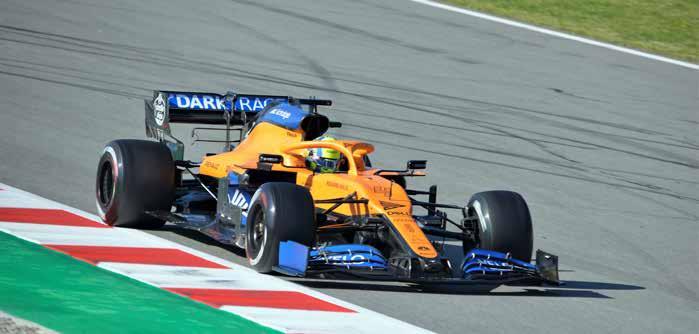
8 minute read
How 3D printing makes McLaren go faster
from AMT DEC 2021
by AMTIL
Since its founding by Bruce McLaren in 1963, McLaren Racing has relied on state-of-the-art manufacturing technology, so it was no surprise when it teamed up with Stratasys to push its use of additive manufacturing (AM) to the next level.
The competitive nature of Formula 1 (F1) racing pushes teams to develop the best solutions possible in their quest to reach the winner’s circle. Using tools like AM, F1 racing has become an inspiration to other enterprises on how to maintain the lead in their own industry. In F1, every gram of weight is critical. But simply cutting weight is not the only thing the McLaren team has to watch out for. The safety of the driver is of utmost importance as well. For this reason, it’s crucial for engineers to ensure they are meticulous in their approach regarding how loadbearing features of the car’s suspension are bonded together. Too much adhesive and the car will be slower, giving the other teams a chance to pull ahead. Too little adhesive is not an option either. In one clever example, McLaren printed clear surrogate suspension parts to practice the bonding process. The clear material lets technicians see how the adhesive spreads when parts are pressed together and provides visibility to the integrity of the bond joint – something that’s not possible with opaque materials. They can refine the technique with the right amount of adhesive, safeguarding against an insufficient amount but also eliminating excess weight. By taking advantage of the VeroUltraClear material on the Stratasys J850 PolyJet printer, McLaren successfully used transparent 3D-printed test parts to ensure their bonding processes are accurate before the final components enter production. Using AM for innovative solutions like this helps McLaren finetune manufacturing processes, reducing costs. “This tool allows us to quickly verify the bonding process integrity between a composite suspension wishbone and its mating metal end fitting,” says Neil Oatley, Design & Development Director at McLaren. “Using AM, rather than machining metal or polymer, allows us to achieve a component quickly with less personnel involved. Less time, fewer people, less material, less wastage.” The J850 printer enables McLaren to create high-resolution wind tunnel models for aerodynamic research. The technical team uses them to make small mechanical adjustments to prototyped parts. This results in a race-ready car faster than testing iterations on full production vehicle components. Using PolyJet technology gives McLaren the ability to reduce time from initial design to physical part, and offers something other technologies cannot – flexible, durable parts. The flexibility of certain PolyJet materials allows the team to make small mechanical adjustments in the wind tunnel to find ideal solutions without having to rebuild the parts. Using GrabCAD Print software, engineers can vary the stiffness of different regions of the model. This adjustability reduces time spent producing and finishing parts for the wind tunnel and allows more time for designing and testing. “Speed is as crucial off the track as it is on the track,” says Piers Thynne, Executive Director – Operations at McLaren Racing. “An F1 car is made up of around 16,000 parts and on average, one part is upgraded every 15 minutes, so speed of production is really key. From the traditional first race of the season in Australia to the final race in Abu Dhabi, we expect 85% of the designed parts of the car to change. It is a constant race against time not only on the track but in the factory too.” Printing production parts
Like other race teams, McLaren uses composites for aerodynamic parts of their racecars because they’re lightweight but strong. In some cases, however, there isn’t time to fabricate these parts due to the hours required to make new lay-up tools and cure the composite material. The need for alternative parts that are light but strong and stiff led McLaren to employ 3D printing instead, using FDM Nylon 12CF material. This composite thermoplastic contains chopped carbonfibre, resulting in parts with exceptional strength and rigidity. Although traditional composites may result in a lighter part in some cases, the time savings afforded by 3D printing makes the extra weight worth it. In one example, McLaren was able to go from CAD model to physical part in just five days, for a task that previously took 29 days. Instead of racing with inadequate parts on their car for numerous races, engineers were able to have optimised 3D-printed parts on the vehicle for the next week’s race. 3D printing saved approximately 25% in cost compared with
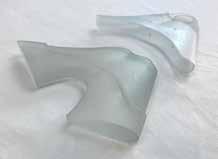
