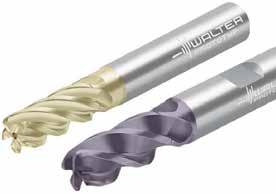
20 minute read
PRODUCT NEWS: Selection of new and interesting products
from AMT OCT/NOV 2021
by AMTIL
Walter: Tools for titanium with twice the expertise
Walter has launched its MD377 Supreme and MC377 Advance solid carbide milling cutters, designed for the effective machining of titanium.
Incorporating a corner radius and central through coolant supply, the new MD377 utilises Walter’s proven HPC Ti40 titanium geometry and new WTZ coating that makes it perfect for full slotting up to 1XD, ramping, shoulder milling and plunging. Also, the MD377 Supreme is suitable for dynamic milling processes. In comparison, the MC377 has a centre-cutting geometry without the through-coolant supply. The MD377 Supreme has been developed for the aviation and aerospace industry and is therefore precisely matched to its requirements. The titanium specialist with a central coolant supply represents a benchmark when it comes to machining engine and structural components. It allows for tight tolerance machining and it stands out thanks to its extremely high metal removal rates. This high material removal rate is a credit to the optimised cutting geometry and the five cutting edges that can improve productivity levels and reduce vibration credit to its differential pitch design. The MD377 Supreme is available with a range of corner radii in diameters of 6mm, 8mm, 10mm, 12mm, 16mm, 20m and 25mm with a flute length of 13mm on the 6mm diameter tool ranging up to 45mm on the 25mm tool with each tool designed with a back radius into a necked diameter for clearance when machining deep cavities. In contrast, the MC377 is a four-flute titanium end mill that is also suitable for ISO P and M material designations. This diversity is credit to a tough AlCrN coating that works with Walter’s WK40EA substrate that makes the MC377 suitable for steel, stainless as well as titanium alloys. With regard to the MD377, the tool life and performance is assured with the latest Walter-exclusive AlTiN+ZrN (WTZ) coating with HIPIMS technology. The impressive new MC377 end mill without corner radii is available in diameters of 2mm, 3mm, 4mm, 5mm, 6mm, 8mm, 10mm and 12mm, whilst the MC377 with corner radii is offered with a 2mm, 3mm, 4mm, 5mm, 6mm, 8mm, 10mm, 12mm, 16mm, 20mm and 25mm diameter, with the 2mm tool having a three-flute geometry and all other diameters having four flutes. Depending upon the tool diameter, each MC377 tool is available with a choice of corner radii from 0.2mm to 4mm. The series has a flute length that ranges from 6mm on the 2mm diameter tool through to 45mm on the 25mm diameter tool. The MC377 cutter range is also designed with the back radius into a necked diameter feature for clearance. Both tools are the perfect partners for the machining of small parts, engine components or structural components as well as additively manufactured components in the aerospace, motor sport and medical technology sectors. From a process security perspective, both the MC377 and MD377 are available with plain cylindrical shank across all diameters, but from 16mm to 25mm diameter there is also the option of a cylindrical shank with clamping flat to DIN6535 HB to prevent tool pull out and increase stability. In addition to the standard ranges with cutting lengths up to 2XD, Walter also offers custom-designed tools via the Xpress service with short delivery times. www.walter-tools.com
ADDE brings OTTO Motors autonomous mobile robots to Australia
Melbourne-based automation system builder Andrew Donald Design Engineering (ADDE) has partnered with OTTO Motors to bring the OTTO range of autonomous mobile robots (AMRs) to the Australian market.
