collaboration within our supply chain is crucial in achieving our sustainability goals. Therefore, Allshoes works closely with suppliers, manufacturers and other partners to develop and implement sustainable solutions.
By focussing on carbon reduction, a responsible supply chain and circularity, we are committed to a more sustainable future. Although many steps have already been taken, we cannot do it alone. Let’s work together to create a more sustainable world! Watch the video and be inspired and above all challenged by our partners in the supply chain to join forces!
Watch the video
Let’s listen to...
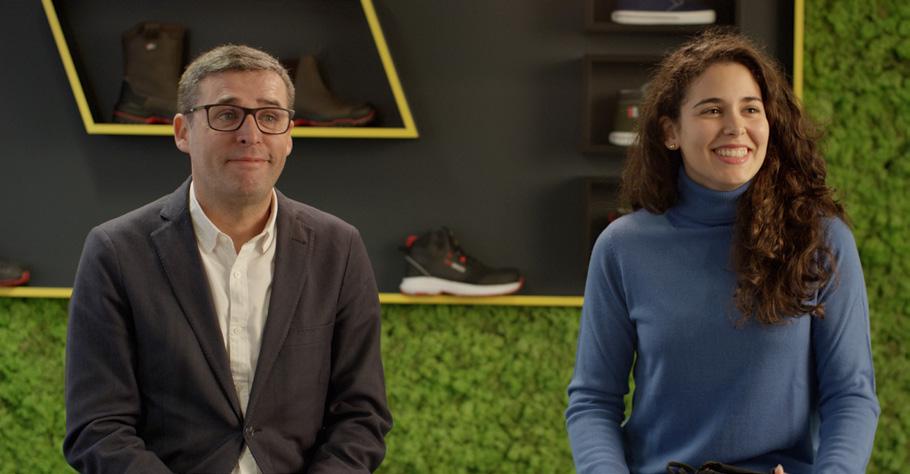
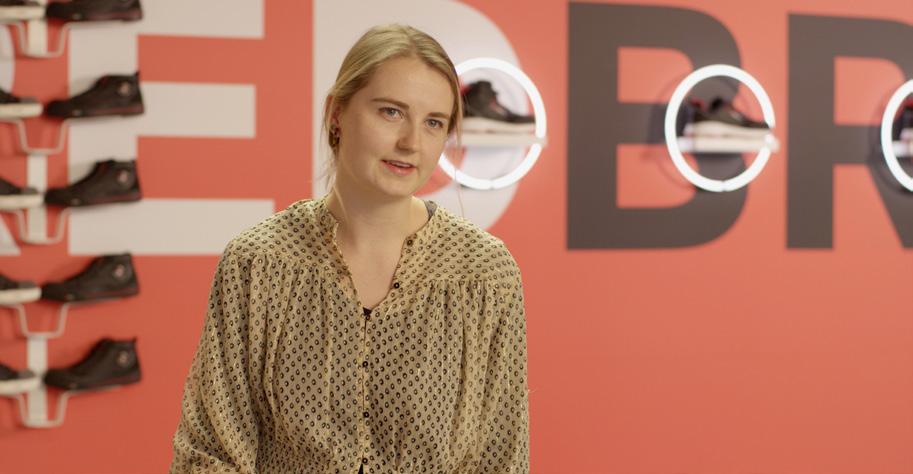


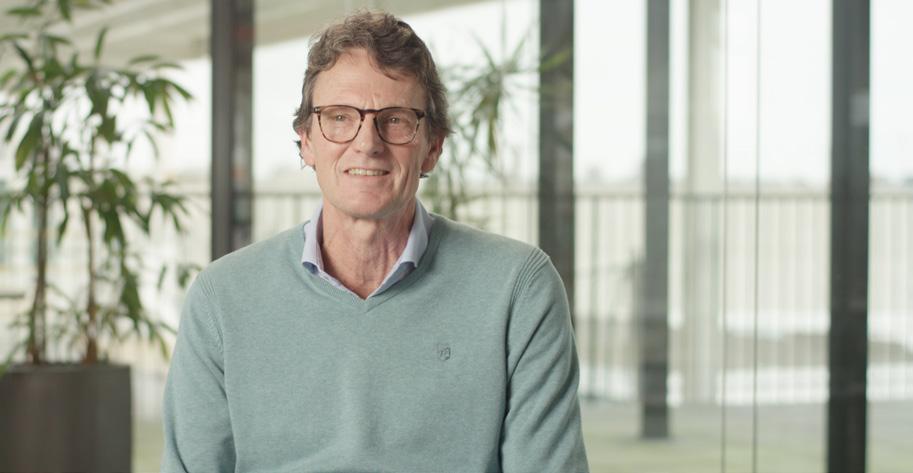
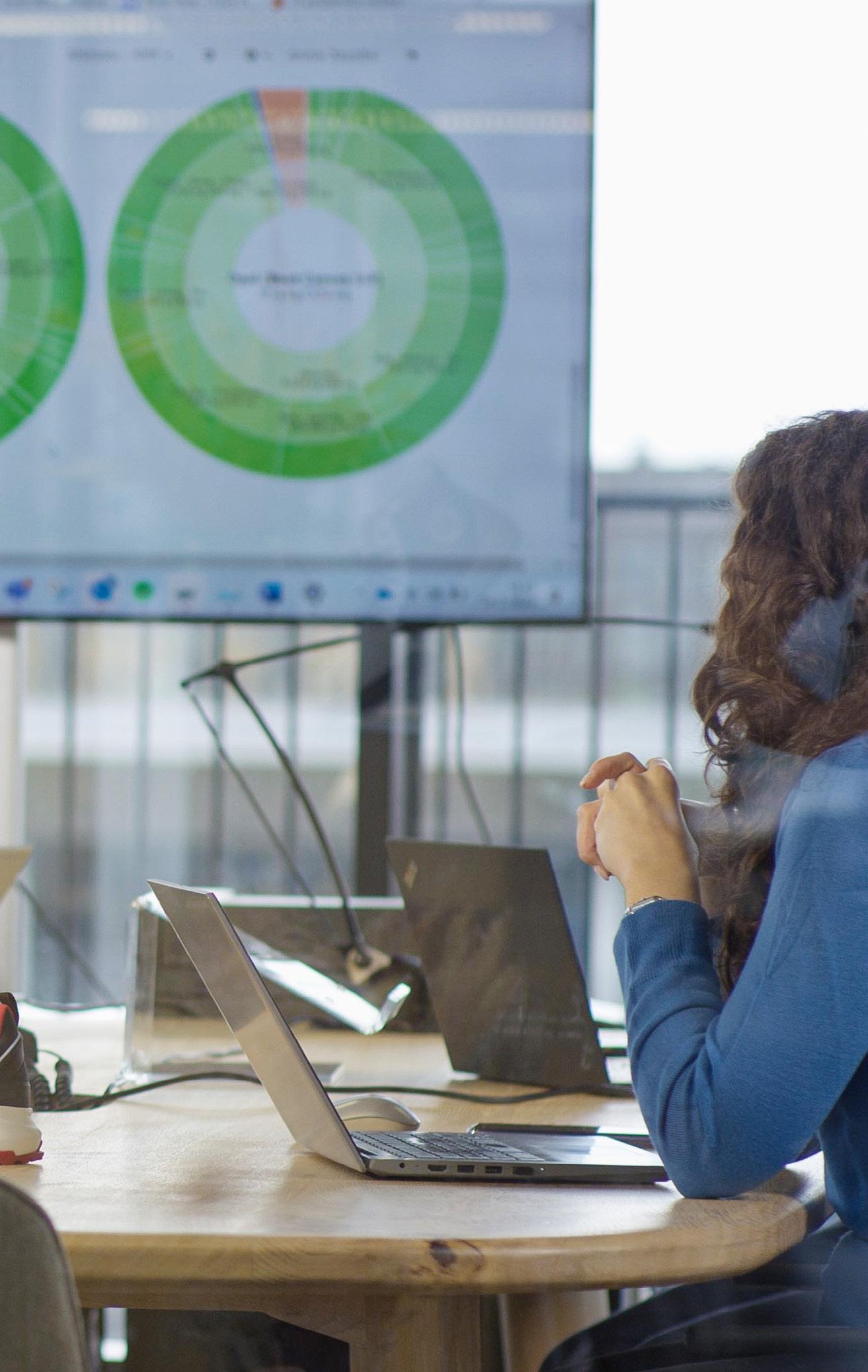
About Allshoes THE ORGANISATION
We are safety footwear specialists. We put workplace safety first, but style is just as important for all our products and brands. Therefore, we constantly renew our product range in terms of appearance, technology, and innovation. In this way, we create a collection of footwear where safety and the latest trends from the world of fashion and sports collide. Something quite different from those bulky boots that come to mind when you hear the word ‘safety shoes’. In addition, we always keep an eye out for new materials that will improve our shoes even further.

Where Protection meets Style
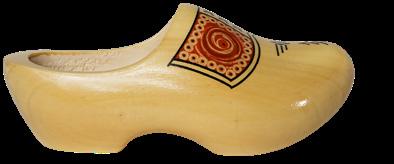
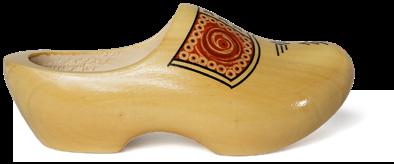
As market leader in our field, we distribute a huge quantity of occupational and safety footwear each year. And for the distribution of so many shoes (as many as 750,000 pairs by 2022!), we shoulder our responsibility. Since 2019, our focus has been on making our product range and operations more sustainable. Through our three main focus areas – carbon reduction, circularity, and a responsible supply chain – we are taking steps towards a sustainable future and the circular safety shoe!

