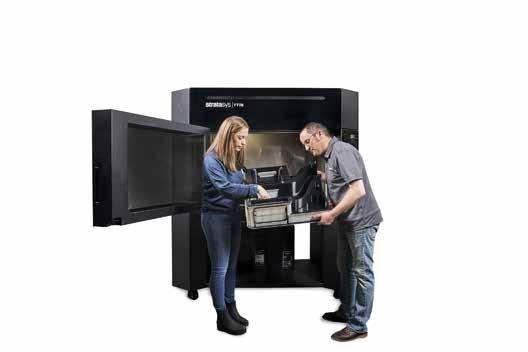
9 minute read
Next-gen 3D-printed catalysts propel hypersonic flight
from AMT OCT/NOV 2021
by AMTIL
Next-gen 3D-printed catalysts to propel hypersonic flight
Ultra-efficient 3D-printed catalysts could help solve the challenge of overheating in hypersonic aircraft and offer a revolutionary solution to thermal management across countless industries.
Developed by researchers at RMIT University, the highly versatile catalysts are cost-effective to make and simple to scale. Lab demonstrations show the 3D-printed catalysts could be used to power hypersonic flight while simultaneously cooling the system. Lead researcher Dr Selvakannan Periasamy said the work tackled one of the biggest challenges in hypersonic aircraft development: controlling heat build-up. “Our lab tests show the 3D-printed catalysts we’ve developed have great promise for the future of hypersonic flight,” Periasamy said. “They offer a potential solution for thermal management in aviation – and beyond. With further development, we hope this new generation of ultra-efficient 3D-printed catalysts could be used to transform any industrial process where overheating is an ever-present challenge.” Only a few experimental planes have reached hypersonic speed (defined as above Mach 5 – 6,100km/hour). In theory, a hypersonic aircraft could travel from London to Sydney in four hours, but many challenges remain in the development of hypersonic air travel, such as the extreme heat levels. First author and PhD researcher Roxanne Hubesch said using fuel as a coolant was one of the most promising experimental approaches to the overheating problem. “Fuels that can absorb heat while powering an aircraft are a key focus for scientists, but this idea relies on heat-consuming chemical reactions that need highly efficient catalysts,” Hubesch said. “Additionally, the heat exchangers where the fuel comes in contact with the catalysts must be as small as possible, because of the tight volume and weight constraints in hypersonic aircraft.” To make the catalysts, the team 3D-printed tiny heat exchangers made of metal alloys and coated them with synthetic minerals known as zeolites. The researchers replicated at lab scale the extreme temperatures and pressures experienced by the fuel at hypersonic speeds, to test their design’s functionality. When the 3D-printed structures heat up, some of the metal moves into the zeolite framework – a process crucial to the unprecedented efficiency of the new catalysts. The next steps for the team from RMIT’s Centre for Advanced Materials and Industrial Chemistry (CAMIC) include optimising the 3D-printed catalysts by studying them with X-ray synchrotron techniques and other analysis methods. The researchers also hope to extend the potential applications of the work into pollution control for vehicles and miniature devices to improve indoor air quality. Distinguished Professor Suresh Bhargava, Director of CAMIC, said the trillion-dollar chemical industry was largely based on old catalytic technology: “This third generation of catalysis can be linked with 3D-printing to create new complex designs that were previously not possible. Our new 3D-printed catalysts represent a radical new approach that has real potential to revolutionise the future of catalysis around the world.” www.rmit.edu.au
The F770. Complexity without complications.
Print large parts up to a meter long with an affordable, large-format 3D printer. The F770 delivers spacious build capacity in an easy-to-use platform with the reliability and consistency of Stratasys FDM technology.
Build volume 372L
Simple, no-hassle operation.
An intuitive user interface, GrabCAD Print software for easy file prep and remote print monitoring, and soluble support for design freedom and hands-free post-processing.
Stratasys FDM reliability.
Proven technology with print-and-forget dependability so what you design is what you get.
Large print capacity.
Enough space to print parts up to a meter long in an affordably priced system.
Additive manufacturing and the ‘zero-mile’ supply chain
The production of parts using additive manufacturing (AM) offers the possibility of a ‘zero-mile’ supply chain, ith significant potential benefits for manufacturing operations.
Manufacturers must often respond fast regarding the repair and turnaround of faulty equipment, minimising production disruption and downtime. Using 3D printing, parts can be produced rapidly in common materials such as steel, titanium, aluminium, or more exotic materials. Moreover, new materials designed specifically for AM offer improved performance. Given the large inventories found within typical manufacturing operations, a major question is: which parts are technically and commercially viable for AM? A recent audit for a US operation included a total inventory of 4,500 individual parts. Of these, some 450 were identified as technically feasible for printing, and 200 offered significant commercial benefits to the company compared with historic sourcing. Given the speed of production possible using AM in prototyping and serial production, manufacturers may consider investing in their own in-house 3D printing operation. The advantages include a ‘zero-mile’ parts supply chain, avoidance of high inventory levels, better process control, and risk mitigation against costly downtime. The alternative option is to source from a supplier offering printing services, with their specific lead times and supply chain risks. However, given the focus on productivity among mainstream manufacturing operations , it may be hard to justify the investment of time, technology and resources associated with an in-house AM facility. A more viable, proven option offers the ‘best of both worlds’, with quality parts are manufactured rapidly ondemand, with a zero-mile supply chain. This results in low operational risk, supporting onsite manufacturing or maintenance operations, but without the need for high capital investment or increased fixed manufacturing costs. In this scenario, an end-to-end provider of AM services, working under a parts supply contract, establishes a production facility, requiring minimal physical space, on or near the customer’s premises. A dedicated, secure digital parts library is established following a full audit of the client’s inventory. Relevant printing technology is established onsite and print parameters developed for the materials concerned. The supplier manages the AM production and internal parts order system on the customer’s behalf, delivering virtual on-demand parts production with a zero-mile supply chain. Operational risk is mitigated against the lack of availability of components, and inventories can be managed at lower cost. 3D Metalforge has developed this model at the Port of Singapore, undertaking a full audit of AM-suitable parts, digitalising them into a dedicated parts library ready for production, and manufacturing them on demand for the Port using a Hybrid Wire Arc printer. www.3dmetalforge.com
CSIRO develops low-cost titanium wire for additive manufacturing
The CSIRO has developed a novel and innovative process for turning inexpensive alloy waste into a high-value wire product suitable for the additive manufacturing market.