OTTO Motors, a division of Clearpath Robotics, develops market-leading AMRs that enhance the logistical operations of facilities in order to reallocate valuable manpower to more specialised tasks. These mobile robot platforms are designed to withstand the day-to-day rigors of industrial environments while maintaining the safety of the human operators around them. OTTO AMRs are being used by Fortune 500 manufacturing companies to deliver cost reductions and operational efficiencies. ADDE has extensive experience developing automation solutions for the Australian industry with robotics and custom engineered solutions. “We see enormous opportunity to improve efficiency and safety in manufacturing and distribution operations with autonomous vehicles,” said Barry Hendy, ADDE Managing Director. “Like traditional robots, AMRs require a complete solution design and tight integration with existing equipment, workflows and data systems. The OTTO range of vehicles and the supervising Fleet Manager system give us a powerful capability to offer turnkey solutions to our clients.” John Stikes, Director – Strategic Alliances at OTTO Motors, added: “As we have deployed our systems around the world we have always looked to partner with experienced local integrators to ensure every deployment can be seamlessly and fully integrated into the client’s facility. We are excited to now be able to offer our vehicles to the Australian market through ADDE.” The OTTO motors range spans from the 100kg-capacity, smallfootprint OTTO 100, to the heavy-duty 1,500kg-capable, palletsized OTTO 1500. For multi-vehicle application the OTTO Fleet Manager provides the integration, overview control, traffic flow and vehicle management to allocate missions to appropriate vehicles. www.adde.com.au
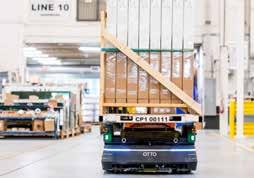
MAQ – Self-tuning boring bars reduce vibration
Minimising vibration during machining operations has a number of advantages, including improved surface finish, reduction of scrap parts, increased cutting insert life and improved production costs.
Vibration issues are often present in machining operations where there is a high length-to-diameter ratio or if the machine tool itself is aging. The challenge for “mass-dampened tools” is the change of the vibration frequency on machining tools due to change in the cutting conditions such as tool wear, condition of the machines moving parts, and the variation of work piece materials. For these reasons traditional mass-dampened tools require the tuning of the mass damper to optimise performance. An out-of-tune condition can make the vibration problem worse in the form of tool chatter, which is often solved by reducing cutting speed or depth of cut, or increasing feed per revolution. The team at MAQ in Sweden studied the effects of vibration on the machining process and in 2015 developed a method of measuring a polymer’s frequency-dependent stiffness. They found that some polymers exhibited an increase in stiffness where there was an increased frequency, and it is the results of this study that were incorporated into the development of MAG’s STMD series of toolholders. The STMD (Self Tuning Mass Dampener) series boring bars from MAQ use a different approach where the mass dampener in the toolholder body will automatically adjust its stiffness as in relation to the vibration frequency of the machine tool. Inside the tool is a tungsten mass that is completely dry; this is supported by polymer discs that react to changes in vibration and change the stiffness of the tool; this response maximises the dampening effect. STMD toolholders are designed to be “plug and play” – no tuning is required, and one holder can be used for more than one application. As the tool is self-tuning it adjusts to the vibrations that are causing tool chatter, allowing an increase in speed and feed with improved surface finish. All MAQ vibration damped turning tools have the self-tuning mass damper technology inside and cover lengths from 3xD to 15xD. Starting from 10mm in diameter up to 60mm in diameter. Some of the boring bars in the range have an interchangeable cutter, the user can choose the cutter head to suit different insert shapes. MAQ is also developing a range of adaptors that incorporate the same self-tuning dampening technology to reduce vibration during milling operations. www.whitelawtooling.com.au

LinX tubular linear motors: Superior alternative to pneumatics, ball screw and flatbed
Modular, flexible and highly dynamic, the LinX range of tubular linear motors from ANCA Motion delivers improved performance even in harsh environments.
