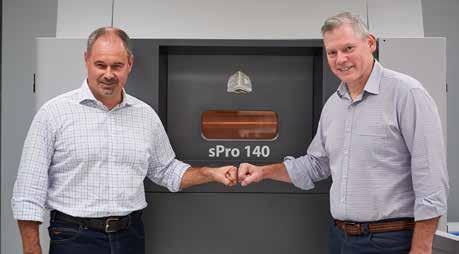
13 minute read
GoProto expands industry presence
from AMT FEB/MAR 2021
by AMTIL
GoProto expands industry presence with new acquisitions
GoProto has become the largest digital manufacturer in the Australian market with the acquisitions of 3D Systems’ Australian facility and WYSIWYG 3D.
GoProto acquired 3D Systems’ Australian on-demand manufacturing facility in Melbourne, the largest digital manufacturing service bureau in the APAC region, on 1 December. Commissioned just two years ago, the state-of-the-art facility houses a full range of 3D Systems productionready 3D printers and a highly experienced management and operations team. This pivotal acquisition will accelerate GoProto’s strategy to become the largest Industry 4.0 player in the Australian market. “This acquisition is a significant leap forward in our growth plans for the region, with an experienced management team that pioneered the introduction of 3D printing into APAC,” says Simon Marriott, Director at GoProto (ANZ) Pty Ltd. “The benefits to our manufacturing customers will be significant as they transition to Industry 4.0 and seek to build agile supply chains that are resilient to global influences.” Earlier in November, GoProto also acquired WYSIWYG 3D, creating a unified laser scanning and 3D entity focused on expansion in the digital manufacturing space. WYSIWYG 3D has been providing 3D scanning services since 2003 and will continue to provide the same quality laser scanning, photogrammetry and 3D CAD modelling service under the GoProto banner in Sydney. Commenting on the development, Shane Rolton, Managing Director at WYSIWYG 3D, said: “We’ve already been working on a number of projects with GoProto. Combining our expertise and resources shortens the time lag between scan data and production, putting ourselves exactly where our customers need us.” By adding this expertise to GoProto’s already expansive service portfolio, the acquisitions enable a streamlined solution for every stage of the product development lifecycle, open up new opportunities for the companies’ combined customer base, and create a firm foundation for further expansion as an Industry 4.0 leader. After receiving the highest ever ranking for an additive manufacturer on the Inc. 500 list of fastest-growing private companies, GoProto has capitalised on this momentum by expanding even further into the digital manufacturing landscape. Further emphasising its global reach, GoProto’s North American facility in San Diego, California, has also installed two new HP 5210 Multi Jet Fusion printers. Adding these two high-productivity 3D printers to its existing six 4200 MJF printers increases GoProto’s production capacity at that location by approximately 50%. With the installation of two new HP 5210 Multi
Left: Simon Marriott, Director of GoProto ANZ, and James Sanders, GM at 3D Systems Asia Pacific.
Jet Fusion 3D printers at the San Diego manufacturing facility, GoProto increases the MJF install base at this location from six HP 4200 MJF printers to a total of eight, and increases production capacity at this site by approximately 50%. With this, GoProto has also upped its build units from 30 to 34, ensuring 24/7 production capability on all eight MultiJet 3D printers. Jesse Lea, President and CEO at GoProto, said: “The current global supply chain structure has shifted during the pandemic. Companies are looking to minimise their risk in procuring production parts. With our business model focusing on Industry 4.0 principles, expansion of capacities for domestic rapid manufacturing with the latest technologies and materials and the complete end-to-end service model, GoProto is ideally situated to help our customers with assurance of supply.”
www.GoProto.com.au
3DM: Rapid post-processing for metal AM
While additive manufacturing is delivering unprecedented speed and flexibility, these gains are often let down by slow post-processing techniques. Australian company 3DM is transforming post-processing in the sector with electroablation technology, enabling the post-processing of parts tens times as quickly and at one tenth of the cost.
