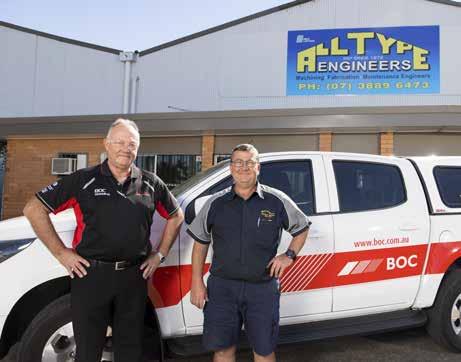
5 minute read
All types of solutions for Alltype Engineers
from AMT OCT/NOV 2021
by AMTIL
Family-owned business Alltype Engineers has been in operation since 1973, providing hiqh-quality fabrication, site installation, construction and maintenance services to its customers locally in Brendale, Queensland, and across Australia.
Since Darren Aldridge took over the business from his father Mike, the company has been expanding its services, originally starting in material handling and diversifying into general fabrication. With up to 12 workers on the floor and out on site on any given day, a top priority is to ensure premium product quality and production efficiency by using high-quality welding equipment and gas. Alltype Engineers faced a challenge when it won its largest ever order to weld aluminium trench shoring boxes. Trench shoring boxes are made from aluminium and placed in the ground on excavation sites to provide stability in trenches and keep workers safe. To meet the requirement of this order, it was essential that the company had the best equipment and gases on hand to increase staff productivity and save time. Meeting demand
Working in a busy workshop with large projects and tight deadlines meant time was of the essence. With customer demands increasing, Alltype Engineers took a holistic view of its services and equipment. The team decided to start shopping around for high-quality gases, welding equipment, aluminium wires and day-to-day consumables. The workshop is welding every day, with anywhere between four and six cylinders used each week. “We were ordering cylinders every second day,” says Darren. “This is hugely timeconsuming when you consider we have at least four people welding at all times and the work involved in connecting regulators and transporting them around the workshop.” When staff detached a regulator from a cylinder, there was always a risk that they would drop it on the ground, break it, or crack the valve open too fast and blow the diaphragm. This creates a safety risk and would occasionally result in damage to the regulators. Alltype Engineers was seeking value for money, and after a survey of the market it found that BOC’s F3 VIPR cylinders exceeded expectations. It decided to upgrade all of its G-size cylinders to the F3 VIPR cylinders. “Not only did we switch over our cylinders but after an initial trial of BOC’s EWM MIG welding machine, we quickly realised this was the premium product on the market with an amazing price point,” Darren adds. “Our staff got the EWM Phoenix 405 and 355s with push-pull torches to cycle
Paul Broughton, Area Manager – North Brisbane at BOC, and Darren Aldridge, Director at Alltype Engineers.
running at 380 AMPs. We were so happy with the EWM that we now have six of them in our workshop.” Time and cost savings
“We immediately noticed time-saving benefits with BOC’s EWM machine,” Darren explains. “With previous welding machines, it would take us three days to weld a 6m panel. Now it only takes us about 16 hours in total, saving us four to six hours of work per day. “The EWM machines have massively increased our productivity. We love the simplicity and versatility of the machine, that allows each welder to programme the machine to suit their task. Our oldest EWM has been working flat out for four years and we have never had a breakdown – that demonstrates just how robust they are. “We were ordering gas every second day and now with the F3 VIPR bottles, we only order once per week. It has relieved me and my staff as we aren’t moving around huge gas bottles, and it saves me money as there is less downtime. In essence, it improves the profitability of our own products.” The innovative F3 VIPR cylinder not only provides value for money by eliminating the need to replace or service regulators and gauges thanks to the in-built regulator, but they are also filled to a pressure of 300 bar and contain up to 15% more gas than the G-size. Consequently, Alltype Engineers
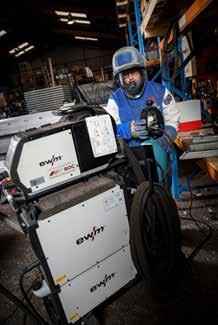
Alltype Engineers has achieved significant productivity gains with BOC’s EWM MIG welding machine.
can get an extra day and a half out of a cylinder. It also has improved safety features including a handle, protective casing for the regulator, and a shorter height for easier transportation, manual handling and installation on the back of the welders. Australian made
Alltype Engineers didn’t stop there. The aluminium trench shoring box project required 25mm-thick aluminium to be able
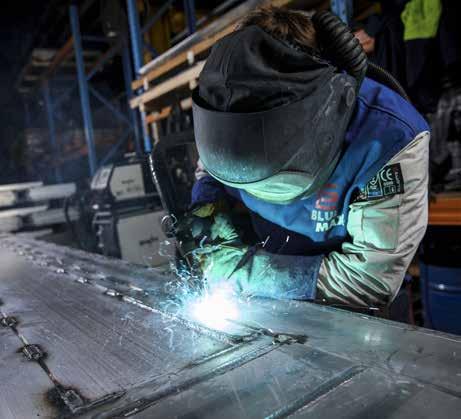
to withstand intense heat. “This was our largest order ever,” says Darren. “It required 115 tonnes of aluminium and 18mm-wide fillets welding at 400 AMPS. We tried 15 products on the market to see what type of aluminium wire best suited our needs and yet again, we found BOC’s aluminium wire to be the highest quality. With previous suppliers, one in ten was a faulty roll. Faulty rolls can damage the welding equipment
Welding operations in progress at Alltype Engineers workshop in Brendale.
by wearing the parts too quickly, but BOC’s SAFRA wire is triple shaved, so the welding spares like liners do not wear, unlike with other aluminium wires on the market. I can confidently say we have never had a faulty roll from BOC. “Our client used to purchase aluminium panels in the US and transport them to Australia, but now we cut and weld the panels together to make an Australian product.” Darren concludes: “We wouldn’t have been able to do the aluminium trench box project five years ago, but thanks to our gas and welding solutions, we are the only aluminium panel maker in Australia, with panels that are 35% stronger than our US competitors. That is something we are very proud of. “We were getting our gas off BOC and now we get everything – gas, welding machines and all of our day-to-day consumables – because we know they are reliable and BOC experts are always on hand.”
www.boc.com.au www.alltypeengineering.com.au
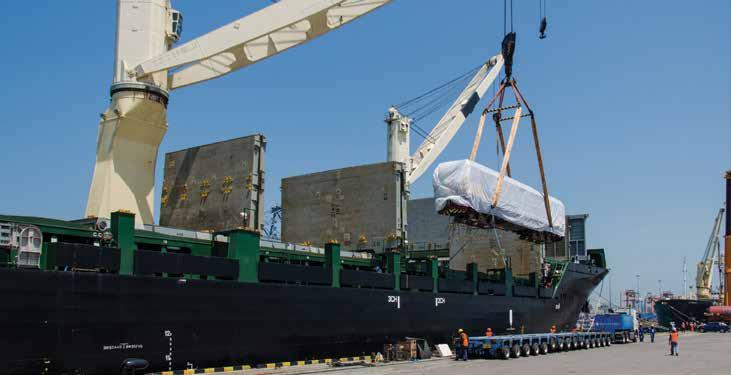