
8 minute read
AMC member collaboration combats equipment wear
Together, Alberta Industrial Heat Treating Inc. (AIHT) and Apollo-Clad Laser Cladding are laser-focused on combatting equipment wear and offering new possibilities of repair for Canadian farmers. The two Edmonton, Alberta-based units of the parent company Apollo Machine and Welding Ltd. (Apollo) have joined forces to develop innovative solutions for wear and corrosion protection that have taken the oil and gas sector by storm. Now, they are offering these same state-of-the-art solutions to agricultural manufacturers.
By Paula Schuck The partners
Advertisement
Apollo-Clad Laser Cladding is the laser cladding division of Apollo which has been around for 14 years providing laser materials processing solutions to the oil and gas industry. Apollo-Clad’s main products are laser clad coatings (or overlays) for wear and corrosion protection of drilling components used in oil and gas exploration. The business has expanded into mining, pulp and paper, defense, plastic processing, rail, nuclear, aerospace, and now agriculture. The benefits of laser clad coatings are vast, and Apollo-Clad has made significant investments in automation and process sensing to improve productivity and be cost competitive with existing welding solutions: better performance at a cheaper price. The Apollo-Clad facility currently employs 34 engineers, machinists, grinders, and support staff. Including the other three business divisions, Apollo now has over 200 employees. The business is growing, looking to hire labourers, laser operators, and engineers. Alberta Industrial Heat Treating (AIHT) is the traditional heat treatment division of Apollo. AIHT provides critical heat treatment services including quench and temper,
precipitation hardening, solution annealing, stress relieving, bake outs (hydrogen control for welding), normalizing, and full annealing. AIHT also offers state-of-the-art gas nitriding, gas carburizing, and induction heat treatments to tailor the surface properties of components for specific customer applications. AIHT is comprised of a team of eight people and is currently looking to hire and train labourers and operators. Henk Vogelaar, Senior Sales Executive at AIHT, says right now business is thriving, and the company has responded by purchasing new equipment to meet the short lead time demands their customers have come to expect. Together, Apollo-Clad and AIHT complement each other, offering distinct but related products and services to address issues of wear and corrosion, which are virtually universal.
In the last 10 years laser cladding has broken through as a real solution for industrial-scale manufacturing. The process involves using high powered lasers to generate a molten pool. Additional material is added to that pool in either wire or powder form,
which then cools quickly to create a high-quality, fully metallurgicallybonded coating. Gentry Wood, a senior research and development engineer for ApolloClad, calls laser cladding versatile. “Laser cladding can be used as a repair technology (chemistry match), coating technology and even as a path to metal 3D printing, known to those in the additive manufacturing world by the name ‘Directed Energy Deposition’ or DED. All the benefits of laser cladding are rooted in the laser heat source. Lasers provide precision application of heat, which minimizes material mixing and other negative side effects of excessive heat input making it a great technology for dissimilar metal coatings. The technology is routinely used to repair parts of a range of sizes with the incorporation of robotics and large CNC systems. The opportunity to fix components that are only worn out locally is immense, and we see laser cladding as a green technology for its ability to capitalize on the underappreciated “Re-use” of the 3Rs.” (See Figure 1.)
For complex surfaces, large surface areas, and components with internal features that require treatment, traditional heat treatment processes such as nitriding, carburizing, or induction may be an alternative to laser clad overlays. These processes are completed in batch processes that take advantage of the hardening capabilities inherent to a specific material and its response to heat and potentially the addition of nitrogen (nitriding) or
carburizing (carbon) into the surface. Each technique has its own niche applications, but the AIHT advantage comes from a combination of digital process control and support in process development and R&D from the Apollo team of Ph.D. metallurgists. “AIHT and Apollo-Clad have a unique relationship with customers as we can offer metallurgical Lab services to do R&D for our customers and offer a solution, either from AIHT services or Apollo-Clad, tailored to the customer's unique application,” says Henk Vogelaar, Business Development at AIHT. (See Figure 2.)
Apollo-Clad has commissioned its ninth state-of-the-art laser cladding cell, which is focused on fast, highvolume manufacturing. The system has been custom designed to meet the needs of new agricultural customers, who are utilizing Apollo’s nickeltungsten carbide products to improve the performance and longevity of equipment for mechanical weed seed control during harvesting. The laser cell has been outfitted with a full sensor suite to monitor and control the process for maximum productivity and superior quality. This system is also likely to be used for Apollo’s work on industrial applications of laser additive manufacturing. (See Figure 3.) Recently, a second gas nitriding furnace was commissioned to offer this in-demand service for stainless steel products as an effective alternative to liquid nitriding. A state-of-the-art induction heat treatment unit with automated process control, increased working envelope, and superior case depth (hardened depth) for steel components has also been added. Apollo-Clad and AIHT have partnered to develop a patent-pending ApolloShield™ process, which combines the application of laser technology with AIHT’s traditional heat treatments
Figure 1: Laser cladding of a stainless-steel coating on a high carbon steel R&D test piece for a railway application. Figure 2: Induction heat treatment of a cylindrical alloy steel shaft.


