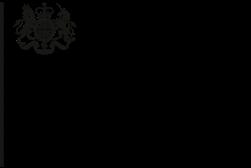
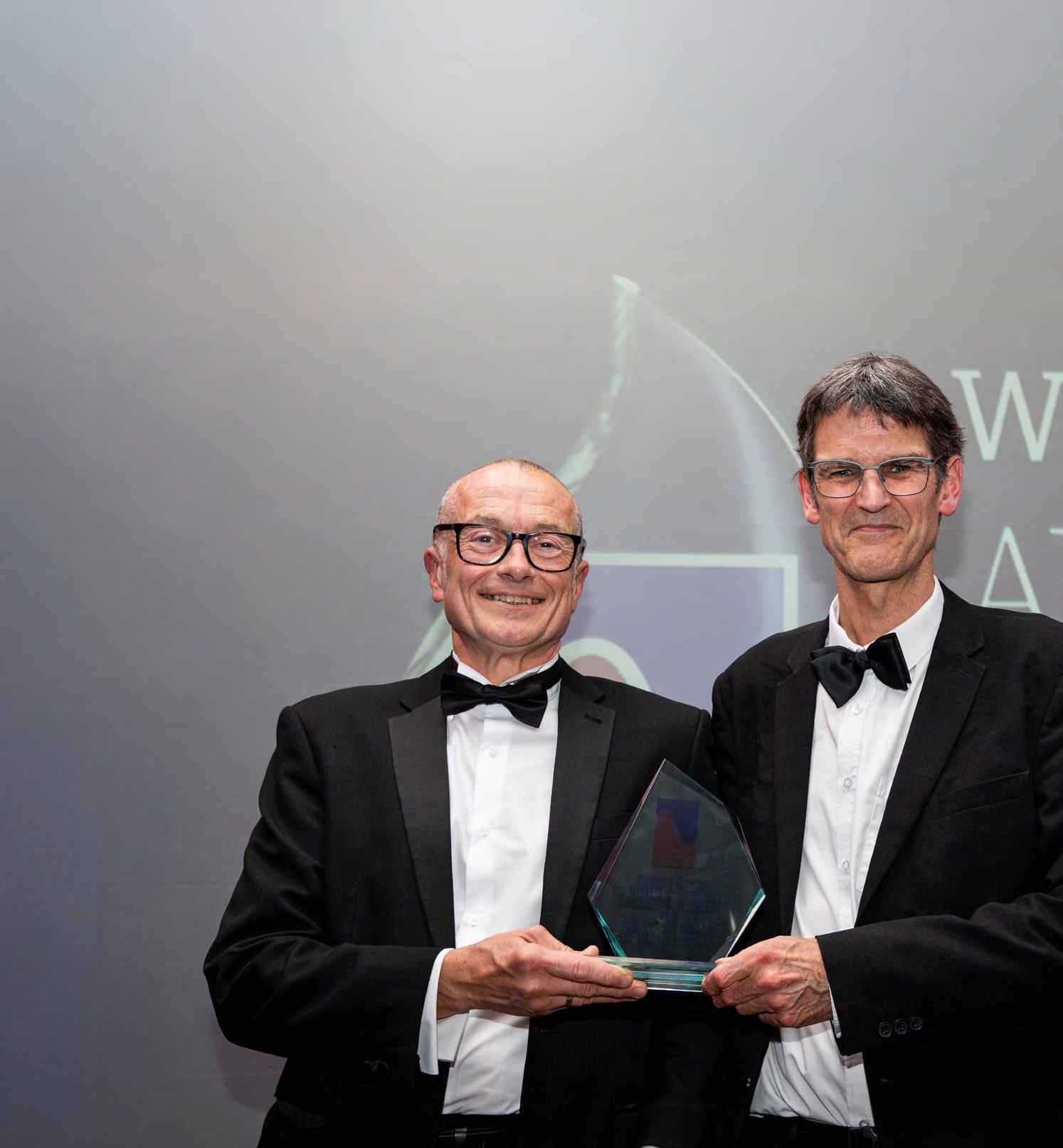
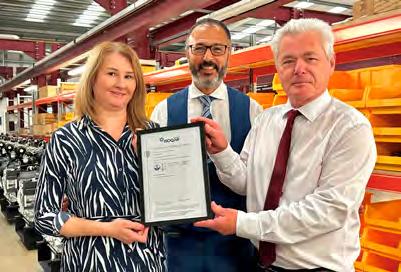
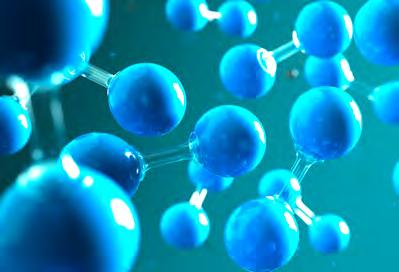
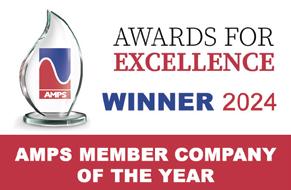

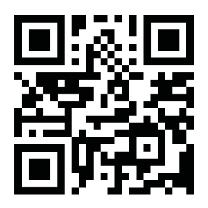

AMPS Power celebrates another year of promoting innovation and excellence in our industry.
It has been a great privilege to edit AMPS Power over the last year – not least to learn about the terrific products and projects that AMPS members have delivered. I still get the feeling that some of our members don’t shout loud enough about their achievements, so my mission for 2025 is to help turn the spotlight on them in these pages.
Where AMPS has really taken a big step forward is in sharpening its profile to be recognised as an expert partner of government departments. Hats off to David Oates, Joanna Oliver and the technical team in achieving this success. Much more to be done but the groundwork has been laid with the current government.
If you are an AMPS Member, don’t forget to let me know what you are doing!
Rob Oliver
MBE
Editor – AMPS Power Magazine
Unit 19, Omega Business Village, Thurston Road, Northallerton, DL6 2NJ, UK
Director General: David Oates – david.oates@amps.org.uk
AMPS Chair: Louise Hazel - amps@amps.org.uk
AMPS enquiries: amps@amps.org.uk
AMPS Power (editorial & advertising): ampsmagazine@amps.org.uk
Director General of AMPS
I would like to take this opportunity to thank all Members who have supported AMPS Power magazine with articles, advertisements and news items throughout 2024. Without you the magazine would not be the success that it is.
We are fortunate to be in an industry that has shown remarkable growth across many of our segments and to capture and share some of these stories in the pages of AMPS Power has been a great pleasure. I understand that in some areas we need to make further progress. The adoption of Stage V has still to fully impact on the market to the anticipated level due to inconsistent local authority enforcement and exceptions in many parts of the UK. The overall drive however is, without doubt, that towards Net Zero and the day when “zero diesel” will be the norm on UK construction sites.
With a relatively new Government tenure and the settling down of its manifesto and policies, we expect as an industry that official policies will reflect the need to fulfill the promises
embedded in the Paris Accord. We as an Industry are part of that journey and will ensure that AMPS Power remains part of the debate and development of policies which will shape the future of our businesses.
It was wonderful to see the industry come together at the 2024 AMPS Awards for Excellence, in London. We were able to celebrate another year in the “genset world” - and we are indebted to our sponsors and excellent awards entrants who made it a remarkable evening. My congratulations go to those that came through on the evening as worthy winners of their respective categories. The competition was as fierce as ever, making the Judges’ decisions evermore challenging. And so, we look forward to 2025 – with all its challenges, opportunities and unpredictabilities. My good wishes to you for a successful year, in the knowledge that AMPS will be working on behalf of our industry and your business.
Alan Beech, who led AMPS input to DESNZ policy
AMPS was selected from over 200 organisations to be one of the expert industry advisers chosen to present our strategy to the newly formed UK Energy Security and Net Zero Committee, chaired by Bill Esterson MP. The Committee provides key inputs into the policies of the Department for Energy Security and Net Zero (DESNZ)…
The Committee: comprised of Members of Parliament and the House of Lords, is tasked with guiding government strategy on decarbonising the UK economy. Participating organisations included a mix of government bodies (e.g., Ofgem, NESO), trade bodies (Citizens Advice, BSI, BEAMA, Make UK), major energy providers (e.g., Centrica, Octopus Energy), and global manufacturers (e.g. Siemens, Hitachi). AMPS was the only trade association representing the UK’s Powergen Sector at the Committee.
The Engagement Process: the session involved rotating presentations where representatives from each organization were given time to present their priorities, followed by a Q&A with the Committee Parliamentary members. This format allowed each table of six organisations to engage with MPs on diverse issues.
AMPS Objectives: AMPS aimed to establish itself as the prominent industry voice to the DESNZ Committee. The AMPS proposal focused on expanding recognition of Greenhouse Gas Protocol (GHGP) Scope 4 reporting to highlight the benefits of low-emission engines (e.g. Stage V), hybrid technology, and renewable fuels like HVO and biomethane. The goal was to support a lower-carbon, resilient future. Participation itself strengthens AMPS’ standing as a trusted adviser within government circles, reflecting its role as the Voice of the Power Generating Industry.
Thanks to Alan Beech, Sales Director of Clarke Energy and AMPS Council member, who represented the Association at this important event.
Prime Minister Starmer has revised down the government’s policy for the 100% decarbonisation of the National Grid by 2030, to a 95% target.
