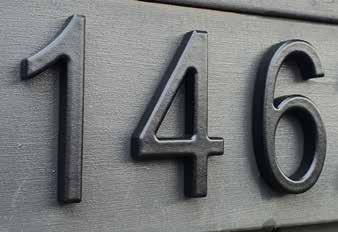
4 minute read
Postive signs for Addeva
from AMT OCT/NOV 2021
by AMTIL
Positive signs for +addeva
Victorian start-up +addeva is developing an online, end-to-end platform that allows customers to have design input and purchase signage on the same platform. +addeva then supplies the tailored signage, printed locally, inclusive of user-friendly mounting options.
The idea behind +addeva came about several years ago. Whilst running prototyping and manufacturing facilities, Leon Gairns, now director at +addeva, was regularly approached to quote and supply custom signage, vehicle badges and to remedy parts ordered offshore. Often, these projects were well suited to local additive manufacturing but lacked the appropriate CAD files and design input. In the early stages, the team at +addeva approached several software developers that could offer part of the solution but ultimately did not proceed, instead deciding to provide an end-to-end solution themselves. The Build It Better (BIB) voucher programme, provided through AMTIL’s Additive Manufacturing Hub, offered a pathway to design, optimise and validate the part geometry intellectual property (IP) in parallel with developing the online platform. The intent was to maximise the adoption of localised additive manufacturing. The challenge
• To allow the geometry and process validation of a customisable signage system with design freedom. • To remove the burden of CAD expertise, production lead times and often minimum order charges. • The inclusion of an alignment and mounting system as integral to the final product. The adoption of additive manufacturing allowed +addeva to quickly scale from a single letter, a combination of letters or even 2,000 letters without the commitment of tooling or having to machine from solid workpieces. The signage is printed in a robust polymer, with further post-finishing offered as optional. The solution
In undertaking the project, the Additive Manufacturing Hub engaged the assistance of registered service providers (RSPs) X-FORM Pty Ltd and GoProto (ANZ) Pty Ltd. +addeva’s familiarity with Multi Jet Fusion (MJF) as an additive production solution, along with robust material properties, presented MJF as the ideal candidate process against other legacy production processes. The project followed the following stages: a) Additive part geometry and appearance validation trials. b) System volume and online customer additive production trials. c) Printed and post finished marketing samples. Rapid design iteration and flexibility in geometry allowed +addeva to arrive at validated parameters, ensuring mass customisation and repeatability. The trials allowed the team to optimise the geometry, packing density, mounting system design, and post-finishing options to ensure consistent production throughput. The final geometry saw a 40% reduction of the original material requirement and allowed for a 15% increase in packing density. Once the validation and production parts trials were complete, +addeva had confidence that the outcome was repeatable, so CAD automation and print trials were then undertaken. These then increased to production volumes. Marketing reference samples followed, paired with volume trials for select customers. The MJF process enabled +addeva to trial and re-trial in quick succession and to ultimately supply quality end-use production parts, quickly and sourced locally. Additive manufacturing provided the flexibility to quickly scale without the upfront expense of CAD, tooling or shipping. It eliminated the significant lead-times experienced with legacy production such as subtractive and moulding processes.
How the Additive Manufacturing Hub helped
It was predicted the project would make full use of the $20,000 BIB voucher co-contribution. The estimated breakdown was: • $20,000 to X-FORM ($10,000 via BIB voucher). • $20,000 to GoProto ($10,000 via BIB voucher). Ultimately, a total of $30,250 (ex GST) was spent with the two RSPs. Of this amount, $15,125 was contributed by the BIB voucher and the remaining $15,125 was paid by +addeva. The breakdown per RSP was as follows: • X-FORM: $19,750 (ex GST). • GoProto: $10,500 (ex GST). Funds spent with GoProto were less than planned, largely because +addeva could reduce the final parts’ density, allowing more parts in each combined prototype build. MJF’s versatility in combining builds also reduced the quantity of printing required before +addeva was sure it had a commercial-ready production option. (Please note the software element was outside the BIB voucher scope). +addeva’s online platform is focused on signage, but it allows for the addition of other customer-defined products with set customisable geometry to be added in the future. +addeva’s adoption of additive manufacturing allows for a relatively risk-free ramp-up stage to supplying thousands of parts per week, and allows for manageable peaks and troughs that invariably come with early production. The IP developed in this project allows for easy transition to existing user groups but with added flexibility in design and supply. As volume increases, additional sales and production resources will see increased employment at +addeva. The outcome
The project outcome has allowed +addeva to develop: • A lean, fast, end-to-end local supply chain. • An online, self-serve customer-customisable signage. • The ability to scale from one part to thousands. • Several, flexible mounting systems. Over the project, part geometry could easily be modified, printed, and trialled in real-world conditions. +addeva was able to optimise the parts to further increase production capacity.
