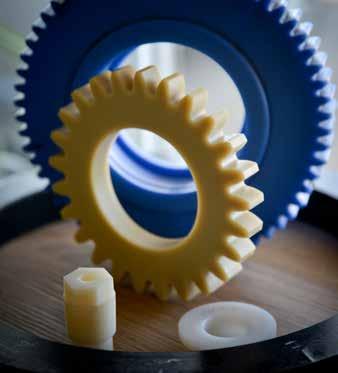
6 minute read
McNeall Plastics advancing tech & exports to the world
from AMT FEB/MAR 2021
by AMTIL
McNeall Plastics hits half-century advancing technology and exports to the world
Celebrating more than 50 years in the plastics industry, McNeall Plastics continues to invest in advanced technology to further enhance its volume capabilities and deliver national and international customers machined and milled components to a consistently high level of precision.
Based in Melrose Park, New South Wales, McNeall Plastics services customers across the broadest range of industries, including mining, energy, pharmaceutical, transport, automotive, packaging, building and construction, bulk handling, foundries and many more. The company continues to looking to the future to expand on its reputation as a leading supplier of high quality engineered plastics. Its latest acquisition is the recently commissioned Okuma Genos L3000-eMYx1000 CNC lathe, along with an OSP-P300LA controller and accessories. The new machine is already enhancing volumes and size capabilities in precision components and will allow the company to produce tooling for casting moulds in-house. “The selection of the Okuma machine was an easy one for us as the name is known throughout the industry as one of the highest precision machine brands available,” says Josh Budd, Managing Director at McNeall Plastics. “And the technical support and training from Okuma is just outstanding.” McNeall Plastics has the only major nylon casting facility in Australia, and has formulated and perfected AUSTLON, a robust hardwearing nylon polymer material that is regarded as unparalleled in performance in the most demanding conditions. AUSTLON is resistant to high impact, abrasion, brittleness, vibration and ultraviolet (UV) deterioration. The product is flexible in design, easily machined and has applications in a variety of areas including the food industry, and mining and quarrying. It has higher mechanical strength than most industrial plastics, and the highest mechanical strength in cast nylons. AUSTANE is another premium grade polyurethane specially formulated by McNeall Plastics, developed for extreme dynamic applications. It is produced by a special hot casting process, either manually or by machine to open moulds, adhering firmly to a variety of base materials. It has unsurpassed mechanical properties; resistance to abrasion and tears; excellent impact resistance; and is lightweight. AUSTANE has a wide range of applications such as materials handling, casters, paper cyclones, blades, screens, chute linings, rollers, crane buffers, valve linings, bridge bearings, process and form rollers, grippers for packaging equipment, and any component made from rubber. McNeall Plastics also produces a wide range of Polyethylene HD, Acetal and Teflon products for machine parts, chain wear strips, chute-and-hopper liners, guide strips, cutting boards and more.
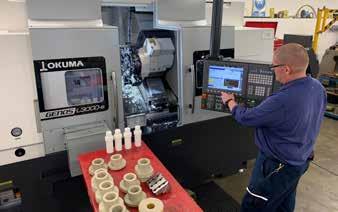
Components manufactured by McNeall Plastics.
With such a diverse range of plastic materials, McNeall Plastics offers its customers a complete consultancy service, drawing on its experienced team of mechanical engineers to provide advice on suitable alternative materials, in a one-stop shop for cut-to-size and fabricated plastic parts. The design service offered by the company involves comprehensive market leading technology including 3D modelling software enabling stress loadings, clearances, tolerances and much more to meet and exceed the application requirements. Comprehensive custom machining by the company includes CNC turning, routing, milling, spindle moulding, grinding, waterjet cutting, laser cutting and stamping. “Today the company is focusing on its ever-expanding Australian and international client base with Australian manufactured highquality products,” says Budd. “It is negating logistic challenges for customers with shorter lead times and fast turnarounds, and again competitively producing components being drawn back from overseas suppliers. “The new Okuma CNC lathe is opening the door to new high and low-volume precision components for the company in areas such as aerospace, defence and medical. And our operators love the machine, with morale through the roof, marvelling at the quality of the finished product.” Okuma Managing Director Dean McCarroll says: “Our leadingedge Okuma machines continue to enhance competitive Australian manufacturing, and it is exciting to witness many products returning to Australia for manufacture due to the expertise and skills here, along with the many logistic advantages that go with local manufacturing. There is strong evidence that McNeall Plastics, like many other Australian manufacturers, are taking products to the world market and winning.”