The Prime Minister made a renewed commitment to fast-track infrastructure schemes - by tripling the number of approvals for major developments compared to the last Conservative parliament by streamlining the approval process. Starmer described the current planning system as a “blockage in our economy that is so big it obscures an entire future”, adding that it was preventing the construction of projects including roads, grid connections, laboratories, rail lines, power stations and wind farms. However, he also scaled back plans to decarbonise the UK electricity grid by 2030, admitting the government was now aiming for 95% clean energy by the end of the decade.
The Centre for Policy Studies was amongst a number of voices calling the original target unattainable in their Great Grid Gamble report. They wrote that, “Ed Miliband hailed a recent report from the National Energy System Operator (NESO) as vindicating his plan to decarbonise the grid by 2030. But new analysis shows that the NESO report is built around a series of assumptions designed to cast Miliband’s plans in the best possible light, rather than reflecting the reality of the energy markets. For example, it envisages building twice as much transmission network capacity in the next five years as was built in total over the last decade, with zero delays.”
The former 100% target had also been criticised as “mad, bad and dangerous” by Shadow Energy Minister Claire Coutinho MP and has been described by the National Grid as “incredibly stretching” due to the amount of work required over the next five years.
Perkins hosted the 2024 AMPS Industry Day at their Peterborough facility – which attracted an attendance of over 100 members and guests.
Themed as Decarbonisation and Electrification of Power Generation, the day featured an impressive roster of expert speakers. Ed Hodson of Perkins’ Customer Solutions Team provided a briefing on his company’s perspectives. Tim Huntly, a Senior Advisor in the Environment Agency’s Energy Industries Decarbonisation Team spoke on the EA’s Methane Action Plan. His presentation was complemented by Andrew Gordon and Luis Bassett of Cleaner Machinery – the London-based initiative to ensure compliance of Non-Road Mobile Machinery (NRMM) with Low Emission Zone requirements. Luis was subsequently recruited as Decarbonisation and Sustainability Manager for the Construction Plant-hire Association.
Ian Jackson of the Society of Operations Engineers focused on those holding positions of engineering responsibility. He stressed the need to ensure registration with the Engineering Council as EngTech (Engineering Technician), IEng (Incorporated Engineer), or CEng (Chartered Engineer), or a recognised international equivalent.
Commenting on the event, Andrew Bell, the MD of Mecc Alte UK, said it was a fantastic event, “The venue was excellent, the speakers were outstanding, and the attendance and networking opportunities were top notch!”. Andrew Gordon concurred in saying, “A fabulous event, and an invaluable opportunity for our policy implementation team to hear from so many stakeholders in the field, developing our understanding of the decarbonisation options and challenges ahead”.
AMPS are particularly appreciative of Mike Rosser and his team at Perkins for their generosity and efficiency in ensuring the day was such a success.
Promoted as the official plant marking and registration scheme, the industry-owned CESAR ECV initiative has been identified as a further potential benefit of AMPS membership.
AMPS’ Director General, David Oates, has progressed talks with both the Construction Equipment Association, owners of the CESAR plant marking and registration scheme, and Datatag ID which delivers the scheme on their behalf. The objective is to establish how best AMPS can partner with them for the benefit of AMPS members. Registration of all on-site machines not only has anti-theft benefits but aligns with municipal and major project priorities to ensure their environmental standards are met. This is because CESAR ECV (Emissions Compliance Verification) registration captures key machine data, in addition to ownership and model information, which includes engine type. This provides ready identification for site managers and inspection teams requiring a minimum of Stage IV or Stage V engines to be installed in powered plant. For example, CESAR ECV is seen as a key tool in NRMM identification which can help the work of London’s Cleaner Machinery initiative which has been covered extensively in the pages of AMPS Power.
Superintendent Andrew Huddleston is the National Police Chiefs’ Council (NPCC) lead for the theft of Agricultural and Construction Machinery. In a separate development, he has been in touch with AMPS for help in combatting the spike in genset theft and to support machine marking and registration.
AMPS is anticipating another busy year, working on behalf of our members. Here are some of the highlights of planned events…
Members should make a diary note for Wednesday 30 April as the date of the 2025 AMPS AGM, CONFERENCE & LUNCH. Once again it will be hosted at One Great George Street, Westminster – the home of the Institution of Civil Engineers. A chance to meet with the fellow industry leaders and guests within convivial and historic surroundings.
Monday 2 June is confirmed for the AMPS ANNUAL GOLF DAY – at the prestige home of the Forest Pines Hotel, Spa & Golf Resort. The Lincolnshire venue offers not only a fine golf course, but excellent facilities for non-golfers who want to join the day.
AMPS will be part of a busy trade show programme in 2025 – see page 39 for the full listing of dates and venues. This will include stands at Data Centre World, Solar & Storage and PlantWorx. For the latter show, in September, the organisers have offered AMPS official partner status which includes special benefits for AMPS members.
The success of the 2024 INDUSTRY DAY means that a 2025 event will be organised with an autumn date set to be confirmed. The well-established annual AMPS AWARDS FOR EXCELLENCE GALA DINNER will be hosted in Manchester this year with a venue to be announced in due course.
WEDNESDAY, 30TH APRIL 2024 ONE GREAT GEORGE STREET, WESTMINSTER, SW1
The market for generators of less than 750 kVA increased very significantly in 2022 and early 2023. This was due to the robustness of construction and more especially the fear of an energy crisis linked to the Russian Conflict. It is now experiencing a decline and returning to a “normal” level, the trend amplified by the decline in construction in Europe and product inventories still a little high. The market should stabilize in 2025, but a return to strong growth is not expected.
On the other hand, the market for generators
>2000 kVA is still in hyper growth, driven by the data centers and artificial intelligence segment. This high growth (>15%) should continue, and data center projects are now being deployed throughout Europe. In particular, strong growth is expected in Southern Europe (Italy, Spain). The challenges to support this growth will be the increasingly significant energy needs of data centers, and the ability of engine manufacturers to supply sufficient quantities of engines. The trend towards HVO will also continue.
Electricity demand for data centres in Europe could more than double by 2030, according to Bloomberg Intelligence.
According to a report from Bloomberg Intelligence (BI), EDF, Rolls Royce and other companies racing to build next-generation nuclear reactors may miss the window to capture the potential surge in power use stoked by the rollout of AI. BI estimates that electricity demand for data centres in Europe could increase 2-3x by 2030.
Europe hosts 15-20% of global data-centre capacity, with proximity to customer hubs explaining their location. The UK, where these centres make up 3% of power demand, may remain a top market, with energy use from the sites seen rising 6x by 2035, according to National Grid. Data centre supply in the Frankfurt-London-Amsterdam-Paris-Dublin hub expanded by c.20% in 2024, while European data-centre power use could surge 3x over the 2023-30 period, according to Iberdrola, the multinational Spanish energy company (owners of ScottishPower).
HEADLINE SPONSOR
Our special report on the 2024 Awards Winners – representing excellence in our industry. The Awards evening was held at the De Vere Grand Connaught Rooms, London, and hosted by TV and radio personality Kate Thornton.
Crestchic Loadbanks proved to be a true ambassador for AMPS’ aims and value – exemplifying excellence in growth, innovation and environmental responsibility. The latter is central to their operations, as evidenced by their new refurbishment centre designed to extend product life cycles and their investment in renewable energy. As a founding AMPS member, Crestchic continues to lead by example, guiding and supporting fellow companies to drive industry collaboration and progress. Read Crestchic’s story of success on page 18.
Highly commended in this category were Genny Hire.
WB Power Services’ forward-looking programme is designed to offer a clear and structured pathway for individuals to launch successful careers in the power industry. Their investment in a state-of-the-art training facility at their Heanor headquarters—one of only two in Europe— demonstrates their commitment to hands-on, quality education. Their programme covers everything from Maintenance Operations Engineering Technician (MOET) qualifications to more advanced levels. They use the latest technology to ensure apprentices are well-prepared for the industry’s demands. Success stories abound, with former apprentices moving into leadership roles, underscoring the programme’s effectiveness. Read more about WBPS on page 20.
Highly commended in this category were Crestchic Loadbanks and Dale Power
In a category filled with exceptional growth successes, Wernick Group’s strategic approach to growth set them apart from the rest. Their proactive and forward-thinking business strategy has driven impressive results which speak for themselves. Wernick Power Solutions has significantly expanded its operations, growing to 63 staff across six hubs. Their revenue soared from £16 million in 2023 to a projected £20 million in 2024. Their substantial investment of £10.8 million in cutting-edge technologies, including PP200 Flybrids, battery storage units, and Stage V generators, highlights their commitment to futureproofing their business. Additionally, a £2.1 million investment in sustainable power solutions (such as SolarFrames and smart systems) emphasises their dedication to environmental responsibility.
Atlas Copco Power Technique UK & Ireland showcased an inspiring commitment to sustainability, impressing the judges with its holistic approach, which spans facilities to innovative energy solutions. Their Technology House in Hemel Hempstead is a shining example of sustainable design. The renovated facility features solar panels, rainwater harvesting and refurbished furnishings. It demonstrates a comprehensive effort to minimise environmental impact. The collaborative, open-plan layout encourages cross-brand collaboration while reducing the carbon footprint.
Beyond their facility, Atlas Copco’s ZSC 100-400 Portable Solar Containers offer renewable energy solutions for off-grid sites. These plug-and-play units are quick to deploy and drastically reduce emissions, providing a clean and efficient power source. By combining energy-efficient facilities with innovative technology, Atlas Copco sets environmental responsibility benchmarks.
