
7 minute read
Member Spotlight
by AOPA
FACILITY: RogueProsthetics
OWNER: Sheri Hatt, MHI, LPO
LOCATIONS: Bastrop and Lufkin, Texas
HISTORY: 11 years

Owner Sheri Hatt, MHI, LPO, has treated several patients who have overcome great obstacles to successfully use prostheses.
One Patient at a Time
Texas facility prioritizes individualized care
Sheri Hatt, MHI, LPO, has been a practicing O&P clinician for more than 20 years. After working for two different practices in her early years as a clinician, “I decided to go ‘rogue’ and open my own business,” Hatt says. She launched Rogue Prosthetics in 2011.
Since then, Hatt has enjoyed providing patient care by her own standards, which sometimes involves extra unreimbursed hours of work. Her diligence has paid off with company growth: She opened the facility as a solo practitioner, but Rogue has grown to two locations and five employees, including another clinician. Throughout the expansion, Hatt has stayed true to her company’s stated mission: to help one amputee at a time meet their mobility goals.
One key differentiator at Hatt’s facility is that she and her colleagues look at the whole person, not just their disability. “We actually sit down and listen to the patient,” she says. “Our initial interview may take a whole day. We also visit each patient’s home to analyze conditions and come up with a plan that allows them to be successful using a prosthesis at home.”
Hatt is open to new technology and has used 3D scanning and printing—but admits she usually comes back to hand skills, where she feels she has more control. The facility uses an O&P practice management system, which streamlines the work and has eliminated the need for additional administrative staff, according to Hatt.
Rogue regularly employs outcome measures. “We use AMPPro [the Amputee Mobility Predictor assessment tool] to evaluate patients’ progress every three to six months. Our practice management software also includes a tracker that allows us to enter information and monitor when patients reach their goals.”
Hatt has treated several patients who have overcome great obstacles to successfully use their prostheses. “I have one patient I work with every week,” she says. “He is 6 feet, 5 inches tall and weighs 364 pounds. He couldn’t afford a prosthesis after his amputation, so he spent a year in a wheelchair before we even saw him.” Hatt was able to get donated components and fit him for a leg, “but we were concerned that because of his size and inactivity, he wouldn’t be able to use it.” Hatt met with the patient regularly, and he is now walking with a walker and about to graduate to a cane. “I honestly don’t think he would be as successful if he’d gone anywhere else,” she says.
That sentiment also applies to another patient, who lost his leg at 73. “He was almost not able to move ahead with a prosthesis because he was so upset,” she recalls. Hatt worked closely with him—and he is now so adept with his prosthesis that he participated in Rogue’s annual limb loss skydiving event.
In addition to sponsoring skydiving, Rogue works with a local organization that helps underfunded patients gain access to prosthetic care. The company also works with the Texas Ramp Project to identify homes that need a ramp in case of a fire.
In another effort to support families, Rogue made room on its website for a group called Careopolis, an online “caring community” for families to coordinate care for their loved ones. “We had more than 700 people sign up, so even though we are not affiliated with the group, we want to make it available to our patients and their families,” she says.
Hatt has big plans for the future, both in growth that stalled during COVID and in a greater emphasis on education, including a partnership with Texas A&M Agrilife to provide a diabetic education program.
However quickly the company grows, Hatt’s love for her work will remain consistent. “I’ve been in this field for 33 years,” she says, “and I don’t feel I’ve worked a day in my life.”

Deborah Conn is a contributing writer to O&P Almanac. Reach her at deborahconn@verizon.net.