Additive manufacturing enables the creation of advanced designs that were never achievable before. These 3D-printed parts often have various surface finish requirements for complex surface geometries and internal passages. As a result, restrictive surface-finishing options have become a significant production bottleneck, consuming valuable time and limiting design freedom. Electro-ablation overcomes the traditional surface finishing limitations, polishing surfaces from 10 micron to 0.5 microns in a little as five minutes, including complex geometries and internal cavities. Electroablation not only polishes surfaces, but removes sharp edges, support-structure contact points, and trapped residual powder. It provides an efficient and effective post-processing solution that is suitable both for single parts and for mass production. 3DM brings together more than 20 years of experience with patented technology to deliver the rapid post-processing solution that the additive manufacturing sector is seeking. 3DM electro-ablation technology overcomes the post-processing bottleneck in the additive manufacturing value chain. Now the company is looking for forward-thinking partners to help it demonstrate how this technology is going to transform additive manufacturing.
www.3dmsurfacefinishing.com
New industrial 3D printing method offers potential benefits for aviation industry
A team of scientists from the Australian Nuclear Science & Technology Organisation (ANSTO) as well as from overseas have discovered how to theoretically avoid cracks and deformations in metal parts created with 3D printers, with potential benefits for the aviation industry.
The team, led by the Linköping University in Sweden, travelled to ANSTO’s Lucas Heights Campus prior to commencement of the COVID-19 pandemic to study how the orientation of the part impacts the additive manufacturing (AM) process. Using ANSTO’s Kowari strain scanner, a scientific, non-destructive technique known as neutron diffraction was used to measure and characterise residual stresses within nickel-based superalloy samples that were produced by selective laser melting (SLM) AM method. Superalloys are an important group of high-temperature metals and are often used in the hottest sections of jet and rocket engines, where temperatures can reach 1,200 to 1400 degrees Celsius. The technique, which allows you to “see inside” a material without damaging it, is used at ANSTO to study materials commonly used in industry. It can reveal information about the structural integrity of pipes, rail and bridge sections, along with many other metal components. The research concluded that the particular direction in which metal parts are physically oriented, will significantly impact the formation of residual stresses, and therefore has the potential to prevent unwanted deformation or cracks in the AM part. When investigating various orientations of printed samples, the team found that for ‘L-shaped’ parts, the horizontal position resulted in the least residual stress. The new findings represent a step forward in controlling the properties of AM parts and could eventually mean savings and more durable engine parts for the aviation industry. Measurements on the Kowari strain scanner provided a better understanding of how the orientation of specific parts contributes to the development of residual stresses during the AM process. This research reveals that in AM, it is very important to look at the orientation of the part – in order to find out which direction is best to build up that particular part during manufacture. When manufacturers are making parts, they cannot see what stresses are building up inside the materials, but this approach enables them to predict stresses beforehand, Neutron scattering confirmed that the predictive models were correct. More work is planned to investigate how different scanning strategies and laser power influence the development of residual stresses. www.ansto.gov.au
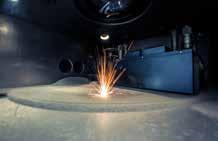
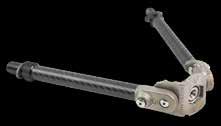
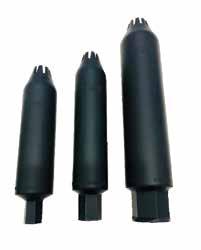
REAL-WORLD PARTS FOR PRODUCTION & PROTOTYPING
RAM3D is a market leader in additive manufacturing focusing on selective laser melting (SLM).
With over 10 years’ experience in the additive manufacturing industry, their services Include:
• Metal 3D printing, consultation on design for additive manufacturing and polishing options. • They print in Stainless Steel 15-5ph and 316L, Titanium 64,
Inconel 718 (high temp alloy) and Aluminium (AlSi10Mg).
