
9 minute read
Frontline Manufacturing –New Deratech press brake
from AMT OCT/NOV 2021
by AMTIL
Frontline Manufacturing – Reinforcing capability with new Deratech press brake
Having overcome some big challenges in its 25-year history, Frontline Manufacturing is now a thriving manufacturing business operating from its plant in Meadowbrook, in Brisbane’s southern suburbs. The company recently invested in upgrading its specialist technical capability with the purchase of a state-of-the-art Deratech press brake, supplied by CMTS Sheetmetal Machines.
Matthew Ellis is a true inspiration to the Australian manufacturing industry. He established Frontline Manufacturing in 1996 when he was just 26 years old . In 2010 he lost it all when the Queensland floods destroyed his business and the insurance did not cover the loss. However, he successfully rebuilt the company and subsequently sold it to a larger company that shares his belief in Australian manufacturing. This financial support has seen Frontline grow into a 40-staff operation. With investment in news machines such as the recently acquired Deratech Ultima 1500/6100 press brake, the company’s future looks ever brighter. Ellis spoke to us about the company and the new machine. AMT: Tell us about Frontline Engineering? Matthew Ellis: I started Frontline in Queensland in 1996 with the aim of manufacturing pressed components. We started making componentry for the Australian manufacturing industry, and over the years we have grown to have a substantial manufacturing service that is highly respected. Lately we have been trying to establish Australia as a hub for military-grade armourplate products. These are the metal plates that are placed in military vehicles to protect soldiers from the danger of IEDs (Improvised Explosive Devices). The sheetmetal material used in this industry is very expensive and needs specialised expertise, equipment and technical ability to work with. There is folding tolerance that must be met. Because of the flexibility of the steel, it needs a lot of tonnage to fold. Get it wrong and the sheet is wasted at great cost. We needed to update our technology if we were to establish Frontline in the armoury plate industry. AMT: What brought you to CMTS Sheetmetal Machines? ME: One of our engineers went to a manufacturing exhibition in Melbourne where he came across the CMTS stand. They were displaying a range of machinery including the Deratech range. It was while striking up a conversation with Michael Schneider (Director Sales and Service at CMTS) and Bjorn Rabiot (Managing Director of Deratech Industries) that we decided to look further into Deratech’s
The new Deratech Ultima 1500/6100 press brake, in Frontline Manufacturing’s workshop in Meadowbrook, Queensland.
technology. We found them knowledgeable, and they seemed willing to help us out in our endeavour to establish Frontline in the armour plate industry. AMT: Tell us about the machine you ended up purchasing. ME: We decided to buy the Deratech Ultima 1,500-ton, 6,100mm machine. The Deratech Ultima is a CNC-controlled synchronised press-brake equipped with a multi-axis CNC-controller with angle programming possibilities. It has a CNCcontrolled mechanical crowning system and a fast and accurate backgauge on ball screws. This machine has the capacity and intelligence to work with the armoury plate steel. It has a laser angle measuring device that measures and controls the angle as it is folding. As mentioned, any mistake when folding this material will be costly. This laser technology manages the fold accuracy; therefore, there is no material loss and reduced costs. AMT: How did the installation go? ME: It was a massive project just to get the machine into Australia. With COVID-19 everything coming in from China had stopped. Everything required exemptions from the Australian Government. This was like a minefield because of all the restrictions in place. The staff at CMTS did so much work for us on this. They even had to bring in an engineer from Belgium to help with the install. They were outstanding; I can’t praise them enough. It took at least a year with everyone working together to get the job done. There were times where the CMTS team were in tears trying to get things done, but they did, and we really appreciate their efforts. AMT: It sounds like it’s been a significant commitment on your part. ME: Frontline Manufacturing is taking a leap of faith by investing in this machinery. We need to build a capacity that we believe will pay off. Our aim is to build the “Australian-Made” sector, and to do this we need to gear ourselves, ready for what we believe will be a growth in this sector. This installation was a major project for us, and it was good to have the CMTS team getting us there. AMT: Why is investment in technology like this so important for the Australian manufacturing industry?
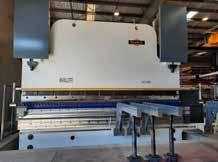
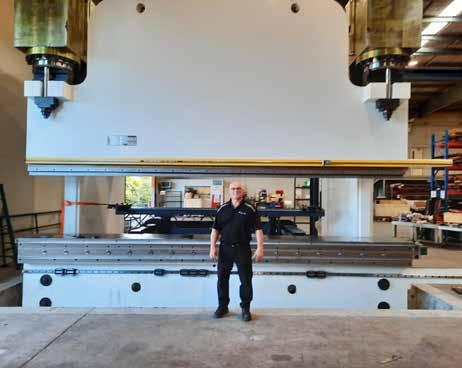
ME: It is using this technology that allows Australian manufacturers to save on costs and therefore become more competitive globally. It’s amazing what Australian manufacturers can produce, and if we can be competitive there is no reason why things can’t be made here in Australia. So, we went to look for what machines are out there to make this happen. We had assistance from the Australian Government, so it is also important to the Australian economy to make this work. It is important for manufacturers to invest in their business with capacity, machinery, technical knowledge, and people. Frontline Manufacturing’s new owners believe in the business and have put their efforts and capital in so that they can grow and lead new industries such as the armoury plate technology. We need to promote the idea that “Australian-Made” is worth it for all of us. In doing this, our government must also take the leap of faith in Australian manufacturing. Australian manufacturing is some of the best in the world and we
Michael Schneider, Director Sales and Service at CMTS Sheetmetal Machines, with the new machine.
now have the opportunity to do so with our lessening reliance on China. We all need to look internally to see what we can do. Australia is in a perfect storm right now, and as a country we should start looking at what we can manufacture here.
www.cmts.net.au www.frontlinemanufacturing.com.au
6KW MITSUBISHI STOCK MACHINE ON THE WAY. WE WILL ACCEPT TRADE-INS.