CSIRO Team Leader Dr Robert Wilson said researchers used low-cost titanium alloy particulates like machining swarf to produce a wire that can be used to make 3D-printed parts such as aerospace components. “The result is a product that is significantly cheaper than titanium wire made by conventional processes,“ Dr Wilson said. The wire is being fine-tuned for use in large format additive manufacturing such as Sciaky electron beam manufacturing and Wire Arc Additive Manufacturing (WAAM) – processes that melt the wire to form beads that stick together to create a layer of metal material that is then built up to form the 3D-printed part. The global market for titanium wire is worth over $200m. There is a lucrative market for 2.5mm to 3mm titanium wire as feed for this type of wireadditive manufacturing, and the cheaper wire generated from recycled sources can also be used to produce metal powders for 3D printing. The patented wire extrusion process, which is optimised using computational modelling, is being demonstrated to produce 50kg of titanium wire at pilot scale. The team is working to scale this up to 100kg-300kg pre-commercial volumes over coming months.
Richard Newbigin, Director of the Australasian Wire Industry Association, said Australia is well represented in various types of wire manufacturing, but until now has lacked sovereign capability in wire production for additive manufacturing: “Currently, Australian additive manufacturers have to source their titanium wire offshore, but this new capability will change that.” Barrie Finnin, CEO of additive manufacturing company Amaero International, agrees that locally produced titanium alloy wire and powders offer a valuable local capability for Australia’s growing additive manufacturing sector. “This technology has the potential to put Australia on the map as a competitive supplier of aerospace grade titanium alloy wire for additive CSIRO’s wire production process manufacturing and will greatly impact on our has been demonstrated at pilot global competitiveness,” Finnin said. “Even plant scale. © Nick Pitsas better, the end product will be comparable to what is currently available overseas, but much cheaper because it is using waste product.” The wire can be used to make large complex parts for markets such as aerospace, biomedical, defence, marine, automotive, construction and consumer goods. www.csiro.au
UNSW MMFI delivers AM solutions with help from Konica Minolta
Konica Minolta Australia is assisting the Materials & Manufacturing Futures Institute (MMFI) at the University of New South Wales (UNSW) with 3D printing technology for rapid prototyping and the manufacture of products.
The MMFI is an interdisciplinary research hub delivering tangible solutions to emerging global problems by studying, building, and transforming the future of materials innovation and advanced manufacturing. Through the MMFI, Australian manufacturers have access to state-of-the-art advanced manufacturing research and problem-solving skills coupled with the technology to address the barriers and opportunities in material sciences and advanced manufacturing, with diverse applications in printed electronics, transport, energy, information technology, and health. Professor Sean Li, the Institute’s director, said: “MMFI has the research expertise and infrastructure to support local industry. It also has access to other skills within UNSW such as science, chemistry, electrical engineering, and medical science, providing an even broader skillset that can be tapped. Not only can MMFI come up with a theory, we can use the in-house resources to test it, make changes, and in a short timeframe, produce a practical, real-world solution.” Matthew Hunter, Innovation Product Marketing Manager at Konica Minolta, said: “There is a renewed focus on onshore manufacturing and a massive opportunity for manufacturers in sectors such as aerospace, defence, automotive, and food and beverage. Therefore, it’s critical to have access to resources and skills such as those available through the MMFI to assist with this without requiring massive investment. MMFI has a unique capability to help local industry produce specialised parts that they may previously have had to source offshore.” The MMFI houses a 3D Systems ProJet HDMax 3500 and a Markforged ProX DMP 300, provided and supported by Konica Minolta. These were both recently used to ensure smooth transfer of graphite powder along the length of a helical screw in a manufacturing line. From prototyping to the end-use part, the finished tool was delivered successfully and is now being used to manufacture quality composite materials. From the prompt to the prototype to the product, this whole process was completed within two weeks using the expertise and facilities at the MMFI. Professor Sean Li said, “MMFI is keen to continue working with diverse industries to provide simple and elegant solutions that meet specific, complex requirements. MMFI has the capability to assist with any step of the process, whether it’s just a concept or ready for the production line. MMFI is committed to helping the industry with the creation of real and useful products, with a balance between commercial viability, performance, usability and sustainability.”
www.unsw.edu.au www.konicaminolta.com.au
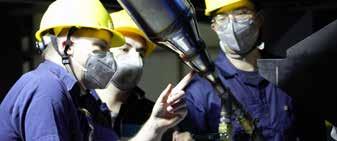