Applications such as packaging, labelling, sorting, and pick and place require robust and efficient actuation methods. Significant compromises are made by machine makers on linear actuation mechanisms used under harsh conditions. This is where the LinX M-Series Linear Motor from ANCA Motion stands out as a lucrative solution offering better outcomes. LinX with its fully potted body and cylindrical design achieves higher IP ratings than conventional flatbed linear motors and rotary motors, and enables system integrators and original equipment manufacturers to target applications that were previously not on their radar. The ability to achieve high speed and acceleration, the flexibility offered by its modular structure, and its higher IP rating make LinX an ideal choice for material handling applications within factory automation such as warehousing. Thanks to its cylindrical design and direct drive nature, LinX motors do not wear on railings, significantly improving machine lifetime and drastically reducing maintenance costs. Larger spacing between the magnets and the machine base ensures that safety of operators is never compromised. The LinX range is designed to allow easy replacement of ball screw and pneumatic cylinders in existing machine designs. Elan Anbanandam, Automation Product Manager at ANCA Motion, said: “Our cylindrical motors are highly dynamic with integrated position feedback giving absolute accuracy to ±0.5mm and resolution of 10μm. Their pneumatic retrofit-friendly mounting, direct drive nature, higher IP rating and the ability to achieve velocities of up to 10m per second make LinX M-Series motors suitable for a multitude of applications.” ANCA Motion is an Australian developer and manufacturer of motion control systems, hardware, and software including for its sister company ANCA CNC Machines. ANCA has used LinX tubular linear motors for its globally renowned tool and cutter grinders since 2014. As experts in motion control, ANCA Motion’s local team provide bespoke solutions for custom needs. A world-leading supplier of flexible motion controls, ANCA Motion also offers a range of other automation products such as human machine interfaces, servo motors and servo drives. www.ancamotion.com

The heavy-duty M450 portable compressor from Kaeser has been especially developed to deliver unwavering performance under extreme environmental conditions.
The largest portable compressor in the Mobilair series, it assures a dependable supply of quality compressed air no matter whether in the desert or in the cold. This versatile portable compressor offers a maximum available flow rate of 48.1 cubic metres per minute and adjustable pressure between 6 and 14 bar. In addition, it also provides exceptional power and versatility. Beneath the hood is an electronically-controlled MTU engine with an output of 2,360kW. In combination with a premium efficiency compressor block – featuring the flow-optimised Sigma Profile rotors – and the energy-saving fan installed as standard, it ensures exceptionally economical diesel consumption. Thanks to the innovative pV control, the operator only has to choose between two pressure levels. The set pressure 'p' directly influences the maximum flow rate 'V'. One and the same system can therefore deliver pressures between 6 and 14 bar. For applications requiring 7 bar, a version delivering up to 8.6 bar is available, for example, with a powerful flow rate of 48.1 cubic metres per minute. Operation could not be simpler, as the M450 uses the proven Sigma Control Smart controller, which also indicates when the next scheduled maintenance is due. Following the push-button start, the system runs in unloaded state to ensure a safe cold start in all situations. The display shows the end of the warmup phase and the system can then be switched to load operation to generate compressed air. Pressure adjustment is also straightforward. Depending on the application, the system can be equipped with a compressed air aftercooler, or with a microfilter combination for technically oil-free compressed air. With environmental protection in mind, accumulating condensate does not drip out of the system, but is evaporated via the hot exhaust gases. The M450 is optionally available on a construction site chassis with a steering axle and parking brake, or as a stationary version with skids. The system is equipped as standard with an integrated forklift guide and lifting eyes for ease of transport, which can be safely accessed using climbing aids.
www.kaeser.com.au

Konica Minolta announces availability of MiR250 mobile industrial robots
Konica Minolta Australia has announced the availability of the MiR250 through its partner Mobile Industrial Robots (MiR), a leading manufacturer of collaborative mobile robots that increase efficiency and drive productivity.
