
6 minute read
Aerospace & defence push boundaries of metal AM
from AMT FEB/MAR 2021
by AMTIL
Aerospace and defence push boundaries of metal 3D printing
RAM3D, a 3D metal printing service provider based in in Tauranga, New Zealand, works with a large range of clients in the aerospace and defence sectors. Gilly Hawker of RAM3D reports on some of its most interesting projects.
Both aerospace and defence have been early adopters of additive manufacturing, mainly because complex geometries can be achieved that would be difficult to create using traditional manufacturing. Organic shapes, non-uniform sections and hollow areas become possible - leading to a part optimised for function and cost using metal 3D printing. RAM3D’s services include metal 3D printing in stainless steel 15-5ph and 316L, titanium 64, Inconel 718 and aluminium (AISi10Mg), as well as consultation on design for additive manufacturing. Last year, RAM3D printed more than 3,500 parts for spacecraft, while closer to earth it has been working with companies like Oceania Defence and Aeromotors. Oceania Defence – A partnership going from strength to strength
It’s no secret that RAM3D has been working in collaboration with Oceania Defence, a world leader in firearms suppressors since 2012. Oceania Defence relocated its business to RAM3D’s bespoke factory in Tauranga in July 2019, and the business relationship continues to move from strength to strength, with more exciting projects being designed and metal 3D printed for an array of military and police tactical groups throughout the world. Bert Wilson, Managing Director of Oceania Defence, an engineer and long-time shooter, was inspired to design a titanium suppressor once he learnt about the capabilities of the metal 3D printing. Suppressors reduce the noise created when a bullet leaves the barrel of a firearm and allows the shooter to fire the gun multiple times without the need for ear protection. The partnership has allowed both companies to fine-tune suppressor designs to create a range of suppressors in both titanium and Inconel that many defence forces want to use. Oceania Defence’s titanium suppressors are similar in weight to aluminium suppressors but can handle much higher temperatures, meaning multiple shots can be fired without disfiguring the suppressor due to excessive heat. The suppressors are printed as one integral unit from Titanium 64 and Inconel 718 powders, thus reducing any need for spacers, thread assemblies or other support structures. This ensures the tightest manufacturing tolerances possible combined with the lightest, smallest, and efficient devices available to the market. Aeromotors – Revolutionising drone design
Clever drone design takes innovative thinking and people who are willing to take bold steps along the way. Bill White, an aviation propulsion engineer and owner of Aeromotors, is revolutionising drone design for military operations. His journey started more 20 years ago when as a Christchurch engineer, he first started designing and building engines. The smaller three-cylinder engine he has redesigned and built for an unmanned aerial vehicle (UAV) has a weight of 50kg and aircraft wingspan of 6m; it can fly to heights of 5,500m and has a cruise speed of 110 km/hour. In White’s own words: “This little engine is now a yardstick for the rest of the industry to catch up with.” White’s aim is to design and build these engines to be proportionally lighter as all drone manufacturers want their drones to fly higher and further. With White’s extensive experience in developing, manufacturing, and testing engines, he convinced his clients to go with a four-stroke engine design, despite this engine type being
Aeromotors has redesigned and built an engine for unmanned aerial vehicles (UAVs) that can fly to heights of 5,500m and has a cruise speed of 110km/hour.
The parts RAM3D are 3D printing for Aeromotors can’t be manufactured any other way and require high precision.

considered ‘old technology’ in the small UAV world. Most drone engines are electric, while a two-stroke engine is inefficient, so White’s ingenious four-stroke engine is leading the way. The parts RAM3D are 3D printing for him can’t be manufactured any other way; they are printed in Inconel 718 (a high-temperature alloy) and require high precision, especially where mass matters. With rapid prototyping and additive manufacturing this is finally achievable. It was refreshing for the RAM3D team to see some great CAD designs specifically suited for its metal 3D printing process. They have printed production runs of manifolds, exhaust mufflers, collectors, and engine sumps. From prototyping to production
Over the past five years, RAM3D has had to contend with a seismic shift from low-volume prototyping to high-scale production services. To this end the company now operates eight additive manufacturing systems to service many industries – including aerospace and defence. RAM3D has seen an unprecedented increase in both large and smaller companies interested in trying 3D metal printing as an
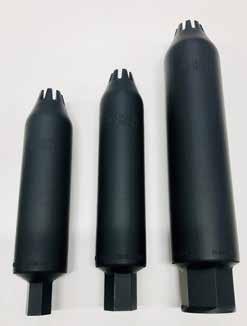
RAM3D has been working in collaboration with Oceania Defence, a world leader in firearms suppressors since 2012.
alternative to other forms of manufacturing. Since the COVIDi19 lockdown in New Zealand, it took on more projects – possibly because designers have had time to work on projects during lockdown. RAM3D’s CEO Warwick Downing comments on what he thinks the future is for metal 3D printing: “Globally speaking, I think the metal 3D printing sector is at a bit of a tipping point right now, and it’s certainly only going to grow in importance and influence. It is no longer a ‘new technology’, it’s here and now.”
www.ram3D.co.nz
Key benefits of additive manufacturing in defence
Customisation of equipment
This is a big drawcard. When designing for metal 3D printing for the military, it is almost like designing for a different kind of elite athlete, and additive manufacturing has the best toolkit to exploit. Not only is this form of manufacturing rapid, but it is also flexible in that products can be altered, and additional features can be added quickly to meet emerging requirements or combat scenarios. This design freedom results in a highly optimised part in terms of both functionality and cost. Lead times, supply chain and parts availability
With additive manufacturing, lead times can be reduced to days, and this shortens the product development cycle. The printing of these parts on demand offers an alternative to keeping a stock of parts. It’s likely that, because of additive manufacturing, inventories will decrease. Reduction in inventory also means agility to process and updates version of a part. The soldier’s heavy load
Military personnel are required to carry heavy loads, and therefore lightweight equipment is an important factor in minimising the mass carried by a soldier. This is easily achieved using additive manufacturing technology. Product development
With additive manufacturing it becomes possible to host trials with actual personnel and that leads to a much better evaluation. It also suits any number of design variations.
MTI PE200 SWING DOORS
The most robust solution for food industry, retail and logistics

The new PE200 HDPE double acting impact traffic door, exclusively available from MTI See-Thru, offers the perfect solution for insulation, functionality and durability.
Benefits of the MTI PE200 Swing Door;
• Made of solid polyethylene – non breakable • Hygienic (EU/FDA approved) • Maintenance-free • Made to measure • Short production time • Easy installation • Long service life • PVC finger protection • 10 year guarantee on door leaves • Stainless steel hinges Trusted by food and retail companies worldwide; • Kraft Foods, Bahrain • Nestlé, Germany • Aldi, Ireland • Lidl , Germany, England • Edeka, Germany • Kaufland, Germany • IKEA, Turkey Contact M.T.I. Qualos today to discuss your industrial door needs.