COMPANY: Icarus MedicalInnovations
OWNER: Dave Johnson
LOCATION: Charlottesville, Virginia
HISTORY: Three years
Dave Johnson
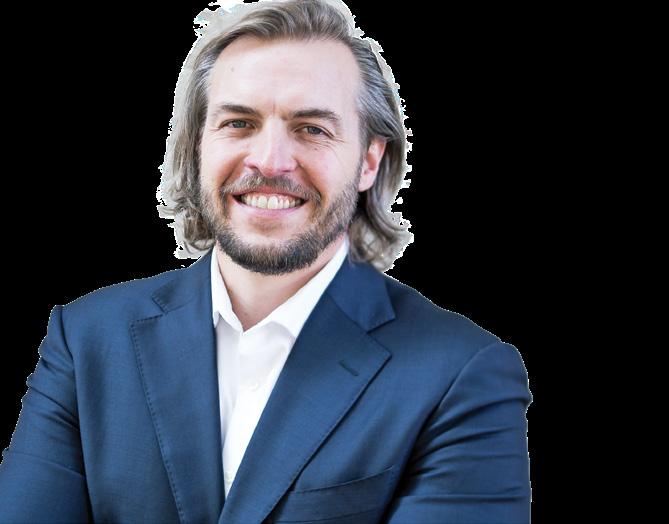
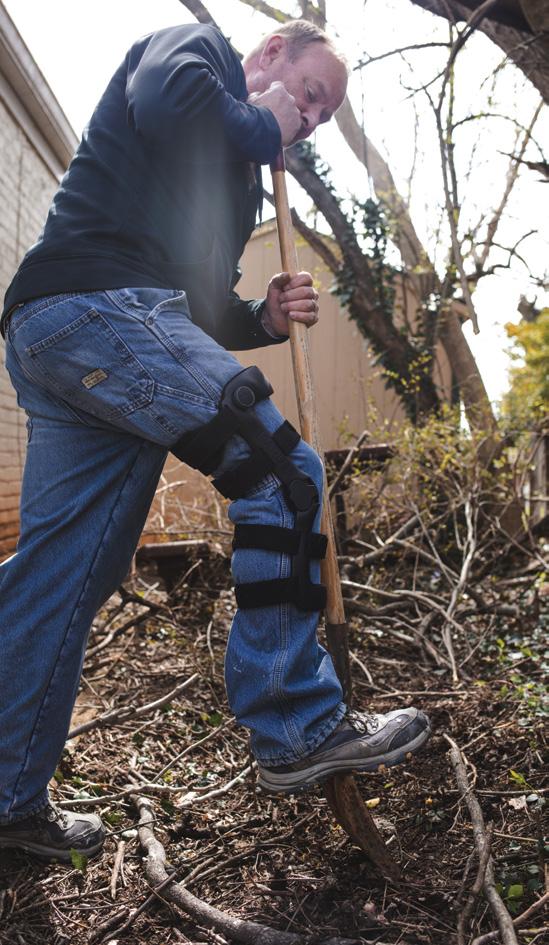
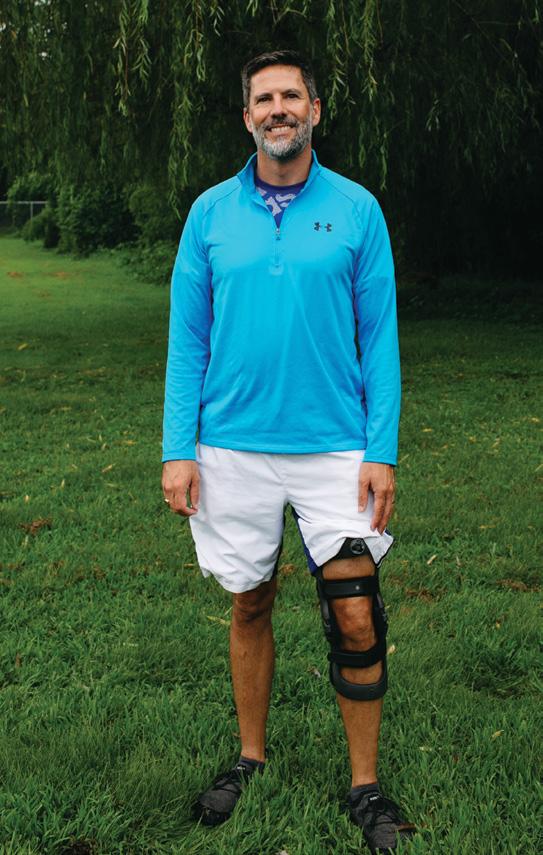
Patients leverage braces from Icarus Medical Innovations to unload weight from the knee and improve their ability participate in activities.