They will be introducing maraging steel, a tool steel, in 2021.
GET IN TOUCH
P +64 7 557 0344 E info@ram3d.co.nz ram3dprinting ram3dprinting www.ram3D.co.nz
ViscoTec – Printing a miniaturised soft robotic gripper
The areas of application for soft robotics are still in their infancy, but the potential is promisingly large. As part of an in-house test, the vipro-HEAD 3D print head from ViscoTec was able to print a very small, sophisticated pneumatic actuator – a so-called ‘Soft Gripper’.
Robots are such an integral part of industry these days it is hard to imagine production facilities without them. However, their use requires strict safety measures, especially when they come into contact with people. A new generation of robots drastically minimises the risk of injury and offers other advantages: these new robots are made of a flexible material, such as silicone. The movement of the robot is created by a specific filling and emptying of cavities (often using compressed air or vacuum). An example of a soft robot already used in industry is the so-called pneumatic gripper. These actuators are characterised in particular by their high flexibility in gripping shapes and the non-destructive handling of fragile objects. However, the production of these flexible grippers is a challenge. The complex geometries and the many cavities make injection molding very complex or, in some cases, impossible. This can be remedied by using additive manufacturing and its immense design flexibility. Thanks to the high degree of automation in 3D printing, a change in geometry can be achieved with little effort. This makes the process perfectly suited for researching and testing new gripper concepts. Recently a project of this kind was undertaken at the ViscoTec 3D technical centre. An essential factor in successful printing is the extremely precise processing of the desired material, which is mainly silicone in the case of the Soft Gripper. The vipro-HEAD 3/3 or 5/5 is capable of creating particularly fine structures from silicone – with a layer thickness of 0.2mm. By actively retracting the material, no material drips into unwanted areas and a completely airtight component is achieved. After initial tests it was found that, with the help of the viproHEAD 3/3 or 5/5, pneumatic actuators with very small dimensions

The result of the first tests with the ViscoTec 3D print heads is a pneumatic actuator with very small dimensions.
can be produced: high-precision, additive-manufactured functional components made of silicone. Particularly in the field of medical technology, the application possibilities of the miniature grippers are intensively tested. For example, in the area of minimally invasive medical procedures, the lower risk of injury from soft robots is a significant advantage over tools made of metal. For this reason, medical-grade silicone was also used for the tests at ViscoTec, to meet such requirements.
www.viscotec-asia.com
Additive Manufacturing Hub case study: XROTOR
XROTOR is an Australian company specialising in unmanned aerial vehicles (UAVs) and UAV components for military and government intelligence, surveillance & reconnaissance (ISR) services. XROTOR was involved in a research contract to reduce the acoustic The outcome signature of Australian Defence Force (ADF) UAVs, sponsored by the Defence Science & Technology Group (DST). XROTOR expects to commercialise the intellectual property (IP) developed, develop a Victorian manufacturing capability, and provide an export market for UAV components for recreational, commercial and defence applications. XROTOR engaged the Additive Manufacturing Hub (AM Hub) to identify a suitable additive manufacturing (AM) service bureau. The team was also seeking advice on manufacturing options and identifying suitable materials for specific applications. Ultimately XROTOR surpassed the expected outcomes of the research contract for its client. The AM Hub, the registered service provider and Croft were very helpful in assisting XROTOR achieve this goal. Because of the nature of the engagement, XROTOR’s client and non-disclosure agreements in place, many particulars of the outcome cannot be disclosed. If successful in the outcome for Stage I (currently being assessed by DST and Department of Defence), XROTOR may be invited to proceed to Stage II, which will undertake specific defence use cases and assist XROTOR The solution in commercialising its IP. For XROTOR, the engagement was A number of solutions were employed via registered service provider successful in assisting in low-fidelity testing to deliver the successful GoProto; however none effectively satisfied the required use case. outcome required of XROTOR for its client. A carbonfibre-impregnated nylon material partially delivered low- The AM Hub is an initiative delivered by AMTIL in partnership fidelity results, but XROTOR needed to engage other third parties with the Victorian State Government to provide an industryusing stereolithography (SLA) technologies and the Somos EvoLVe 128 material. driven collaborative network of technology users, suppliers and supporters that will promote the adoption of additive manufacturing technology. For more information, please The total value of XROTOR consumed funds used with the contact John Croft, AM Hub Manager, on 03 9800 3666 or registered provider was $3,693.47 (with a Build It Better (BiB) email amhub@amtil.com.au. voucher contribution of $1,846.74). AM Hub Manager John Croft www.amhub.net.au www.goproto.com.au www.xrotor.com.au also offered advice on options available to XROTOR to achieve the expected outcome.
