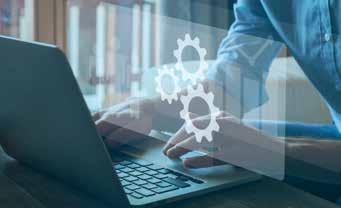
22 minute read
VOICEBOX Opinions from across the manufacturing industry
from AMT FEB/MAR 2021
by AMTIL
Grasping the opportunities of a COVID-normal world
Australia’s manufacturing industry stands to benefit significantly as the Federal Government seeks ways to spark post-COVID economy recovery. To truly grasp these opportunities, businesses must embrace digital transformation, writes Vijay Sundaram.
After an extraordinary 2020, the dawn of the new year has brought with it an Australian economy continuing to grow and recover, and new opportunities for businesses in a COVID-normal Australia. For manufacturing organisations and the industry as a whole, the importance of innovating, growing and playing a central role in Australia’s ongoing economic recovery is imperative. While many will be understandably keen to forget 2020 altogether, last year’s Federal Budget announcement was a good one for manufacturers, with the Federal Government putting a large focus on – and announcing a significant investment in – the Australian manufacturing industry. Over the course of the next four years, billions of dollars will be invested in projects that will grow emerging technologies, or enhance those in which Australian manufacturers already perform strongly. A few short months after the budget announcement, the Australian economy is already showing remarkable signs of recovery, coming out of nominal recession in December as most states and territories continued easing restrictions, and as industries found ways to innovate in a COVID-normal environment. However, with unemployment high, global supply chains disrupted and the looming cloud of escalating and volatile trade tensions, the industry must be dynamic and committed. To capitalise on the Government’s recovery plan, and to continue creating local jobs within the manufacturing industry, manufacturers must embrace digital transformation and befriend the technologies that will allow them to increase productivity, lower costs and drive their operations - and Australia - forward. Capitalising on the Government’s recovery plan
Manufacturing is a vital contributor to the Australian economy, employing 900,000 Australians and contributing around $100bn to the economy each year. However, over the course of the last 30 years, the employment rate within the industry has experienced a massive decline – once accounting for 16.5%, today it makes up only 6.4% of the country’s total employment. While identifying the industries crucial in helping to rebuild the Australian economy, the local manufacturing sector was given an empowering and unequivocal mandate to innovate. The Government’s significant financial commitment includes $1.5bn for the Modern Manufacturing Strategy, $1.3bn for the Modern Manufacturing Initiative, and millions more for the Supply Chain Resilience Initiative and Manufacturing Modernisation Fund. This is a glowing appraisal for the short, medium and long-term importance of Australian manufacturing, presenting an undeniable opportunity to revitalise an industry in need of renewal. Over the course of the pandemic, and even now as much of the world continues to experience varying lockdown restrictions, imports and exports have been disrupted, affecting the industry locally. It presents an opportunity for Australian manufacturers to capitalise on the faster-than-expected economic recovery, the Government’s financial injection and the disrupted status quo, to evolve internally and externally, and to lead by example. Digital transformation will be the foundation upon which manufacturers individually and the industry collectively can reinvent itself.
Befriending technologies long-term
In disrupting global supply chains in 2020, the pandemic has provided an opportunity for the local industry to evolve, become more self-sustainable and even capitalise on Australia’s strong sentiment for supporting local. By no means a new phenomenon, for years digital transformation has been highlighted as the future of work in every industry – manufacturing perhaps more than most. Adoption of simple integrated cloud-based technologies can significantly improve the way an organisation runs, creating agility, enabling rapid innovation and allowing companies to learn from experiences of others through connections and communities. Adopting the right software can also allow businesses to streamline, scale up, lower costs, and spend more time on productivity, growth and innovation. Customer relationship management (CRM) systems to manage leads and clients, collaboration software to bring in organisation-wide experts, and analytics tools to analyse and enhance, all customised and combined with countless other integrated platforms, from finance to process automation … this is what truly technologyempowered manufacturers look like. And then, with that as their platform, manufacturers can innovate through digital transformation and establish itself as a leader in smart manufacturing and factories, and Industry 4.0. While Australia has entered a more stable economic environment, much of the world is still in severe economic contraction and experiencing frequent fluctuations and restrictions that make it difficult to achieve stability or pursue growth. Despite Australia’s comparative success, the pandemic and escalating trade tensions with China don’t make the task a straightforward one. But with great challenge comes great opportunity. Through the Government’s multi-billion dollar commitment, strategic technological adoption can transform the entire manufacturing lifecycle, from the supply chain and the factory floor, through to the end users. To reap the full benefits – as an industry and as a country – digital transformation must be industry-wide. That’s the opportunity, and if seized the Australian industry can reclaim its former glory and set new standards in COVID-normal manufacturing.