Knee Assist
Virginia company leverages 3D printing to design braces
Dave Johnson’s first invention, the Ascender Brace, was born of desperation. Johnson had blown out his knee playing football as a high school student. The damage was significant and later contributed to a patellofemoral cartilage defect that turned into knee osteoarthritis. Normally this would be cause for a knee replacement, but Johnson was in his 20s at that point, so a replacement might need to be redone after seven to 10 years, particularly given his higher level of activity.
Johnson, who eventually became an engineer, decided to explore creating a brace that would help the knee spring back up after bending down.
“I wanted to stay active, especially because your body weight is multiplied in the joint and causes more pain, so I needed a device to assist the knee and unload weight,” he says. “I bought some knee braces, cut out the hinge, and 3D printed my own hinge. I designed torsion springs out of heavy piano wire to make them the right size with enough power and range of motion.” Johnson tested his brace and found he could snowboard without pain.
“I realized I was on to something, but I had to make it lighter and allow the user to adjust the tension level,” he recalls. Using his free time, Johnson spent the next five years turning his idea into a viable product, and in 2019 he launched Icarus Medical Innovations. “At first, this was just to solve my problem, but other people saw it and wanted one.”
Icarus is based in Charlottesville, Virginia, and Johnson’s first intern was a University of Virginia student, whom he hired in 2020. Later that year, Icarus launched the Ascender Brace as its first product. Today, the company has 40 employees, many from the university. Starting a business just before the COVID-19 pandemic was challenging, but Johnson benefited by securing an office and manufacturing space right on the busy Downtown Mall.
The Ascender Brace unloads up to 40 pounds from the knee. Icarus developed a smartphone app that captures a 3D scan of the leg, so the brace is 3D printed to exactly conform to the patient. The device is extremely lightweight, and the user can adjust the tension to improve stability and support a variety of activities, according to Johnson.
Icarus also developed a knee-ankle-foot-orthosis (KAFO) that enables users to gain stance control by adjusting the tension level of the device. “The KAFO is only 26 ounces and conforms perfectly to the leg,” he notes.
Icarus’s products are available to orthopedic physicians and orthotists, as well as directly to the public. Many physicians and orthotists carry the devices, using the app to send precise measurements to the company.
As 3D printing and scanning technologies evolve, Johnson believes costs will come down and products will be increasingly tailored to each user. “As orthopedic bracing improves, insurance companies will recognize that savings can be had by delaying surgery,” he predicts.
Icarus gives back to its community in several ways. The company holds a ball each year to raise money for veterans’ groups, and it supports the clean-water initiative of the Chris Long Foundation, a nonprofit founded by two professional athletes who met at the University of Virginia.
In addition, Icarus has an “every patient” policy, where it tries to get every patient braced, regardless of their financial situation.
It would have surprised the high school Dave Johnson to see how his sports injury engendered a career and a mission. “We have a cool culture at Icarus,” he says. “We like to try new things. If you have an idea, you can have it in your hands in 12 hours. Everyone is so excited and motivated to invent useful stuff [and] to solve problems that have been ignored for a long time. It’s a blast!”
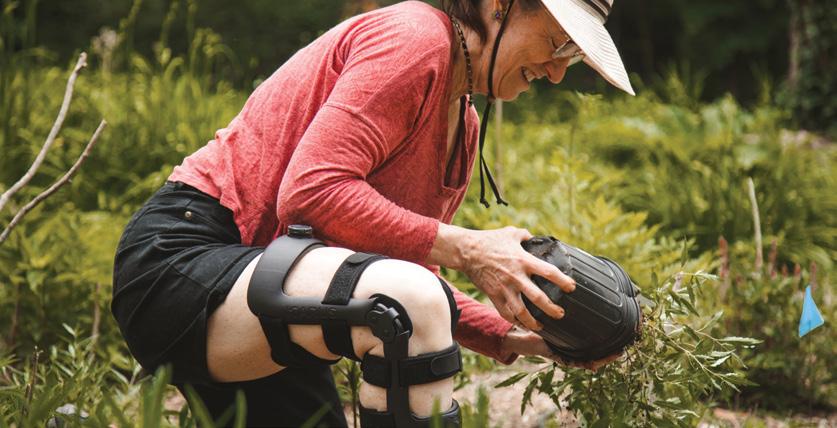
Deborah Conn is a contributing writer to O&P Almanac. Reach her at deborahconn@verizon.net.
