
4 minute read
Akubra Hats humidifies with Condair
from AMT FEB/MAR 2021
by AMTIL
Australian hat manufacturer, Akubra, has recently installed a JetSpray humidification system from Condair to humidify its forming area, creating the ideal air humidity to ensure a perfect finish on the felt during the manufacturing process and provide the long-lasting quality Akubra is known for.
Akubra is an iconic Australian brand, manufacturing classic bush hats made of rabbit fur felt with wide brims that are worn widely across rural Australia and internationally. Founded in 1874 by Benjamin Dunkerley, Akubra is now arguably the world’s greatest fur felt hat-making business. Each hat is handmade, with more than 70 pairs of hands touching each one before it is finished, in a process taking over one month. Akubra hats have been sported by Prince Harry, Crocodile Dundee, the Australian Olympic team and the Australian military. According to Ron Palin, General Manager Operations at Akubra, the key to hat-making is forming the “cone”, and this is done in the forming machine. “The fur is sucked onto a large revolving cone and, as it rotates, hot water is sprayed onto the fur,” he explains. “This interlocks the fibres in each direction. It is critical to maintain the relative humidity at 70% in the forming room to prevent any imperfections in the felt during this process, faults which will only show up later in the finishing process stages.” Akubra engaged Condair to design and supply a low-energy humidification system for installation in the large forming room area. This had to be undertaken with limited disruption to manufacturing and while maintaining the ideal humidity of 70%RH. Condair was chosen because of its proven track record of supplying large industrial humidification projects in Australia and worldwide. The Condair JetSpray system was selected and installed at the manufacturing plant in Kempsey, NSW. The system incorporates 18 nozzles, each capable of introducing 3.5 litres of moisture per hour into the atmosphere. A wall-mounted JetSpray control panel regulates a supply of compressed air and water, which is provided to the nozzle lines. Each nozzle perfectly combines the air and water to release extremely fine aerosols, with droplets of just 7.5 microns that rapidly evaporate into the air. The compressed air prevents any possibility of drips from the nozzles and makes the spray highly directional, thus preventing wetting on machinery, walls or the floor. “The Condair JetSpray is maintaining the ideal humidity of 70%RH in Akubra’s forming room,” says Palin. “This significantly reduces imperfections in the felt, helping to deliver the highest efficiency and quality throughout the hat-making process.”
www.condair-group.com.au www.akubra.com.au
Peerless Products – Innovation in compressed air
Most people wouldn’t give them much thought, but air compressors are heavily relied upon by many consumers in the Australian market.
From inflating your car tyre at your local service station or getting your car washed at the automatic car wash, many everyday tasks make use of compressed air from a type of piston or rotary screw compressor. Even when you get your fast food, the drinks that you get are being filled by compressed air these days. As technology advances in pneumatic equipment so is the technology used to make compressed air. Manufacturers like Peerless Products are always thinking outside the box for creative ideas to generate efficient compressed air while reducing power or fuel consumption. Power consumption is a key point for the Australian market amid fluctuations in voltage supply and rising costs. As advancements in electrical motors and variable speed controllers become more accessible and affordable, manufacturers are taking advantage of this technology. By implementing them in single-phase and three-phase rotary screw compressors, consumers get overall cost savings in the long run for the lifespan of the air compressor. Variable speed drives (VSD) give the consumer greater control of how they use their compressor without wasting air or power. They use the air and power based upon their demands sized to their consumption on application. Compressor manufacturers can confidently tell a workshop, factory, car wash, milking station, production line, packing facility or fast-food chain that it can save up to 35% in energy costs, simply by using VSD technology. Along with this, the user achieves greater air consumption, which is more efficient and cooler by 20%, increasing productivity. Fuel costs are also an ever-growing expense. Peerless Products designed and developed the Under and Over piston air compressor. The Under and Over design is a tube tank frame that utilises the frame as the pressure vessel with no large tank, unlike conventional air compressors. In doing so it offers a very quick pump-up time to 100PSI of 5-7 seconds, and air recovery time of 2-4 seconds. The standard conventional air compressor takes at least 70 seconds on a 60-litre tank to achieve this if it is producing 350 litres of air per minute. The Under and Over design is highly fuel efficient, while offering increased productivity by not waiting for the air tank to reach full pressure. The compact design also gives you more real estate for your service vehicle to be able to carry more essential parts for the job along with reduced overall weight compared to conventional air compressors. Diesel models can have a diesel lift pump fitted to be able to use your vehicle fuel, reducing hazards by not having to manually fuel your air compressor, and offering a further weight reduction by not carrying extra fuel containers.
www.peerlessproducts.com.au

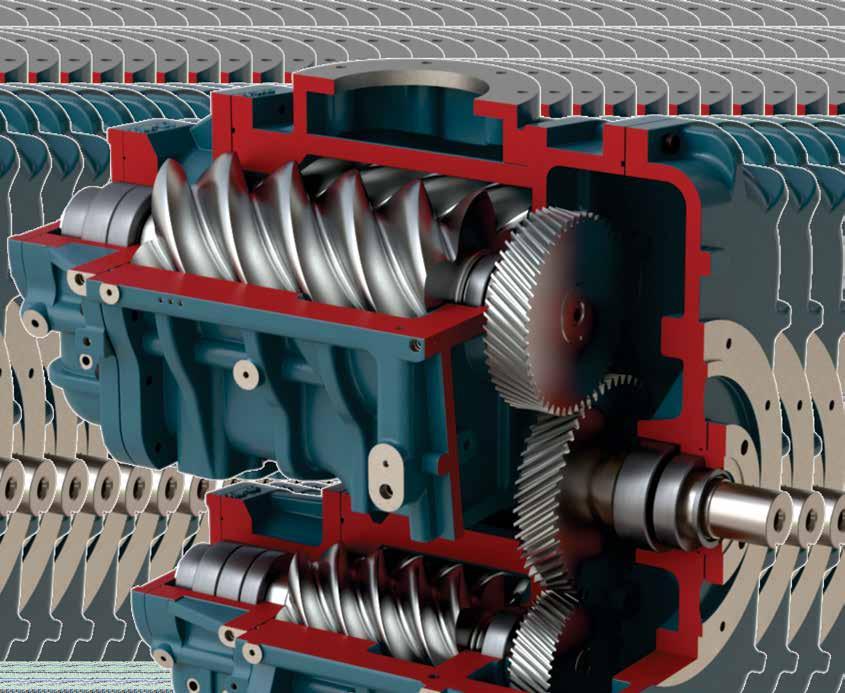
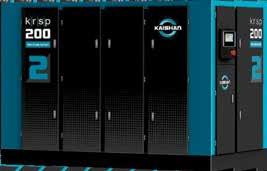