Vijay Sundaram is the Chief Strategy Officer of Zoho Corporation. www.zoho.com
Coming ashore? Australian manufacturing after COVID-19
In the 1960s, manufacturing accounted for almost 30% of Australia’s GDP; today, the figure is approximately 5.7%. With recent events exposing major risks in the global value chain, the notion of ‘reshoring’ is gaining added impetus, writes John Young.
Last year, Australia’s lack of self-sufficiency and its dependence on China for many key supplies was demonstrated to be a greater problem than many previously assumed. This was true in the pharmaceuticals sector most obviously, but other sectors, such as chemicals and automotive, have felt the impact of an over-reliance on China. In many places, there is serious and often excited discussion about the possibility of reshoring manufacturing. In Australia, talk of this phenomenon certainly predates the current crisis. The pandemic occurred at a time where mounting structural pressures were already reducing the appeal of offshoring. Structural context
Across the Western world, many companies moved their manufacturing capacity offshore, to take advantage of lower labour costs in Asia. The trend began in earnest in the 1970s, was especially prominent in the 1990s, and has continued into the 21st Century. Australia has been impacted by this development more heavily than most. Remarkably, no cars are manufactured in Australia. The closure of Holden’s last plant in 2017 served as a powerful symbol of the decline of the country’s manufacturing. The chief driver of this transformation has been cost. Companies were enticed by the lower wages in many parts of Asia, which placed domestic workers at a severe competitive disadvantage. This reality coincided with a period of relative international stability in the immediate post-Cold War years, seemingly reducing the risk of longer supply chains and an over-reliance on foreign imports. However, the cost benefits of offshoring are less obvious given the emergence of two important structural changes. Firstly, rising prosperity in China is eroding the advantage that low labour costs previously offered. Secondly, the technologies associated with Industry 4.0, including automation, additive manufacturing, and artificial intelligence, are becoming commercially viable in a greater range of applications. According to the World Economic Forum, Australia is a ‘high potential country’ in relation to Industry 4.0, being well placed to take advantage of these technologies. While decision-makers had previously focused exclusively on cost, many of the risks of off-shoring were somewhat overlooked. Concerns about product quality have been foremost among these, but sustainability considerations, risks to intellectual property, and growing consumer preferences for ‘Made in Australia’ are also relevant here. The trigger
Prior to the coronavirus pandemic, evidence of reshoring as a genuine phenomenon was mostly anecdotal. An OECD research paper in 2016, which examined aggregate level data, failed to find evidence that significant onshoring activities were taking place, despite an increase in media interest in the idea. The authors of the report concluded it was a ‘trickle’ rather than a ‘flood’. Experts are clear that there will be no return to a bygone era of largescale manufacturing on Western shores, and offshoring will continue in many cases. A recent scholarly survey of the many contributions to this discussion concluded: “We do not believe that COVID-19 will make … offshoring out of date or change completely the validity of the theoretical lenses that we have used in the last 50 years.” However, the same experts argue that the pandemic demonstrated that the risks of offshoring were higher than many assumed, and that the pandemic would ‘foster and accelerate decisions’. In the structural context of the pressures outlined above, the pandemic could therefore function as a trigger to boardroom decision-making. Many governments are introducing initiatives to encourage this development. In Australia, the Government accelerated depreciation deductions and raised the threshold for tax deduction for capital investments. Present and future prospects