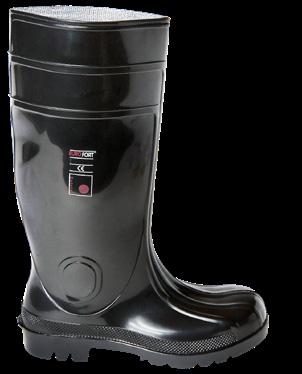
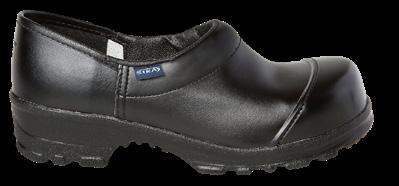
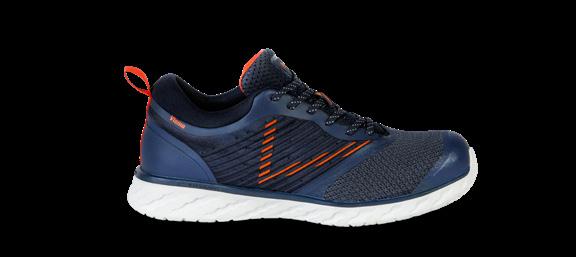
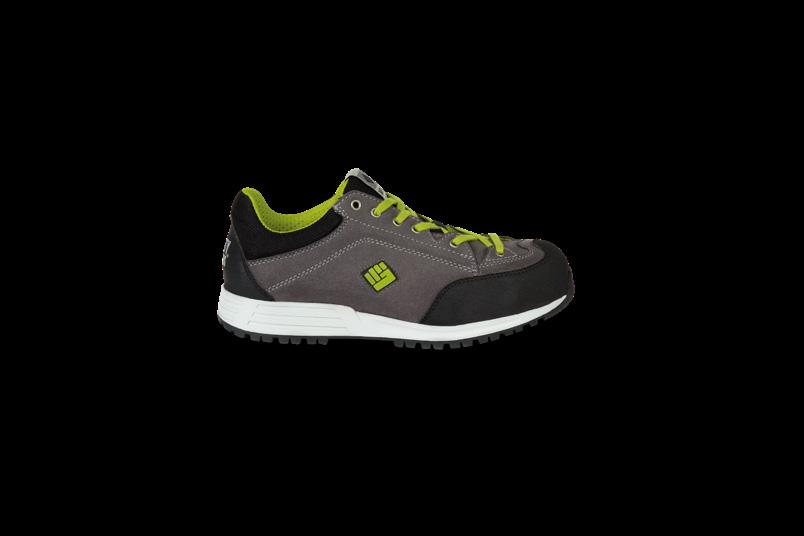
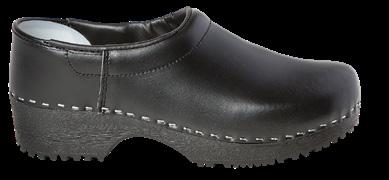
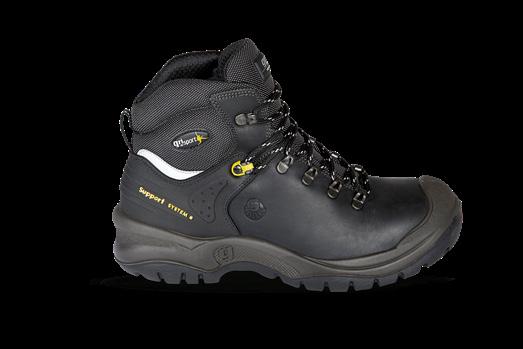
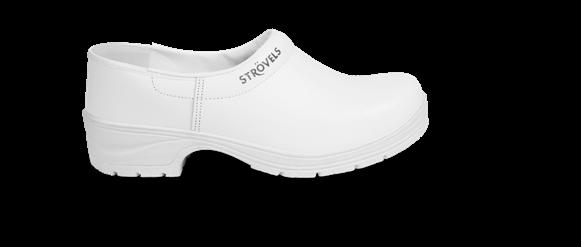
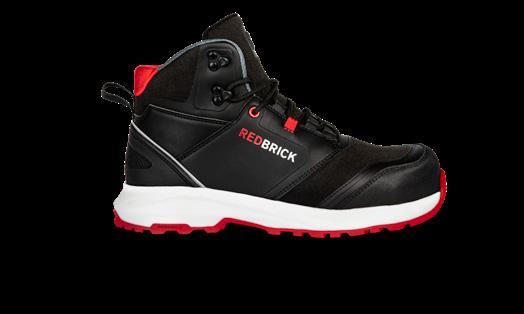
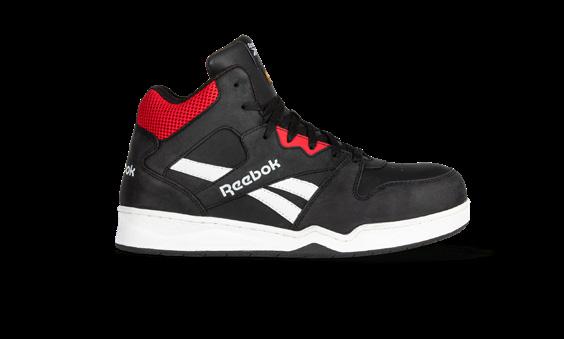
Sustainability strategy and impact
We have been pursuing this vision since we drafted our sustainability programme in 2019. To achieve this goal, we focus on the themes of carbon reduction, circularity, and a responsible supply chain. Our previous sustainability report contains a detailed description of the pillars we use as a starting point for executing projects: Better materials & design, Sustainable operations, Close the loop, Supporting people en Driving change
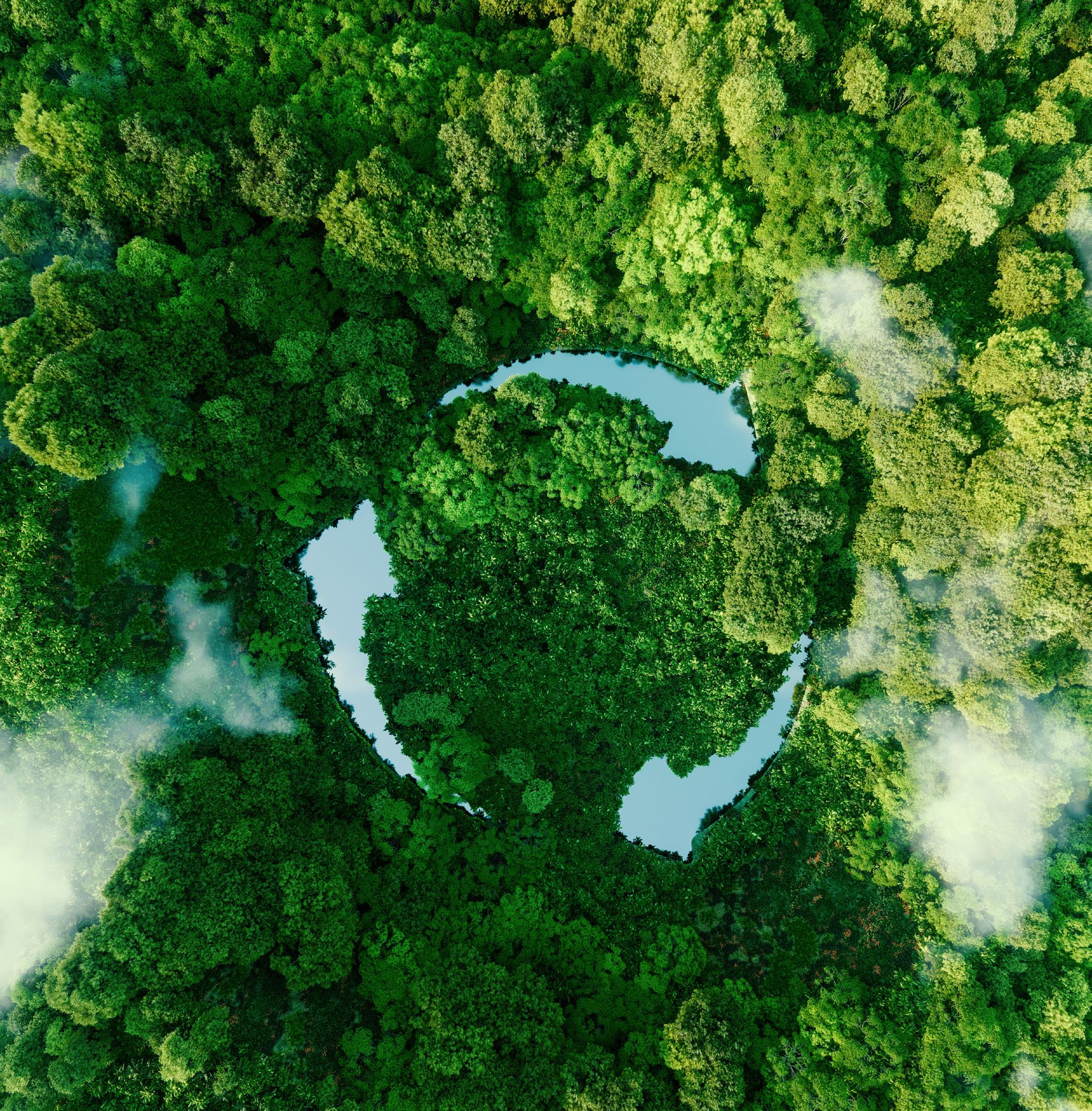
On the adjacent page, you can see an overview of the progress we have made on each theme over the past year. From experience, we know that the process of making an organisation and a complex chain sustainable takes time. We have, however, become increasingly aware that we have set something in motion in recent years. This has made us even more motivated to work on our ambitious goals.
