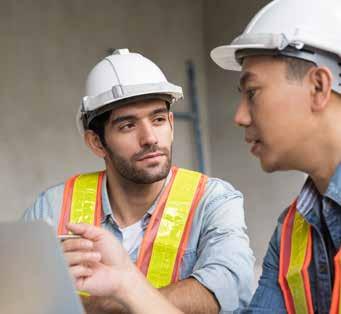
27 minute read
VOICEBOX: Opinions from the manufacturing industry
from AMT DEC 2021
by AMTIL
Why can’t Australia make mRNA vaccines? Because we don’t make enough ‘deep technology’ companies
The delays Australia has seen in the roll-out of COVID-19 vaccines this year highlight a weakness in our national innovation system, and its inability to support and nurture “deep technology” ventures. By Julian Waters-Lynch.
Caught out by its strategy to bet on COVID-19 vaccines that could be made in Australia, the Federal Government is now scrambling to manufacture mRNA vaccines locally. Its “approach to market” strategy has effectively asked companies how much government money they need to do so. But even with subsidies, this plan will take years. So why can’t Australia make the mRNA vaccines?
That’s not actually the right question to ask. The crucial issue is why Australia hasn’t been producing the type of companies that can make mRNA vaccines. Why don’t we produce more start-ups like BioNTech or Moderna – the two companies that developed and brought the mRNA vaccines to market? Answering this question is important not just to vaccines but to the whole range of “deep technologies” that will shape economic development and sustainability in the 21st century. Technology is generally defined as the application of new knowledge for practical purposes. Deep technology is slightly different. It refers to the type of organisation required to bring certain types of technological innovation to fruition. It is more accurate to talk about deep technology ventures. BioNTech and Moderna are two such examples. Both are relatively young companies — BioNTech was founded in Germany in 2008, Moderna in the US in 2010 — that have brought to market a technological solution underpinned by substantive advances in scientific research, engineering and design. Deep-tech ventures span advanced materials, artificial intelligence, biotechnology, blockchains, robotics and quantum computing. A few are now household names, such as Tesla and SpaceX, but most fly under the radar of public awareness, as Moderna and BioNTech did before the pandemic. They include synthetic biology companies such as the Ginkgo Bioworks and Zymergen, which can program organisms to create completely new biologically-based materials for use in manufacturing. These “biofoundries” can produce everything from biodegradable plastics, to new protein-based foods, to probiotic microorganims that improve human health. There are advanced engineering companies such as Carbon Engineering and Climeworks, working on ways to suck carbon dioxide from the air to use for industrial purposes. There are experimental energy companies such as Commonwealth Fusion Systems and Helion, which are working on making the holy grail of clean energy technology, nuclear fusion, a reality. Australia’s problem with deep technology ventures isn’t to do with the quality of our science and research. We produce, per capita, nearly twice as many scientific research papers as the OECD average. We also have some great support structures, such as the CSIRO, the national research and science agency, and Cicada Innovations, the deep-tech venture incubator in Sydney. The problem is our inability to take our scientists’ knowledge and turn it into innovative ventures. Other countries are much more successful at this. Britain, Germany and France, for example, all publish fewer research papers than Australia per capita but produce far more patent applications — a key indicator of potential research commercialisation. The US produces nine times as many per capita. Australia’s primary challenges here are related to the culture of innovation and entrepreneurship and our current mechanisms for long-term venture funding. Deep-tech ventures usually require longer time horizons to translate new scientific insights into commercially successful products. Few universities are set up to see this process through. Public funding mechanisms prioritise basic research leading to publications, not the entrepreneurial processes required to find a market fit for a new product or solution. Nor are venture capital funds — the normal providers of seed funding — well placed to fund deep technology ventures. This is partly because the science itself can be difficult to understand. Also many funds prioritise ventures that can “exit” through an acquisition or public offering within ten years. The complex science and length of time needed to commercialise deep tech mean many good ideas die in the so-called “valley of death” — the gap between initial seed funding and sustainable revenue generated from product sales. This gap is filled in