
6 minute read
Samin Sheet Metal –New Amada Ensis laser
from AMT OCT/NOV 2021
by AMTIL
Samin Sheet Metal – Productivity boost with new Amada Ensis laser
Joining his parents’ business in 1989, toolmaker Wade Samin soon began to reshape Samin Sheet Metal, which until then had been involved in cutting and folding simple sheet metal components. The company has come a long way since then, with an Ensis 6kw laser cutter becoming the latest in its line-up of machines from Amada.
Wade recalls how the business has evolved since he joined: “With my background as a toolmaker and understanding precision engineering, we started to develop a customer base that needed high-precision sheet metal. This move was the key driver for sourcing machinery that would give us the accuracy for precision cutting, folding and punching. “Targeting the electronics industry set our business on a solid growth path. We quickly discovered the unmet demands of that industry, and by satisfying its needs, built great customer relationships that boosted our growth. “Visiting a Brisbane machinery show, we were introduced to Amada equipment and invested in our first Amada press brake. The success of our first high-precision machine encouraged further machinery investment that included Amada turret punches, laser cutters and additional folding machines. “A bonus of our new precision capability was the ability to offer our existing customers additional services beyond cutting and folding. We soon discovered we could help our customers improve their designs or enable them to produce better designed products. For example, our precision manufacturing technology was highly suited for work such as PC board mounting chassis, racks and enclosures for electronic equipment.” Collaboration is taken seriously
“We collaborate closely with our customers on their designs,” Wade explains. “Understanding the end use of the product gives us great insight in satisfying their needs. Working closely with customers at the design stage is a big benefit for them in terms of receiving an optimised product. We believe this close working relationship with our customers is something that few others offer, and has helped us establish valuable goodwill and trust over the years. “Many sheet metal businesses expect a customer to come to them with specifications and drawings and will only produce exactly what they have been asked to deliver. The difference with Samin Sheet Metal is that we engage with customers at the earliest stages of design and we are happy to respond accordingly.” Driven by productivity

Wade Samin, owner of Samin Sheet Metal, with the Amada Ensis fibre laser machine.
Wade. “When we look at purchasing a new piece of equipment we always look at what automation is available, and particularly what automation would suit our job and our manufacturing processes. Our core objective throughout the many years of purchasing equipment is to produce more with the same staff levels – it’s all about productivity. “As an example, prior to purchasing our current Amada EM2510 turret punch equipped with its MP load/unload system, we had two turret punches with an operator at each machine. These machines were being run continuously throughout eighthour days and often at weekends. When we needed more punching capacity, we invested in a new Amada EM2510 servodriven turret punch, which allowed us to run with lights out unmanned operation. “The machine requires little maintenance and gives us a huge reduction in power consumption; an important consideration as energy costs were rising. The Amada EM2510 replaced both machines as well as giving us the extra capacity of a third machine. “The performance of the Amada machines cannot be faulted. The whole Amada package in sourcing, supply, installation and after-sales service has also been totally positive. This experience influenced our latest investment in the Amada 6kW Ensis laser cutter, which includes a load/unload system.” Exceeding expectations
“The Ensis laser has exceeded all our expectations in terms of performance and reliability,” Wade reports. “It is an outstanding machine. It is so fast we no longer needed to run our older automated laser cell, as the new Amada Ensis 6kw laser cutter with its MPL load/unload system was more productive than three machines combined. “The next step was to run the Ensis laser at night, lights off, doing the work of three machines – with a single operator. This has enabled us to keep tight lead times, often on a very short cycle. We can now cut faster, cut thicker material, with lights-out unmanned operation. Its capacity to turn out three times the amount of work in the same timeframe has absolutely proven its worth. “Whether simply cutting and bending material such as a simple flat intercom fascia for an electronic component, or a complete build of a cabin for a piece of earthmoving equipment, Samin Sheet Metal has the capability to deliver a total solution.”
www.amada.com.au www.samin.com.au
Production Manager Hans Kummerehl checking the MPL loading system ready to feed the Ensis laser machine.
Gessner Industries increases output by 50% with Okuma
Toowoomba-based company Gessner Industries recently commissioned the latest Okuma CNC vertical machining centre, model MB56VA with OSPP300MA Control, dramatically increasing output from its machining shop.
A market leader in the manufacture of agriculture and earthmoving machinery, Gessner Industries was founded in 1975 and is now owned by brothers Jim and Michael O’Connor. With more than 45 years of proven service to the agriculture, construction and mining industries in Australia, the company has built up an enviable name for both quality and reliability. Today the company occupies a modern manufacturing facility and boasts a full-time specialist engineering and design department capable of customising equipment to meet the needs of its customers. After establishing a need for additional machining capacity, the Okuma machining centre was selected following a careful analysis of the specifications required for business both now and into the future. This included the importance of four-axis capability, a full review of the service level available, plus strong positive feedback from other Okuma machine users. A critical factor in the selection process was the service provided by Okuma for customers in Far North Queensland and the exceptional level of technical expertise that was available for customers in the more remote areas of Australia. “Like many industries, we are constantly under threat from imports but our customers want to support local business wherever possible and it’s important for us to remain highly competitive with robust quality products,” says Director Jim O’Connor. “Okuma was a good fit for us as both Okuma and Gessner Industries take quality and customer service extremely seriously, and the new machining centre is already providing us with the highest quality output and reducing our costs.” Gessner Industries currently employs some 50 personnel. However, with a 50% increase in output from the machining shop as a result of the introduction of the new Okuma machine, it is allowing more fabricators to be employed to cope with an increase in fabrication work and a reduction in lead times overall for equipment. The company’s product range includes broad acre and row crop equipment, sugarcane machinery, earthmoving attachments and an extensive range of spare parts servicing the market both directly and through an expanding dealer network throughout Australia. The range continues to develop with ongoing R&D and design development into new products, with an eye to export potential, particularly throughout South-East Asia. “Gessner Industries is taking full advantage of the extensive training offered by Okuma,” says Jim. “The experienced staff within the machining department see this major investment in advanced precision engineering as an exciting positive step, opening up new opportunities, skill levels and enhanced job security.” John Baker, Sales & Applications Engineer – Queensland for Okuma, congratulated Gessner Industries on the purchase of its first Okuma CNC machining centre: “We look forward to a long and productive relationship with Gessner Industries. The future looks bright for this business as they reap the benefits of fast production of high-quality precision parts culminating in the further enhancement of competitive Australian manufacturing.”
www.okumaaustralia.com.au www.gessner.com.au

Components manufactured on the new Okuma CNC vertical machining centre.
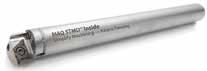
