
6 minute read
Sandvik: The next step to unmanned production
from AMT AUG/SEPT 2021
by AMTIL
The next step to unmanned production
A recent study by China’s Beihang University in the International Journal of Production Research directly linked predictive maintenance with the quality of products. But how can manufacturers combine predictiveness and excellence in steel turning operations with fewer workers on the shop floor, or even unmanned production? Rolf Olofsson, Product Manager at Sandvik Coromant, explains why the right tooling, plus fail-safe processes, are essential for component quality.
While Beihang University’s research highlights “the strong relationship among maintenance strategy, production planning and quality”, Sandvik Coromant is seeing a growing trend where machine tool manufacturers are incorporating process monitoring systems within modern CNC machines. The recent Digital Factories 2020 report by Pricewaterhouse Coopers (PwC) recommends that “Companies must make smarter decisions using predictive analytics and machine learning”, while 98% of manufacturers surveyed in the report said they expect to increase their efficiency through use of predictive maintenance. Meanwhile, the global production monitoring market is expected to grow from $4.0bn in 2018 to $6.4bn by 2023, at a compound annual growth rate (CAGR) of 9.8%, according to Markets and Markets. In line with these trends, predictability has also become increasingly important in the modern turning of steel components. This coincides with increasingly limited human supervision in light of new requirements for social distancing in factories. It’s clear that unmanned production is the way forward – but this cannot be achieved without the ability to detect tool wear and avoid sudden breakages. Without human input
Frequent insert changes, production interruptions and not finding the right insert for each application or material are all time-killers in modern production. Several factors can stop manufacturers of steel components from reaching the desired number of workpieces per shift – not least the wear-resistant properties of the tool. This particularly applies in the ISO P15 and P25 application area. ISO P15 and P25 refer to the demands that different working conditions impose on machining parameters. They include cutting data, surface finish, depth of cut, machined or rough surfaces and continuous or interrupted cuts. It’s in this application area that carbide inserts with superior wear resistance are vital for supporting unmanned, or even lights-out, production. But what do we mean by wear resistance? There are different types. For instance, fracture resistance is paramount, as is a cutting edge capable of resisting plastic deformation induced by extreme temperatures. Also, the insert coating must be able to prevent flank wear, crater wear and edge build-up. Crucially, the coating must also adhere to the substrate. If the coating fails to stick, the substrate is exposed and this can lead to rapid failure. To avoid these wear phenomena, the key is to limit continuous, controllable wear and eliminate discontinuous, uncontrollable wear. This isn’t easy, given the current trend for machining with limited, or no, human supervision – but several technologies can be advantageous. Predictive and preventative maintenance are often talked about, like intelligent software and sensors that can be the ‘virtual eyes and ears’ of a machine and support with optimal recommendations to match deteriorating tool performance. So, we can achieve better wear through sensors – but what about through better tooling? Avoiding breakages
When choosing a better-performing insert, the ideal grade is one that limits the development of wear and, in some operations, prevents it from developing at all. Predictable wear is especially useful for unmanned and lights-out production. To achieve minimal wear, it’s vital to select the right carbide insert that can deliver consistent and predictable performance. This is why Sandvik Coromant has launched a pair of new ISO P-turning carbide grades in its range, GC4415 and GC4425, which are each designed to deliver improved wear resistance, heat resistance and toughness. In particular, both grades are ideal for use with low-alloyed and unalloyed steel. They can machine a larger number of workpieces and contribute towards extended tool life – in both mass and batch production setups. The GC4415 and GC4425 grades – which, as the names suggest, refer to P15 and P25 – each contain the second-generation Inveio technology. Inveio is a uni-directional crystal orientation in the alumina coating layer, with unique properties that can be seen by examining the material at a microscopic level. Every crystal in the alumina coating is linedup in the same direction, which creates a strong barrier towards the cutting zone. The crystal orientation has been improved substantially in the second-generation Inveio coating. This gives the insert even higher wear resistance and longer tool life – and can support with predictable wear. Aligned goals
GC4415 and GC4425 have already delivered impressive benefits for Sandvik Coromant’s customers. In fact, when compared to a competitor’s insert, the GC4425 achieved an increased tool life for 270 pieces, compared to 150 pieces. Another comparison test was performed by a general engineering customer in the US, measuring the performance of GC4415 against a competing carbide insert. Both inserts were used for batch-production turning and finishing processes on a 330HB steel workpiece, and the tool was changed when it exhibited a bad surface finish. Emulsion coolant was used in each case.