traditional counterparts. This improved workflow means McLaren can replace critical components in time for the next race, increasing overall performance and reducing expenses. Composite 3D-printed parts must go through McLaren’s rigorous quality tests just like their traditional counterparts. The value of 3D printing and GrabCAD Print software is the ability to adjust print settings as needed to optimise the part, and makes it extremely easy to assign different toolpaths to individual portions of the CAD model. GrabCAD Print works with all common CAD formats and allows users to leave manufacturing notes on the part to help with communication between engineers and machine operators. The bottom line: Cost
For many manufacturing businesses, time is important but ultimately cost is king. McLaren F1 has found that 3D printing production parts turns the economics completely on its head. It’s not only faster to print, but in some circumstances, it’s cheaper. The reason lies in the fact that by eliminating tooling from the manufacturing process, a major source of cost has also been removed. This was the case in the development of front brake ducts that help channel air into the braking system and manage the flow entering the front of the car. These parts not only resulted in a 60% faster lead time but were also 86% cheaper. F1 cars are noted for their aerodynamic features. They enhance performance by providing additional downforce to keep the car stable, create dirty air to disturb competitors’ cars, and cool heat-critical components. However, when the car isn’t moving, certain components still need airflow. Since the vehicles do not have large radiator fans like those found in production automobiles, they need forced supplemental airflow when the car is parked. McLaren cools the rear of the engine bay using 3D-printed parts. They’re used when the car is stationary, such as when in the garage, between practice runs, or prior to the start of the race. To neatly interface with an electric fan inlet, McLaren prints parts that mate appropriately into the original design of the car. This keeps the engine and its airflow-dependent components from overheating and damage. McLaren produces only two or three sections of their duct design per year. Instead of resorting to traditional manufacturing processes such as composite assembly or metal fabrication, they save time and expense by 3D printing them. “Essentially this allows us to build a very complex part quickly and without tooling,” Oatley explains. “We can iterate design details to hone in on the best-performing ergonomic solution very quickly without investing in multiple tooling options to arrive at a final design, before we commit to long term production composite components.” Tooling
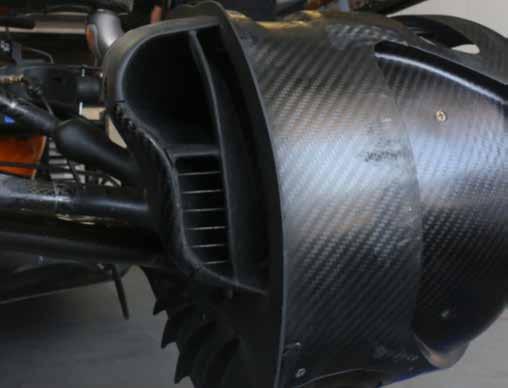
Every profession has specialised tools, with equally specialised price tags. F1 racing is no different. One such tool is the wheel gun, which removes and installs the car’s tires during a pitstop faster than you can blink. This tool needs to function efficiently and repeatedly since the average pitstop is about 2.5 seconds. In F1, a few extra milliseconds during a pitstop can mean dropping position or losing the race entirely. It’s a critical piece of pit hardware and needs to be protected. But it also has to be ergonomic to allow the tire changers to do their job smoothly and without strain. To achieve both goals, McLaren 3D printed a custom wheel gun shell. Rugged FDM thermoplastic material prevents the expensive electropneumatic gun from being damaged as it’s moved around the pit area. Along with that, 3D printing’s design freedom lets McLaren configure the shell for maximum comfort and usability. It’s a perfect example of how FDM technology is a good fit for tooling, satisfying multiple objectives: protection for equipment; lightweighting for easier usability; and easy customisation for ergonomic comfort and safety. This type of application is not limited to tool covers, but also fixtures such as conformal soft jaws and testing equipment. McLaren has learned the only thing that limits the application is the imagination. Some of the more difficult parts to make on F1 cars are composite tubes and ducts. Fabricating these parts usually requires complex tools or clamshell moulds. But both methods have drawbacks and in some cases, the parts can’t even be made with traditional tooling. In this situation, McLaren uses sacrificial cores to make the parts. The soluble core forms a mould of the duct’s internal shape, and is 3D printed using ST-130 sacrificial tooling material. The mould is then wrapped in carbonfibre. Once the composite material is cured it’s immersed in a dissolution tank where the sacrificial mould dissolves, leaving behind the desired composite duct. This application is a fast, simple way to make small batches of custom, high-performance parts and is a great alternative to the time and cost of making traditional tooling. McLaren maximises 3D printing’s capabilities to get better results and go faster. But it’s not some specialised technology limited to only F1 racing teams. Rather, it’s a tool that virtually any business in any industry can leverage to improve processes and ultimately, the bottom line. McLaren exemplifies how 3D printing benefits one company. But any business could just as easily reap the same advantages.