www.okumaaustralia.com.au www.mcneallplastics.com.au
The latest innovation from Tornos to support its sliding headstock lathe customers is its pneumatic unloading system for the Swiss DT26 machines. The system has been specially conceived to avoid any damage to the particularly intricate or fragile machined workpiece features.
For long and fragile workpieces with delicate features such as a fragile thread, the standard long-part system on the Swiss DT and Swiss GT sliding head machines may not provide the careful handling of the part required by the end-user. For such types of workpieces, with a diameter up to 24mm and a maximum length of 260mm, the Tornos engineers have now designed a solution that enables parts to be removed with particular care. The new solution has been specifically designed on demand by the engineers of Tornos’ development team for specialist tasks. The internal team of experts are always on-hand to develop special solutions to meet the demands of customers, regardless of the machine model. Such solutions are not restricted to sliding head lathes and bar-turning applications but also developed for milling, automation and robot-automated purposes. Designed to unload workpieces without damage to the machined features and to preserve the excellent surface finish achieved by the capabilities of the Swiss DT26 machine, this system can solve various problems related to fragile workpieces. Mounted on the tooling block for back machining, it does not impair the possibility of using the T510 and T520 tools. Ejection is done pneumatically by using clamping jaws adapted to the respective workpiece type and material to ensure there is no harm to the workpiece. The jaws can be manufactured using a 3D printer and can be customised to the workpiece form to be machined, giving endless possibilities. The system is equipped with sensors used to monitor the machine movements and to provide optimum protection of the device and avoids interference with the counter-spindle of the machine. With the addition of this system, a machine can be kept up to date and in conformance with customer component requirements, while employing only minor modifications. Existing machines can be easily retrofitted with this function and the appropriate software functions loaded into the machine control. The system is used in conjunction with the standard parts conveyor belt of the machine but can be supplemented by the addition of a robot for workpiece palletising or even workpiece cleaning and measuring functions. Based on the measured data, it is also possible to update offset values on the machine automatically. The system offers numerous enhancement options for sliding head lathes and Tornos’ other bar turning and milling products.
www.tornos.com
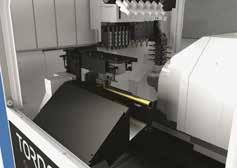



Your Specialist in New CNC Machines, Service & Support
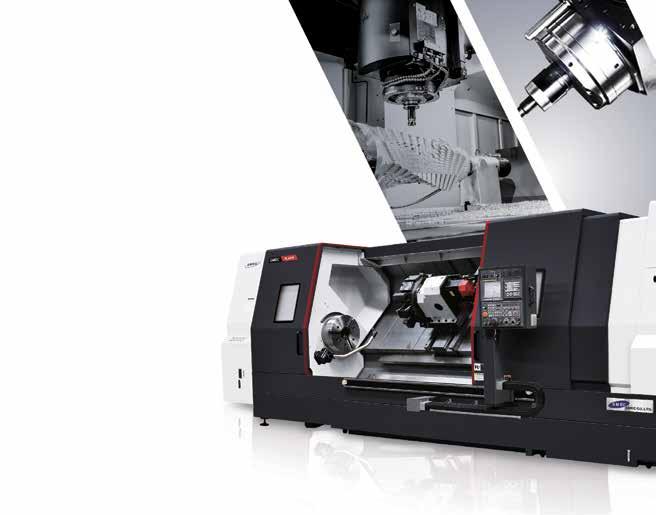
Call us today for a quote 1300 252 262
Proud Partners
I
bjcmachinetools.com.au I BJCMachinetools I BJCMachinetools