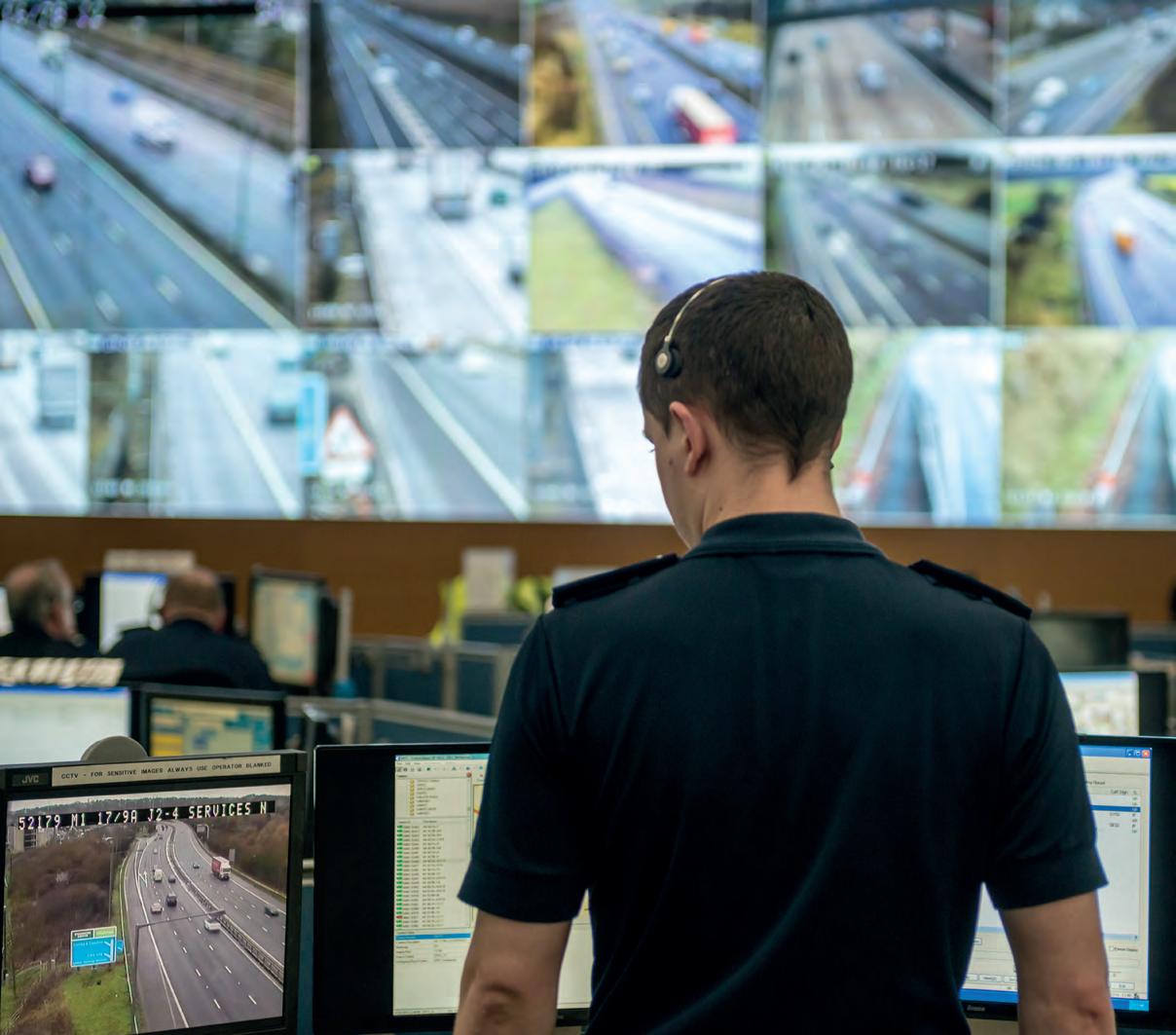
5 minute read
A shortcut to control room cost-efficiency
Figure 2: Caption
Upgrading control-room screen technology is an expensive business, but now you can fit LED illumination to old units at a low cost. As a result, running costs can be saved without having to upgrade entire systems
Words | Peter van Dijk, Mitsubishi Electric, Netherlands
Technology will always deliver better ways of doing things – more cheaply, faster and more efficiently. However, systems can only evolve as fast as the infrastructure allows. In an increasing number of cases, this inertia is costing traffic control room operators dearly. But a new innovation from Mitsubishi Electric offers an elegant solution.
Enhancing possibilities in one area of a system invariably increases demands in other areas. In traffic control rooms, with the long lifespans of installations – 20 years in some cases – the problems of overloading can become acute as aging infrastructure struggles to cope with increasing demand, changing mission goals and management ethos. Typically, these problems manifest themselves most clearly at the focal point of all control room activity – the main video-wall display.