The attractiveness of reshoring clearly varies by market segment. For example, an Australian textile company may have moved production to China and Pakistan for cost reasons. The company was in a market segment where large orders were won or lost on very small differences in price. Reshoring was not a commercially viable option because of the higher cost. In contrast, for an Australian machine tool company that was selling high-tech equipment, reshoring was a more attractive option. The business was selling premium equipment, so in its market segment, cost was not the only consideration. Reshoring was more viable because the quality of the product and the stability of the supply were key considerations for its customers. It is no surprise that those businesses successfully exploiting the onshoring opportunity are geared up to take advantage of automation technologies. Pairing with a reliable automation parts supplier, like EU Automation, is a key part of the preparatory stage of onshoring. One difficulty many manufacturing businesses face is that even where the case for reshoring is strong, the domestic workforce cannot supply the engineering and technical expertise required. A survey in 2018 showed that 21% of Australian manufacturing CEOs highlighted skills shortage as their top concern for coming year. Some companies may stop short of fully onshoring but consider alternative strategies to the traditional offshore approach. One option that is likely to prove popular is near-shoring. We may see manufacturers move their production out of China, only to take advantage of the lower labour costs in developing countries like Vietnam and Indonesia that are closer to home. The fate of Australian manufacturing is also, to some extent, dependent on the fortunes of the dollar. The boom in mining has fueled a significant increase in demand for the country’s currency, making our other sectors’ exports less competitively priced in international markets. Long-term economic and technological trends, combined with the shock of COVID-19, are making a serious dent in the appeal of offshoring. It remains to be seen whether anecdotal reports of reshoring translate into an increase in Australia’s manufacturing base. However, investment in automation and calls in some quarters for a clearer national strategy are positive signs that many more will be coming ashore in the months and years ahead.
John Young is APAC Director at EU Automation. www.euautomation.com
Cyber-attacks – A serious, physical threat to manufacturing plants
A pandemic may seem like an unprecedented risk but it has a lot in common with a much more likely threat: cyberattacks. A serious cyber-attack has the capacity to significantly disrupt, if not entirely stop, a company’s operations across the globe, hitting downstream processes and deliveries to customers. By Pankaj Thareja and Matthew Pilgrim.
Manufacturing businesses are critical to the economy yet are increasingly being targeted by cyber-attackers. Physical damage to equipment and facilities is perhaps the most significant and growing threat manufacturers face from cyber-intrusions. Hackers could take control of machinery and force unsafe conditions like overspeeding, or they could disable the safety systems designed to detect and intervene in these situations. It’s vital that Australian manufacturers get on the front foot with this growing threat. Many manufacturers are becoming technologically sophisticated, implementing more robotics, automation and Industrial Internet of Things (IIoT) , and thereby increasing their attack surface. This is only set to increase as the Federal Government pushes ahead with plans to grow our advanced manufacturing industry. The irony is that within this super-connected IIoT environment, ageing industrial control systems (ICS) control and monitor industrial processes, increasing the vulnerability of operations . ICS, found in operational technology (OT) environments, have historically been separated from an organisation’s main IT systems but are now becoming more integrated. This can create new attack vectors. Furthermore, with a production line under constant operation, upgrading control systems is not straightforward, often involving significant cost and business disruption. It’s not easy to go in and just patch these systems without proper planning, and fixing vulnerabilities may not always be feasible. Also, patches for legacy systems may no longer be available, leaving equipment at risk. OT’s longevity also means it can end up unsupported by manufacturers, making it more susceptible to cyber vulnerabilities. Hackers understand this – they will target the weakest link. Manufacturers can manage cyber risk in a number of ways: Network segmentation is critical. Network segmentation is about building a wall around the crown jewels of your operations, and your weakest links – vulnerable, ageing, operational technology. Appropriate segmentation improves an organisation’s security posture and helps harden the controls network. FM Global recommends the use of firewalls, data diodes and routers for greater control of data flows, as these can act as a layer of protection between your business systems and your ICS. Where possible, set up ‘demilitarised zones’ (DMZ) between the ICS and business IT networks, and direct all communication to and from the ICS through the DMZ to avoid exposures. Employ network monitoring and logging of activities on the ICS network to detect unauthorised activities. Even in well-segmented networks you need to be vigilant about back