To find out more about +addeva, please contact Leon Gairns on 0477 352 549 or email: leon.gairns@addeva.com.au. www.amhub.net.au
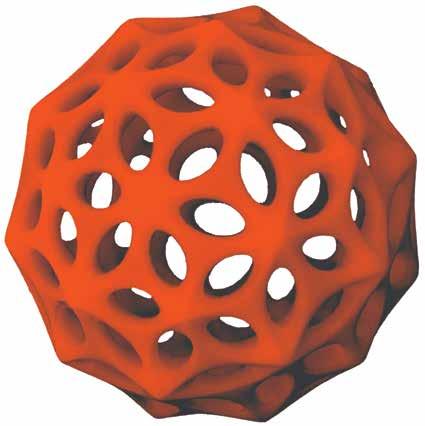
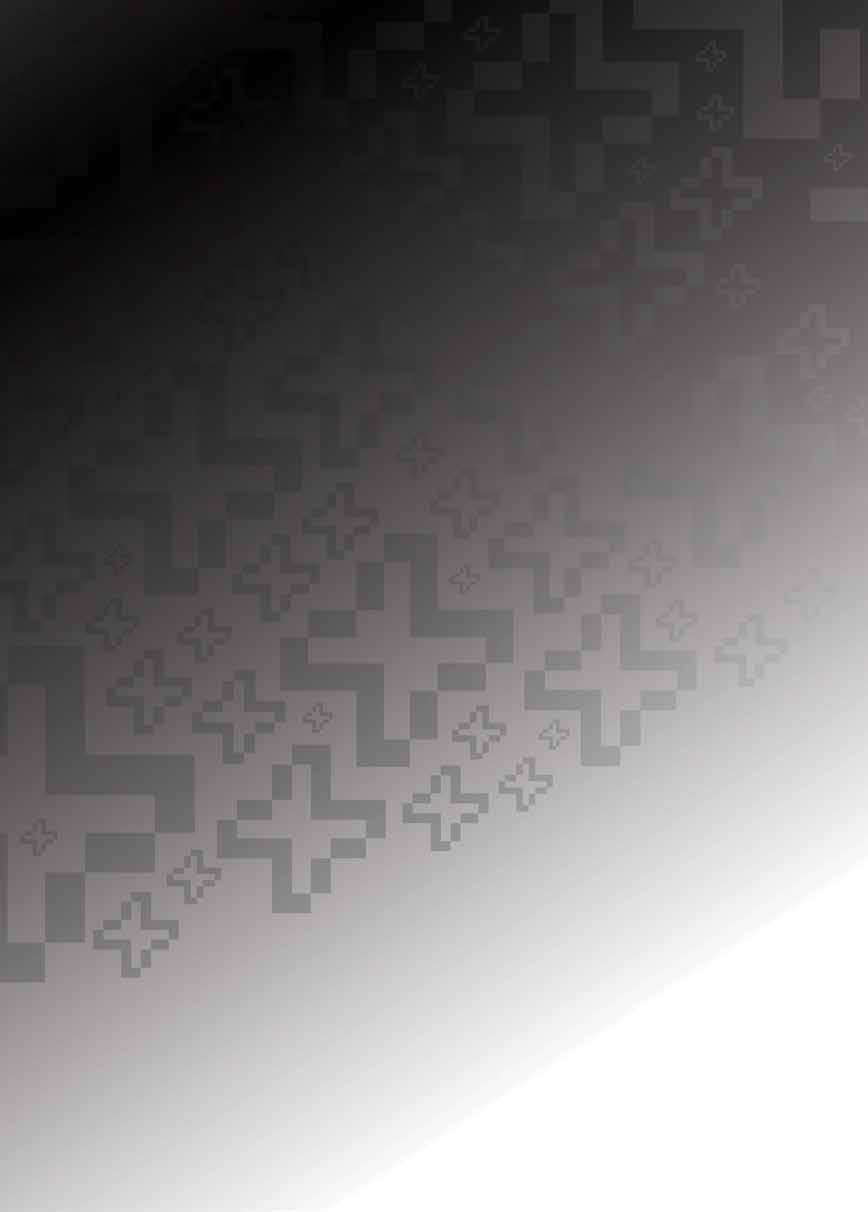
Explore your unlimited possibilities additively
The Additive Manufacturing Hub is a $1.85m programme that will grow and develop additive manufacturing capability and investment in Victoria. The vision of the AM Hub is to provide an industry-driven network of users, suppliers and supporters that will foster and grow the use of Additive Manufacturing technology in Australia. + Promote and market additive manufacturing sector capabilities. + Expand the knowledge base of additive manufacturing technologies. + Support the creation of high quality additive manufacturing jobs. + Be a voice to Government on additive manufacturing sector development.