Marco Monsurrò (President, Europgen), David Oates and Romain Mocaër (Secretary General, Europgen)
Generator Power Ltd stood out with their groundbreaking solution for powering remote telecom sites in an environmentally friendly way.
Their Solar PV System, integrated with Battery Energy Storage (BESS), offers a sustainable and efficient energy source for telecom sites. The system combines 12kWp solar panels with a 15kVA Atlas Copco BESS providing zero carbon emissions, no noise pollution and minimal maintenance requirements. The setup also features a 40kVA HVO-fuelled generator as a backup, dramatically reducing the reliance on fossil fuels. On average, the system saves 7,500 kg of carbon per site monthly and cuts operational costs through fewer maintenance visits. This product exemplifies how renewable energy can be leveraged to meet the power needs of remote infrastructure while significantly reducing environmental impact.
Power Control & Automation Solutions Ltd impressed the judges with a game-changing Hybrid Control Solution designed to manage complex energy needs while seamlessly integrating renewable sources.
The system, deployed at the Saudi Arabia F1 Jeddah Marina, efficiently manages power conversion between 50-60 hertz and operates at 230V. It integrates energy sources like solar PV and wind, using real-time data and machine learning to optimise energy flow and reduce energy losses. Highefficiency power electronics further minimise cooling requirements, even in extreme heat conditions. Built using recyclable materials, the solution is aligned with Saudi Arabia’s Vision 2030 initiative, promoting renewable energy use and environmental sustainability. Judges commended the family-run business for its technical expertise and its impact on renewable energy integration.
Highly commended in this category were Preheat Engineering Ltd
One project stood out from the others due to its complexity and uniquely different hybrid approach. Clarke Energy’s greenhouse project in Streatham is revolutionising the food and agriculture sectors by demonstrating how sustainable practices can significantly impact the UK’s food supply chain.
This greenhouse facility is designed to produce 10% of Britain’s cucumbers, reducing reliance on imports, currently at 85%. It features the UK’s largest water source heat pump system, delivering 33 megawatts of power from on-site reservoirs, cutting carbon emissions considerably. Rainwater is collected and reused for irrigation, and energy-efficient LED lighting extends the growing season. The CHP units provide electricity, with waste heat reused for additional heating, and CO₂ is captured to boost plant growth. The project is a model of sustainable innovation, creating 160-200 full-time jobs and providing economic benefits to the local community.
The project was a collaboration between Clarke Energy and AGR. Clarke Energy supplied and installed the energy centre, while AGR managed the project as the main EPC contractor, ensuring a holistic approach to sustainability.
right:
David Oates: Chairman of the Awards for Excellence Judging Panel and Director General of AMPS – with 27 years’ experience in the engine and power generation industry.
Louise Carney: a widely experienced communications and trade media expert. She has organised and advised on numerous awards projects.
Bernard Gospel: after a career working in the power generation sector, he is now Technical Secretary of AMPS and Chair of the influential EUROPGEN Technical Committee.
Rob Oliver MBE: former Chief Executive of the Construction Equipment Association – and current editor of AMPS Power.
Dr Susan Scurlock MBE: Chief Executive of Primary Engineer. Susan founded Primary Engineer with the belief that we can enable all children to reach their potential through engagement with engineering.
sales@wbpsltd co uk 0115 9444 422 wbpsltd.co.uk
Michael Smeeth: has over 25 years of executive leadership experience and a track record of success in advancing innovation, operational excellence and sustainable growth. Appointed CEO of BAR-UK, the aviation trade body, in 2024.
Richard Payne of Cummins was presented with a surprise AMPS Award for his, “tireless dedication to advancing standards and regulations for the UK Genset industry”
AMPS Technical Committee Chair, Chris Marsland, surprised Cummins’ Richard Payne on the Awards Evening with a special Award recognising his outstanding work for AMPS over many years. Chris explained, “Richard recently announced his plans to retire which sent shockwaves through the Technical Committee and we are genuinely concerned that he may be irreplaceable! He has been pivotal in ensuring that the interests of the genset industry have been properly represented in the UK and in Europe over innumerable years.”
In his company position of Off Highway Regulatory Affairs Director, Richard established himself as a highly respected, practical and dedicated technical expert within numerous UK and international forums. All at AMPS record our thanks to him for his exceptional contribution to the work of the Association.
Learn more: https://www.volvopenta.com/en-gb/
At the 2024 AMPS Awards for Excellence, Crestchic Loadbanks, a global leader in load testing solutions, was named the Member Company of the Year. As long-time supporters of AMPS, the Crestchic team was proud to receive the award, which highlights the company’s commitment to innovation, sustainability, and strategic growth. Chris Caldwell, MD of Crestchic, reflects on the company’s journey and the strategic choices that have driven its success.
A legacy of innovation: with over 40 years in the business, Crestchic has long been synonymous with quality and innovation in loadbank technology. However, recent years have marked an unprecedented era of growth. This momentum is not by chance, but the result of well-calibrated strategies aimed at meeting the evolving demands of the power generation, data centre, and marine sectors.
“We have always prided ourselves on anticipating industry needs and responding with products and services that exceed expectations” explains Chris. “The last few
years have been a testament to how strategic planning, investment in talent, and embracing innovation can accelerate growth.”
Doubling output and manufacturing capacity: one of Crestchic’s most transformative milestones came in 2022, with a strategic investment in a new UKbased factory. Initially projected to increase output by 60%, the company surpassed expectations by doubling its production capacity.
“The new factory undoubtedly gave us more production and inventory storage space, but the additional growth was made possible
by optimising manufacturing processes and making substantial investments in our workforce” Chris explains. By mid-2024, the manufacturing side of the business had already surpassed the full-year revenue of 2021.
The increased capacity has not only supported sales growth but also bolstered investments in the company’s rental fleets. Crestchic’s manufacturing footprint now serves as the foundation for scaling operations further, enabling it to meet the soaring demand for its loadbank solutions globally.
Expansion of the rental business: since 2020, Crestchic has invested over £21 million in expanding its rental fleets, allowing the company to execute key projects across the UK, Oman, Iraq, China, Israel, and the Falkland Islands. As a result, the rental business has doubled in size and is now the company’s largest revenue stream.
“The rental market has proven to be a resilient and lucrative avenue for growth” says Caldwell. “It’s always been critical to the business. The fact that, as an OEM, we offer the full package of design, build, sales, rental and service means we have a comprehensive and unique range of products. By reinvesting in our fleets and focusing on strategic geographies, we’ve established ourselves as a trusted partner for critical projects worldwide.”
Tailored solutions for a dynamic market: Crestchic’s commitment to innovation has also driven its success. Recognising the unique demands of the data centre sector, the company introduced a sector-specific loadbank in 2024.
Crestchic’s success in bringing the solution to market lies in its adoption of advanced manufacturing techniques and a customer-centric approach. By analysing market needs, the team designed a product that addressed pain points, resulting in a modular, stackable solution capable of controlling up to 20 machines via one controller. The engineering team revolutionised the company’s traditional design and production process, using AI, 3D modeling, and Design for Manufacturing principles to create smarter, more efficient designs and streamline production through concurrent sub-assemblies and modular design and build.
Significant investments in bespoke tooling, precision jigs, and an enhanced quality control process further ensured speed of manufacturing, while keeping quality at the forefront. Each production step is now checked for quality in real-time, enabling issues to be resolved early and reducing
reworks. These innovations, combined with focus on process efficiency and supplier collaboration, have dramatically reduced time to market while maintaining the highest standards of quality, meeting growing customer demand with precision and speed.
Investing in people and talent: a cornerstone of Crestchic’s strategy has been its investment in people. Since 2020, the company has effectively doubled the size of its teams across production, engineering, sales and after-sales functions. Enhanced benefits packages, improved health and safety measures, and robust training programmes have ensured that Crestchic attracts and retains top talent. The company has also reinvigorated its apprenticeship and mentoring programmes, offering young professionals a tailored and supportive pathway into the industry.
“Our apprenticeship initiatives not only cultivate skilled workers but also address the skills gap that challenges our industry” Chris notes. “We’re building a pipeline of future leaders who will drive Crestchic and the wider sector forward.”
Sustainability at the core: as Crestchic scales its operations, environmental responsibility is an important consideration. The company has made significant strides in waste reduction and sustainability, from installing solar panels and EV chargers to implementing smart lighting and heating systems at its Burton-on-Trent facilities.
One of the most impactful initiatives has been the establishment of a refurbishment and overhaul centre in Burton. Here, containerised loadbanks undergo extensive restoration, extending their lifecycle by an average of 10 years. This approach not only reduces waste but also aligns with the company’s commitment to circular economy principles.
“The last thing we want to see as a business is containerised loadbanks on the scrapheap. Our equipment is built to last, and we often see loadbanks that are decades old operating just as they did on
the day they were built. However, just as with any piece of industrial equipment, maintenance is important” Chris explains. “The new overhaul centre is home to a team of qualified and experienced engineers who undertake audits, replace and upgrade parts, undertake cleaning and repairs on the container, and bring the equipment to an “as new” state, using state of the art components.”
Digital transformation, for datadriven decisions: to further optimise its operations, Crestchic has invested heavily in enhancing its enterprise resource planning (ERP) system. This has provided the company with real-time management information, enabling data-driven decisions that support sustainable growth. The advanced system helps Crestchic streamline processes, monitor performance, and adapt to challenges with agility.