doors inadvertently created in your system. For example, equipment manufacturers and vendors often remotely extract data from machinery to monitor and optimise it. It’s critical to understand how people and devices connect to your system – including how you allow third parties to connect. Consider how operators access control systems and what your password management practices are – including how often they are updated, how simple they are, and if multiple people share the same usernames and passwords to access important systems. Think about what would happen if someone inserted a rogue USB into one of your computers – whether a malicious actor, or an employee wanting to play music. It’s critical to create and enforce strict policies around connecting external devices. As remote capabilities and increased interconnection between systems become more prevalent, it’s important that organisations keep security front of mind and strike a suitable balance with business enablement. Put time limits on remote connections, revoke remote access for those who are no longer working within the organisation, and apply strict controls like multi-factor authentication for remote network connections. Configuration management is the next step to a higher security posture, ensuring no changes are introduced into your environment that could weaken security. After all, anything that can be configured to protect an environment can also be misconfigured, introducing new vulnerabilities. Appropriate configuration management involves having an ICS oversight team assisting to analyse, validate, and approve all changes to your critical digital environment to reduce vulnerabilities due to misconfiguration or improvised security. This approval process should include all the relevant people – production, maintenance and/or IT – needed to assess the impact of the change on the plant’s security. Physical security is yet another critical component of your cyber strategy and one of the most common deficiencies in the manufacturing sector. While the most insidious threat from a cyberattacker is usually one who will never set foot in your property, creating easy physical access points where a malicious actor could compromise your equipment will lessen the impact of any hardening measures carried out with regard to your network. Consider what security the business has in place at a property’s perimeter, including requiring swipe cards to enter locations where equipment is located, and locking cabinets where critical equipment are kept. No matter how much preparation is undertaken, there’s still a possibility of succumbing to an attack. A key part of your defense strategy should be planning for the worst-case scenario. Recovery can be prolonged and losses exaggerated when people are unprepared. The key is to understand your recovery objectives before things start falling apart, and to build programs to ensure you can maintain or restore operations within those parameters. Among other things, this requires having secure, up-to-date backups of all of those server files and PLC codes. Employees must be clear on what to do in the event of an incident. This includes documented plans on how to detect an attack is happening, how to safely mitigate the damage and spread of malicious software, and how to restore operations as quickly as possible. Resilience is a choice – and cyber risk must be treated like any other risk. Just as a facility could burn down or hit by a cyclone, it could be hit by a cyber-attack and the result could be just as damaging, or worse. Amid a rapidly evolving cyber threat landscape, prevention, mitigation and recovery planning will help manufacturers decrease the likelihood of serious business interruption and losses.
Pankaj Thareja is a Cybersecurity Consultant at FM Global. Matthew Pilgrim is Field Engineer – Manufacturing at FM Global. www.fmglobal.com
Australia: H2X Marine begins construction on hydrogen ferry
Construction is underway on a hydrogen-fuelled passenger ferry in Queensland, with the vessel expected to launch in the first quarter of 2021. It is being developed by H2X Marine, the new boat-building arm of automotive manufacturer H2X Australia, in partnership with ship building specialist WildCat Marine. The two companies will together develop a range of zero emission passenger ferries for industrial and commercial use, driven by hydrogen fuel cell technology. The vessels will comprise an aluminium hull, with 50 passenger capacity and fitted with two 120kW electric power trains driven by green hydrogen. The company is aiming to manufacture up to 30 ferries at its Brisbane factory. “Australia stands at the forefront of the future hydrogen economy: this potential can represent billions of dollars through domestic and export sales whilst locally delivering high value long term stable job opportunities” said CEO Sam Blackadder.