The MiR250 is a more flexible autonomous mobile robot (AMR) that can work around the clock and is simple to set up for improved productivity. With a smaller footprint and increased adaptability, it can help optimise internal logistics without changing layout in industries such as manufacturing, fastmoving consumer goods (FMCGs), and defence. The MiR250 has a footprint of 580mm by 800mm and is only 30cm high. It can move up to 250kg at speeds of 2m per second. The MiR250 is more agile than any other AMR on the market and highly adaptable for challenging environments. According to the SafeWork Australia website, forklift and cranes accounted for 15% of fatalities in 2019, above the average of 11% over the past five years. Martin Keetels, National Manager – Robotics & Innovation at Konica Minolta, said: “The MiR250 eliminates risk around forklift operations and is one of the safest autonomous mobile robots on the market designed according to current applicable safety standards. The latest scanning technology with a 360-degree view means there are no blind spots so it can navigate safely around other objects and humans.” The MiR250 has a fast charge of zero to 80% in one hour with an operating time of 13 hours at full charge. As a critical piece of infrastructure, it has the ability for a fast battery swap to support 24/7 operation. This means production flow remains uninterrupted with no downtime. Top modules can also be mounted on the MiR250 for a complete solution to tow carts and shelves and lift and transport shelves. The MiR250 signals with light and sounds to demonstrate its status. The LED light band indicates its current operational state such as emergency stop, mission paused, path blocked, or mapping. The MiR250 also has signal lights that work similarly to lights used on cars; white at the front, red at the back, and indicating a left or right turn by blinking. Signal lights suggest the immediate motion plans by signalling forwards, backwards, braking, and left and right turns. Keetels added: “Konica Minolta is excited to bring innovation to highly dynamic manufacturing and logistics environments by safely and cost-effectively automating the movement of materials. Humans move thousands of carts manually around the factory floor, a highly repetitive and time-consuming task. This solution frees up workers for other critical tasks and significantly improves safety.” www.konicaminolta.com.au
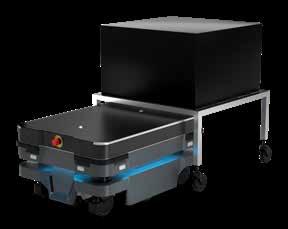
Guhring: New drills deepen productivity gains
The productivity of deep hole drilling has taken a step forward according to Guhring, with the arrival of its new fourfluted series of gun drills.
The new VB 80 four-fluted deep hole drills with a solid carbide head and the solid carbide VB 100 Series are ideal productivity partners for cast iron drilling. The straight flute deep hole drills are extremely robust with a geometry that ensures the drill core is more than 50% of the overall diameter, demonstrating maximum rigidity, strength and performance. Guhring has also developed an innovative geometry that consists of two core cutting edges that are supported by four outer flutes that are axially displaced to split the chips, improve centring and precision while reducing cutting forces. This means the bottom of the hole will be two-stepped, as the drill has a 141-degree angle on the primary cutting edge, which is followed by a 145-degree cutting angle on the outer cutting edges. The chip clearance is further improved by four cooling channels that allow high-pressure coolant to be directed to each of the four cutting edges – prolonging tool life by preventing swarf re-cutting and creating an efficient chip removal sequence. The new VB 80 and VB 100 deep hole drills also consist of four round margins with a 90-degree division that further enhances precision, concentricity and surface finishes down to IT6. With the abrasive wear divided through four flutes as opposed to two, as in most ranges, the new VB 80 and VB 100 have proven to improve tool life and performance significantly. In fact, the new deep hole drills have reduced cycle times by more than 30% during field tests whilst also extending tool life, hole quality and overall performance far beyond the realms of two-flute gun drill variants. At present, the new VB 80 and VB 100 Series is available in diameters from 13.5mm to 28mm diameter with flute lengths up to 500mm. Additional diameters and lengths can be specified upon request. The new drills can be reground from five to ten times depending upon the axial wear on the drills. This regrinding facility drastically reduces cutting tool costs for the end-user with the drills being returned in a perfect ‘as-new’ condition. At present, the VB 80 and VB 100 are new product lines and Guhring is working tirelessly to develop an extended range of drill diameter and length options whilst trialling the exciting new drills on a host of additional materials, an exercise that will undoubtedly create huge productivity enhancements for manufacturers. www.guhring.com.au
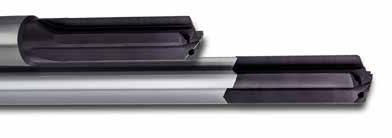
Hyster UT Series: Raising comfort, lowering cost
A new range of the Hyster UT Series is being introduced to Australia to provide enhanced driver comfort and a low total cost of ownership for the forklift operator.