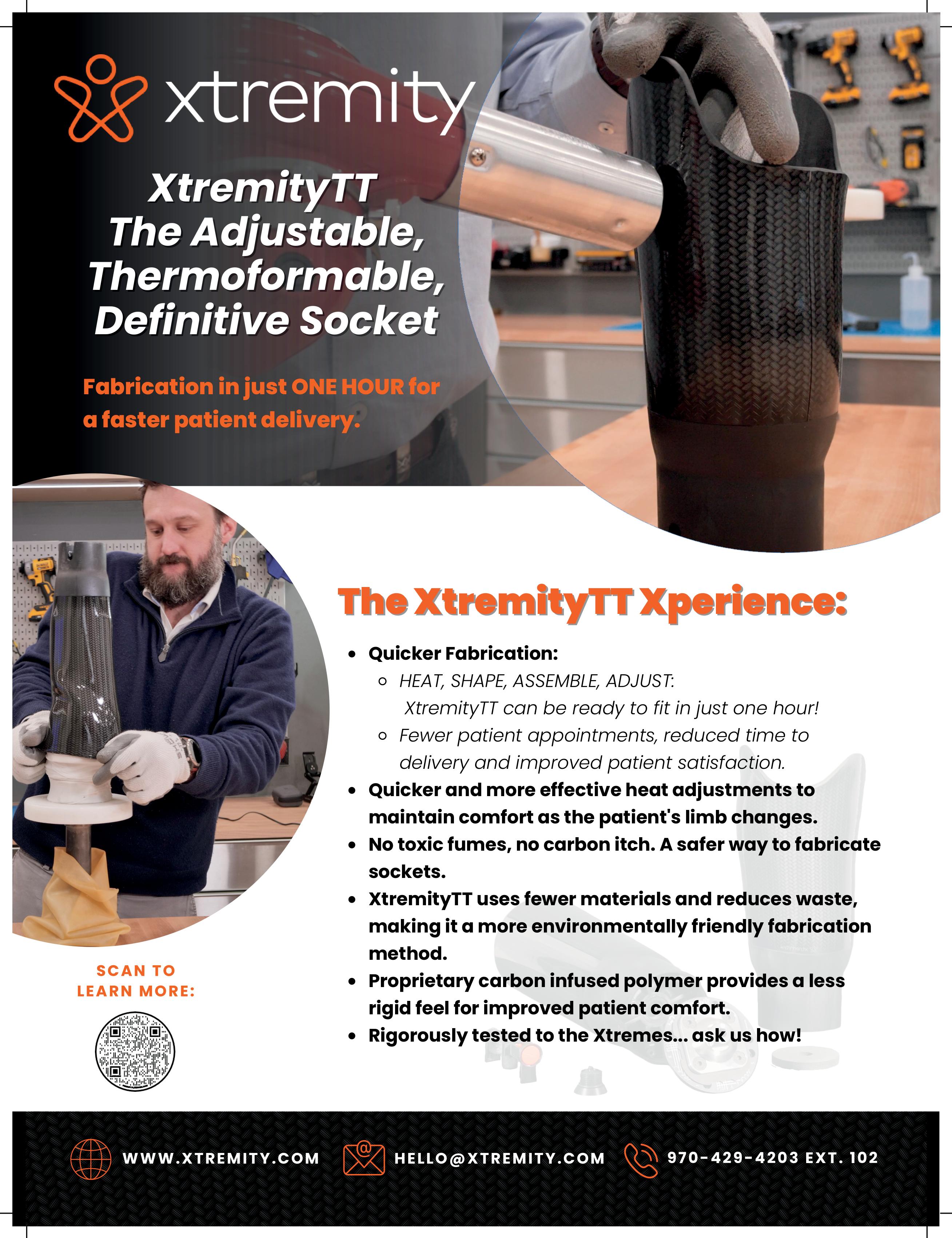