Industry leadership and collaboration: Crestchic’s influence extends beyond its own operations. As a founding member of AMPS, the company actively contributes to the power systems community by sharing expertise and fostering collaboration.
“We believe in the power of collective growth” Caldwell says. “By working together, AMPS members can strengthen the industry and create a more resilient future for all.”
Looking ahead: as Crestchic continues to scale, the company’s focus remains on innovation and strategic investment. From expanding its manufacturing and rental capabilities to developing cutting-edge products and nurturing talent, Crestchic is well-positioned to lead the industry into the future.
“Being named AMPS Member Company of the Year is a reflection of our team’s hard work, our strategic vision, and our commitment to excellence” Chris concludes. “It’s not just an achievement for Crestchic but a validation of our approach to creating value for our customers, our industry, and the sectors we serve.”
Last autumn, WBPS opened their brand-new Training Academy at their Head Offices in Heanor, Derbyshire. The Academy helped them win AMPS’ 2024 Apprentice Programme of the Year Award.
In its first week, the Academy welcomed 18 new engineering apprentices into its new home. They were able to make full use of the first-class facilities and training modules - offering glowing reports and positive feedback. The Academy is one of only two of its kind in Europe and provides an excellent platform for bright individuals to grow their knowledge and expertise within the power industry.
As the new apprentices kickstarted their journey, the Academy also featured its maiden training session, welcoming engineers and representatives from WBPS, Kohler EMEA and DE Power Solutions.
Hosted by Kohler’s Xavier Perseq, their Regional Training Director, the training session covered APM802 and AMP403 architecture and basics, with advanced synchronisation, and proved a major success for all involved. Offering certified Kohler
training and covering the whole of the East Midlands region, WBPS’s newest learning centre brings power-related training and industry know-how to budding engineers starting out in the industry.
A centre of innovation and excellence, the Academy also houses stateof-the-art equipment including, 2 Motorgens, APM403 Stations, APM802 Stations, DES Automatic Transfer Switch and a R110C5 Stage V Kohler generator. These are available to be used for fundamental mechanical generator training courses.
Andy Wilmott, Managing Director of WBPS and Wiltech Acoustics Ltd and CEO of the Wilmott Group says: “We are thrilled to have opened our doors to WBPS’s newest Training Academy at Heanor and warmly welcome our 18 new trainee engineers to the fold. We are hugely excited for our new facility
and believe we can offer a great platform for the very future of our industry, helping those passionate about learning to really kick-start their careers and grow their skills.”
“Our Training Academy offers so much for our students. As well as first-class facilities and certified training modules, our course leaders too are some of the finest in the industry, offering our trainees the very best in leadership and skill sets. From the inner workings of a generator to the maintenance and service of a power system, we have a range of subjects available to study. As the power industry and its power systems continually evolve, it is crucial that we keep our workforce up to date with advances in technology.”
“As well as enhancing technical know-how and expertise, the courses are also designed to refresh knowledge too. We believe our new courses will enhance day-to-day operations by keeping our workforce empowered with the latest developments within the industry.”
Providers of critical power for over 40 years, WBPS’s Training Academy ensures all those who have successfully joined are armed with the best industry-related know-how.
WB Power Services are experts in the reliable delivery of critical power projects, generator maintenance and hire solutions nationwide. As a leading family-owned operator of critical power infrastructure, they have led projects of all sizes, across all sectors.
To discover more about WBPS and the courses on offer at the WBPS Training Academy, visit the website at www.wbpsltd.co.uk
OUR ENGINE OVERHAUL PROCESS OFFERS A COMPREHENSIVE ASSESSMENT OF EVERY SINGLE COMPONENT THAT MAKES UP YOUR ENGINE. OUR RE-BUILD PROCESS
We visit your site to assess the issue at a time that suits you.
We visit your site to assess the issue at a time that suits you.
We visit your site to assess the issue at a time that suits you.
All fluids are drained, and components are disassembled.
All fluids are drained, and components are disassembled.
All fluids are drained, and components are disassembled.
All parts are thoroughly cleaned using ultrasonic and wash tanks to prepare them for inspection.
All parts are thoroughly cleaned using ultrasonic and wash tanks to prepare them for inspection.
All parts are thoroughly cleaned using ultrasonic and wash tanks to prepare them for inspection.
We inspect components to decide if they need replacing or restoring.
We inspect components to decide if they need replacing or restoring.
We inspect components to decide if they need replacing or restoring.
You receive progress updates, including costs and timelines.
You receive progress updates, including costs and timelines.
You receive progress updates, including
We replace approved parts with OEM components.
We replace approved parts with OEM components.
Some parts can be refurbished to OEM standards. The engine is reassembled and refueled.
Some parts can be refurbished to OEM standards. The engine is reassembled and refueled.
The
The engine is tested and prepared for re-installation.
The engine is tested and prepared for re-installation.
sales@wbpsltd.co.uk 0115 9444 422
sales@wbpsltd.co.uk 0115 9444 422 wbpsltd.co.uk
9444 422
OUR ENGINE OVERHAUL PROCESS OFFERS A COMPREHENSIVE ASSESSMENT OF EVERY SINGLE COMPONENT THAT MAKES UP YOUR ENGINE.
OUR ENGINE OVERHAUL PROCESS OFFERS A COMPREHENSIVE ASSESSMENT OF EVERY SINGLE COMPONENT THAT MAKES UP YOUR ENGINE.
Allam Marine, the UK’s leading manufacturer of both Tempest (ready-to-run) diesel generating sets and distributor of CKD (loose engines and alternators) to the genset industry has changed its name to Allam Power, as it embarks on a new chapter for the business.
The OEM distributor, based in Melton (East Yorkshire), has undergone an extensive period of business change. It has used the opportunity of a period of relatively slow growth in the international genset market to make crucial preparations for the market upturn.
Stocking over 8,000 engines and alternators, from brands such as Perkins, Cummins, Volvo, Leroy-Somer and Mecc-Alte, the company is investing in future technologies, as well as improving processes for supporting customers across the world with their current power generation challenges. Whilst the core parts of the business remain fundamentally unchanged, the rebrand represents a commitment to future-proofing Allam Power’s business, as well as its customers’ businesses, as Managing Director Ehab Allam explains:
“We have always believed that investing in the business is the best way to deal with the challenges of an unpredictable market, and our strategy of carrying the right stock of engines and alternators continues to be at the centre of our strategy.
We’re in a strong position to supply global demand. We’ve recently bolstered our purchasing team and, by following market trends carefully and using our buying power, we can continue to offer our customers competitive pricing on gensets, CKD and genuine spare parts, as well as significant savings on transport and import duty.”
Allam Power has embarked on a recruitment drive over the past 18 months, restructuring the business ready for a very different looking global power generation industry. Mr Allam continues:
“Changing the company name to Allam Power, with a subtle brand refresh, reflects our refocusing of the business strategy –we’re a one-stop-shop for the world’s power generation industry. We have built a team with the powerful combination of industry experience and versatility, meaning we can adapt as the industry changes at pace. For example, we’re developing a hybrid solution for smaller gensets, as well as increasing capacity for data centre builds.”
Allam Power is also renowned for its Tempest brand, designing and building quality gensets from 5kva to 3000kva since 1935. Tempest Sales Manager, Paul Thorpe, has been overseeing an ambitious programme of research and development for his brand, but is keen to emphasise that it’s not all about future projects:
“On the manufacturing side of our business, Tempest has always worked closely with our valued technology partners to understand the advances in technology, using this knowledge to directly benefit our customers.
Being one of the first OEMs to develop a product using the new Perkins’ 5000 series engine has given us a good view of how the genset supply and maintenance model is evolving. We’ve also got a team of design engineers dedicated to research and development, including the adoption of hybrid technology.
But our biggest strength has always been to use our extensive experience to provide the most efficient and well-designed solutions to suit our customers’ current needs, and we’re continuing to offer the same quality and reliability which our customers know comes with gensets made
in England, with only genuine components. That being said, we’re always looking for ways to improve our product designs, and I’m excited to reveal that we’ve been working on a new range of in-house designed canopies which are now at the prototype stage.”
Quality is important to a business with the size and reputation of Allam Power, which is why one particular focus over the past 12 months has been to achieve the ISO 9001 quality standard, as Head of Finance, Helen Lewis explains:
“Our customers – and the wider industry –have always recognised us for the quality of our genset manufacture, but also our efficient business systems. It has been very selfassuring to be able to acknowledge our quality standards by achieving the ISO 9001 standard in such a short period of time.
This formal recognition allows us to continue to support our customers in winning tenders and contracts where the ISO 9001 standard is required. But beyond that, this achievement reflects our commitment to continual improvement across both the CKD and Tempest parts of the business.”
As a market leader, Allam Power is investing in the people, skills, technology and processes to ensure it continues to offer the very latest products and solutions, with innovative added value, at the most competitive prices.
Look out for an exciting year and further announcements from Allam Power in 2025!
The introduction of electrolysed hydrogen and oxygen to the intakes of a somewhat conventional compression engine, is one of broadly three ways in which hydrogen can help, the others being full H2 combustion and fuel cell technology. In this issue I would like to pick up on some of the policy drivers for hydrogen in off-grid applications.
Andrew Gordon Project Manager [Pan-London NRMM] Cleaner Machinery
This is the 4th in a series of articles contributed to AMPS Power by Andrew Gordon – who was a guest speaker at AMPS 2024 Industry Day, hosted by AMPS members, Perkins.