Will you join us?
By 2025... Allshoes safety footwear will be produced responsibly, with the lowest possible carbon footprint and in line with the principles of the circular economy.
Carbon reduction
Reducing CO2 emissions is one of the biggest challenges in the fight against climate change. We aim to reduce carbon emissions both within Allshoes (scope 1 and 2) and across our entire chain (scope 3).
Carbon reduction of 10% within Allshoes
Within scope 1 and 2, we were able to reduce our emissions by 10% compared to the base year 2018. Because we have started working at the office more and have grown as a company, we do see a slight increase compared to last year during the COVID pandemic. Read more about our carbon emissions in the chapter Sustainable Operations.
Carbon reduction of 2% per product sold
In our chain (scope 3), emissions per product sold decreased slightly by 2% compared to the year 2020. We expect to further reduce our emissions per product sold by 2023, as we will use new materials with less environmental impact in our shoes. By 2023, we will launch the first models with more than 50%weight-based recycled material. An absolute first among safety shoes!
In 2023, we will accelerate the reduction of our carbon emissions in scope 1 and 2, as well as in scope 3. We achieve this, for example, by using recycled raw materials and materials with less environmental impact and by using green energy. Our Life Cycle Assessments, calculated in collaboration with Ecochain, give us insight into the areas that offer the most potential gains.
99% of our emissions come from our products. That is why it is so important to make the designs of our products more sustainable!
Aim for 2025
• A climate neutral organisation (scope 1 and 2) with 30% reduction of greenhouse gases within our organisation*1
• And 25% reduction in greenhouse gases per product sold*2
Progress
• 10% reduction of greenhouse gases within our organisation by 2022*1
• 2% reduction in greenhouse gases per product sold by 2022*2 *1 -
*At Allshoes we are constantly learning, also on the topic of sustainability. The calculated CO2 emissions are a recalculation of the data in the report of 2021.
Circularity
As the market leader in the safety footwear industry, we are taking the lead in the transition to a circular economy. We focus on bringing materials from used work and safety shoes back into the chain through the Circular Footwear Alliance (CFA). We are also working to reuse these raw materials in new shoes.
The past few months we have been working hard on developing safety shoes with more than 50%weight-based recycled raw materials. This is a big step towards the goal of a circular product range. We will apply this in other models as well. The growth and professionalisation of the CFA also contribute to this. Over the coming period, we are committed to internationalising the CFA, promoting legislation (Extended Producer Responsibility- EPR) and further developing recycling technologies.
10.540 pairs of used safety shoes collected in 2022 through the Circular Footwear Alliance
Aim for 2025
A fully circular range.
According to Allshoes, a circular product meets the following requirements:
1. Contains at least 50%weight-based recycled content
2. Is designed for a long service life
3. Is designed for easy dismantling
4. Can be recycled into applications with the highest possible quality
Progress
• Together with our supplier AMF, we have developed four new Redbrick models with 53-57%weight-based recycled raw materials.
• In collaboration with Grisport, we developed the Grisport 103 with 50%weight-based recycled raw materials. For the above shoes, we already meet our criteria 1-3 for a circular product.
• Wherever possible, we work with materials certified to the Global Recycle Standard (GRS).
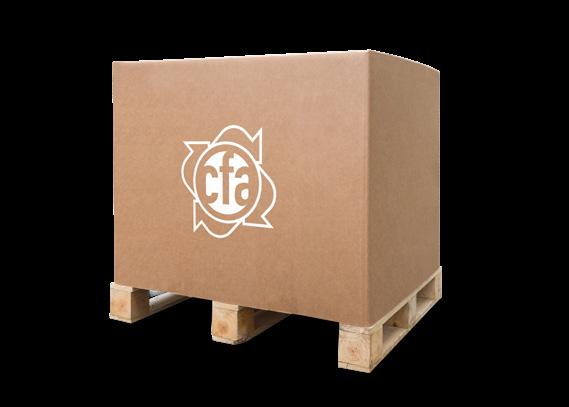
>50%weight-based recycled raw materials
• In 2022, we have recycled 11,800 pairs of used occupational and safety shoes through the Circular Footwear Alliance (CFA).
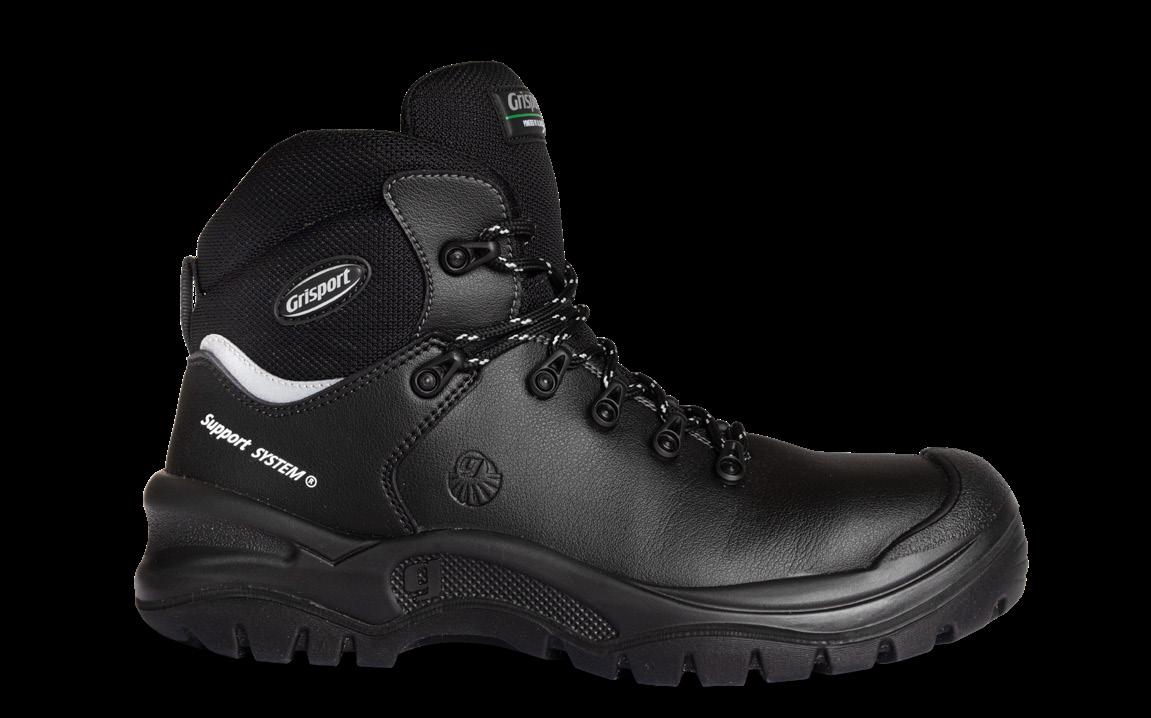
Responsible supply chain
Naturally, at Allshoes, we are well aware of who our direct suppliers are. However, it is still not always clear who the suppliers of our vendors are and who supply them. In order to guarantee the working conditions and terms of employment for the people deeper in our chain as well, we want to gain more insight into what that chain looks like.
Fully mapping our chain is an enormously complex process. The deeper down the chain we go, the more difficult it becomes. We are constantly working on new methods that allow us to achieve transparency while ensuring the privacy of our chain partners.
Aim for 2025
• A fully transparent supply chain
Progress
• Allshoes is a member of the Transparency Pledge, an initiative to make supply chains within the clothing and footwear industry transparent.
• Allshoes has created insight into 78% of the production locations of their direct suppliers.
• We have started mapping the suppliers of our direct suppliers.