Rapid growth in technologies such as IP cameras and other sensors means that as time marches on, older display systems are being stretched to the limits of their capability. The increased use of technologies such as computer-aided dispatch (CAD) and record management systems, together with policy favoring the economies of scale offered by centralized command and control facilities, only serve to compound
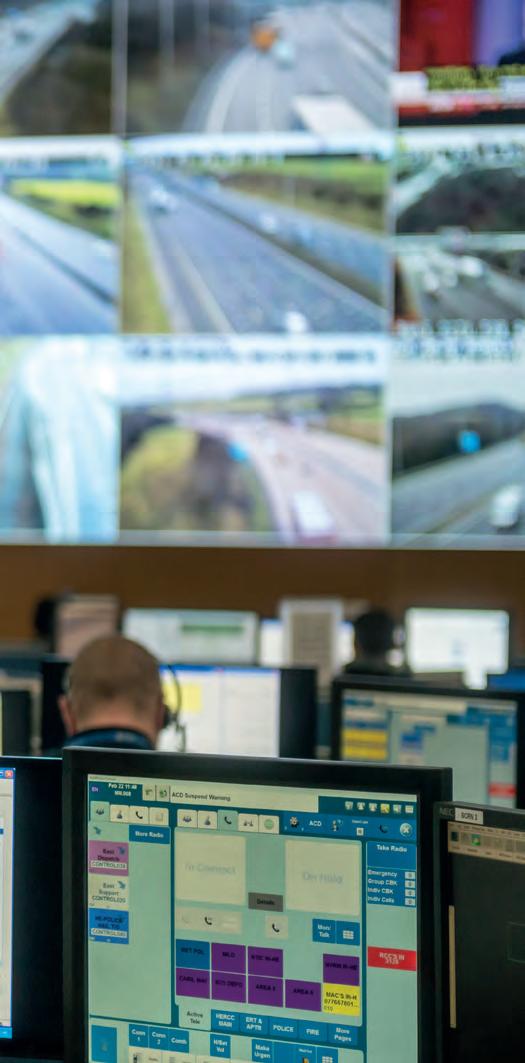
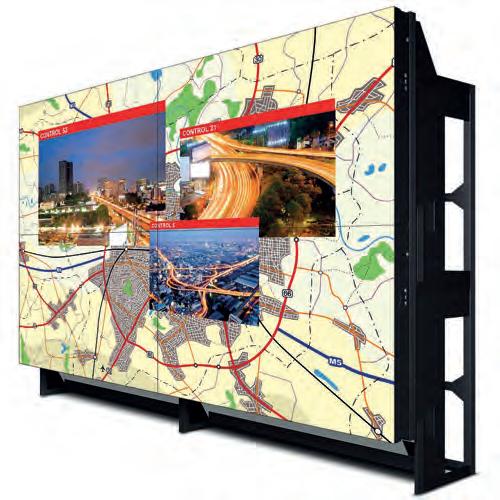
the problems. An industry survey from 2016 found that 74% of participants believed that control rooms are struggling to keep up with demand, with the evolution of LTE networks and big data in traffic control applications promising no prospect of respite.
But it’s not just the hardware that is finding it difficult to keep pace with ever-increasing demands. Business and management policies and priorities have also changed dramatically over the last 15 years. Procurement is now subject to very much more stringent policies with regard to sustainability. The UK government guidelines, for example, set minimum requirements in areas like energy in use; end-of-life-related costs such as repairability, upgradeability and recyclability; the hazardousness of materials used; and resource efficiency in terms of quantities of scarce materials used and content recycled. Older display technologies employing non-LED illumination such as mercury lamps are simply not capable of meeting the standards required today. Both financially and ethically, the continued use of older, less efficient technologies such as mercury lamps is increasingly out of step with contemporary management policies.
