
4 minute read
Reliable rumble strip creation
A modern IT platform and tried-and-tested thermoplastic extruder are making it easier to create centerline rumble strips, a very effective traffic safety measure
Words | Christina Krogh, Borum Industri, Denmark
Borum’s thermoplastic extruder has been used to make rumble strips for decades
Many international studies demonstrate that centerline rumble strips are an effective measure in reducing road traffic crashes. Some studies suggest that they can reduce the number of crashes by up to 55%1. It is also the reported experience of Borum’s customers who apply this kind of marking.
Single-vehicle run-off-the-road crashes and collisions caused by cars going across the centerline and into the path of oncoming vehicles are not uncommon on highways and two-lane rural roads. This has inspired various stakeholders to experiment with centerline rumble strips. They are placed between opposing lanes of traffic to alert drivers that they have crossed over into the path of oncoming traffic. These raised or grooved patterns suddenly produce an uncomfortable vibration and noise as the vehicle’s tires pass over them, to stimulate the driver’s attention, and consequently act as a countermeasure against run-offthe-road accidents and head-on collisions.
Borum machines have been used to apply these markings all over the world, in countries including the USA, Australia and Denmark. They can be implemented as extruded profiles in thermoplastic material, or as a two-component profile application.
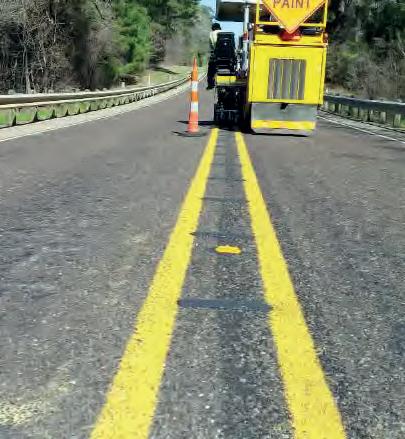
Thermoplastic extrusion
Extrusion of thermoplastic material is the classic solution used to achieve
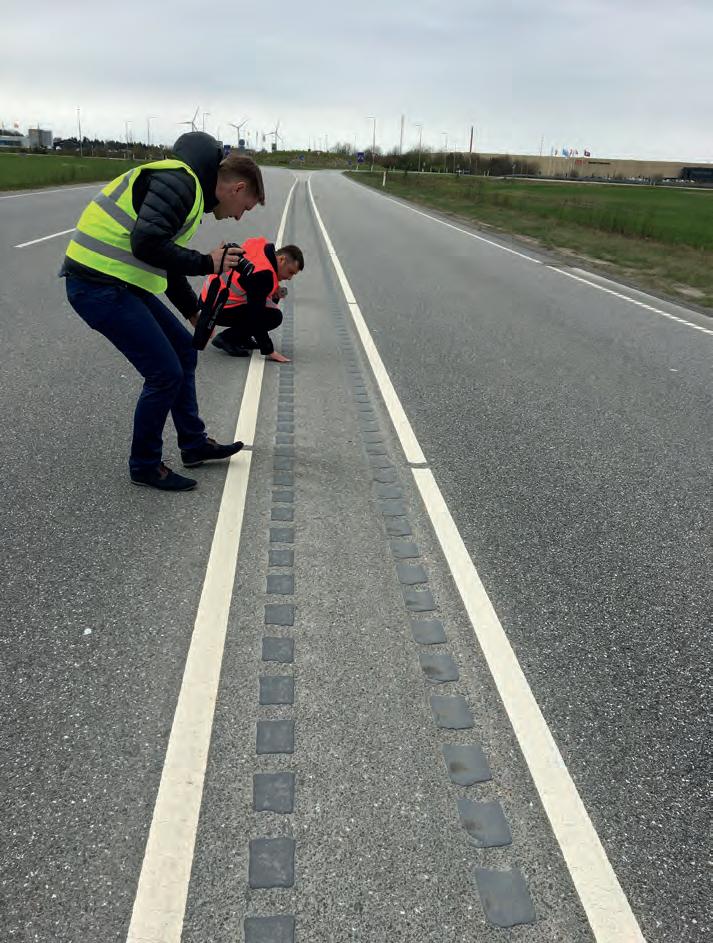
a safe and cost-effective type-two road marking, ensuring long durability even on demanding road types.
Borum has set the industry standard for decades with its thermoplastic extruder, which makes it possible to fulfill the marking requirements set by road authorities across the globe.
The Borum technology inside the extruder equipment perfectly controls the heat and the pressure of the material in front of each shutter, ensuring that the width and the thickness of single and double lines remains constant. A strong pump located inside the feeding auger of the extruder ensures the recirculation of the material from the outlet of the material deposit and all the way down to each of the shutters in the extruder head. This technology also ensures a perfect line start, even after the machine has been standing still – while the thermoplastic material is filled, for example, or while traffic is redirected.
The extrusion performance is automatically adaptable to changes in speed. Within the speed range for extrusion, the BM LineMaster computer can automatically increase or decrease the internal circulation rate according to the speed of the machine and thus compensate for the difference in thermoplastic consumption at different speeds. This releases the operator from a focus-dependent task so they can concentrate on other important issues.
Another crucial feature is the speed of the extruder’s shutters, which must move very fast. This is especially important for structured/profiled markings, to be able to make high profiles. The Borum extruder’s shutters can open and close at around five times per second, controlled by high-quality pneumatic valves. The height of the extruded profiles differs from one country to the next. In Denmark, it’s typically 3-5mm (0.11-0.19in), whereas in Australia and the USA requirements can range from 3-12mm (0.11-0.47in) in height.
The extrusion process works with all types of premium thermoplastic material, as long as the material fulfills demands for thermal stability and viscosity.
Computer control
Another piece of equipment that is required to make this kind of marking is the Borum LineMaster. Using the LineMaster, operators can control all shutters from their seat. For example, to make a line that is 30cm (12in) wide, they would need to open six shutters at the same time. Mechanical and pneumatic delays could prevent the shutters from opening at the same time, but this can be rectified using the LineMaster. The operator can set a delay for each shutter to start and stop, to synchronize the line.
The LineMaster is easy to program, as the sequence follows the daily marking routines. Marking programs can be stored, making them easy to find again for the next day’s or next year’s work. It is simple to learn and easy to operate.
The markings made during the day are logged in the computer’s memory, enabling easy and fast reporting to management. The operator simply plugs in a memory stick to retrieve the data and can also access the data in the cloud (Borum Online). The IT platform is Window CE, so the data is compatible with nearly all computers. This also enables dialog between the road marking computer and office computers – a feature that makes training and learning more efficient, as it can be done in the office. n
Left: Black centerline rumble strips being
implemented in Denmark
1) Mustaf Jama Mohamud, supervised by Jens Christian Overgaard Madsen, Centerline Rumble Strips – Safety Evaluation, Aalborg University (2011), p37. Literature analysis of a study by Masayuki Hirasawa, Hisashi Aita, Motoki Asano and Kazuo Saito, Development and practical use of rumble strips as a new measure for highway safety, Journal of the Eastern Asia Society for Transportation Studies (2005)