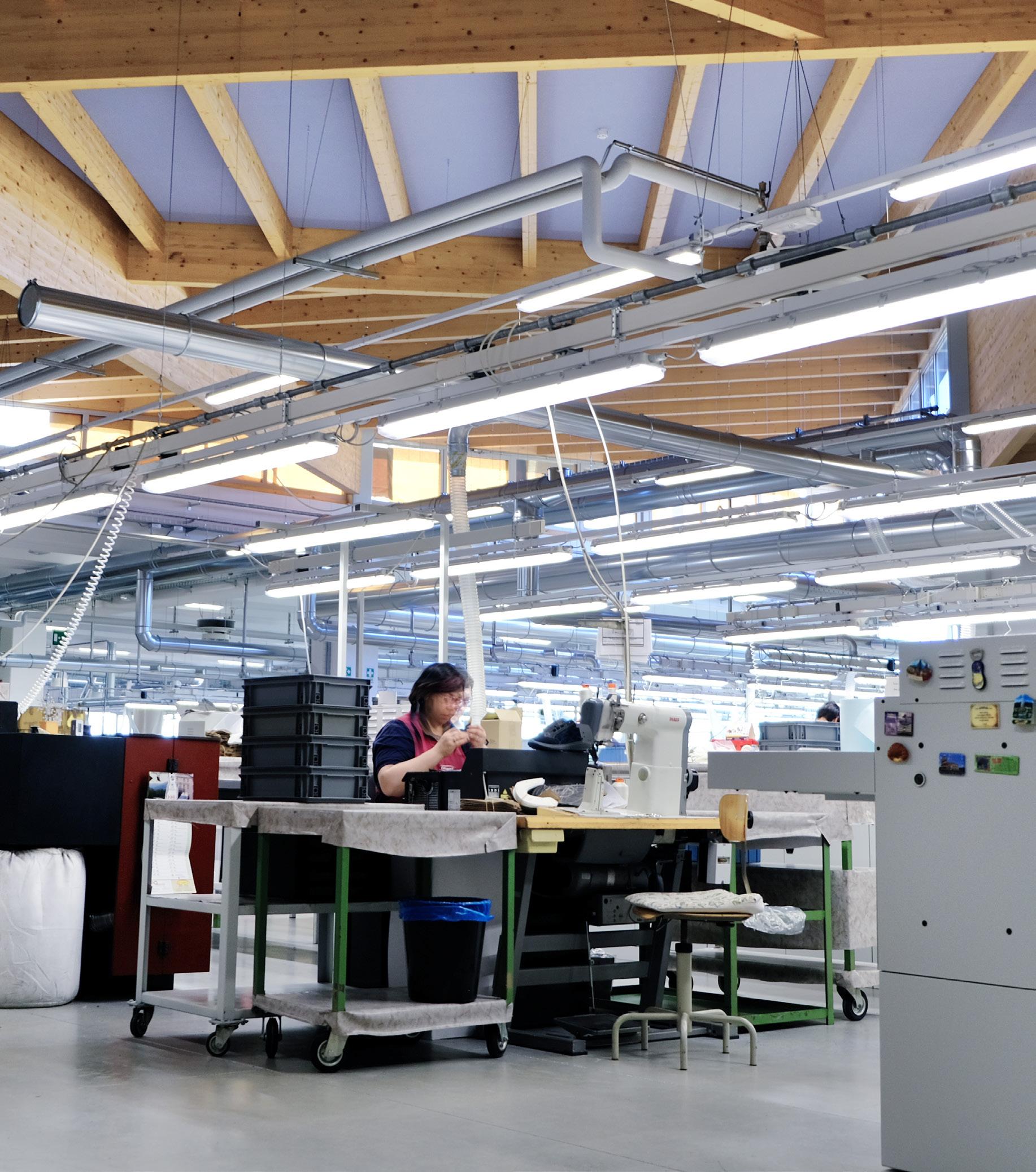
Allshoes has created insight into 78%* of the production locations of their direct suppliers
Better materials & design
Life Cycle Analyses as the basis for sustainable design
In collaboration with our partner Ecochain, we perform a Life Cycle Analysis (LCA) for all shoes in our range. With the LCA, we calculate the environmental impact and carbon footprint of our shoes and gain insight into where we can improve. This is how we apply our principle of ‘to measure = to know’. The calculation method we use for this and the results for a number of new models are currently being validated by an independent third party: Ecoreview. In doing so, we are taking a step further in terms of honest and transparent communication to the market.

New design for our shoe boxes
60%
Ink reduction
New shoe box designs with 60% ink reduction and made of FSC-certified cardboard, compared to the current design. For all Redbrick, Grisport and Strövels models. All other brands will follow in 2023.

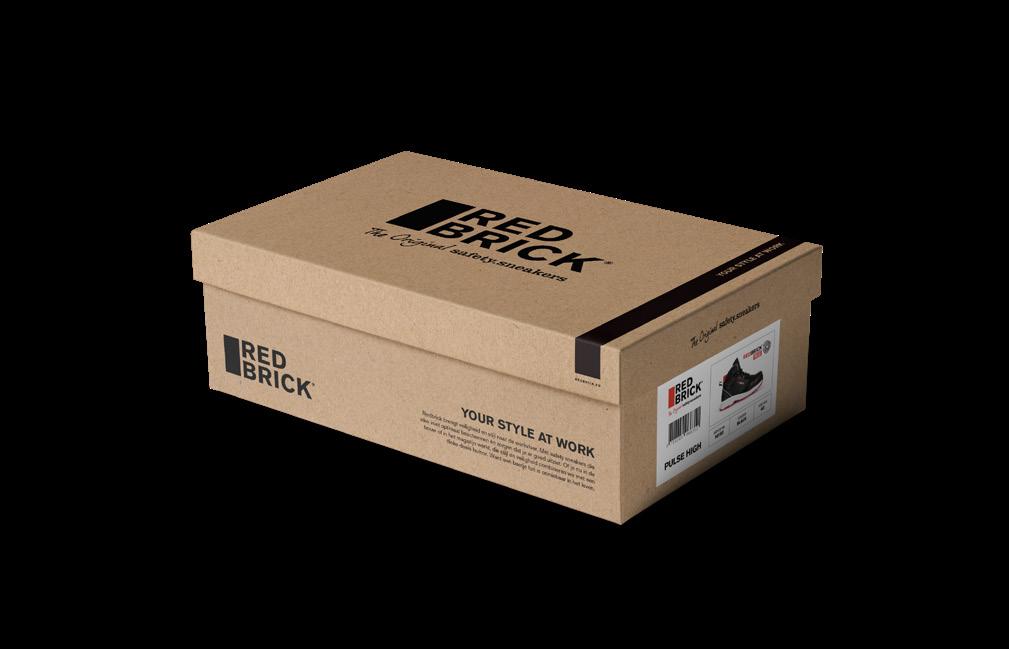
Use of water-
based ink
No leather in our new designs, but more sustainable alternatives such as microfibre.
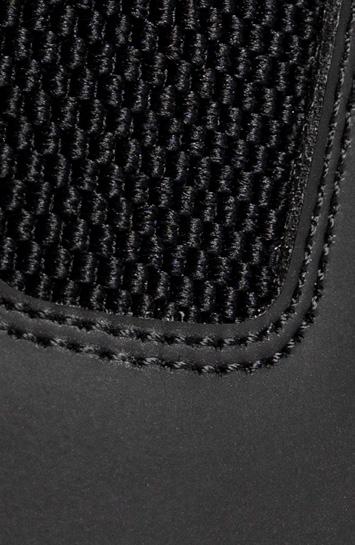
weight-based Recycled cardboard
FSC-certified
>50% Recycled material
Six new models with >50% recycled raw material developed.
Life Cycle Assessment
LCAs as a starting point for more sustainable choices in the design process.
Redbrick Pulse Boots
The Pulse collection consists of robust safety shoes with Redbrick’s signature, trendy look. The collection is being expanded to include resilient work boots. Traditionally, boots are often made of leather. We have made the bold choice to opt for a different material: microfibre.

Material selection is one of the most important factors in making collections sustainable. On average, leather production uses 1,5 times as much CO2* compared to materials such as microfibre. On top of that, leather is difficult to recycle and a huge amount of water is required during production.
Microfibre resembles leather in terms of qualities, but is less harmful to the environment. The use of imitation wool lining means these products are animal-free as well. In addition, the adhesive used is water-based.
Leather vs microfibre
A frequently heard reason for using leather is that leather would last longer than a material like microfibre. In this context, some studies see leather as a waste product of the livestock industry. This would result in a lower environmental impact than a co-product: a product deliberately produced alongside the main product.
At Allshoes, we believe leather is a co-product and we choose to substitute leather for materials with less environmental impact in new products. The Life Cycle Assessments we have performed for our footwear provide us with insight into their impact and are leading for our choices in material.
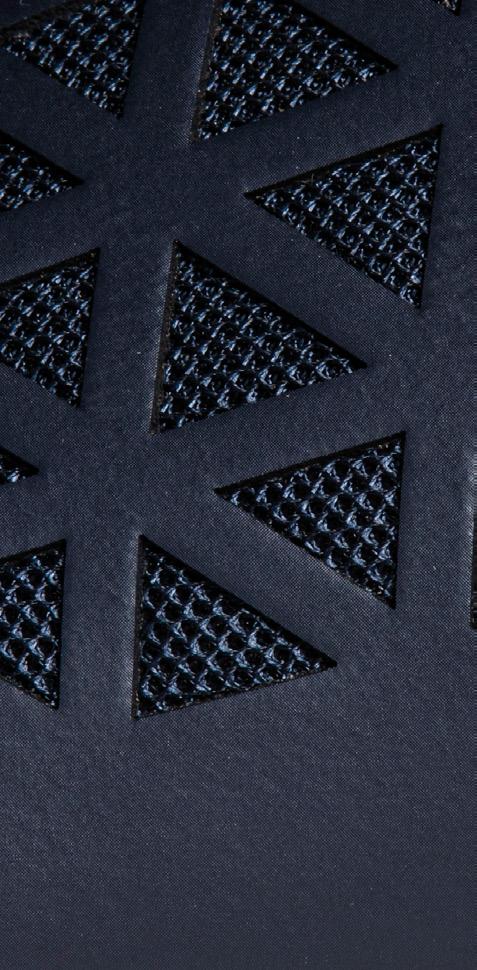
* In our calculations, we calculate a carbon footprint of 12.7kg carbon emissions for the production of 1kg of leather and 8.5kg carbon emissions for the production of 1kg of microfibre.
For the current models still made of leather, we work with the Leather Working Group (LWG) seal of approval where possible. The LWG is committed to building a sustainable future with responsible leather.
Safety footwear with >50% recycled material!
In addition to opting for leatherfree production, Allshoes is also incorporating a growing number of recycled materials into safety footwear. Under the brands Redbrick and Grisport we developed safety shoes using as much recycled material as possible.