some countries by investments from sovereign wealth funds, more “mission”-oriented government programs and even prizes. Australia has yet to emulate these solutions. These issues help explain why Australia’s investment in R&D as a portion of GDP over the past decade has declined, from a peak of 2.3% in 2008 to 1.8% in 2019. That puts us below the OECD average (2.47% in 2019), well behind innovation leaders such as Israel (4.9%), South Korea (4.6%) and Taiwan (3.5%). In 2020 only 12 Australian companies were listed among the world’s top 2,500 R&D leaders (as ranked by EU Industrial R&D Investment Scoreboard). This compares with Taiwan (88), South Korea (59) Switzerland (58), Canada (30) and Israel (22). Australia’s future economic prosperity depends on our ability to translate scientific advances into innovation and entrepreneurship. Technological innovation is the only driver of economic growth over the long term. MIT professor Robert Solow won the 1987 Nobel Prize in Economics for his work demonstrating this point. To correct our trajectory requires more “patient” capital. We are one of the world’s wealthiest nations on a per capita basis, but too much wealth is locked up in property ($8 trillion) and superannuation funds ($3.8 trillion), opting for “safer” investments. If just 0.1% of superannuation assets were allocated to fund deep technology ventures, Australia would have a fund about as large as the nation’s entire current venture capital pool invested in the past financial year. We also need leadership around a shared vision of the benefits of deep technology entrepreneurship. Not enough Australians recognise the importance of science and technology in driving both economic prosperity and addressing global challenges. Some are even suspicious that technology causes more problems than it solves. But these ventures will be crucial to addressing pressing development and sustainability challenges, including climate change. Tomorrow’s economy and society will be built with today’s scientific breakthroughs in deep technology ventures.
Dr Julian Waters-Lynch is a Lecturer in Entrepreneurship, Innovation and Organisational Design at RMIT University. This article was originally published by The Conversation. www.theconversation.com www.rmit.edu.au
How manufacturers can make the most out of Active Intelligence
The manufacturing sector faces a plethora of opportunities by effectively using Big Data. Paul Leahy examines how data can be used to achieve responsible production, augment product engineering through smart automation, drive predictive maintenance, and adapt to the industry’s changing demands?
The benefits of technologies such as Big Data and artificial intelligence (AI) are increasingly apparent; when deployed appropriately there’s no denying their potential impact on an organisation’s bottom line. According to a study by Partners, businesses are reaping the rewards of Big Data and AI, with successful business outcomes almost doubling in the past half decade from 49% to 96%. More and more businesses across sectors are increasing their use of data, with 99% of businesses surveyed by NewVantage shown to have invested in data initiatives. The value of investments in Big Data has also increased 10-fold between 2011 and 2021, and this number is expected to reach US$100bn by 2026. The implication is clear: businesses across sectors are aware that optimal data-harnessing can deliver great value. To achieve this, however, they will need to tap into the right technological framework. Conserving natural resources has emerged as a non-negotiable priority for businesses in the face of the growing climate crisis. According to experts, we will cross the point of no return within the next two decades if necessary measures are not implemented on a large scale. As such, manufacturers across the world are switching to responsible production by adopting sustainable practices. Companies are exploring greener alternatives to generate energy, while focusing on resource and energy conservation. For instance, Australian supermarket Coles has reduced its coal power consumption by switching to 70% clean, renewable energy, and has signed multiple wind and solar power purchase agreement (PPAs) to fulfil its commitment to becoming 100% renewable electricity by 2025. This is where something like Qlik’s Active Intelligence Platform comes in, as it helps create in-the-moment awareness of the business through real-time information to trigger immediate actions. Manufacturers can use this framework to maximise the efficiency of their sustainability initiatives. Active Intelligence analyses up-to-date information sourced from an extensive Internet of Things (IoT)-driven