OWN FOR AS LITTLE AS $321 A DAY
Mitsubishi‘s 5 year warranty
Mitsubishi’s own Japanese-made fiber laser source comes backed by a 5 year warranty. AGR-eco
Mitubishi‘s exclusive AGR-eco technology reduces Nitrogen consumption by up to 90%, drastically improving processing speeds.
AI Assist Cutting
Mitsubishi’s AI automatically fine-tunes the cut conditions during processing by reading multiple cutting-head sensors, ensuring peak performance with no additional training or operator involvement.
Mitsubishi Zoom Cutting Head
Mitsubishi‘s Zoom Head adjusts the beams FROM diameter and focal height on the fly, far exceeding the performance of traditional autofocus cutting heads.
By providing optimal spot-size, cut quality and speed are improved dramatically across all thicknesses and materials. This next-generation high-performance controller from Mitsubishi allows one touch operation of advanced functionality.

Mitsubishi Bar Code Scanner
The use of a unique job barcode and scanner allows easy operation, minimising additional costs associated with operator training and machine downtime.
BEFORE YOU BUY: MAKE SURE YOU HAVE THESE FEATURES!
Mitsubishi D-Cubes Controller
CALL US TODAY: (03) 9115 1444 sales@kaizenmachinery.com.au www.kaizenmachinery.com.au
Metalmaster: An all-applications garage press
The hydraulic press is an essential tool for metal forming or separating rusted parts. Presses also make the job easy when removing and installing bushing, ball-joints and bearings. Garage presses really show their value when straightening or flattening components.
Metalmaster garage presses range from 10 tonnes up to 50 tonnes in terms of capacity. They are ideal for home workshops or mechanical repair shops, and are well suited to the needs of engineering and light manufacturing applications. The popular Metalmaster 20-tonne HP-20PP Workshop hydraulic press has a robust design and is constructed from industrial-grade C channel. The press has an adjustable sliding cylinder ram, a pressure gauge calibrated in both metric and imperial, and bending vee plates. The 20-tonne hydraulic ram and pump unit are also easily removed for use on other pressing jobs outside a workshop, such as straightening or bending. The HP-20PP hydraulic press features an adjustable sliding head, allowing up to 320mm of travel between the centre of the vertical posts. To accommodate offset pressing jobs, the user simply loosens the clamping plate bolts and the head of the press can be moved sideways. The Metalmaster HPF-50 trade press includes a convenient hand or foot operated pump that allows you to have both hands on your job when operating the foot pump. A unique feature of this 50-tonne press is its two-speed hydraulic system. This feature gives the benefit of rapid speed approach to get close to your work piece for increase productivity. The operator simply flicks over the dial switch into the slower working speed for increasing the pressure. As with the HP-20PP, the HPF-50 press has an adjustable sliding head, providing up to 240mm travel between the vertical post, a table height adjusting winch, metric/imperial pressure gauge. Also included are two heavy-duty multipurpose vee block/pressing plates, making this press ideal for professional mechanics or industrial workshops. According to Metalmaster distributor Hare & Forbes/Machinery House, this 50-tonne press exceeds the construction quality of today’s standard market versions, as this model features a fully robotic welded frame for the highest quality, accuracy and extra rigidity. To make the most out of your Metalmaster garage press productivity, a range of accessories are available including a 17-piece push driver set, a bearing race and seal driver set and an 11-piece steel press pin driver set.
www.machineryhouse.com.au

Hafco Metalmaster EB-330FAS Band Saw
The Hafco Metalmaster EB-330FAS is a fully automatic hitch feed, single mitre band saw designed for repetitive cutting of small-to-medium-sized sections in single or pack forms. The EB-330FAS NC Swivel Head Metal Cutting Band Saw features an automatic hitch feed and is equipped with a 178mm touch screen controller that stores 20 programs, while an inverter infinitely variable blade speed control over the range of 25-85mpm. The band saw cuts from 0 degrees to 45 degrees right in its automatic cycle, and from 0 degrees to 60 degrees right in the semi-automatic cycle. It also features hydraulic vice clamping with a manual hand wheel adjustment. Featuring a 500mm stroke hitch feed vice with ball screws and servo driven motor, the band saw is able to cut infinite lengths. Ball bearing blade guides ensure minimal blade clearance wear, which increases blade life due to less friction. A mechanical position sensor allows the saw frame to lower quickly toward the material and automatically detect the start-cut point. Blade wear is minimised by the bi-metal blade function that retracts the vice after cut, preventing the blade from rubbing on return. Other features include a quick action lock/ release lever for the swivel head, a heavy-duty gear drive system and a blade cleaning brush. Operation of the Metalmaster EB330FAS bandsaw is vibration free, with low noise and designed to produce clean, high precision cuts.
www.machineryhouse.com.au