Redbrick’s suppliers (AMF) and Grisport embarked on this design task, which proved to be no easy task. Protective footwear has to meet strict requirements, therefore, not every type of recycled material is suitable. Together, we eventually managed to develop new models with over 50%weight-based recycled material!
Trendy safety shoes made from recycled materials
These recycled material models are more eco-friendly, without any concessions on safety, comfort, quality and appearance! For Redbrick, in collaboration with AMF, we present the Redbrick Topaz, Tourmaline, Opal, and Pearl. Together with Grisport, we present the Grisport 103.
To expand the Safety Sneakers collection, we developed four new safety shoes with supplier AMF. All four with the distinctive trendy Redbrick look and made from more sustainable materials. Without compromising on comfort and
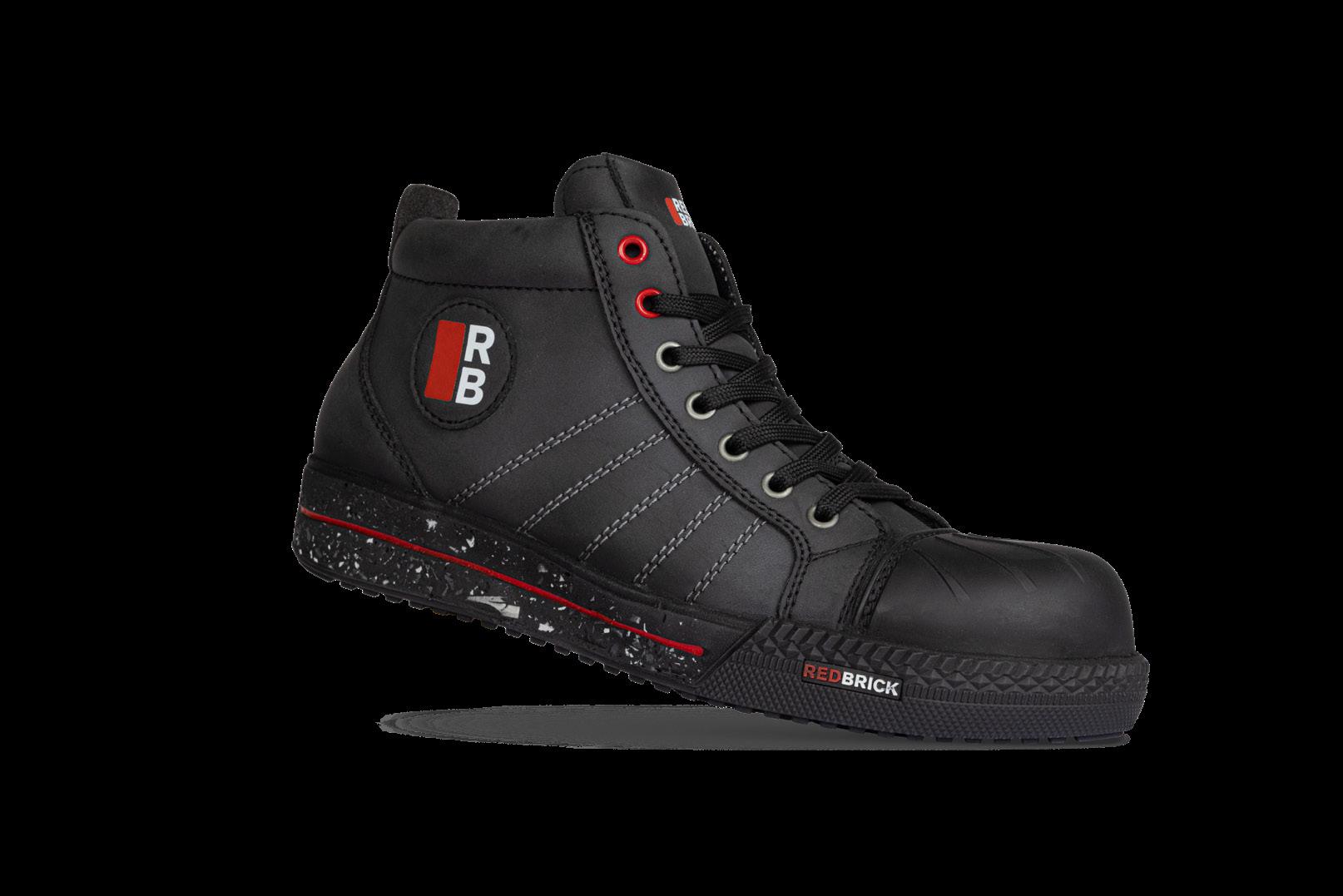
Two models are made of microfibre in safety class S3 (Topaz and Pearl) and two models of canvas in class S1P (Tourmaline and Opal).
These safety shoes consist of 53-57%weightrecycled raw materials. The exact percentage varies from shoe to shoe (high or low model) and choice of material (canvas or microfibre).
With these new models, we expect to save 40% carbon emissions compared to the traditional model of the Redbrick Onyx! These calculations are currently being validated by Ecoreview.
Grisport 103 A sustainable favourite
The Grisport 803 is our best-selling model. Popular for its fit, tough exterior and long service life. The good news? Soon, this shoe will be even more sustainable!
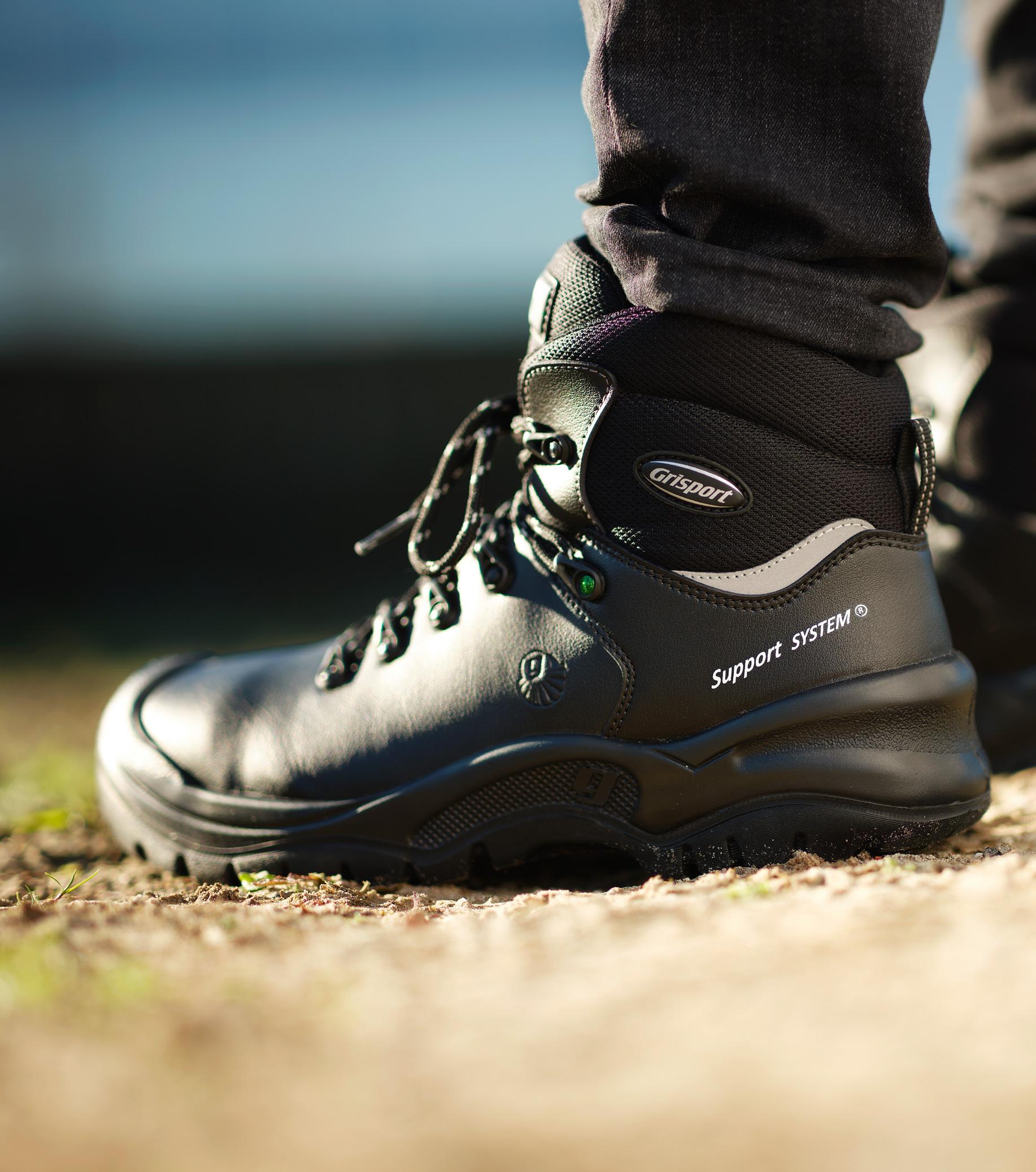
Together with supplier Grisport, we designed a recycled version of the 803. An alternative with less environmental impact has been found for almost every component of the shoe. Without compromising on the quality and comfort of the original shoe. A huge undertaking, especially since the 803 consists of more than 25 different parts. And with the added challenge of maintaining the same quality and comfort. The result is a safety shoe made of over 50%weight-based recycled materials.
Impact per Grisport model measured in carbon emissions
Grisport 803
Grisport 103
This new model is estimated to save more than 30% carbon emissions compared to the traditional 803! These calculations are currently being validated by Ecoreview.