Whenever the topic of hydrogen crops-up in discussions with generator stakeholders, there are typically some splutters of objection and a quick request for a ‘reality-check’. And it’s completely reasonable. Where grid supply can deliver a kWh at £0.34, or diesel at £0.60, whatever is the point in looking at an option at £8.80, a quote typical for hydrogen? Let’s add, this is for the fuelling alone, not factoring the astonishing hire costs for a boutique piece of exotica with a somewhat limited customer base. Perhaps then, an option for certain shortduration events with very special environmental requirements, but surely not on the table for an extended construction project.
Hydrogen is not a fuel in the same sense as oil and gas have been. As the host of COP29, Azerbaijan's President Ilham Aliyev famously stated, fossil reserves are in a sense, ‘a gift from God’. They have been a dense source of cheap energy that has facilitated global industrialisation. Hydrogen, conversely, is not a source of energy, only a useful energy carrier, and one of green sustainable energy most especially.
Plots on graphs from any number of sources,
show an exponential growth in solar and wind renewables. There are similar curves on announced H2 projects, although the true picture shows that only a small portion of these actually reach Final Investment Decision. Why then do we link the transition to renewables with hydrogen? Because in addition to being an excellent energy vector from point of production to point of use, hydrogen is also a vector across time, potentially buffering the fluctuations of supply and demand that occur across the seasons and over 24 hours, both pivotal factors in consideration of UK renewables. The potential H2 power ecosystem necessitates grid-scale energy storage capacity. There are a number of exciting geological options here, which the UK is fortunate to have in abundance, alongside the plentiful wind and solar resources. Such storage can embed UK energy security and resilience, as well as tackle Dunkelflaute, the protracted periods known as known as ‘anticyclonic gloom’, where neither wind nor sun shall cater to our collective national requirement.
But aren’t renewables prohibitively expensive? Or conversely, are they in fact a highly
attractive destination not only in the face of global climate emergency, but because they offer a potentially cheaper energy source than geo-carbon fuels ever have been?
Fear of a new energy infrastructure on such a scale is understandable, although H2 has actually had a fairly early role in industry and transport, it’s not so new as a fuel in itself. Hydrogen is an industrial gas and nothing more, in routine use in chemical engineering. Yet many other industries are risk-averse to what is seen as a novel use of it.
The first hydrogen fuel cell is described in 1838. In transport too, the de Rivaz carriage of 1804, the world’s first internal combustion powered vehicle, utilised as a fuel, hydrogen. It’s not too hard in fact, at least for the more fanciful amongst us, to envisage a possible alternative Industrial Revolution, one where carbon never figured in the combustion reaction at all, and where electrolysed water from renewables achieved the same global result.
Which leads us to the now. What has stalled exactly, and why does a technologically feasible route to decarbonisation on such a massive and unprecedented scale, remain a topic of science-fiction to so many? Are we in the midst of a climate emergency or are we not?
Stakeholders in the hydrogen community will of course point to the present absence of any offset incentivisation, to bring down the cost of hydrogen as a fuel, as against fossil and HVO counterparts. With grey hydrogen at around $1 a kilo, and green at $14 a kilo, cost factors can’t be discounted. However, subsidy alone shall not untie the Gordian Knot. Until there is support infrastructure to transport hydrogen, either in tanks or through new pipelines, it cannot cost-effectively reach the recipient. Storage nodes are not as far-flung as might be first thought, but they are not always local. Scope to re-task the present natural gas network exists, but not while it remains in active use for industrial and domestic purposes.
Skills are yet another limiter. Hydrogen internal combustion is reasonably amenable to the skill set of a conventional engine technician, but skills in support of fuel cells are in short demand. Similarly for the electrochemistry skills required in electrolyser maintenance and development. Electrolysers do have something of a persistent reputation around reliability.
Where there’s no shortage, is in the range of viable products. The UK has been at the forefront of H2 innovation for some time,
although it still lags somewhat in terms of numbers of ‘Hydrogen Valleys’ found in mainland Europe. These are publicly funded localities set up to provide synergies between the supply, use and storage, and seek to pick apart the interrelated factors causing inertia. There’s no great shortage of policy either, with countless UK papers and reports all pretty much aligned.
So, when are we going to be driving hydrogen cars? Not soon. You can buy one today if you want and use it up and down the country fairly easily, but this is not the first-choice destination for an expensive gas. It can be piped into homes as boiler and cooking fuel, as a dilutant in natural gas supply, and this has been trialled. It works unproblematically, but the trial nevertheless went badly. Public engagement was not handled well, setting well a lesson learnt for the future. But no, domestic supply is not where hydrogen shall be headed next. The commercial value of hydrogen, in common with most commodities, is dependent on location. Hydrogen electrolysed at the DC landfall of offshore wind, or electrolysed on decommissioned oil platforms, is quite another thing from hydrogen at the point of industrial requirement. And industry it is, destinations where the most energy intensive processes take place. These are the facilities most greatly contributing to GHG emissions, most keen to decarbonise, and yet most challenged in doing so. These shall be first to make use of green hydrogen on a scale. We’re talking the chemical plants, the glass and steel, the heavy industries. Decarbonising fertiliser production is an easy win. These users operate processes that cannot be paused, and hold infrastructural assets that are immensely valuable, so reassurance is needed before transition can be made, and this is why is has not happened already.
The next uptake sector? Construction, and likely also events. Diesel and HVO generator fleet operators should be keeping a keen ear to the ground. The variable-speed fleet, at least in the higher power bandings typical on most major construction projects, are not especially amenable to simple electrification. As covered in my last article, the smaller excavators, telehandlers and the like, can be charged from Stage V generators, and can derive overall emissions savings on summation, but it’s not ideal and it’s not good optics. Grid supplemented by BESS where required is another sensible option for electrified fleet charging. However, the bigger machines are
taking too long to charge and don’t last the working day, so at least as things stand, it doesn’t seem feasible to just go battery. Hydrogen provides a more viable option. Fuel Cells can work, but internal combustion seems more robust for moving plant in the site environment, and for reasons already mentioned, H2ICE engines are going to be easier to maintain. Products already exist, but they are not yet things we find in use during our site audits. At the last trade show we visited, there was a huge hybrid BESS / Fuel Cell offering in a shipping container format, and a H2ICE genset exhibited in a more typical acoustic enclosure. Once again, the products exist, just are not yet commonplace. There shall be a race between the Tier 1 contractors in London, to run the first hydrogen-only site, a terrific coup in preparation for the zero-emission deadline. And when the zeroemission variable-speed engines are deployed, constant-speed shall have to match.
Lastly, what about events? There are a lot of examples to choose from. Events being of short duration, are most amenable to showcasing best practice. The 2024 World Cup for Touch Rugby was no small event, running for 7 days and attracting 10,000 spectators. Grid supply was limited and typically would have used diesel generators to supplement and meet demand. This time it was successfully powered with hydrogen fuel cell solutions and it went well.
I’ve not managed in the end to minimise the numbers of question marks that arise whenever there are discussions around hydrogen in the off-grid context. What shall be the forthcoming Labour plans for GB Energy? They shall clearly need to be aligned with those of a large number of departments, including those covering education and the public awareness of hydrogen, which is currently very limited if not actually mis-informed. Investment into infrastructure can only then properly follow on. The Labour manifesto commits £500 million into green hydrogen production, a figure dwarfed by those in Europe. Despite UK exit, very considerable EU funding exists for UKbased SMEs seeking to develop H2 products.
We cannot divine the future, but we can see some of the likely inputs into the forthcoming UK Industrial Strategy. This strategy is set for release early in 2025, before time of writing, but possibly by the time you are reading this. Worth a look online.
Andrew Gordon - Project Manager (Pan-London NRMM), Cleaner Machinery
Preheat Engineering set out the compelling reasons why they were recognised as Highly Commended in the AMPS Awards for Innovation and Technology.
There’s a new kid in town, one that took the tried and tested principles of a bimetallic thermostat and built into the design, solidstate technology. Creating a version much more resistant to engine vibration. Voices within the industry have recognized, for some time, that traditional thermostats are not well-suited to engines. The constant vibrations of a running engine effectively shake and unsettle the contacts, rattling and juddering components free from their housings, leading to broken circuits and untimely failures. Fails in an industry where critical power is critical and can lead to disastrous consequences. It’s a long-time problem that’s been waiting to get fixed and these long-awaited devices are now a reality for Preheat Engineering who have developed and launched them on their engine coolant preheaters.
These new thermostats are electronic devices that do not contain any parts sensitive to vibration. They consist of electronic components sited on a motherboard and insulated with acoustic polymer; it makes them more durable when attached to engines of any form. It’s a contrast to mechanical thermostats which use two pieces of different metals bolted together to form what's called a bimetallic strip (or bimetal strip), these make-or-break contact based on surrounding temperature but are sensitive to vibration. This tends
to shorten their lifespan. And in the manufacturing industry, it’s all about the bottom line. So, developing new products with extended life that will not need to be replaced as it quickly reduces waste and cost for both the manufacturer and the customer.
HOW LONG IT TOOK AND THE
Back in June’23, Simon Gristwood, long time MD at Preheat Engineering Ltd, commenced the development of a new solid state thermostat, initially as a range of informal conversations with long-term customers and friends. He was frustrated by thermostat failures and replacement heaters he was providing free of charge to his customers. He recognized this was not only bad for his profitability and brand reputation, but it seriously jeopardised his customers’ loyalty and gave them additional inconvenience in swapping out heaters. That’s where his background in electronic engineering came in, he knew there was a better way and connected with Nixer UK Ltd to design and develop a digital control unit and temperature sensor which could withstand the vibration associated with a running engine and still provide accurate temperature readings. Nixer’s experience in building audio over IP diagnostic and monitoring systems and Simon’s electronic and mechanical engineering expertise provided an ideal blend to design and build the prototype.