H2 View

Craig Elvin, Chairman of H2X Marine, and Guy Obren, Founder of Wildcat Marine. The user can easily adapt their original concept to create an impressive glass façade fabricable with cold bending.
Australia: Sky's the limit for flying electric car

A full scale prototype of an Australian designed and built electric Vertical Take Off & Landing aircraft (eVTOL) was launched last November to be used by CareFlight in medical emergencies. Named Vertiia and produced by startup AMSL Aero, it is claimed to be the world’s most efficient aircraft of its type in the world for passenger and aeromedical transport. Its unique aerodynamic and structural design means it travels further using less energy. Without the need for a runway, it cruises at 300kph, will travel 250km powered purely by electric batteries and will travel non-stop for 800km+ using hydrogen. Some key advantages are proprietary technology which extends battery life, a light weight and simplified airframe and easy passenger entry and exit. The project is a collaboration between the Uni of Sydney, AMSL Aero and the charity CareFlight and forms part of a $3m grant from the fed. government. Commercial production is expected by 2023.
Vertiia.com/mixed
Austria: Bend, don’t break: New tool for economic glass design
Traditional construction methods for curved glass façades are extremely expensive. Panes are usually made with “hot bending”, where glass is heated and formed using a mould or specialised machines - an energy-intensive process that generates excess waste. Cold-bent glass is a cheaper alternative in which flat panes of glass are bent and fixed to frames at the construction site. However, given the fragility of the material, coming up with a form that is both aesthetically pleasing and manufacturable is extremely challenging. Now, an interactive, data-driven design tool allows architects to do this. The software allows users to interactively manipulate a façade design and receive immediate feedback on the fabricability and aesthetics of the panelisation. The team ran more than a million simulations to build a database of possible curved glass shapes, represented in a CAD format. Then, a deep neural network (DNN) was trained on this data. This DNN precisely predicts one or two possible glass panel shapes for a given quadrangular boundary frame; these can then be used in a façade sketched by an architect.
Institute of Science & Technology, Austria
Australia: Improving fatigue life of aluminium alloys x 25
A world-first study by Monash University engineers has demonstrated improvements in the fatigue life of high-strength aluminium alloys by 25 times. Researchers demonstrated that the poor fatigue performance of high-strength aluminium alloys was because of weak links called PFZs. The team made aluminium alloy microstructures that can heal the weak links while in operation (a form of self-healing). Aluminium alloy’s fatigue properties are notoriously poor compared to steel of similar strength. 80% of all engineering alloy failures are due to fatigue. Using commercially available AA2024, AA6061 and AA7050 aluminium alloys, researchers used the mechanical energy imparted into the materials during the early cycles of fatigue to heal the weak points. This strongly delayed the localisation of plasticity and the initiation of fatigue cracks, and saw enhanced fatigue lives and strengths. This could be applied to other precipitate hardened alloys containing PFZs.
Monash University
USA: Laser-based process to 3D print detailed glass objects
Researchers at the The Optical Society have developed a new laser-based process for 3D printing intricate parts made of glass. Most 3D printing processes build up an object layer by layer, but a new process avoids the limitations by using a laser beam to
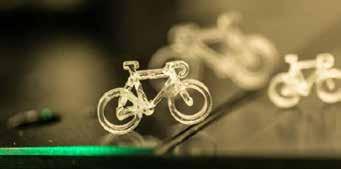
transform – polymerise – a liquid precursor into solid glass. The approach is based on multiphoton polymerisation, which ensures that polymerisation only takes place at the precise laser focal point. It allows direct fabrication of 3D parts that range in size from a few microns to tens of centimetres with a resolution that is theoretically only limited by the optics used for laser beam shaping. The researchers used a mixture containing a photochemical initiator to absorb the laser light, a resin and high concentration of silica nanoparticles. This mixture's high viscosity allows a 3D part to be formed without deformation problems or supports to keep the object in place during 3D printing.