10% Greenhouse gas reduction
(scope 1 en 2, 2018 as base year)
However... this came with a 2,9% increase of greenhouse gas emissions compared to 2021 (during COVID), due to an increase in employees and an expansion of the office.
Sustainable operations
In addition to changes at product level, we are also working on the sustainability of our operational processes. For example by reducing CO2 emissions caused by energy and the transport or reduction of packaging material and waste. We are not only critical of ourselves but also work with our suppliers on implementing changes.
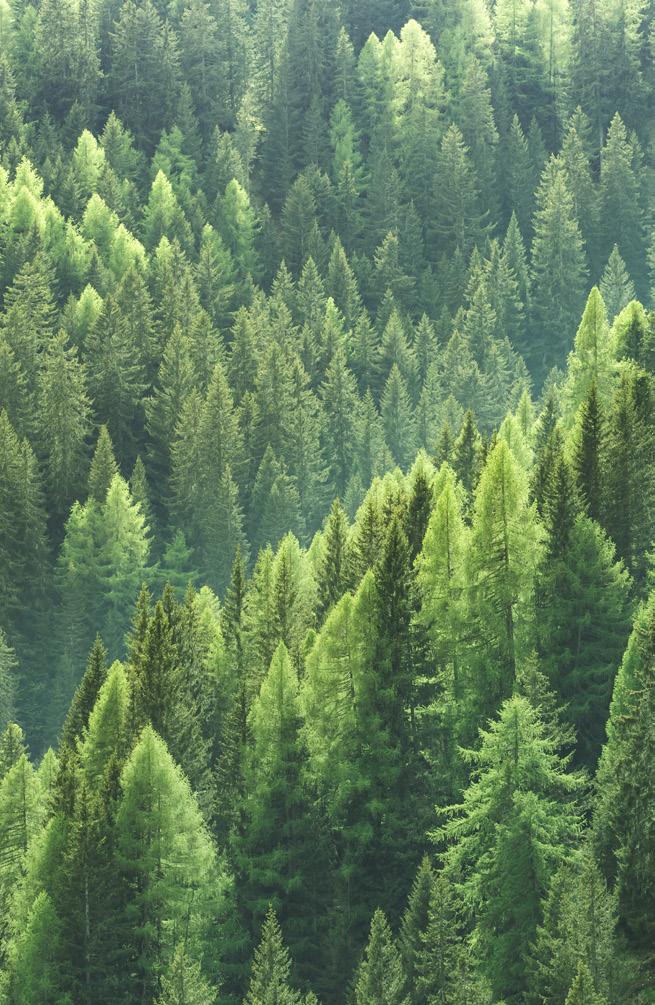
2% Greenhouse gas reduction
Per product sold (scope 3, 2020 as base year)
785 Trees planted
As part of a campaign by parent company Bunzl, Allshoes planted 785 trees in 2022 through the United Packaging Forest initiative. 50% in NL and 50% in Bolivia.
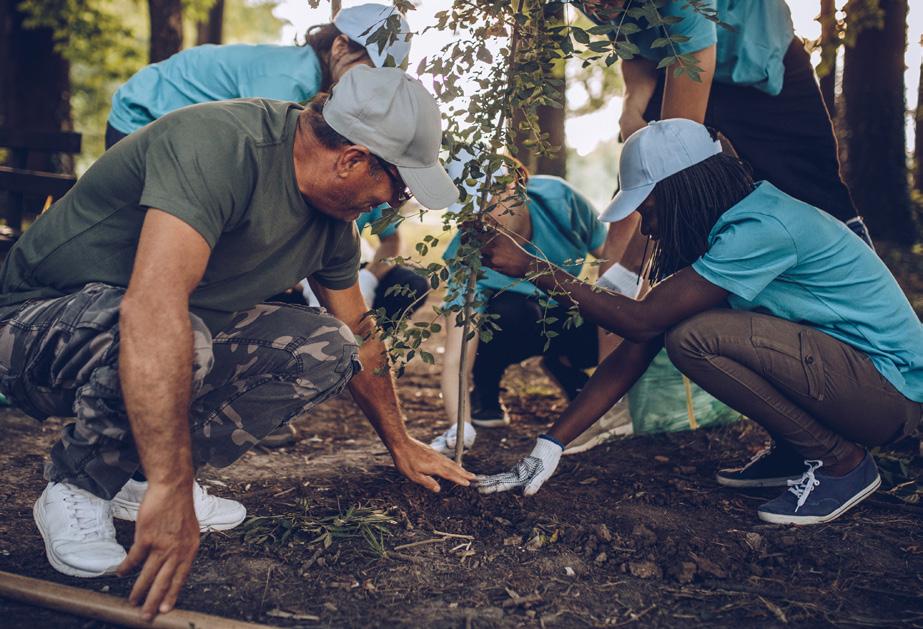
Where do these carbon emissions come from?
In collaboration with software platform Ecochain, we perform calculations regarding the environmental impact of our company (scope 1 & 2) and of our chain and products (scope 3). This impact is expressed in our carbon footprint.
When compared to the base year in which we started measuring (2018), we were able to reduce the direct environmental impact of our company (scope 1 & 2) with 10% last year. And we are pleased with that! However, compared to 2021, our emissions increased slightly in 2022 (with 2,9%). This is due to the fact that during the corona
period, our employees’ emissions mainly took place in their homes, where we had no visibility of them. In 2022, we were finally allowed to return to the office. On top of that, our office and staff numbers have grown in recent years. If we look at the emissions per employee, they are lower than they were during our baseline measurement, and we are committed to reducing them further.
With regard to the environmental impact of our suppliers (scope 3), we see a slight decrease of 2% per product sold. This is because – in new models – we are no longer using leather, but other materials with a smaller carbon footprint. We also observe an increasing number of customers opting for shoes with less environmental
impact. With the launch of the new models with recycled material in 2023, we expect to achieve more reduction next year.
We have made progress in reducing our carbon footprint across scope 1, 2 and 3 compared to our baseline measurements, and remain committed to meeting our 2025 targets. This also involves a deeper engagement with our partner Ecochain for further reduction steps in 2023.
10.540 Pairs of shoes returned in 2022 through CFA

CFA operational in 5 countries
Close the loop
With the optimum use of raw materials, waste streams must be converted into raw material flows. In our case, this means that materials from discarded footwear are converted into raw materials again.

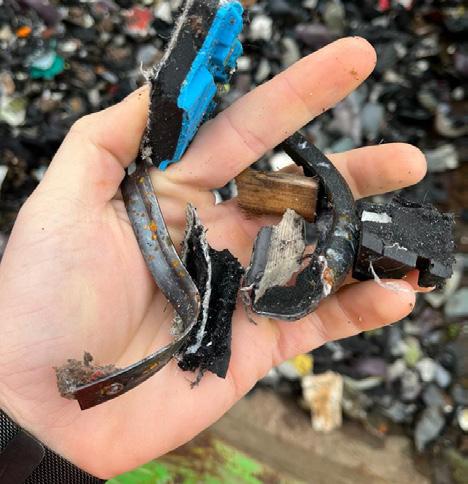

Next steps Extended Producer Responsibility
11.846 Pairs of safety shoes recycled* in test batches through CFA
371 Collection points CFA (dec 2022)
70 Locations End-user CFA introduction (Picnic linked to CFA, 70 locations)
Allshoes to spearhead an EPR for safety shoes
EPR = Extended Producer ResponsibilityAs market leader in protective footwear, we also take responsibility for our product at the end of its service life. The Circular Footwear Alliance (CFA), the collection initiative for used occupational and safety shoes which we cofounded, ensures that the shoes stay out of the waste stream, allowing the materials to be used as new raw materials. This is how we encourage the circular economy.
The Circular Footwear Alliance has grown significantly and was professionalised further in 2022, which includes the arrival of the CFA Officer. Partly due to this, as many as 128 new collection points were added in 2022!
From these collection points, the shoes are sent to a central location after which they are recycled. With so many different types of safety shoes, the dismantling process still has its challenges. Each shoe is constructed differently and often contains different materials. By partnering with dismantling
partners, we are looking for the ideal way to recycle raw materials at the highest quality possible.