That process in itself took some time and at times Simon told me, “there were moments that this project was like pushing treacle uphill”, but perseverance is always needed in product development. When the prototype was born back in February ’24, thanks to ANR Manufacturing Ltd, it also included a monitoring system that would provide data for diagnostics and forensics. Giving valuable feedback on temperature and operating environments to users and maintainers.
Once the initial prototypes were made, they were connected to the power supply at Preheat, placed in buckets of water and tested for weeks on end. There were a few design changes during this time and one or two components got swapped out to ensure operational continuity. They even needed to swap out one electronic component which came under import sanctions by the US government. Once the design became stable and a consistent temperature was maintained in the test facility, Simon and the team approached their customers to conduct field trials with the new heater units. The first triallists really helped with understanding and feedback for these new devices, which were tested over the following six weeks with no problems and with very positive feedback.
business problem and make change happen. Preheat are now in full production of their Peregrine preheaters with these thermostats included and currently have over 150 installed with various customers.
THE OUTCOME AND BENEFITS: Projected benefits of solid-state thermostat over traditional versions:
ʝ Enhanced Reliability: Solid state thermostats are less prone to failure, as they eliminate the mechanical wear and tear associated with traditional thermostats. This reliability is critical in maintaining consistent preheating operations, especially in harsh critical locations.
ʝ Improved Precision: These thermostats offer highly accurate temperature control, ensuring that engines are heated to the exact required temperature, thereby optimising performance and reducing unnecessary energy consumption.
ʝ Energy Efficiency: With better precision comes enhanced energy efficiency. Solid-state thermostats reduce the risk of overheating and the corresponding waste of energy, leading to lower operational costs and a smaller environmental footprint.
ʝ Durability: Built to withstand extreme temperatures and conditions, solid-state thermostats offer longevity that surpasses that of conventional thermostats. This durability makes them ideal for use in challenging environments where engine reliability is paramount.
Preheat launched their solid state (digital) thermostat in August’24, some 18 months following the initial conversations with customers and friends. The new product launch is testament to the appetite, tenacity, technical understanding, time, energy and money spent by Simon and his team at Preheat to tackle an industry and
Preheat digital thermostats represent, what they believe to be, a first for engine coolant heaters, providing a much more consistent temperature, with adjustable temperature settings and accurate readings by connecting to the onboard PIC device. They have increased accuracy as readings are taken every few milliseconds and can now provide valuable historic information logs and feedback for operating environments. They ultimately use less electricity than traditional counterparts and more importantly will provide better longevity, meaning a much lower replacement rate and ultimately lower overhead and cost of repair for both customers and the manufacturer.
With solid-state thermostats set to become a standard in the industry, it means more reliable engine start-ups, reduced maintenance costs, and a greater commitment to energy efficiency and environmental responsibility.
For these reasons, Preheat believes that this product development represents a major industry innovation.
If you would like more information or would like to contact Preheat Engineering - please send your enquiry to sales@preheat.co.uk.
Bernard Gospel
Technical Committee
Secretary TechSec@AMPS.org.uk
This is a series of articles on the topic of the history of engineering from AMPS’ Technical Secretary
Bernard Gospel
. The articles are loosely based on the BBC radio programmes and podcasts ‘A History Of The World In 100 objects’ and ‘50 Things That Made The Modern Economy’.
Europgen held a conference with an awards event and formal dinner at the Palazzo Real in Naples in October 2024. This cast my thoughts towards the Romans and aqueducts. (Note: Roman units of length measurement have been used, see the end for a relevant list).
Marcus Drusus Sulla was puzzled and concerned. As an Aquarius, water engineer, in Rome, he had been summoned to the presence of Silvanus Staberius Flavinus, the Curator Aquarum, who was in charge of Rome’s water supplies. Marcus was curtly
greeted by Flavinus, a person he had not met before. He was then told that due to a sudden and unexpected vacancy, he, Marcus, had been transferred with immediate effect to Napoli to examine the Aqua Augusta aqueduct system and to report his findings to the Curator there Julius Lucius Gracchus. Marcus was appointed Aquarius of the Aqua Augusta, a senior position, for a man of his age, twenty-three.
Armed with a warrant from the Curator, Marcus took a place on a ship from Ostia, Rome’s then port to Napoli. He reported as
instructed to Napoli’s Curator Aquarum whose office was located close to the forum. Marcus was told little, other than that the previous Aquarius had been sent to Syria to oversee the construction of a new aqueduct system at Homs.
By the curator’s attitude Marcus detected that the previous Aquarius had upset some member of the rulers of Napoli, the capital city of the region of Campania, and the second city of Roman Italy. Marcus made no comment, remaining silent as the curator stared at him. Marcus was told to go to his office, with the warrant of appointment the curator signed and gave to him. He was to return the next day at the time of Hora Septa to receive his instructions from the city council. After lunch noted Marcus…
Marcus left and was directed to his office by a slave. He introduced himself to the only other occupant of his office, a clerk by the name of Julius. Marcus asked Julius for a plan of the Aqua Augusta, and was given a roll of parchment, Marcus took it to his desk and unrolled it, holding the ends down with paper weights to hold it flat.
Marcus studied the plan, noting the scale given at the bottom left.
The layout was similar to the aqueduct systems of Rome, this was to be expected as Roman engineers were trained to follow the practices of their forebears. The system originated at springs at Fons Augusteus in the mountain of Termino. It then ran roughly east to west to Napoli, with branches to the north feeding the towns of Nola, Acerrae and Atella. To the south, feeders ran to the coastal cities of Pompeii and Ercolano, straddling the mountain of Vesuvius then to the town of Pozzuoli. A further southerly branch led to the villa of Posillipo. The system terminated at the Piscina Mirabilis Castella at Misenum, a major Roman Naval base, Marcus knew. Marcus noted that there was no collection from springs on Vesuvius, nor any river water intake although there were a few additional spring infeeds elsewhere.
The clerk knew his job, and silently handed Marcus the next roll, a section of the aqueduct system showing the levels along
the aqueduct from the source to where the system terminated at Misenum where there was a tank, the infeed height there was given. The actual tank level would be on the daily records but was not material at the moment. He remembered the route length of the aqueduct from spring to Misenum, 59 miles. Experience gave him the average gradient: 1 in 350. Not unusual, but above the minimum to keep a steady water flow. As an Aquarius, Marcus knew that if the water was not to suffer from stagnation, then the water should always be flowing, even if some of the end product was discarded. He knew the smell and colour of stagnation, but not the cause, the germ theory of disease being much in the future.
The opposite and too high a flow would result in erosion of the stone of the aqueduct and support at horizontal bends would be required to mitigate the thrust as the fluid turned. Newton would begin to understand that, again in the future. Filling the channel completely with water would result in it being pressurised, requiring a much stronger and expensive construction. The Romans seemed to have understood cost benefit analysis, but it is not known how they quantified it.
Most of the aqueduct was in a covered channel, built of stone. Channels on bridges like we see today at Pont du Gard and Sergovia are dramatic but were only used where necessary, as they are expensive, at least in manpower, to construct. There was a stretch near Napoli, to cross a wide valley which was arched. There were several tunnels along the route, these as Marcus expected, contained pipelines, probably terracotta clay, but inside tunnels to allow maintenance for access. The diagram showed him that the pipeline sections were fed by Castellas to allow the flows to be balanced. It was difficult to match the flow capacity of an open channel to a flooded pipeline. A Castella allowed the pipeline to be constantly flooded with the surplus spilled over. A Castella is what we would call a tank, usually constructed in stone.
The whole system ran by gravity, Newton would have been proud! If it were not for the intermediate Castellas, which also acted by virtue of reduced flow as settling tanks, a
stone ball placed on the aqueduct floor at the source, were the system dry, would roll all the way to the terminus of the aqueduct.
Romans knew about pumps, and could have built them large enough, but did not have any power source to drive them continuously. Watt and Trevithick would have been rich in Roman times!
Marcus worked his way through the other documents kept here since the army built the aqueduct some one hundred years earlier.
The clerk carefully returned the rolls to a chest, then took Marcus to visit the local depot where a team of maintenance men were based. He gave them instructions for the morrow, then left, thinking about the meeting the next day.
Points….
ʝ Romans did not invent the aqueduct but improved the technology.
ʝ Herculaneum, at the time and now, is known locally as Ercolano.
ʝ Whist there is no evidence of the Aqua Augusta being connected to Herculaneum, other similar cities were.
ʝ At the time of this event, the aqueducts of Rome supplied as much water daily to Rome as that currently supplied to modern major cities, i.e. London, New York.
ʝ The flow of the Aqua Augusta is estimated at 50 000 m3 per day from the source.
ʝ Some roman aqueducts are still in use today, typically the Aqua Virgo, which, continues to serve modern Rome, its waters flowing through the iconic Trevi Fountain.
ʝ Roman Aqueducts were usually ‘open channels’ i.e. the water did not rise to the level of the roof. The roman engineers seem to have preferred these because being unpressurised the construction was simpler and maintenance more straightforward. Pipelines or pipes were only used after the termini or where thought advantageous. Marcus avoided speaking to the council about one thing Roman Engineers had not resolved: how to predict the flow in an open channel. Two thousand years later it is still usually left to empirical means, as the flow is so complex!