Sciencedaily
Australia/International: A new way to make diamonds
An Australian-led international team has made diamonds in minutes in a lab at room temperature; a process which normally requires many years, huge amounts of pressure and super-hot temperatures. The team, led by the ANU and RMIT University, made two types of diamonds: one found in jewellery and another type called Lonsdaleite (58% harder than regular diamond). The discovery has major implications for diamond manufacturing, because traditional processes are more difficult and expensive. "The twist in the story is how we apply the pressure. As well as very high pressures, we allow the carbon to also experience 'shear'. We think this allows the carbon atoms to move into place and form Lonsdaleite and regular diamond" ANU Prof. Jodie Bradby said. These Lonsdaleite diamonds may become a miner’s best friend if they can reduce the rate of costly drill-bit replacement.
Prof Bradby holding a diamond anvil cell, a device which generates the extreme pressures needed to create ultra-hard materials.
ANU/Business Insider
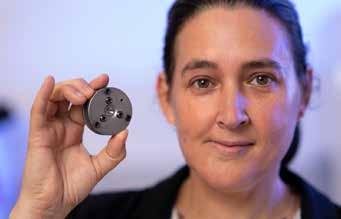
USA: Turning coal powder into graphite in microwave oven
Using copper foil, glass containers and a conventional household microwave oven, researchers have demonstrated that pulverized coal powder can be converted into higher-value nano-graphite. This “one-step method with metal-assisted microwave treatment” is a new approach that could represent a simple and relatively inexpensive coal-conversion technology. While previous research has shown that microwaves can be used to reduce the moisture content of coal and remove sulfur and other minerals, most such methods require specific chemical pretreatment of the coal. In their experiment, the researchers simply ground raw coal into powder. That powder was then placed on copper foil and sealed in glass containers with a gas mixture of argon and hydrogen, before being placed in a conventional microwave oven. The sparks caused by the microwaves generated the high temperatures necessary to transform the coal powder into polycrystalline graphite.
University of Wyoming
USA: 3D print biomedical parts with supersonic speed
A 3D printing technique has been developed that creates cellular metallic materials by smashing together powder particles at supersonic speed. Instead of using only heat as the input for bonding, plastic deformation is being used to bond these powder particles together. AM is not without its challenges. Among them: metallic materials need to be heated at high temperatures that exceed their melting point. To eliminate the resulting problems, a method has been developed using a nozzle of compressed gas to fire titanium alloy particles at a substrate. This method is sixty times faster than direct energy deposition. The team determined a speed just under the titanium alloy particle’s critical velocity. When launched at this slower rate, the particles created a more porous structure - ideal for biomedical applications. While the process is technically termed cold spray, it did involve some heat treatment. Once the particles collided and bonded together, the researchers heated the metal so the components would diffuse into each other and settle like a homogeneous material.
Cornell University
UK/Austria: Spacecraft made from aluminium alloy
A new alloy that will harden aluminium without increasing its weight significantly has been investigated. Compared with other conventional aluminium alloys, the alloy developed was radiation tolerant – ie the hardening phase does not dissolve under high radiation doses. Alloys help aluminium become harder via precipitation strengthening, but the radiation encountered in space can dissolve the hardening precipitates. The research (in partnership with MUL, Austria) discovered that a particular hardening precipitate does not dissolve when bombarded with particle radiation. This process highlights an exciting new field of research called “prototypic space materials for stellar-radiation environments”. The advantages of spacecraft that are light enough to launch and withstand radiation to protect their crews are clear.
University of Huddersfield

The ion accelerator at Huddersfield's MIAMI-2 (Microscope and Ion Accelerator for Materials Investigation) facility.
“Australia stands at the forefront of the future hydrogen economy: this potential can represent billions of dollars through domestic and export sales whilst delivering high-value long-term stable job opportunities.” Sam Blackadder, CEO of H2X Marine, which plans to launch its first hydrogen-fuelled passenger ferry early this year.