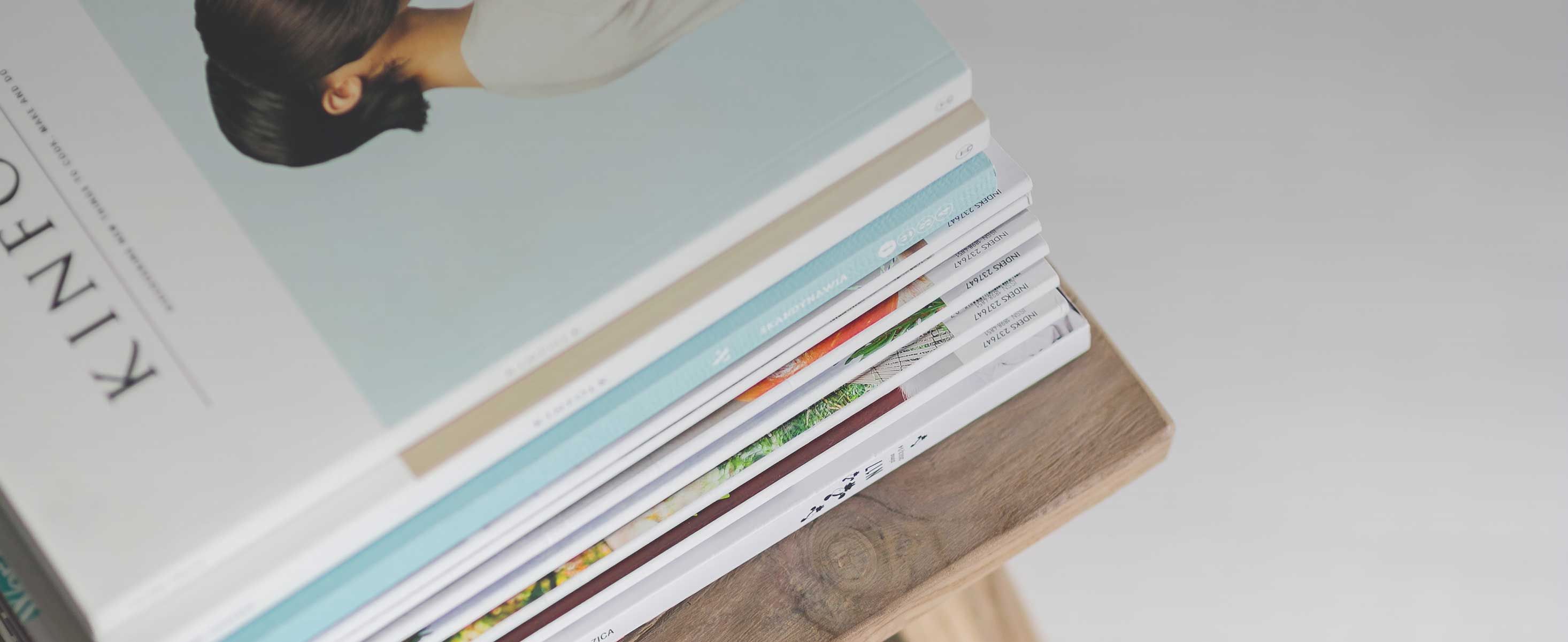
2 minute read
Importance of Containment in Abrasive Blasting
Uncontained emissions and debris from surface preparation operations, such as paint, coatings, paint chips and primers, can be toxic and lethal to aquatic life, can leach into the soil and be taken up by plants, bioaccumulate up the food chain and ultimately effect humans. The goal of containment is to prevent blast emissions and debris from leaving the worksite, where they can be effectively collected for disposal.
The most important consideration regarding particulate dust is its level of toxicity, which depends upon three interdependent factors: the substrate being blasted, the contaminants being removed, and the type of blast media used. Substrates such as concrete and sandstone masonry, for instance, are partially comprised of toxic materials; the more abrasive the blast media, the more toxic substrate is forced into the air in the form of dust during blasting. The same holds true for the toxic contaminants being removed, such as paint chips and many types of coatings.
Advertisement
One of the chief advantages of wet abrasive blasting over dry blasting is the reduced requirement for containment. Because the emissions and debris are encapsulated and weighed down by water, they can be effectively contained with fewer preventative measures.
Ground containment is the most basic form, consisting of overlapping, anchored tarps overlaid with geo-textile material. Geo-textile material is particularly valuable to the wet abrasive blaster: this light-weight material, with a texture similar to cheese cloth, allows water to pass through while filtering abrasive and debris. At the end of the job, the geo-textile fabric is simply wrapped up and deposited in drums or other suitable containers for disposal.
When hazardous runoff is a consideration, the blaster can construct a berm to catch spills from heavy machinery, storage tanks and drums. Depending on the type of contaminants to be contained, the berm can be constructed at heights ranging from inches to several feet, with metal, wood or foam and an outer layer of rubberized or polyurea coating, and lined with geo-textile fabric. A submersible pump can be placed inside the berm to transfer waste water into a collection container or drum barrel.
When the blast site is located near open water, residences, urban environments and other high-traffic areas, stationary structured containment is required. In these settings, traditional dry blasting requires full containment – or “hoarding” – where the blast area is hermetically sealed to prevent non-filtered air, emissions and debris from escaping. For vapor abrasive blasting, partial containment is usually sufficient, and can be achieved by enclosing the area with tarps supported by a rigid or flexible structure, or a plywood barricade. Due to the inherent dust-suppression of vapor abrasive blasting, ventilation and exhaust fitration are not required in most cases.
On large projects, often the most cost-effective containment is a portable structure. For example, blasting operations on an overpass can be contained with tarps suspended from trusses by cables over ground containment. As work progresses, the rigging can be moved to contain the next section. A bridge over an open body of water might require a sophisticated, engineered structure that not only contains and collects emissions and debris, but provides a platform for workers to stand on.
In most cases, it is up to the blaster to recommend, design and construct containment that satisfies the project requirements.