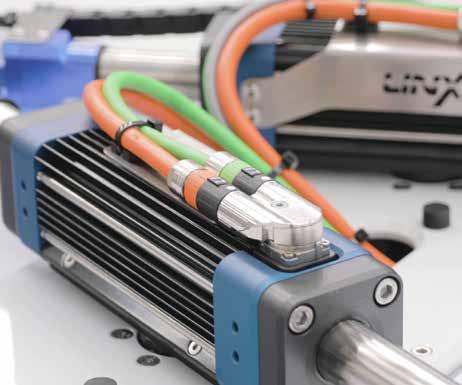
3 minute read
Motoring a revival for the food & beverage industry
from AMT DEC/JAN 2021
by AMTIL
Motoring a manufacturing revival for the food & beverage industry The food & beverage sector has been widely tipped to be integral in Australia’s post-COVID revival, but it needs to find ways to operate more efficiently to truly deliver on its potential.
Food & beverage is an important part of manufacturing, itself an important sector in rebuilding the Australian economy postpandemic. Food is the biggest part of the local manufacturing industry. Out of the top 100 Australian manufacturers by revenue, 35 are in food & beverage, and it makes up over a quarter of all manufacturing jobs and value-added output. The sector is a net exporter, selling to more than 200 markets and enjoying an enviable “clean and green” reputation globally for excellence. It is vital and resilient, continuing to grow even through recent conditions for manufacturers described as “reminiscent of... the Global Financial Crisis (GFC)”. Food manufacturing is also viewed by some of our leading businesspeople as a key area for accelerating the country’s economic recovery. To do the best at the important job ahead, the food & beverage sector – like every other – will need to find better ways of working. This includes investing in its people and processes, and adopting new technologies, such as flexible robotics, traceability solutions, increasingly digitalised supply chains, and new processing machinery. One area that operators wanting to run their factories more efficiently can look to are the motors behind processes like line distribution, filling, cutting and sorting. Pneumatic cylinders are a tried-andtrue solution, but they’re also noisy and energy-inefficient, and it can take hours to fine-tune air pressure. Tubular linear motors, on the other hand, can achieve very precise positional control and flexibility. Instead of being at one end or another, a linear motor can move to any single position within a stroke. Newer actuation methods, such as tubular linear motors, are a way manufacturers can drive efficiency and productivity in their factory equipment. Such linear electrical motors are quicker and more accurate, allowing higher throughput at higher qualities over the same period, and use less energy. They have fewer moving parts so require less maintenance. Moreover, their servo drives are easily calibrated, meaning less time spent between line changes. ANC Motion’s new LinX M-Series linear motor is an alternative to pneumatic, ballscrew, linear flatbed and other options. M-Series LinX motors are highly dynamic, with velocities up to 10m per second, acceleration over 30G, and are able to achieve a peak force of 1,200N. The direct drive nature also means there is no wear and no backlash, a clear benefit over ballscrew options. The high-speed product also allows high repeatability across cycles, with position feedback accuracy of 50μm. A typical payback period is between six and 12 months, with increased uptime and throughput and decreased maintenance quickly offsetting any cost difference versus pneumatics. The M-Series LinX’s mounting is designed so it can work as a “drop-in” for existing pneumatic cylinders. Installation is made easier by the 1mm air gap between the shaft and the forcer, which means a very relaxed tolerance requirement. The M-Series has users worldwide in machine tools, electronics, packaging and other sectors, but its high level of ingress protection (IP67, easily upgraded to IP69K) make it particularly well suited to food and pharmaceutical manufacture and the requirement of regular washdowns. Each unit has a fully potted body, with magnets fully encased in a stainless steel tube and tightly sealed using end caps and o-rings. ANCA Motion’s linear motors were originally developed for sister company ANCA CNC Machines’ FX Linear and MX Linear machines. ANCA is a leader in CNC tool grinding technology, with a series of world-firsts since beginning in 1974 and numerous awards acknowledging it as a leader in Australian industry for both its innovation and export achievements. LinX was designed and assembled in Australia, with a team of support engineers offering a high level of locally-specific expertise. International support is also available through a network of 125 support engineers in the United States, Mexico, Germany, Brazil, the United Kingdom, Turkey, and various Asian markets. The COVID-19 pandemic has put a magnifying glass up to the importance of Australian manufacturing, both during and after the crisis. Thankfully, the scramble to tool up and provide essential medical and sanitation products is over. In the short term, Australian manufacturers proved they’re more than capable of responding to a crisis. Again, the country is looking to them, this time over the longer term, to help generate prosperity, jobs, and play a role in the return to economic growth. It’s important that the country’s manufacturing sector – including its food & beverage component – can grow sustainably, firing on all cylinders.