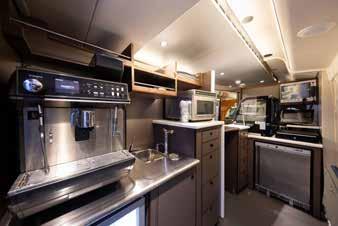
6 minute read
AM Hub case study: Cobalt Design
from AMT OCT/NOV 2021
by AMTIL
Additive Manufacturing Hub case study: Cobalt Design
Cobalt Design made use of 3D printing to create small-scale models for the refurbishment of a railway carriage’s servery café, with support and assistance from AMTIL’s Additive Manufacturing Hub.
Regional rolling stock across Australia and New Zealand is experiencing a surge in refurbishment programs aimed at extending the usable life of the interior spaces and amenities. Vehicle structure (as well as propulsion, braking and so on) are retained, while rejuvenating and refreshing the interior spaces as a means to upgrading the rolling stock or repurposing it for emerging markets, growing needs or new destinations. The challenge
The traditional method of refurbishing a carriage is to produce 2D CAD drawings and imagery to convey the approach, and to then rely on the experience of manufacturing personnel to implement the designs directly into the carriage at full scale. The process is timeconsuming due to a range of issues: • Components and brackets are often custom-made due to specific designs and low quantities. • Solutions often have to be compromised to be suitable for production requirements. • Feedback from stakeholders and management is only possible on a full-scale mock-up or an actual first-iteration 1:1 build. • Construction of structures in situ on rolling stock requires optimisation of subassemblies – minimising the number of subassemblies has advantages, but this must be balanced against the weight and size of the subassembly. Currently, this is typically managed ‘on the run’ during reviews of the first build or when a full-scale mock-up is built. Either approach is inefficient, and modifying full-scale structures and components extends development timelines. • Rolling stock depots that facilitate the build work often do not have the experience to move quickly through this process as it can be their first exposure to the vehicles being refurbished or to the refurbishment of interior spaces such as serveries (or both). Project Servo aimed to utilise additive manufacturing to create small-scale models of carriage interior spaces, components and equipment. This would enable stakeholders to communicate and evaluate different equipment alternatives within the space, as well as to test production methodologies and assembly sequences. The solution
Cobalt Design had been designing a servery café to be installed into a number of refurbished carriages. After the design concept was in development, Cobalt Design needed an effective method to communicate the design to the various project stakeholders, including production, maintenance, café staff and management. Cobalt Design engaged GoProto (ANZ) Pty Ltd to create 1:15 scale models of the interior space, major sub-assemblies and important components such as: • Bench workspaces. • Serving areas. • Storage cupboards and drawers. • Refrigerators. • Food display and warmer units. • Walls, door and structure. • Food cart and food cart storage options. The Multi Jet Fusion (MJF) process was chosen as a reliable method to produce accurate models, with high durability, which would enable the servery to be disassembled and reassembled many times. This would be necessary to simulate the different configurations and assembly order options, and gain input by different stakeholders. Quick 3D CAD models were created for the main sub-assemblies, and components of the servery were simplified to approximately 15 robust units able to be pieced together in a Lego-esque manner. 3D CAD images were sent to GoProto for production of the MJF parts. Within three days, parts were completed for Cobalt Design to verify the scale models, before air-freight to a New Zealand-based customer. Therefore, within a fortnight of initiation, the servery concept and various options were being simulated for use and evaluated by team stakeholders. How the Additive Manufacturing Hub helped
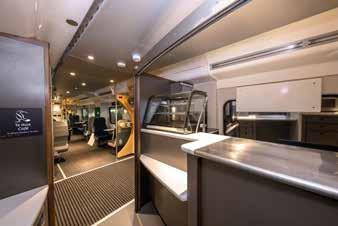
Scale models proved an important tool in achieving approval of the servery design by different stakeholders, offering various advantages: • Scale models enabled physical evaluation of the space – not just virtual evaluation via computer. • Physical model parts allowed production staff to physically test the assembly order and methodology • Robust MJF parts allowed repeated assembly and disassembly, while evaluating and discussing alternatives
• The servery model was designed to be able to be quickly modified if desired; new iterations of parts could be prototyped and fitted to the model quickly. However, such iterations were not required as stakeholders were satisfied with one of the original versions of the assembly. • Quicker sign-off was made possible as stakeholders could quickly evaluate the servery and physically test alternatives. In addition to the benefits of the scale models, using 3D printing opened up discussions about additive manufacturing methods for production. Since many refurbishment programs require smallscale production, additive manufacturing opens up greater design possibilities and engineering materials – such as 3D printing using metals and fire-retardant polymers. Several parts were investigated and quoted using additive manufacturing for production. It was assumed that the project would make use of a significant amount of a $20,000 Build It Better (BIB) voucher co-contribution from the Victorian Government via the Additive Manufacturing Hub. However, a only a small amount of the BIB voucher was spent, with GoProto. This was largely due to the successful design solution reached with the first concept, with no further iterations of the model required to be built. While this may appear a truncated use of the RSP budget, it was far from ineffective. Cobalt Design contributed substantial in-house hours of engineering and costing of the other DFAM (Design for Additive Manufacture) proposals in an attempt to progress to additive manufactured samples that would demonstrate the effectiveness of additive manufacturing for rolling stock production parts. Other rolling stock projects have since commenced (with others forecast) that are planned to employ the use of scale models and additive manufactured parts for production.
The outcome
The servery space was able to be built as a small-scale model – enabling stakeholders to evaluate and have input on the design, which would usually not be possible without the construction of a full-size mock-up. The scale model enabled the design to quickly move from concept stage to approval stage. With the model soon approved by stakeholders, the project was then able to proceed into final development and production. This saved weeks of work that would have been required to construct a full-scale mock-up, and then evaluate it, make possible modifications to full-scale parts, and so on. Cobalt Design has been able to showcase additive manufacturing to an industry where traditional methods such as full-scale mock-ups and techniques like hand-fabrication are the standard. With further projects on the horizon with the same customer, 3D-printed scale models will probably be used again to speed the project’s development and enable wider stakeholder engagement earlier in the design phase. In addition, Cobalt Design has been able to highlight benefits of additive manufacturing for production parts. It is anticipated that metal 3D printing will be used in a refurbishment program in the near future, particularly as cost of this service reduces over time.
www.amhub.net.au www.cobaltdesign.co
Home of intelligent additive manufacturing
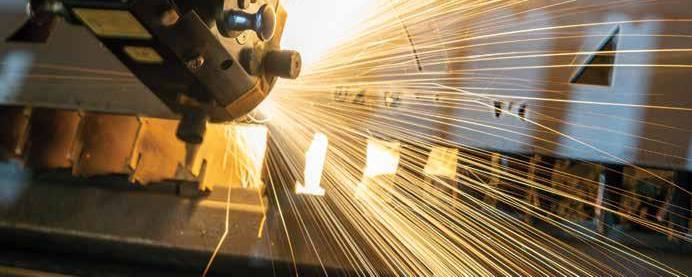
With considerable experience and proven capability in delivering additive manufactured parts, 3D Metalforge has the resources and technical know-how to make parts rapidly, precisely and for various environmental conditions. Working with a wide range of materials, component sizes and geometries, 3D Metalforge can create the quality parts you need cost-effectively and on time to avoid unplanned downtime. Ask about our end-to-end additive manufacturing services.
Call +61 0410 851 018 Email: david.green@3dmetalforge.com www.3dmetalforge.com