Figure 3: Cutting edge laser cladding system for agricultural manufacturing.
to maximize the hardness and case depth potential for a given material. This revolutionary new process is poised to be a disruptive technology for industries that need these types of wear protection and surface performance modification. Both Apollo and AIHT are excited to continue to develop the technique and find new applications to demonstrate its potential.
On AMC
AIHT and Apollo Clad have both been members of AMC for two years now. “We consider it a strategic advantage to be a member of the AMC organization, and we look forward to meeting the people and businesses that comprise our Canadian agricultural sector through continued participation in upcoming conferences and events,” says Wood. “Canada’s farmers have demands for cost and quality, and we think that our laser cladding solutions should provide the value they are looking for with a 'Made in Canada' solution they can afford. We are excited for the future, where we feel we have only scratched the surface of the potential of lasers in Canadian manufacturing.” “AMC gets members in front of the right people to discuss solutions to help our customers. It is a big family of companies that support one another and help AMC and our company grow,” says Vogelaar.
Why ‘Made in Canada’ is important to their business
“With COVID-19 being so serious right now, it’s comforting knowing that right here in our backyard we have our 'Made in Canada' companies that can
Modern solutions to wear and corrosion
A proven leader in the field of heat treatment

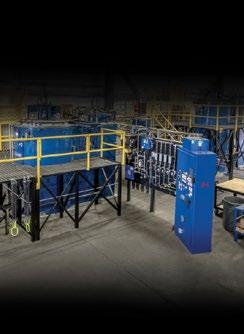
• Laser cutting • Laser welding • Laser cladding • Laser hardening • Additive manufacturing
780-980-5231 apollomachine.com Fully Equipped Metallurgical Lab • Gas nitriding • Gas carburizing • Induction heat treating
780-988-7798 aiheattreating.com
meet any supply or service need. We need more than ever to support each other to grow and excel,” says Henk Vogelaar. “We are a Canadian, family-owned business that takes great pride in our industry-leading products and services. Our push for productivity and quality has helped keep manufacturing jobs here in the country, and it is vitally important that we meet the needs of local customers who are also members of our community," Gentry Wood of Apollo-Clad comments. "'Made in Canada' means world-class quality, ingenuity, and reliability. Purchasing products 'Made in Canada' means supporting our local manufacturing industries, which strengthens our communities and provides prosperity here at home.” “As a Canadian manufacturer, we at Apollo appreciate those who recognize the impact of supporting our industry within our borders. As we compete internationally, it is becoming more important to work together strategically to navigate the complex ecosystem and unpredictability of global markets.”
See more of what Apollo-Clad & AIHT do here:
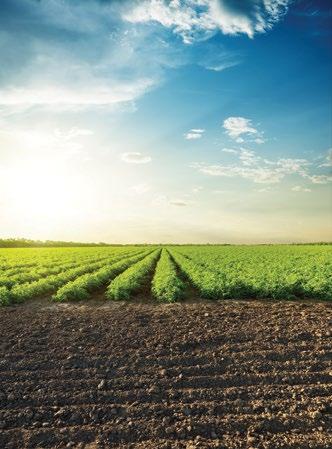
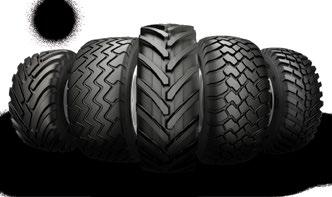
AMC Advocates
One United Voice for Our Industry
AMC Collaborates
National Catalyst for Thought Leadership
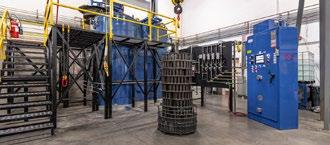
Figure 4: New gas nitriding system for stainless and alloy steels at AIHT.
www.yokohama-oht.com @yokohamaohta
NEW COMPANY NAME— SAME GREAT FARM TIRES.
The wide range of Alliance tires—including cutting edge VF flotation tires, fast flotation, rugged R-1 and turf tires, and more—is now under the umbrella of
Yokohama Off-Highway Tires America, Inc.
That means an even bigger global R&D, engineering and manufacturing team to back up your familiar Canadian reps. And we still promise warranty coverage up to 10 years and our convenient Warranty Wizard app. So our new name backs up our long-standing promise: any size, any spec, any challenge. Alliance is ENGINEERED TO KEEP YOU AHEAD.