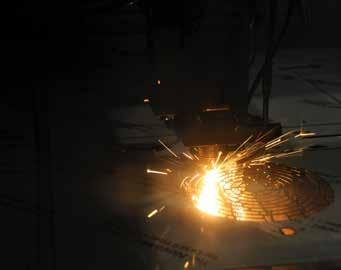
6 minute read
Salvagnini – Cutting with compressed air
from AMT FEB/MAR 2021
by AMTIL
The use of compressed air as an assist gas is one of the most interesting topics in laser cutting today. Salvagnini has been working on the evolution of air cutting for years, and is currently achieving great results with high power density sources. But how signficant is the use of compressed air used in cutting operations?
The first data the team at Salvagnini has available is the percentage of its systems with the ACUT option – where the system and parameters are set up for air cutting – compared to the total number of lasers sold. “If we analyse the data from the last few years, over 90% of laser systems have been supplied with the ACUT option,” explains Pierandrea Bello, Product Manager for laser technologies at Salvagnini. “This is an important figure, but it is not in itself sufficient for understanding how many customers actually cut with air. This is why we use data from LINKS, our Internet of Things (IoT) solution used to monitor system performance in real time and to conduct analyses. “The database consists of a significant sample of our laser systems installed around the world. It includes a wide range of models and different source powers, and concerns annual production: we’re talking about around 1,200,000 sheets.” More than 30% of these sheets were cut with compressed air, and this interesting figure underlines a growing trend. “The second question we asked ourselves relates to thickness,” continues Bello. “Which thicknesses do those who cut with compressed air handle? In the thin and ultra-thin sector, so for thicknesses of less than 2mm, air cutting exceeds 35%. But at 20% of the total, the percentage of mid-range thicknesses, between 3mm and 8mm, is also impressive.” The next step is to investigate the relationship between thickness and material: it is interesting to discover that 40% of sheet metal cut with air is galvanised under 2mm. “After this analysis, we wanted to know which criteria are used for air cutting,” Bello adds. “At Salvagnini, for cutting with compressed air, we use very similar technology to that used for nitrogen. Air is composed of 80% nitrogen and 20% oxygen, and this means that we can use air cutting with technology – parameters, pressure, speed – similar to that used for nitrogen, yet work at lower pressures. This allows us to compare the productivity, quality and costs of the two gases.” For thicknesses up to 5mm, the productivity and cutting speed with compressed air are very similar to that of nitrogen. Today, with the high-power density 6kW source, it is possible to exceed the 5mm threshold. With compressed air, the cutting quality is different from nitrogen, but it is still a valid alternative in very many applications. Even more so with the high-power density 6kW source, which reaches quite considerable cutting speeds and can therefore reduce the quality gap. With regard to costs, on the other hand, cutting with compressed air is cheaper than with nitrogen. This is even truer if we consider the increasing cost per cubic metre of nitrogen, which varies from country to country, and even from region to region . The higher the cost of nitrogen, the more costeffective cutting with compressed air becomes. “With the high-power density 6kW source, we have been able to increase the maximum thicknesses that can be cut with air, up to 10mm,” Bello continues. “But how much are productivity, quality and costs affected by the increase in thickness? What happens when we go above 5mm?” Generally speaking, the maximum cutting speed with nitrogen is higher, in some cases significantly so. When cutting with nitrogen, productivity is consequently higher. There is one exception to this: stainless steel. On a thickness of 8mm, the speed is the same, and on 10mm, air cutting is in fact quicker. To assess quality, the team at Salvagnini cut three materials with both air and nitrogen: 6mm thick aluminium, 8mm thick mild steel and 10mm thick stainless steel. For the 6mm aluminium the quality is similar: there is no oxidation, the cut is white and almost indistinguishable, and the burr – typical of aluminium – is light and present on both samples. The 8mm mild steel cut with nitrogen has a white edge, while the cut with compressed air is darker: there is less burr and the process is simpler and improved by the absence of calamine. Finally, the differences for 10mm stainless steel are quite clear: the cut with nitrogen is white, whereas the cut with compressed air is burnished. Finally, when assessing the costs, it’s first necessary to stress that this depends heavily on the cost of nitrogen. Let’s imagine cutting a part like the one used to compare quality, using both compressed air and nitrogen – in a market where the cost of nitrogen is €0.2 per cubic metre, a low cost but common in highly industrialised areas. In these conditions, cutting with compressed air is costeffective for stainless steel and mild steel, on thicknesses of up to 10mm. If nitrogen costs more, for example €0.5 per cubic metre, things change: for stainless steel and mild steel the cost/part is even more advantageous, but air cutting becomes advantageous for aluminium too. “Let me say a few things about 10mm thick mild steel,” Bello notes. “This thickness is generally handled with oxygen, so we compared the cost/part of oxygen with that of compressed air: the result is that, for these thicknesses, cutting with air is cheaper than with oxygen. “In this context, we really must mention the new APM option,” adds Bello. “This is a compact, turnkey system for cutting with compressed air. Connected directly to the factory pneumatic supply or a compressor upstream of the system, APM normalises the pressure, filtering and drying values of the compressed air, optimising it for air cutting. Connected to the factory supply, there are no costs for dedicated compressors.” The final step is a profitability analysis, again comparing the cost of cutting with nitrogen with that of cutting with compressed air – and again using an actual production mix taken from the LINKS data. While for nitrogen three different scenarios were considered, with the gas costing respectively €0.2, €0.5 and €0.8 per cubic metre, for air cutting the team also also considered the investment required to purchase the APM option as well as the variable costs – i.e. an air production cost of €0.045 per cubic metre.
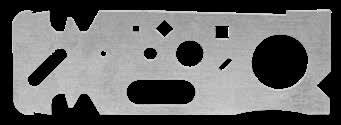
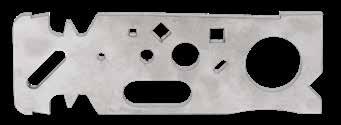
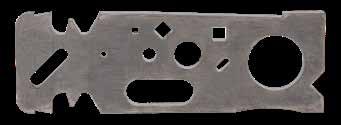
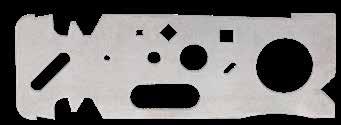

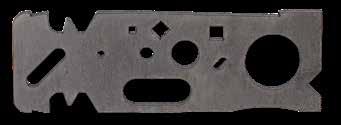
Samples of (from top) aluminium, stainless steel and mild steel cut with N2. The same metals cut with compressed air.
“Air cutting is the only cost that decreases in proportion to the increase in hours of system usage, with the hourly cost dropping from €2.70 to around €2. On the other hand, the hourly cost of nitrogen is constant: depending on the industrial context, this may be between €6.66 and €26.63 per hour. Considering a typical situation, with two shifts and nitrogen costing €0.2 per cubic metre, the return on investment for the ACUT and APM options is around nine months. After this, savings of around €4 per hour on gas can be achieved,” Bello concludes.
www.salvagninigroup.com www.machineryforum.com.au

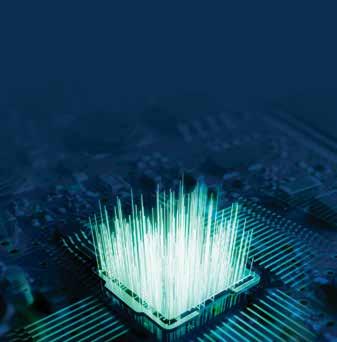