framework that can help companies accurately calculate the rate of resource usage and depletion. It can also help them forecast and determine the quantity of raw materials required to achieve the delivery targets that are subject to change in a volatile market landscape, especially in the post-pandemic era. The seamless workflows enabled by Active Intelligence improve the interactions and flow of data between manufacturers, distributors and retailers for more accurate and efficient decision-making and demand projection. The insights generated can also be used to minimise wastage while sourcing materials from the primary sector. These insights can empower manufacturers to enhance the intermediate processes, ensuring optimal utilisation of non-renewable resources. Therefore, the intricate analysis performed via Active Intelligence can help companies come up with innovative strategies that reduce and recycle materials to create alternative sources of revenue – boosting overall profitability. Traditional design procedures involve many levels of scrutiny and fault testing that are not only difficult to maintain manually but can also lead to human errors. Top manufacturers leverage the power of automation and analytics to overcome this challenge while optimising the efficiency of product engineering generative design. A vast amount of data is involved in the process – and the greater the volume, the more efficient the algorithm. Active Intelligence can help companies leverage dynamic content and logic through AI and machine learning (ML) to drive innovation while minimising costs and time as well as eliminating errors from the production process. To give an example, a company designing a three-legged chair can feed a detailed design brief into generative design software. The Active Intelligence-powered AI/ML algorithms then come up with all possible configurations and, aligned with ergonomic constraints fed by engineers, produce the best set of solutions. Following the testing phase, the system finalises the optimal solution. Machine breakdowns are costly affairs – not only because of the cost incurred to replace/repair the machine but also in terms of hours lost due to the operational disruption. What compounds the challenge is that, in the absence of the right technology, predicting equipment failure is difficult. As per a 2018 study, unplanned downtime, or part maintenance, upgrades or repairs cost manufacturers US$50bn a year. Active Intelligence can empower manufacturers to achieve this. Industrial machines generate huge volumes of real-time and historical data – which can be analysed with AI/ML to predict and trigger proactive maintenance. In doing so, manufacturers can ensure peak performance and business continuity. Top companies such as Mitsubishi Electric are already using intelligent, interconnected systems to drive predictive maintenance, minimising costs and downtime while augmenting productivity and responsiveness. While the COVID-19 pandemic is a one-off event, disruptions in the supply chain are a regular occurrence. Armed with the power of Active Intelligence, manufacturers can determine with precision how much further they should advance a delivery date in line with the delay in procuring the raw material. Besides calculating how disruption will affect their operations, both in terms of time and finances, Active Intelligence can help businesses to determine the regions/markets where they can divert their supplies to – or source their raw materials from – to mitigate the negative effects on their unit economics. For instance, Active Intelligence empowered Qlik customer Multipack, an Australian packaging services provider, to strategically scale up and down its operations in line with fluctuating demand during the pandemic. By reducing decision-making time from days to minutes, the platform helped Multipack take just-in-time decisions to efficiently streamline its production processes. Using systems like Active Intelligence to eliminate operational bottlenecks and optimising processes, industries can start to gain superior financial benefits. Utilising technology to collate, combine and analyse incredible volumes of information will allow enterprises across sectors to make optimal business decisions that ensure they effectively navigate the post-pandemic, increasingly digital-first business ecosystem.
Paul Leahy is Country Manager – ANZ at Qlik. www.qlik.com
Why manufacturing firms must ramp up their contractor management approach
The COVID-19 pandemic and its resultant disruption have highlighted the need for manufacturing businesses to take careful steps in the management of on-site contractors. By Stephen Darracott.