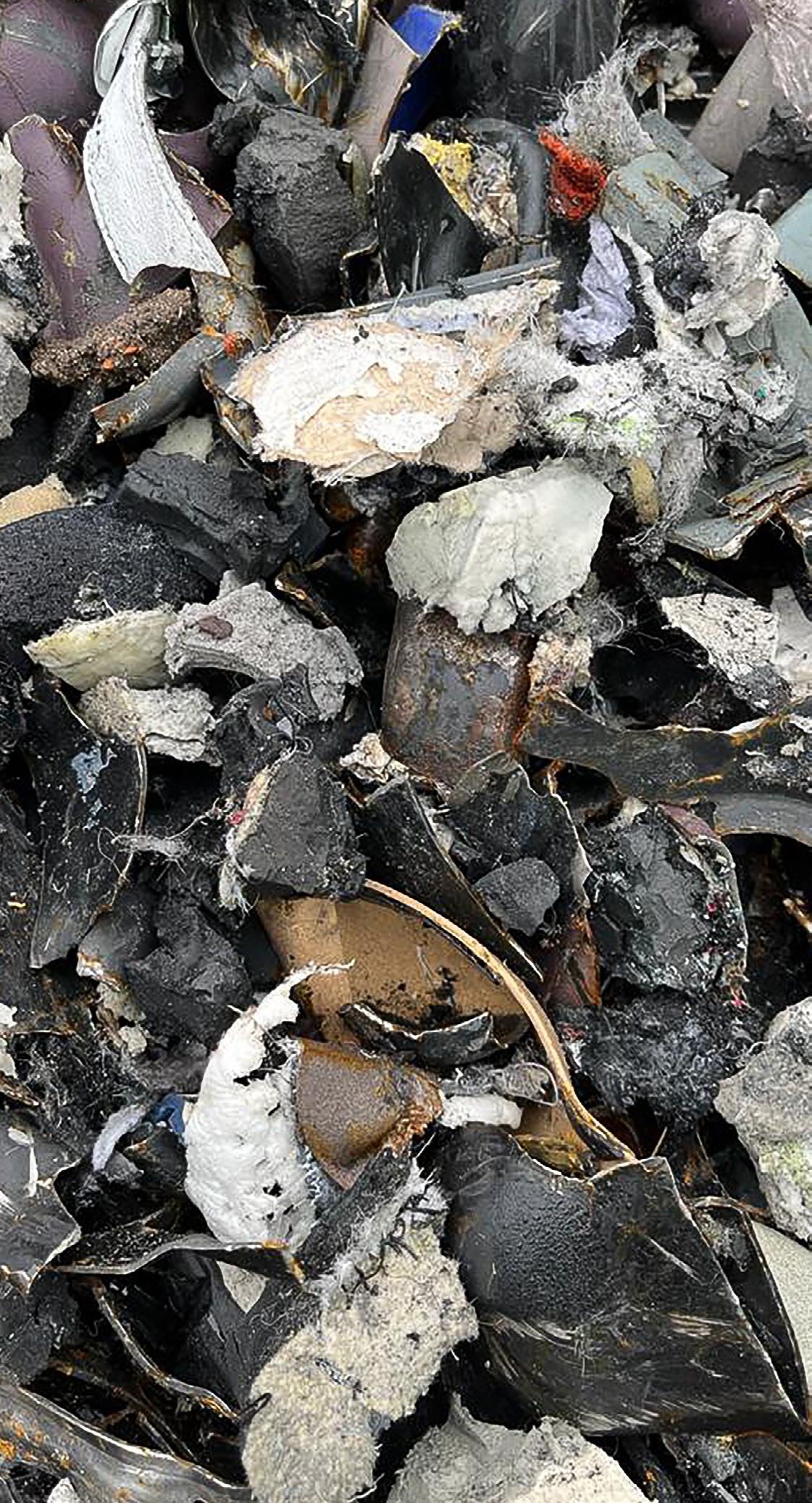
The next step within Allshoes is a focus on ‘design for dismantling’. In this process, we examine how to design a shoe that can be taken apart in just a few steps without compromising on the quality of the shoes.
Huge challenges, such as high-quality recycling, become easier when there is a solid support base. Through the CFA, Allshoes therefore wants to promote Extended Producer Responsibility (EPR) for safety footwear. This legally obliges manufacturers (and importers) to collect used safety shoes and return them to the chain. Currently, the textile industry is working hard on an EPR for textile (this includes occupational wear). We follow these developments closely and are inspired by them. In the coming year, we will also ask other safety footwear manufacturers to join the CFA as partners.
Do
>400 Pairs of shoes
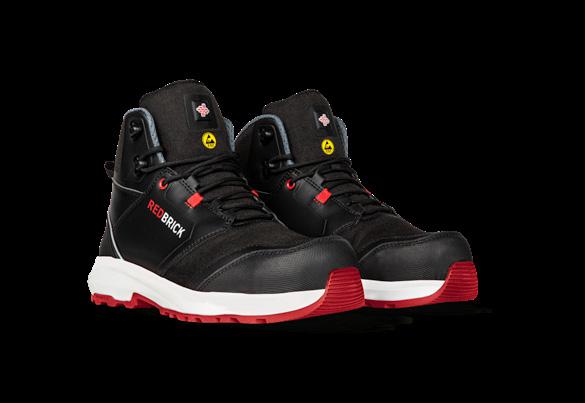
Supporting people

‘Supporting people’ goes beyond helping our own employees. It includes people across the globe. We support our producers’ labourers and various charities such as the Vluchtelingenboot in Amsterdam, HVO Querido and Leger Des Heils. In December alone, we donated over 400 pairs of safety shoes to organisations we care about.
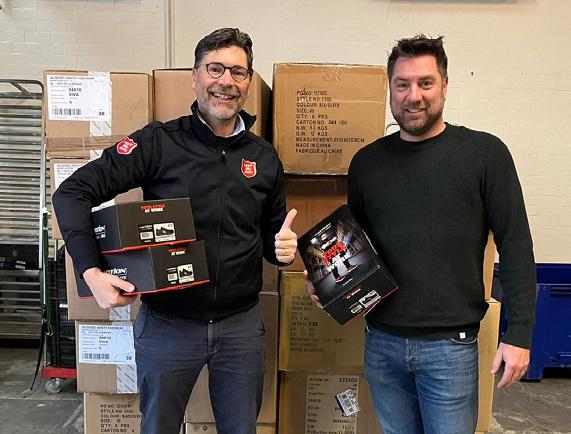
Production locations of our direct suppliers made transparent
3 days for volunteering
Each employee is granted 3 days for volunteering each year
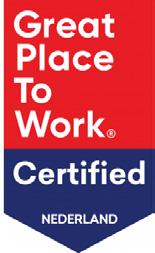
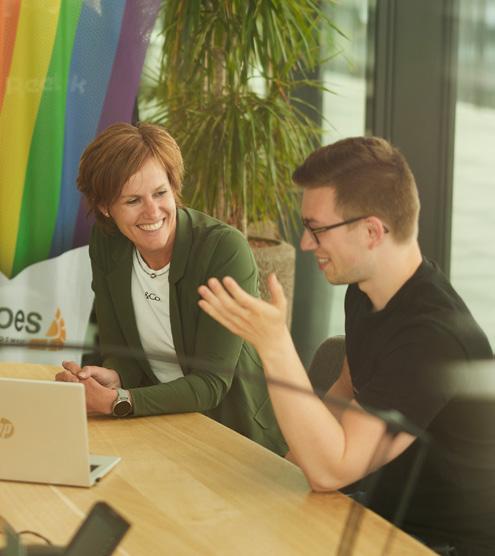
Responsible supply chain through transparency
In line with the ‘Transparency Pledge’ to which we have committed ourselves in 2021, we are helping to improve the working conditions at our producers and their suppliers. We have come to understand that it is very complex to create transparency in our supply chain, since we are dealing with a lot of different stakeholders.
In order to promote transparency within the clothing and footwear industry, the ‘Transparency Pledge’ requires us to make our production sites known. For this purpose, we have published a factory list of our suppliers on our website. It was last updated in May 2022 and we were not able to include all production locations of our suppliers just yet.
Allshoes as Great Place to Work
Whereas some suppliers are perfectly happy to cooperate, others are not very straightforward about participating or not and about which data they want to share about their own factories. Let alone share data from their own suppliers. This is still a common occurrence in our line of business.
Creating transparency is thus quite a challenge. We are currently researching how to make Tier 1, 2, 3, etc. insightful without sharing competitively sensitive information.
Eefje Hutjes HR & TALENT ADVISOR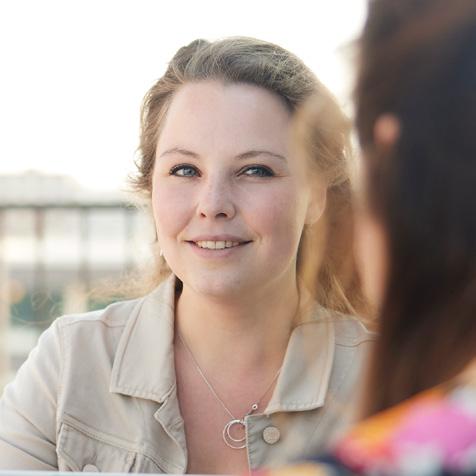
We are immensely proud to be able to call ourselves a ‘Great Place To Work’.
“As of May 2022, we can call ourselves a ‘Great Place to Work’. This certificate reflects the level of satisfaction among our employees. For this certification we also measure the level of pride and confidence in our organisation.
The certificate compels us to think about improving the way we do things even further. By doing research, we encourage feedback from our employees. A lot of new ideas are formed based on this. It is a fact that satisfied employees stay on longer and attract new talent. In this way we are building a strong team where values such as respect, friendship and credibility are important.
*Tier 1 is the tier of direct suppliers to Allshoes Safety Footwear. Each ‘Tier’ is a new layer of producers or suppliers. Tier 2 suppliers are the suppliers of our suppliers. Every time a new tier is mapped, a larger part of the chain becomes visible and thus the chain becomes increasingly transparent.
That’s how we grow as an organisation and when we can be proud. Proud of our company, our employees, and proud of the steps we are taking in sustainability and innovation.”
Driving change
A sustainable future requires new innovations and a common approach. We are continuously looking for opportunities to not only improve our own business operations, but also to be a driving factor in the sustainability of our industry. By focusing on permanent, sustainable and positive change, we aim to secure the well-being of future generations.
2020
Discovering the role of safety shoes in preventing back problems in the workplace.