The new H4.0-5.0UT internal combustion counterbalance pneumatic tyre forklifts, with lift capacities from 4,000-5,000kg, complement the broader range of Hyster UT Series forklifts in providing costeffective performance for everyday materials handling tasks. “The H4.0-5.0UT range features the toughness and backup Hyster is known for globally, but without any advanced functionalities that aren’t required for less frequently used forklifts, meaning total cost of ownership is kept low,” says Mark Chaffey, Area Business Director, Pacific at Hyster. “Industries that may sometimes require less frequent use forklifts – such as food & beverage, frozen produce, manufacturing, distribution and truck & transport – do need a quality forklift with outstanding sales and service backup. The Hyster H4.05.0UT range delivers an ideal solution to less frequent materials handling needs, without compromising on performance.” The new H4.0-5.0UT forklifts – in 4,000kg, 4,500kg or 5,000kg models – have a number of features to further enhance driver comfort, visibility and ease of operation, including: • A small diameter steering wheel with adjustable steer column.
The 300mm steering wheel is easy to manipulate, responsive, with optimum manoeuvrability when working confined spaces.
The ideally positioned steering wheel allows eight degrees of tilt adjustment, to suit a variety of different operators. • A high-strength profiled steel overhead guard to provide enhanced reliability and operator protection. • Excellent through-mast visibility of the load and the operator’s forward field of view, optimising comfort, safety and productivity. • A large access area for service and repairs, including large access space to the engine compartment to minimise downtime when servicing the forklift. • A suspension seat for excellent comfort. • Exchangeable components, including overlaps with other forklifts in the same range, which further optimises maintenance and spare parts inventories. • Improved lift speed, which enables higher productivity. The new machines’ value proposition – “Meets the Need. Makes the Move” – relates to customers who don’t need advanced functionality features, but prefer proven materials handling solutions. The use of high-quality, robust components, efficient filtration and excellent cooling helps contribute to reliable operations and lower wear and tear. This, together with fast availability of cost-effective replacement parts, reduces maintenance requirements and costs.
www.hyster-yale.com
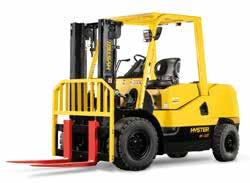
DISCOVER WHAT AN OMAX ABRASIVE WATERJET CAN DO!
OMAX Waterjets streamline operations by reducing your need for multiple machines, secondary processes and extensive employee training. OMAX Waterjets are the perfect complement to your shop. The flexible tool cuts like a saw, machines like a lathe, contours like a mill and shapes like a wire EDM.
Learn more today.
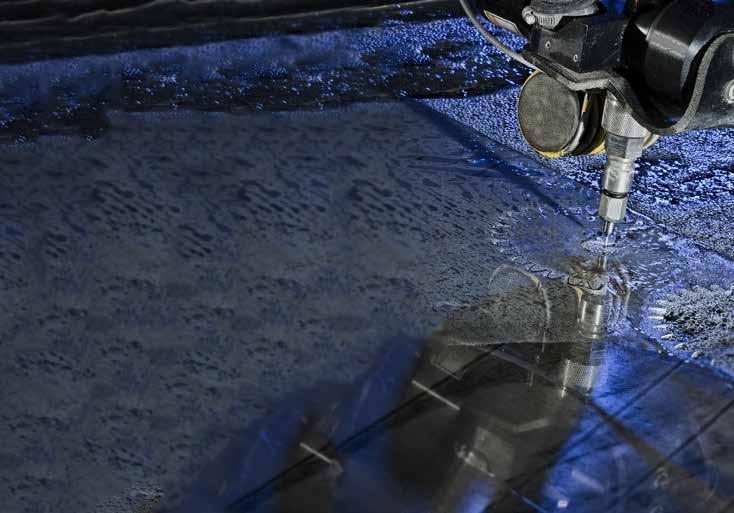
CUTS STEEL, ALUMINUM, GLASS, FOAM, RUBBER, CARBIDE, STONE AND GRANITE
EASY FIXTURING
OMAX@OMAX.COM • WWW.OMAX.COM
FOLLOW US
USER-FRIENDLY SOFTWARE
Enerpac HMT 13000: Rugged, safe and fast low-profile torque wrench
Enerpac has introduced its new lightweight, low-profile HMT 13000 interchangeable torque wrench, offering faster operation, fewer moving parts, with rugged alloys that give it a significantly longer lifespan.