The coronavirus pandemic continues to disrupt businesses and our communities. Nevertheless, the Australian manufacturing sector is thriving. With ongoing restrictions and lockdowns in some regions, manufacturing companies should look for technology solutions that can help them help increase safety and security at their sites. One area that can’t be underestimated is managing contractors, casual workers and visitors. It has always been important to know who is working onsite. It’s also essential to make sure contractors and casual staff have had required training, and health and safety inductions. Furthermore, manufacturers need to ensure that contractors are licensed and insured before letting them get to work. In the past, this has usually been done using manual, paperbased forms and processes. However, this approach is prone to error and can make it difficult to accurately determine who was onsite at any given time; a key requirement of the Government’s COVID-19 safety requirements. COVID-19 has emphasised the importance of being able to securely manage contractors and visitors to manufacturing facilities. Contractors can often move between various manufacturers, which makes it even more important to be able to accurately trace their movements if an outbreak were to occur. The nature of their movement means that contractors could even be an infection vector, making it all the more important to be able to accurately pinpoint where they were, how long they were there for, and whom they came into contact with. Modern solutions to address these challenges include digital visitor management systems. These are cost-effective yet highly efficient solutions that track contractors and include more information than would be possible with manual sign-in sheets or other forms of confirmation. This lets manufacturers dramatically improve safety and compliance within their facilities while simultaneously achieving a return on investment in the digital visitor management system through reduced overheads and administrative costs involved in managing contractors. For example, a digital visitor management system can include a kiosk placed at the facility’s entry or reception. Placing it close to office staff can help ensure that all visitors and contractors sign in on entry, using the system, without having to dedicate resources to sign them in and conduct inductions. By removing the need for dedicated staff members to manage visitors, manufacturers can lower costs and redirect those workers to more valuable, growthoriented tasks. Some systems can include elements such as temperature checks to lower the risk of infected people entering the business. The same system can automatically notify staff onsite if a contractor’s temperature is high so they can determine whether that person should be allowed onsite. This can help protect the business and all its workers during COVID-19 outbreaks and it can also help prevent the spread of other infectious diseases such as influenza. Deploying these solutions now can futureproof the organisation against other health events. COVID-19 requirements are far from the only reason manufacturers should invest in digital visitor management systems. These systems provide an added layer of support when it comes to keeping contractors and other visitors safe onsite. Like the Government’s COVID-19 check-in application, a digital visitor management system can use a QR code to direct contractors to a sign-in page. Visitors can even pre-sign in using a dedicated website, saving time once they arrive onsite. The manufacturing firm can request specific information from the contractor, including details regarding accreditations or licences. Before they can finish checking in, the manufacturer can require contractors to complete a site induction or safety checklist. Digital visitor management systems provide a snapshot of who is onsite at any time and also ensure that all contractors and visitors have completed the necessary inductions. In case of emergency, it’s also easier to determine who should be onsite so that, if anyone is missing, first responders can be alerted and can start searching for them sooner. The latest digital visitor management systems store all of this information in a secure database in real time. This means the information can only be accessed by authorised users, protecting the privacy of contractors while ensuring the business has the information it needs to keep everyone safe. The need for more effective ways to track and trace visitors and contractors to manufacturing facilities has been accelerated and highlighted by the pandemic. However, there are many other benefits that digital visitor management systems can provide to manufacturing firms. These include cost reductions due to less time spent managing visitors, and increased ability to manage the health, safety, and security of the entire workforce, including contractors. While the manufacturing industry faces a bright outlook, recent events have shown that it’s impossible to predict the future. It’s important for manufacturers to prepare for potential events by modernising their visitor and contractor management processes for increased accuracy and control, without increasing costs.
Stephen Darracott is Vice-President and Country Manager at Pitney Bowes Japan, Australia and New Zealand. www.pitneybowes.com
Electric vehicles: Australia’s unexpected boom industry
Despite slow consumuer take-up and public scepticism, electric vehicles are well-suited to the Australian market, manufacturers here are poised to capitalise on a booming market. By Stephane Marouani.