The Royal Australian Navy (RAN) has installed a WarpSPEE3D metal printer at HMAS Coonawarra in Darwin.
A large-format SPEE3D metal 3D printer certification of parts. The program resulted was installed by the Fleet Support Unit in a range of parts that the Army is now able (FSU) at HMAS Coonawarra Navy Port in to print and finish in the field, at a fraction of late November, making the RAN the latest the cost and time of current supply chains. branch of the Australian Defence Force The pilot program with the RAN is expected (ADF) with the capability to print its own to produce similar results. metal parts, on demand. The installation of a WarpSPEE3D at HMAS Sustainment, or the repair, maintenance Coonawarra was made possible after and overhaul of equipment makes up a the Federal Government made a $1.5m substantial proportion of the costs for all The Royal Australian Navy’s investment in a similar 18-month pilot of the defence forces globally. The difficulty and WarpSPEE3D 3D metal Printer installed capability for the RAN. This world-first trial expense of getting spare parts through at HMAS Coonawarra in Darwin. is designed to streamline the maintenance regular supply chains has been exacerbated of patrol vessels and significantly increase and highlighted by the COVID-19 pandemic. The world has been parts available to the Navy compared to those available from looking to additive manufacturing (AM) to solve this problem; regular supply chains. This technology empowers the Navy to however, most AM technology has proven too delicate, too design and manufacture the parts they require, when and where expensive, and far too slow to solve the problem. SPEE3D has they are needed, whether that be on base or at sea. proven to be the exception. SPEE3D CEO Byron Kennedy said: “We are excited to be working SPEE3D’s metal 3D printing technology was developed in Australia with the Royal Australian Navy on this programme. Having the and is the world’s fastest and most economical metal 3D printing capability to produce high-quality metal parts on-demand, in the technology. It is also the only large format metal 3D printing field or at sea will be ground-breaking for the Australian Defence technology that has been trailed and proven field-deployable by the Force.” ADF. SPEE3D was recently awarded the AIDN-NT Innovation Award SPEE3D recently completed a series of successful field trials 2020 for an outstanding contribution in providing this capability to deploying the WarpSPEE3D printer to the remote outback with the the Department of Defence, and the NT Exporter of The Year 2020 Australian Army. The Federal Government funded the $1.5m trial, and Australian Trusted Trader Technology and Innovation Award which included the training of Army craftsmen and engineers in 3D 2020 in the NT Export and Industry Awards. www.spee3d.com printing at Charles Darwin University in everything from design to
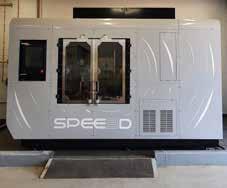

Expert team of Metrologists & Engineers specialising in:
3 Inspection 3 Automation 3 Industry 4.0 3 Quality Control 3 Digital Twin
Supplying Premium Metrology Brands that offer:
• Superior Quality Data • Proven repeatability • Significant reduction in inspection times • Savings to manufacturing costs • User friendly software

Precision Metrology Products & 3D Measurement Services Since 1997
OVER 24 YEARS EXPERIENCE
FREE SOFTWARE
DOWNLOAD