Financially too, continuing the use of older technology carries a hefty penalty. Mercury lamps have an average lifespan of between 5,000 and 6,000 hours, meaning they need to be replaced every year at a cost of around £1,000 (US$1,300)a time. With their diminished popularity, sources of supply are becoming increasingly difficult to find and there is an inevitable upward price-pressure as a result. The RoHS and WEEE directives place special
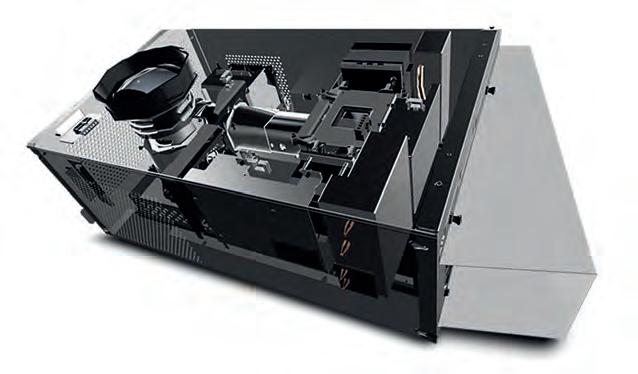
Above: Mitsubishi Electronic’s
Universal Upgrade Engine (projector) and VS-60HE12 Slimcube (videowall display)
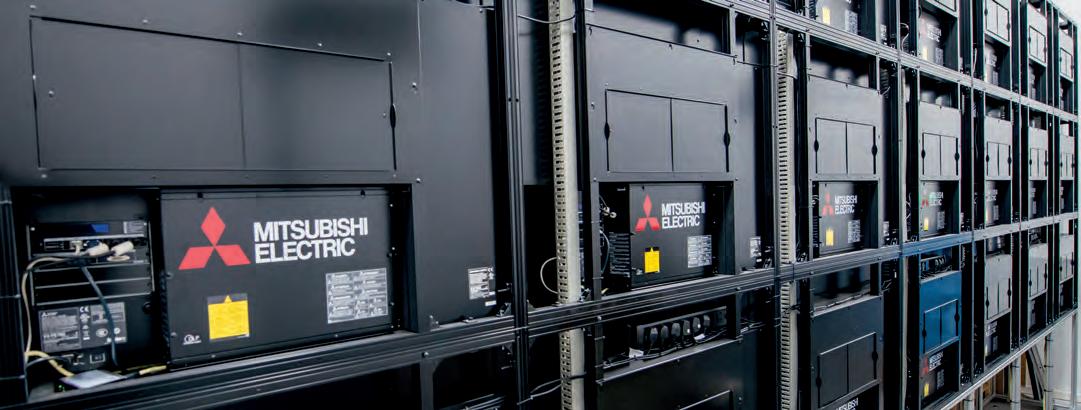
Above and right: The Highways England
control room in South Mimms, UK
restrictions on the disposal of spent units, too. Mercury lamp projectors employ a rotating color wheel, which also needs regular replacement, albeit at much longer intervals.
LED illumination, on the other hand, has on average of 10 times the lifespan of a mercury lamp, and in some cases much more. In Mitsubishi Electric’s VS-WE120U, for example, LED light sources are rated for 100,000 hours of continuous operation. No other serviceable parts are required, and in Mitsubishi’s case, projectors are air-cooled and so require no routine maintenance.
The performance of a modern LED display is also greatly improved compared with the previous generation of technology. Increased light output makes it less tiring for operators and allows for a good deal more flexibility in terms of the ambient light levels employed within the control room environment. Modern displays are quieter, and offer a much improved color gamut and stability. Higher resolutions are often available, allowing more data to be displayed, and behind the screen, connectivity has been greatly enhanced through the use of modern protocols such as DisplayPort and DVI, and in some cases the expandability of OPS slots or user-configurable input modules.
But while the latest technology very effectively addresses the limitations and drawbacks of the previous generation of devices, it offers cold comfort to users locked in to older display technologies that have yet to reach planned obsolescence. The toxic combination of the capital expense required to transition from legacy mercury systems to a modern solution, and the business case justifying the early abandonment of an investment that is still functional, is a difficult hurdle to overcome. The reduction of running costs achieved by switching to LED is considerable, but the investment required to completely replace a working system years ahead of its planned obsolescence, plus the need to write-off of a substantial fixed asset value, has in many cases ensured that even though the upgrade to LED is both logical and inevitable, the decision has had to wait until the cost of early refurbishment drops below that of maintaining the status quo.
Clearly in this situation, reducing the ‘cost’ side of the cost-benefit equation is a game changer – and that is just what Mitsubishi Electric has done with its Universal Upgrade LED projection engines. As a direct slot-in replacement for older projectors, the Universal Upgrade engines employ the latest LED technology and offer a cost-effective route out of financial purgatory, to achieve both a huge reduction in running costs and performance upgrades in terms of resolution and brightness. All the original cabinets and wiring are reused, saving expense and ensuring a fast, efficient installation, measured in hours rather than days.
Naturally, technology itself advances inexorably onward. Products and models that were common a decade or more ago have long since faded into obscurity.
To overcome this problem, Mitsubishi Electric now produces an extensive range of direct slot-in replacements for nearly every model and make of DLP rear-projection manufactured over the past 15 years. The solution has proved extremely popular, with many installations already completed across Europe, saving customers hundreds of thousands of euros annually. In terms of being cheaper, faster and more cost-efficient, Universal Upgrade engines from Mitsubishi Electric are ticking all the boxes. n
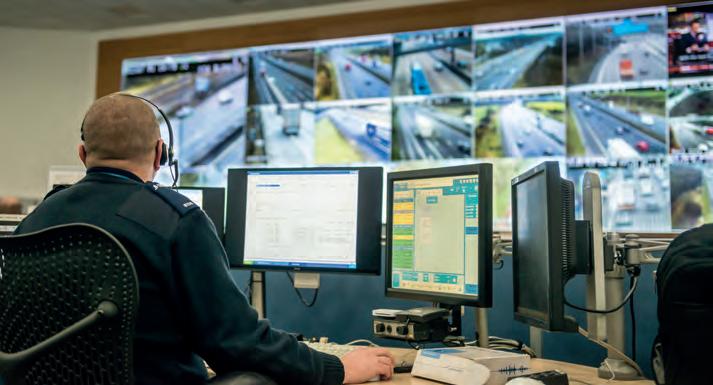