The perception over recent years has been that Australia is not suited to electric vehicles (EVs) due to their perceived range limitations and the long distances we have in Australia. As a result, the adoption of domestic EVs here has fallen behind that of other countries. However, the reality is Australia’s EV manufacturing industry is booming, because this market is incredibly well-suited to EVs. Firstly, our renewable energy capacity (mainly solar) is growing at a world-leading pace, with the ability to provide a cheap and easily deployable recharging network. Moreover, a lot of major Australian industries lend themselves to EV deployment. For example, the use of EVs such as utes or trucks in the mining industry makes absolute sense. It is significantly safer (especially in underground conditions), but the vehicles are also cheaper to maintain, with fewer mechanical parts subject to wear in harsh conditions. Many mines in Australia are remote and already have plans to begin operating their own micro-grids, renewable energy plant and storage batteries for their needs. The same applies to both forestry and farming equipment. As a result, we’re seeing Australian start-ups booming in the electrification space, with the growing need for specialised vehicles in mining (SafeScape), farming, construction and forestry (DC Equipment), and even aviation (MagniX). So, what is it about Australia that has led to this boom? • Engineering experience: Following the departure of the automotive OEMs a few years ago, Australia now has a pool of very experienced automotive engineers who have decided to innovate and create their own start-ups, rather than relocating internationally. • Renewable energy research: For years Australia has hosted the world’s largest solar EV race, leading to significant innovation in the market. For example, the first solar-powered luxury sedan, from a company called Lightyear, had its infancy in the Darwin-to-Adelaide Bridgestone World Solar Challenge. • Industry/university collaboration: Universities such as
UTS or UNSW have been collaborating with businesses to drive electrification research and innovation, which means local innovations in EVs came years ahead of those from mainstream EV manufacturers. As far back as 2013, I had the opportunity to drive the first battery-powered electric
Holden Commodore, developed by Melbourne-based start-up EV Engineering. • Overlap with motorsports: We are seeing automotive suppliers such as MOTEC increasingly transitioning their motorsport racing experience across to the EV industry. • Funding and investment: We shouldn’t underestimate the importance of funding in supporting the industry. The Australian
Renewable Energy Agency (ARENA) has been supporting EV innovation with the investment of a $200m-plus fund targeting charging technologies and infrastructure. One example of an Australian business making waves in the EV industry is Lumen Freedom. The McLaren Speedtail Hyper-GT is the British auto manufacturer’s fastest road car ever. Near the end of testing, a prototype of the sleek gas-electric hybrid sports car hit 403kph at the Johnny Bohmer Proving Grounds, NASA’s runway in Florida. Specs for the 2020 production model say that it can go from 0 to 300kph in 13 seconds. To charge the lightweight battery whenever the aerodynamic three-seat vehicle isn’t in use, McLaren partnered with Lumen Freedom to use the Australian company’s Wireless Electric Vehicle Charging (WEVC) system. The Speedtail is the first vehicle in the world to incorporate it. Although inductive (or wireless) charging is becoming more common for phones, smartwatches and other small devices, Lumen Freedom’s wireless system for the Speedtail represents a unique solution for EVs, according to the comapany’s General Manager Rod Wilson and software team lead Radek Pesina. For Lumen Freedom, the Speedtail project is just the start. Its production-ready system has the potential to transform automotive design, transportation and even the power grid. So what does the future hold for the Australian EV industry? Moving forward, I expect to see an ‘OEM-isation’ of the EV industry. We will start to see the industry moving from large players, such as Tesla, doing everything itself (because as one of the pioneers of the industry, it had to invest in its own R&D – especially in battery development) to a more traditional model, in which the traditional large manufacturers assemble components from specialised suppliers. We’ll continue to see growth in Australian start-ups innovating in areas such as battery techonology, battery management, motors, controllers, wireless charging plates, solar charging roofs and so on. We will also see, as volume rises and technology improves, the EV industry diversifying from high-volume passenger cars to specialised industry-focused vehicles or even “restomod” electrification of existing vehicles. For example, more and more small suppliers, including in Australia, provide crate electrification conversion to either classic cars or industry-specialised vehicles. Australia has a unique pool of engineers and researchers who can combine experience and expertise in electrification, automotive and industry. I don’t think we will see a major car manufacturer coming back to Australia soon, but we can certainly expect a thriving EV supply chain and specialised EV industries here thanks to our engineering excellence, our unique needs and our immense potential.
Stephane Marouani is Country Manager – ANZ at MathWorks au.mathworks.com

Monash University and BiVACOR (based in the US, with R&D/ software facilities in Qld) are leading a consortium to develop and commercialise the world’s first durable total artificial heart. It is a completely new design and could revolutionise the use of artificial hearts. Instead of trying to replicate the way a real heart pumps, the device uses a single spinning disc to drive blood to the lungs and body. With the high-tech rotary pump levitating between magnets (MAG), there’s virtually zero mechanical wear. The left and right vanes are positioned on a common rotor to form the only moving part: a magnetically suspended double-sided centrifugal impeller. The lack of other moving parts means the rest of the heart can be made from ultra-robust titanium. The Artificial Heart Frontiers Program will develop and commercialise it. This will be achieved initially with the Australian-born BiVACOR Total Artificial Heart.