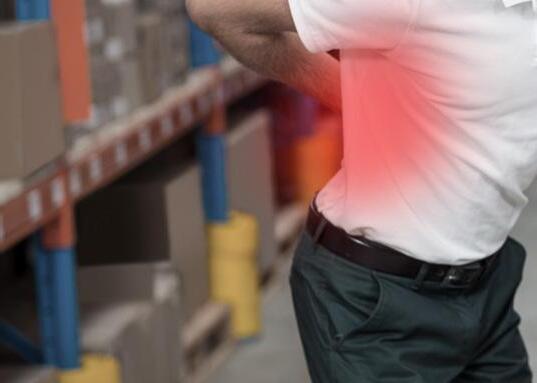
2021
2022
Validating the prototype of the Smart Safety Shoe.
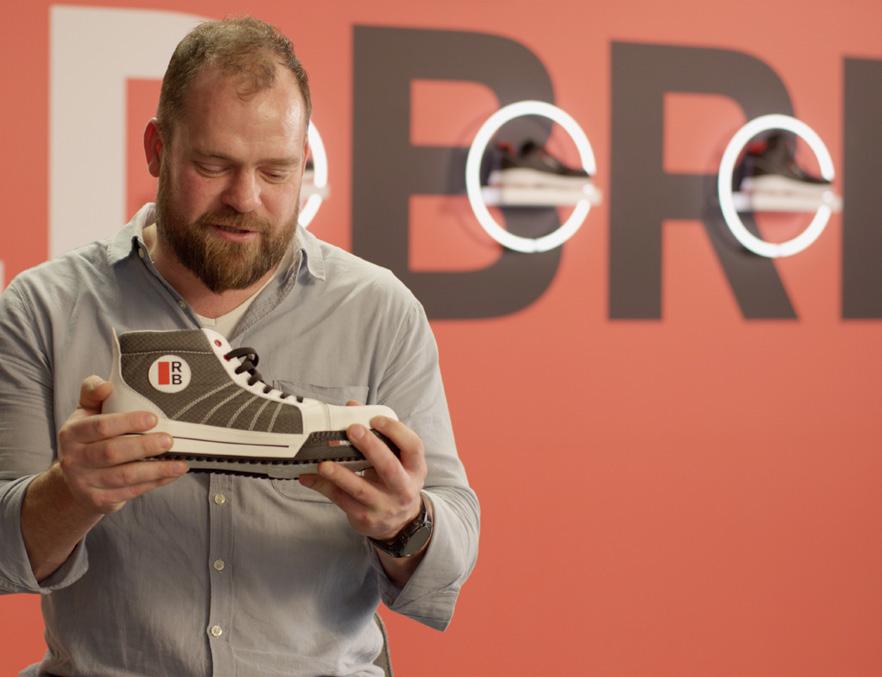
Concept development of the Smart Safety Shoe and a smart sole.
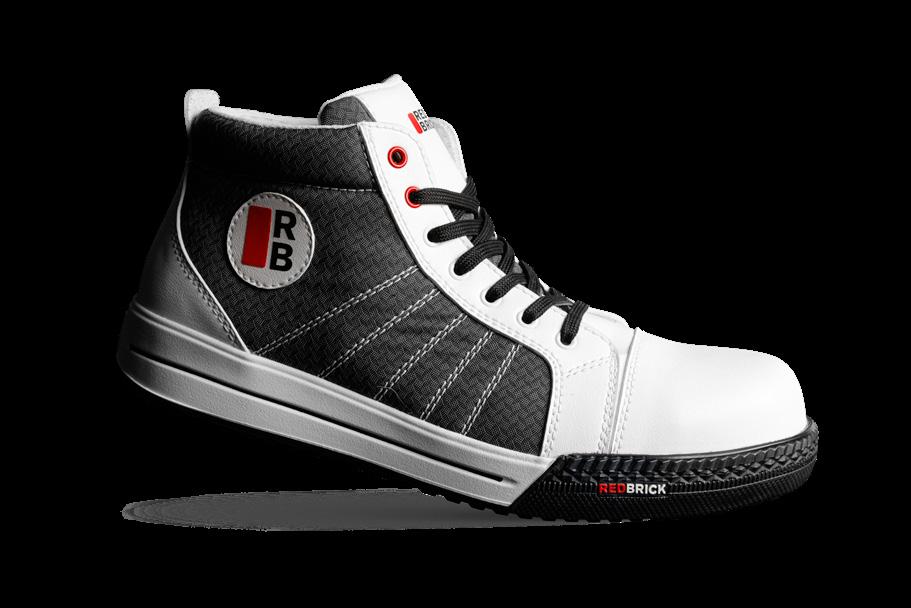
Smart Safety Shoe
Prevention is better than cure! This notion formed the basis of the Smart Safety Shoe. In the Netherlands, 1 in 3 workers in warehouses and construction regularly perform physically demanding work. A link between a great deal of physical work and back complaints has been established in several studies. Complaints that can cause employees to call in sick or even become (partly) unfit for work. While this is incredibly unpleasant for the employee, it also imposes costs* on the employer.
The Smart Safety Shoe offers a solution to this. This smart safety shoe is equipped with sensors that help prevent complaints for the wearer of the shoe. The shoe recognises unsafe lifting positions in various conditions and can ward wearers for potential dangers. This is safer for the employee and beneficial for the employer if it leads to less absenteeism.
Producing this shoe requires a great deal of research. Allshoes has been working intensively with Delft University of Technology (TU) in recent years. Research into a smart safety shoe began in 2020. The key question: what actually makes a ‘smart’ shoe smart? This resulted in the concept: the Smart Safety Shoe designed to actively protect the wearer from workplace hazards. In several stages, the initial prototype was gradually refined. The final phase of this project was initiated in 2022, with a student specialising in Design For Interaction converting the prototype into a physical, usable product.
The time has come for the final touches. We are gearing up to produce this shoe of the future. We expect to launch the Smart Safety Shoe by the end of 2025.
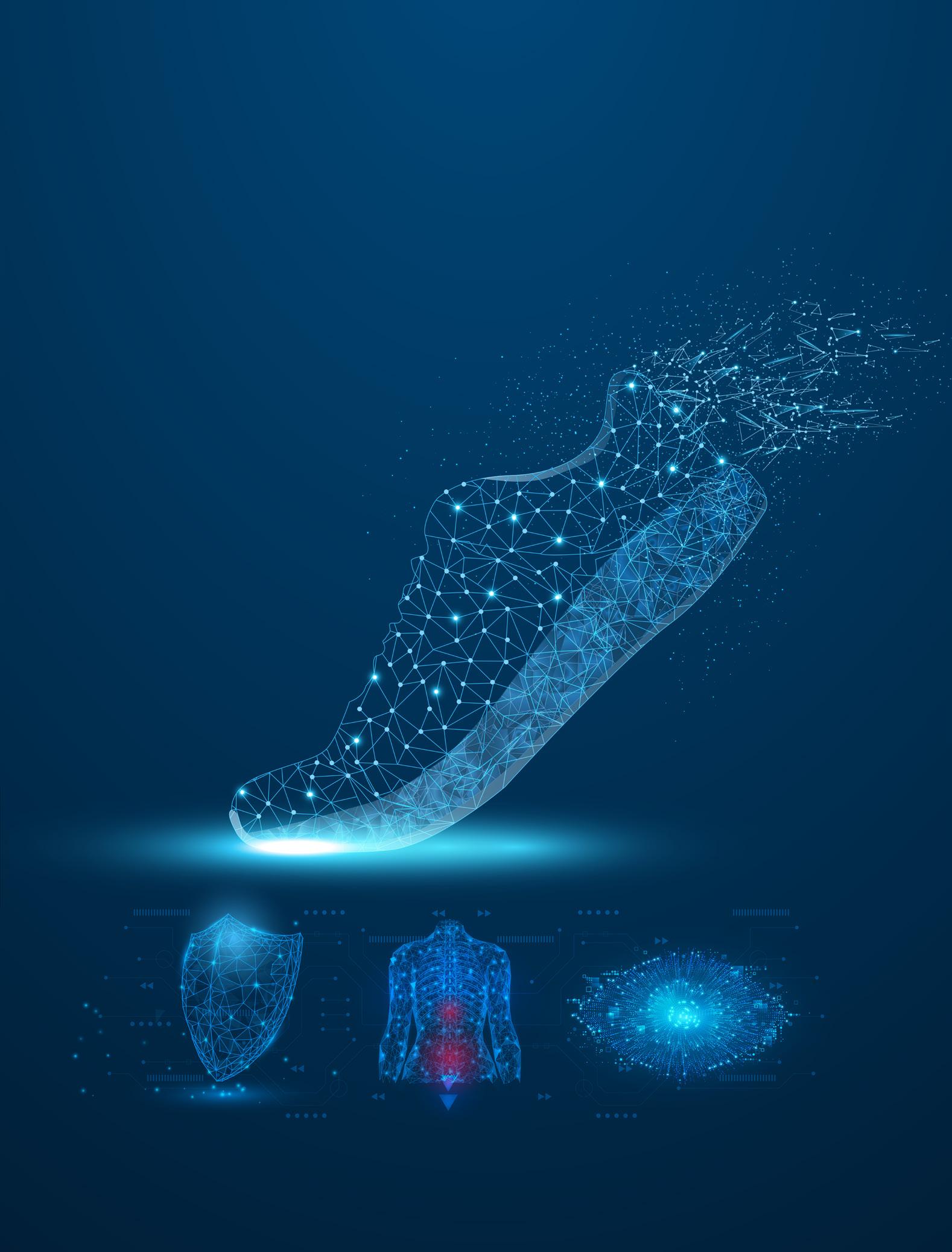
Smart Safety Shoe
Source: TNO.