The HMT 13000 – an extension to the previously introduced HMT product line – is designed especially for low-profile applications only and suits hex sizes from 62mm to 115mm AF. The HMT 13000 delivers output torques from 1,829 to 18,289 Nm in applications including those requiring powerful tool access to confined spaces in tasks in mining and aggregates, oil and gas, infrastructure and construction, manufacturing, maritime and power generation and distribution. “The HMT 13000 shares the same low cost of ownership as the broader range, and is also costeffective and reliable because the cassettes have up to 25% fewer internal components than other manufacturers, reducing the risk of failure and cost of repair,” says Tony Cooper, Marketing Manager at Enerpac Asia-Pacific. “The HMT 13000 distinguishes itself through speed, durability, and efficiency. It is designed to be interchangeable with different tools in the market. When it comes to speed, it offers a best-in-class outputto-weight ratio and is up to 25% faster than leading competitors. As for durability, superior alloys make this tool lightweight and gives it a 2.5 times longer life expectancy than comparable tools.” With regard to operator efficiency, the modular parts allow for interchangeability, but at the same time guarantee a higher productivity. Its 30-degree angle of rotation saves time and money and is 25% more efficient. Other features that improve operator efficiency are a 360-degree swivel hose attachment, lightweight design that results in less fatigue, and a standard ergonomic safety handle. The HMT series is complemented by Enerpac’s broader range of non-impact professional bolting technologies – including market-leading S and W torque wrenches – and by one of the world’s most comprehensive ranges of pump technologies. These include system-matched electric, air and petrol-powered types as well as the XC Series cordless torque wrench pumps, which are ideal for remote locations, sites that do not have access to power or where having electric cords could cause trip hazards, such as in maintenance workshops. www.enerpac.com

Algra Tooling: Going from strength to strength
Started up in 2019, Algra Tooling has pulled out all the stops in its two years of trading to help industrial companies throughout Australia access cutting tools. Now Algra has announced the launch of its brand new eCommerce website.
The sole importer of Dormer Pramet products into Australia, the new company has enjoyed rapid growth. To date Algra stocks more than 2,500 product lines, with a wide range of round and indexable tools provided to industrial distributors across the country. Dormer Pramet is a global manufacturer and supplier of tools for the metal cutting industry. Its comprehensive product program encompasses both rotary and indexable tools, covering drilling, milling, threading and turning applications for a variety of production environments. Andrew Sherry heads up Algra, assisted by fellow director Sandra Sherry and their competent team from the company’s premises in Hallam, Victoria. Sherry said: “Since launching Algra we have recruited additional staff, increased stock holding of more product lines, opened more accounts, created additional storage and now launched a brand new eCommerce website. The first two years have been a whirlwind, as with starting any new business. However, we have been really pleased with the reaction and support we have received from the marketplace. Algra can offer next-day delivery for most items right across Australia, meaning customers have easy access to high-quality tools whenever they need them. Even during COVID-19 times, the company has been receiving deliveries twice weekly from Dormer Pramet’s global warehouse in Europe. Therefore if it doesn’t have the relevant product available, it knows it can be here within four days.
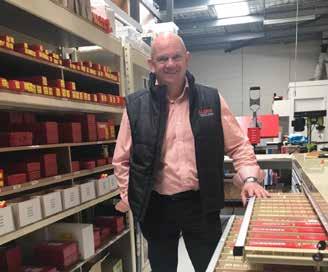
Andrew Sherry of Algra Tooling.
“The launch of our new website allows our customers to find products and place orders at the touch of a button, as well as read key features and benefits of the assortment available,” Sherry added. “The search functionality is an added time saver and the machining tips offer bite-sized learning. Dormer Pramet’s 2021 catalogues are featured on our website showing the complete and up-to-date ranges. And of course, we are still only a phone call away.” www.algratooling.com.au