Hospital Health/Science Focus/mixed
USA: Wooden knife three time sharper than stainless steel
The sharpest knives are made of either steel or ceramic which must be forged in furnaces under extreme temperatures. Now, engineers have developed a more sustainable way to make sharp knives: using hardened wood. The method makes wood 23 times harder, and a knife nearly three times sharper than a stainless-steel table knife. The material can also be used to produce wooden nails as sharp as conventional steel nails. Unlike steel nails, the wooden nails are resistant to rusting. Wood is made up of only 40%–50% cellulose, with the rest consisting of hemicellulose and lignin. The team removed the weaker components while not destroying the cellulose skeleton. After removal of the lignin, wood becomes soft and flexible. Heat and pressure is then applied to the chemically processed wood to densify and remove the water. After the material is processed and carved into the desired shape, it is coated in mineral oil to extend its lifetime.
University of Maryland
Hong Kong: Supreme titanium alloy properties through AM
Scientists have successfully developed a super-strong, highly ductile and super-light titanium-based alloy using AM. Metallurgists consider a lack of uniformity (heterogeneity) in alloys undesirable because it results in bad properties such as brittleness. However, the team found that a certain degree of heterogeneity can actually produce unique microstructures that enhance the alloy’s properties. Their method involves the melting and mixing of two different alloy powders using a focused laser beam. By controlling parameters during the 3D printing process, the team successfully created the non-uniform composition of the elements in the new alloy in a controllable way. The resulting alloy is very strong but ductile and lightweight. While stainless steel is generally 7.9 grammes per cubic cm, the new alloy is only 4.5 grammes per cubic cm (40% lighter). These excellent properties are promising for structural applications such as the aerospace, automotive, chemical, and medical industries.
University of Hong Kong
Australia: AM – Developing high strength wire coil
AML3D is disrupting metal part supply chains using patented Wire Additive Manufacturing (WAM). The company recently partnered with the Institute for Frontier Materials to develop high strength wire feedstock alloys suitable for high strength wire feedstock 3D printing and welding markets. The partnership will support specific designs of alloys that will deliver high strength wire coil for printing, with no need for subsequent post-processing. The new technology is anticipated to open new target industries. For example, AML3D and Deakin’s recent high strength aluminium–scandium wire feedstock project targets expansion into the marine, defence and aerospace sectors, with opportunities existing in the Asia Pacific, European and North American markets as well as creating opportunities for bespoke wire feedstock sales.
AML3D
Australia: Unbreakable glass
Cracked phone screens could become a thing of the past thanks to breakthrough research to produce next-gen composite glass for lighting LEDs and smartphone, TV and computer screens. The innovation enables the manufacture of glass screens that are not only unbreakable but also deliver crystal-clear image quality. This is a huge step forward in perovskite nanocrystal technology as these nanocrystals are extremely light, heat, air and water-sensitive. And previously, researchers were only able to produce the technology in the bone-dry atmosphere of a laboratory. The team developed a revolutionary process to wrap or bind the nanocrystals in porous glass to stabilise the materials, enhancing efficiency and inhibiting the toxic lead ions from leaching out. Millions of tiny holes are injected with the nanocrystals and stay protected, wrapped inside. The technology is scalable and opens the door for many applications.
University of Qld/ABC
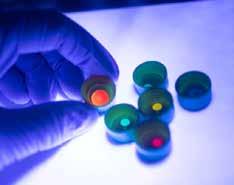
Researchers at the Uni. Of Qld are developing a process to embed perovskite nanocrystals into glass
Canada: Liquids moving without fluid loss
A newly developed polymer coating that allows for certain liquids to move across surfaces without fluid loss could usher in new advances in a range of fields, including medical testing. The new technology can directionally transport not only water droplets, but also low surface tension liquids that easily spread on most surfaces. The innovation has important implications for microfluidics, a field where small quantities of liquids are transported within tiny channels, often less than a millimetre wide. This technique has many applications, one of them being to miniaturise the standard analytical tests that are currently preformed in chemical laboratories. The new coating enables low surface tension liquids to be transported over distances of over 150mm without losing any of the liquid, about 15 times longer than currently possible.