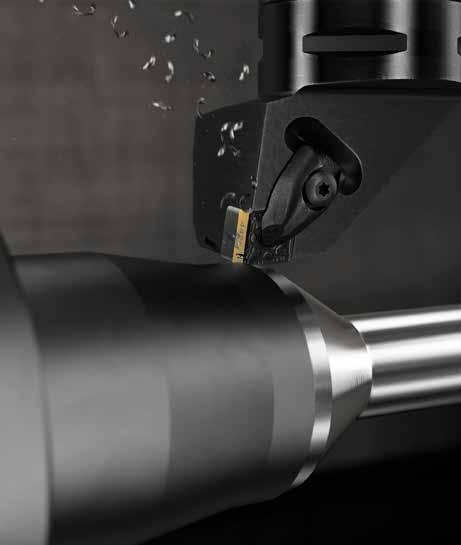
The end results were clear. With the GC4415 insert, the customer was able to almost double its cutting data parameters. This included a cutting speed (vc) of 280 metres/min with the GC4415 versus 200 metres/min with the competing tool; and a feed rate (fn) of 0.15mm/rev versus 0.1mm/ rev. The customer was able to significantly increase its tool life and productivity. Overall, the Sandvik Coromant GC4415 insert with Inveio technology produced twice the number of pieces, a total of 80, before showing signs of wear, against just 40 pieces with the other tool. This equates to a 100% productivity increase and twice the insert tool life. Enhanced by digital
Aside from enhanced tooling with the GC4415 and GC4425 grade inserts, Sandvik Coromant has also advanced its digitalisation offering. To do so, its specialists worked closely with machine tool builders, cloud suppliers and network companies to develop its CoroPlus, a digital platform of connected tools and software. The software reflects how times have changed. It used to be the case that operators had to rely on experience and instinct to improve processes, and detect wear in tools. Today, with the use of sensorequipped tools, production managers can adjust, control and monitor their machining performance automatically in real-time. The CoroPlus platform already has already proven valuable in monitoring and controlling sensor-equipped tools. The platform helps to optimise processes by eliminating the aforementioned ‘timekillers’ of modern production, minimising the number of production stops needed to replace worn tooling – including carbide turning inserts – and reducing waste. Moreover, in combination with the GC4415 and GC4425 grade inserts, or other enhanced Sandvik Coromant tools, CoroPlus is integral to supporting predictive maintenance. It is through a combination of the right software systems that manufacturers can predictively detect tool wear and avoid sudden breakages. This not only opens the benefits of unmanned production – increased process security, reduced downtime and protected investments. It does so in ways that, as in Beihang University’s study, links predictive maintenance directly to consistent product quality.
www.sandvik.coromant.com
The portable, affordable solution to improve quality, reduce scrap, and increase the productivity of any workshop.
The Master3DGage from Verisurf Software is a versatile 3D measuring CMM ideal for shop-floor measurements and use in the workshop.
The system is both easy to use and produces accurate and repeatable results when coupled with Verisurf CAD/Measure inspection software for inspection and reverse engineering tasks. A complimentary 3D laser scanner is available for the Master3DGage, making this one of the lowest entry-cost laser scanning systems available on the market.
For full sales, support, installation and training of all your metrology needs contact Met Optix:
1300 363 409
info@metoptix.com.au www.metoptix.com.au