To be continued…
Naples was the location of EUROPGEN’s successful 2024 conference and Grand Gala Dinner and Awards event. The gathering was themed “Generating Sets, Industry Insight 2024” – and was a collaboration between EUROPGEN and Generazione Distribuita, the Italian generating set trade association.
AMPS representatives participating included Louise Hazel (AMPS’ Chair), David Oates (Director General) and Bernard Gospel (AMPS’ Technical Secretary and Chair of EUROPGEN’s Technical Committee). Amongst others present were AMPS’ Council members Riccardo Sardelli (Volvo Group) and Andrew Bell (Mecc Alte UK) – as part of an international attendance of 180 delegates from four continents. Awards recipients also
Conference dinner guests at the Palazzo Reale di Napoli
featured a familiar name to AMPS members, Richard Payne of Cummins.
The Conference was chaired by Marco Monsurrò, President of Generazione Distribuita and EUROPGEN. He stressed to the European Commission the need for a regulatory framework to recognise the critical role of energy security played by generating sets. The Commission was represented by Elena de Gregorio of DG Energy (ENER).
Guest speakers also covered prospects for the genset market, particularly from high data centre related demand and rental. Discussions underlined a consensus that there would be a continuing need for combustion engine technology, right through to mid-century. On rental, there was debate on whether Stage V was fully embedded across the EU and the likelihood of whether Stage VI would be forthcoming.
Steph Shencoe, the Social Media and Partner Communication Manager of Primary Engineer, explains
how her organisation works to enthuse and inspire future generations of engineers by working with schools and industry.
From the sleek smartphones we cradle in our palms to the towering skyscrapers that pierce the skyline, engineering is the unseen force shaping our world. It's the intricate network of roads that connect us, the powerful machinery that fuels our industries, and the groundbreaking technology that pushes the boundaries of human innovation. Yet, despite its importance, the UK faces a double-edged sword: an aging workforce and a reduced pipeline of engineering talent.
A world without engineers is a world we can scarcely fathom. But it’s not all doom and gloom. You know that phrase, “children are our future”? Well, they aren’t wrong.
The importance of early engineering engagement with pupils has never been more acute. Research shows STEM aspirations and perceptions are formed during the primary years and have solidified by the age of fourteen. In addition, there is an increasing recognition that a more diverse talent force with a problem-finding and creative problemsolving approach will be critical if we are to successfully transition to new technologies and provide the solutions required to achieve net-zero and other global challenges.
But despite engineering being the backbone of our world, many young people remain unaware of the exciting and diverse world of engineering. They often perceive it as a complex and unapproachable field, dominated by outdated stereotypes.
But despite these challenges, for the past 20 years everyone at Primary Engineer, a UK-based educational not-for-profit, have been on a mission to bridge the gap between education and industry. We have been bringing engineering to life in classrooms across the UK with our range of fully funded educational programmes, competitions, and qualifications. These activities are designed to engage both teachers and pupils in significant ways by creating meaningful connections between engineering principles and real-world applications.
We have seen a fantastic increase in the number of engineers volunteering their time and companies supporting their mission. Their involvement has helped us showcase the variety of engineering careers and opportunities, making the field come alive in classrooms across the UK.
By fostering collaboration between industry professionals and educators, we are breaking down barriers and creating a more inclusive and accessible engineering landscape.
Our reach extends far beyond the boundaries of the UK’s devolved curricula, touching schools from bustling city centres to expansive rural areas. In the 2023-2024 academic year alone, we reached an impressive 117,047 pupils, 6,630 teachers, and 1,608 engineers, collectively investing over 842,846 pupil hours in engineering education which is the total amount of time school
pupils spent learning about engineering in school. These statistics are a testament to our impact and commitment to inspiring the next generation of engineers.
Beyond the numbers, are the stories from engineers, parents, carers, teachers, and the young people themselves are extraordinary examples that the dial is changing significantly. Our approach is much more than just a fleeting moment – it’s about creating lasting memories, developing skills and opening doors to their future careers and interests.
The definition of an engineer and the perception of engineers has been at the heart of STEM engagement for decades. We can clearly see that from the 117,047 pupils who took part in our competitions and programmes over the 2023 – 2024 academic year, they perceive engineers to be the people who help others, produce creative solutions to the world’s problems large and small, are not afraid of automation, robotics or AI.
The engineering skills gap is a complex issue, but we are so proud of our work. Over the past twenty years, the perception of engineering has been transformed but there’s still more work to be done. If you are looking for a partner who can help with skills, social outreach or to simply inspire young people with engineering then reach out to us https://www.primaryengineer.com/ funding-enquiry/
Be part of the story and help share the future of engineering in the UK.
This
is the second half of
an
opinion
piece authored by Geoff Halliday for WB Power Services. We rejoin his commentary as he addresses issues around Nitrous Oxide. The first part of the article was published in the Autumn 2024 issue of AMPS Power.
Medium Combustion Plant Directive (MCPD) - Reduction of Nitrous Oxide: The MCPD is EU legislation that became UK law in December 2017 (Directive (EU) 2015/2193) and covers diesel engines with ratings between 1 and 50MWth requiring them to meet a level at or below 190mg of NOx/Nm3. These “medium sized engines” represent an important source of the emissions of Nitrous Oxide (NOx) and dust (Particulate Matter). The Directive seeks to regulate the emissions of them with the aim of reducing the production of these substances known to be harmful to human health.
Selective Catalytic Reduction (SCR) are active post-combustion NOx emission control systems. These units work in a similar way to how a catalytic converter works to reduce NOx emissions in a car. Catalytic converters circulate un-oxidised portions of the exhaust stream in an oxidising environment to break down additional hydrocarbons and react with NOx. SCRs are different in so far as they incorporate a gaseous or liquid reductant, generally ammonia or urea in this case, to the exhaust gas stream. The exhaust gas mixes with the reductant and travels through several catalytic layers, where a reaction between NOx emissions and the injected reductant occurs. The reaction converts the NOx emissions into N2 and water vapor. The benign elements are then released into the air through an exhaust/flue arrangement specifically designed for the application.
One common problem with selective catalytic reduction systems (SCR), or many other catalytic devices, is that they
operate effectively within a relatively narrow temperature band. In the case of standby generating plant specifically it means that the set(s) must be working at relatively high levels of load for at least ten minutes (and consistently thereafter) for the optimum operating temperatures to be achieved that will allow the catalytic reaction to occur. A close loop management system is essential to ensure there is no ammonia slip produced in the exhaust discharge.
In this section we consider current and developing solutions that can be built into new infrastructure currently in the early stages of development. We also consider the limitations as we currently know them to be. These products include:
ʝ Battery storage systems such as Lithium – Ion. These are available today and being trialled on the grid, data centres and other large-scale projects.
ʝ Other more compact and efficient
battery/chemical storage types under development.
ʝ Mechanical Energy storage systems such as pumped water storage have been around for a long time. Others such as such as compressed air storage and flywheels are also under development.
ʝ Fuel Cells have been around for many years and continue to see improvements in performance. They have a lower footprint compared to batteries, and the possibility of quick refuelling with more readily available pressurised or liquid H2 open up the possibility of wider acceptance. These factors mean fuel cells could be adapted for backup applications and more extended storage periods.
ʝ A new range of standby generator engines that can run on hydrogen rather than diesel or HVO alternatives. Whilst this technology is available today on smaller engines it will be some time, maybe ten years or more, before medium and larger engines are available for applications such has hospitals and data centres.
HVO and hydrogen are a current and potential future fuel to power standby generation as we know it to be today. This section of the disposition looks at the care that needs to be taken in the selection and sourcing of these alternative fuels.
Hydrotreated Vegetable Oil (HVO) is a liquid fuel that is a paraffinic bio-based liquid fuel produced using a special hydrotreatment process. It is manufactured from many kinds of vegetable oils, such as rapeseed, sunflower, soybean, and palm oil. Some or all of these sources can be from waste products such as used frying oils or animal fats hence can be made from an entirely renewable energy source that do not impact crop resources.
First-generation biodiesels such as EN590 B7, which we currently use in road vehicles and standby generation, contains just 7% of bio content. The adoption of HVO (EN 15940) could translate into a widely claimed maximum 90% reduction in CO2 emissions over its entire lifecycle. It has not been possible to find a reliable source to back up this claim and how it might be realised. Some HVO however is manufactured either as an entirely “new” product or a mix of products. Such products use newly harvested oils such as sunflower, palm oils etc which remove these from the food chain, and in the case of palm oil production, is known to be responsible for widespread deforestation. Care should be taken when selecting a source of supply to ensure that the up to 90% CO2 lifecycle reductions are maximised.
I have only been able to locate one manufacturer of HVO in the UK. This source is using totally recycled products. It must therefore be assumed that all other supplies are manufactured outside the UK.
Other points to note are that:
ʝ HVO has a slightly higher energy density than fossil diesel by weight but it has a lower energy density by volume. Test results undertaken by an engine manufacturer indicate that engine fuel consumption by volume is higher 4% in l/hr.