Australia: Cosmic rays - Solving deadly mining problems
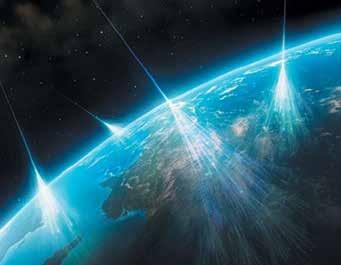
Mining tech startup mDetect - a spin-out from Swinburne - has received a $1.5m grant from the AMGC to commercialise its worldleading solution for one of the most dangerous and environmentallydamaging problems in mining globally: the failure of tailings dams (in 2019, 270 people were killed in Brazil due to a tailings dam collapse). Until now there have been no detectable early warning signs from deep within the walls. mDetect uses sub-atomic particles from space (muons) to detect weaknesses in dams; patenting new detectors, that scan solid rock, revealing different density structures. Muons are made when cosmic rays slam into atoms in Earth's atmosphere. They travel far before decaying - passing through almost any substance and penetrating far below the Earth’s surface (potentially down to 2km). OZ Minerals will deploy the device at their tailings dam at the Carrapateena Province in SA and commercial opportunities in other fields have been opened.
Swinburne and mixed
USA: Self-healing cracks in ceramics
Researchers have discovered that a class of ceramics called MAX phases (which are uniquely layered), can self-heal cracks even at room temperature. They have shown that these engineered ceramics form natural faults or kink-bands during loading that can not only effectively stop cracks from growing, but can also close and heal them. So far, self-healing of cracks in ceramics has only been achieved at very high-temperatures by oxidation and that is why self-healing of cracks at room-temperature by kink-band formation is remarkable. When the researchers viewed the deforming sample while applying loading, they observed that there were kink-band- like defects that formed in the material. More interestingly, they discovered that the material within kink-bands rotate during loading which not only form a barrier against crack propagation but also eventually close and heal the cracks. “We have had self-healing soft materials and polymer composites, and now, remarkably, ceramics” said Program Director Siddiq Qidwai.
Texas A&M
UK: New solder extends life of EV electronics
A new form of solder made with the addition of microalloying elements and nanoparticles is expected to extend the lifespan of electronics in Electric Vehicles (EVs). The weakest link for electronic devices are usually the solder interconnects. Lead has traditionally been the base metal of solder but, due to its toxicity, is nearly phased out. Its most common replacement – an alloy of tin, silver and copper – currently presents a big technical challenge due to the high operating temperature in EVs. The team is working on a leadfree solder that doesn’t degrade under high temperature; achieving this by adding nanoparticles and micro-alloying which enhances the properties of solder and reliability of solder joints. Early results indicate the new materials should be more resistant to cracking over a product’s lifetime operating in a harsh environment.
Liverpool John Moores University
USA: A robot that finds lost items
Researchers have developed a fully-integrated robotic arm (RFusion) with a camera and radio frequency (RF) antenna attached to its gripper. This fuses visual data from the camera and signals from the antenna to find and retrieve objects, even when they are buried and fully out of view. The prototype relies on RFID tags, which are cheap and battery-less. Because RF signals can travel through most surfaces, RFusion is able to locate a tagged item within a pile. Using machine learning, the robotic arm automatically zeroes-in on the object’s exact location, moves the items on top of it, grasps the object, and verifies that it picked up the right thing. The camera, antenna, robotic arm, and AI are fully integrated, so RFusion can work in any environment without requiring a special set-up. This could have many applications in manufacturing and warehouse environments.
MIT
“The heart device is unlikely to fail, and the patient is able to rely on their implanted artificial heart to pump the blood they need for the rest of their life.” Daniel Timms, CEO and founder of BiVACOR. The company has raised a further $22m to develop its world-first durable total artificial heart as a viable alternative to heart-transplantation for end-stage heart failure. The company is poised to take the technology to the first Australian patients.
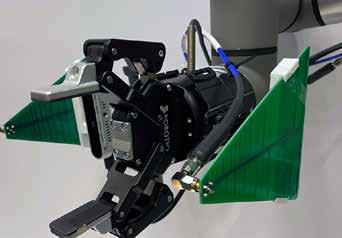
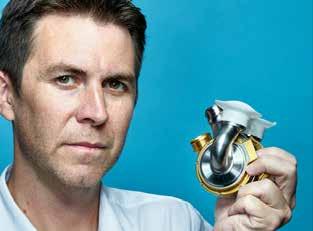