ʝ HVOs (or HWCOs) are straight chain paraffinic hydrocarbons with the chemical structure CnH2n+2, free of sulphur and aromatics (Aatola et al.,
Figure 4 – Selective Catalytic Reduction (SCR) unit
HC (Hydrocarbon Injection) for active regeneration when exhaust gas temperatures are low i.e. Low Loads
2008). As HVO contains no oxygen, the oxidation stability is higher compared to market diesel, resulting in very good storage behaviour; its much higher Cetane Number (CN) (EN15940 Class A = 70) when compared with EN590 B7 diesel translates into a much cleaner burning fuel.
In relation to NOx there are a number of conflicting effects which influence the formation of NOx. The absence of oxygen and aromatics in HVO generally prevent the formation of NOx. Aromatic compounds typically have a higher adiabatic flame temperature which leads to a higher local combustion temperature in the cylinder. The very high cetane number of HVO may promote NOx formation, as it leads to a decrease of ignition delay, meaning that the start of combustion is earlier (well before the top dead centre), which results in earlier pressure and temperature rise which of itself could be overcome by changed engine mapping. As a result, no clear conclusion concerning HVO effect on NOx emissions can be drawn, as mixed effects have been observed.
Hydrogen (H2): A number of combustion engine manufacturers are working on projects related to either modifying existing engines or developing new engines to run on hydrogen. These are likely to be “smaller” engines up to 10l in capacity (diesel equivalent) for the mass market i.e. trucks and buses. These will then be adapted for the standby generator market. Some early modified engines are currently coming to the market but there is a long way to go before these are likely to be widely adopted and even longer before mid-range (10-25l diesel equivalent) and large engines (30-100l+ diesel equivalent) are available. Time scales are likely to be in the range of 10 to 15 years. Regardless of the fuel used NOx will always be present in the exhaust of an internal combustion engine. As with
the production of HVO, consideration needs to be given to the environmental impact of production and the operational constraints such as:
ʝ Availability of hydrogen.
ʝ Storage of hydrogen, given that it would currently require over 50 tonnes of hydrogen to support an all-electric major teaching hospital for 48 hours.
Fuel cells or hydrogen fuel combustion engines can only really be considered ‘green’ if the hydrogen used to power them comes from sustainable sources such as renewables or nuclear. Research suggests that using energy generated by wind turbines to make hydrogen by the hydrolysis method is the “greenest” means of production. At time of writing there is a surplus of wind generation which could be readily redirected to this purpose.
Currently around 95 percent of hydrogen comes from natural gas and making 1kg of this ‘grey’ H2 emits 11 tonnes of CO2. ‘Blue’ hydrogen is produced the same way, but the CO2 is captured and stored. Suitable storage sites are currently few and far between, so availability is limited. The long-term solution comes with “green” H2 made from renewable energy such as wind, solar or nuclear. It should be recognised that this is many years away from being practically available at scale. Any H2 produced is hard to store in bulk without significant investment in associated infrastructure.
Efficient methods of hydrogen storage and distribution are key to enable the development of technology for the advancement of hydrogen and fuel cell technologies in applications which include transport, stationary and portable power. Hydrogen has the highest energy per mass of any fuel. However, its low ambient temperature density results in a low energy
Stage 1
Reduction of Carbon monoxide (CO), Hydrocarbons (HC) & Particulate matter (PM) with DOC + DPF
per unit volume, which necessitates the development of advanced storage methods that have potential for providing a much higher energy density. The US department of Energy identify four specific methods of hydrogen storage. These are:
ʝ Compressed Gas.
ʝ Cold / Cryo Compressed Gas.
ʝ Liquid H2.
ʝ Materials based solutions – five options in number.
ʝ Reduced running of generating sets for regular maintenance and testing.
All such methods require the use of additional energy. For example, maintaining the necessary very low temperature required to keep hydrogen in a liquid form. The UK plan to include the large-scale production and wide scale distribution of both “blue” (with carbon capture) and “green” hydrogen as a way by which countries’ climate change objectives can be reached.
It is clear that good progress has/is being made in reducing some of the key pollutants created in the burning of diesel fuel in an internal combustion engine, such as HC’s and PM’s but there is a still a way to go. The two “unavoidable consequences” of this method of combustion are CO2 and NOx which will continue to be persistent problems whilst we
Stage 2
Reduction of Nitrogen Oxides (NOx) and Ammonia Slip with SCR (Selective Catalytic Reduction) and ASC Technology
continue to use conventional hydrocarbon diesel burnt in an internal combustion engine.
The use of HVO when combined with the addition of an SCR can bring a packaged standby generator solution to the point of operation with a potential 90% reduction in CO2 emissions and NOx levels. Well inside the requirements of the MCPD for NOx and other key emissions requirements. This applies to both existing installations and those still in the design stages. Care must be exercised:
ʝ When modifying the exhaust system of generating sets with older engines (typically older than 8 to 10 years depending on model and manufacturer). This should be done in conjunction with both the manufacturer and emissions experts.
ʝ When modifying the exhaust system of generating sets more recently installed (typically less than 5 years depending on model and manufacturer). This should be done in conjunction with both the manufacturer and emissions experts.
ʝ When design and planning new installations to ensure the latest developments in engine design, fuels and emissions treatments are used.
ʝ In the selection of supplier for HVO to ensure that as close to the 90% “claimed lifetime reduction in CO2 emissions” are achieved with the use of sustainable
sources and derived from waste and residue oils not from “virgin” oils.
The use of hydrogen fuel in an internal combustion engine as an alternative to BS590 B7 diesel or HVO for large standby power installations is still some years away. Significant progress needs to be made on the production, storage and distribution of both “blue” and “green” hydrogen before this fuel becomes a possible alternative to HVO especially for large scale installation.
Fuel Cells have been with us for a number of years but their use in larger scale standby applications is still minimal due to the limited capacity of the devices and the availability of hydrogen. They differ from the internal combustion engine as neither CO2 nor NOx is emitted during the conversion of hydrogen to electrical power.
Large capacity batteries, mostly Lithium-Ion, are currently being deployed as grid balancing devices (mopping up surplus wind power capacity for example) and also on some early standby applications. Physical size is a major limitation and as, in the years ahead, Lithium is used more widely across many different applications, such as cars, it could be a limiting factor in their adoption.
A copy of the full article, with supporting references, is available on request to ampsmagazine@amps.org.uk
About the author: Geoff Halliday started as an apprentice. He worked his way up through a variety of roles from customer service engineer to managing director. He has now worked in the critical power sector for over 40 years. Drawing on his management skills, product knowledge and vast application experience amassed throughout his career, Geoff now enjoys sharing his knowledge with others. For more information about WB Power Services go to www.wbpsltd.co.uk.
CHAIR
LOUISE HAZEL IPU GROUP
COUNCIL MEMBER PAUL AITKEN GET POWER SOLUTIONS
COUNCIL MEMBER ALAN BEECH CLARKE ENERGY
COUNCIL MEMBER ANDREW BELL MECC ALTE UK
COUNCIL MEMBER CHRIS CALDWELL CRESTCHIC
COUNCIL MEMBER
PAUL CAMPBELL INDUSTRIAL POWER SYSTEMS LTD
COUNCIL MEMBER
RICHARD A COLLMAN ACOUSTICAL CONTROL ENGINEERS
COUNCIL MEMBER KÖKEN GUNES AKSA POWER GENERATION
COUNCIL MEMBER GEOFF HALLIDAY WBPS LTD
COUNCIL MEMBER
GAVIN HEPBURN DALE POWER SOLUTIONS
COUNCIL MEMBER
RICHARD RUSSETT KOHLER POWER SOLUTIONS EMEA
COUNCIL MEMBER RICCARDO SARDELLI VOLVO GROUP
COUNCIL MEMBER NEIL SMITH
CATERPILLAR RETAIL ELECTRIC POWER SOLUTIONS
COUNCIL MEMBER CARLOS VICENTE EMINOX LTD
COUNCIL MEMBER LISA WILSHAW GREENSHIELDS JCB
TECHNICAL COMMITTEE: CHRIS MARSLAND (CHAIRMAN) BERNARD GOSPEL (SECRETARY)
MARKETING COMMITTEE: RICCARDO SARDELLI (CHAIRMAN)
FINANCE COMMITTEE: RICHARD A COLLMAN (CHAIRMAN)
SECRETARIAT LEAD: JOANNA OLIVER MBE
Powergen International – 11-13 February: Dallas, USA
EXECUTIVE HIRE SHOW – 12-13 February: Coventry
Energy Storage Summit – 17-19 February: London
International Energy Week – 25-27 February: QEII, London
The Energy Transition Expo – 5-7 March: Rimini, Italy
DATA CENTRE WORLD - 12-13 March: ExCel, London
DISTRIBUTED ENERGY SHOW – 12-13 March: NEC, Birmingham
BAUMA – 7-13 April: Munich, Germany
Middle East Energy - 7-9 April: Dubai
AMPS AGM, CONFERENCE & LUNCH
– 30 April: One Great George Street, London
AMPS GOLF DAY – 2 June: Forest Pines (Brigg)
International Power & Generating Sets Expo – 11-13 June: Shanghai, China
PLANTWORX – 23-25 September: Newark (UK)
SOLAR & STORAGE – 24-26 September: NEC, Birmingham
Healthcare Estates (IHEEM) – 21-22 October: Manchester
The Showman’s Show – 22-23 October: Newbury
EMEX – 19-20 November: ExCel, London
OCTOBER
AMPS INDUSTRY DAY
NOVEMBER
AMPS AWARDS FOR EXCELLENCE GALA DINNER (Manchester)
Key: AMPS events highlighted in RED. Events with an AMPS’ presence are shown in BOLD CAPITALS