
5 minute read
Lorch – Bringing cobot welding to ANZ
from AMT DEC 2021
by AMTIL
Lorch Schweißtechnik (Lorch) leads in the design, development and application of advanced welding technologies, operating at the cutting edge of Industry 4.0 to develop smarter solutions for tomorrow’s industrial challenges.
It is a well-known fact that the welding industry is facing a global shortage of skilled welders. In Australia and New Zealand, we know this only too well. Top welders are in very high demand and command substantial annual salaries. Many experienced qualified welders are now over 45 years of age, and Millennials or Gen Z are not queueing up to enter the industry in sufficient numbers to even replace the aging welders of today. The harsh reality is that the situation is not going to get any better in the foreseeable future. Significant demand is building for qualified welding operators in the mining, defence and manufacturing sectors. Competition for the limited welding resources is intense and requires premium rates to be paid to attract and retain the best available talent. Small to medium manufacturing businesses are finding it hard to compete in this environment, with many struggling to find and retain crucial welding personnel. Add to this the constant cost pressures and rapidly advancing technologies, and the industry faces a situation where there is a “perfect storm” building. Today, however, the game has changed, with the advent of new cobot (collaborative robot) technology. Based in Stuttgart, Germany, Lorch has had a dedicated team in place developing and optimising welding with cobots for many years now, providing cutting edge, new solutions for companies facing these issues. It’s important to note cobot welding is not a replacement for industrial robotic welding. Cobot welding from Lorch is a new technology segment that is different from industrial robots in many areas: • Size, weight & portability: Cobots are small, light and relatively portable.
They are designed to be used in the general work environment, in close proximity with people. • Safety: Cobots operate at human speed and have unique integrated safety features, enabling close interaction with people with minimal dedicated safety guards or external protection – and in some cases none. • Intelligence: Lorch’s Cobotronic software creates a simple-to-operate welding system that is typically programed by the welder or shop floor operator. • Speed and versatility: Lorch’s advanced Speed Processes deliver
Lorch’s welding cobots offer a fast, efficient and flexible welding solution that is well suited to small-to-medium businesses.
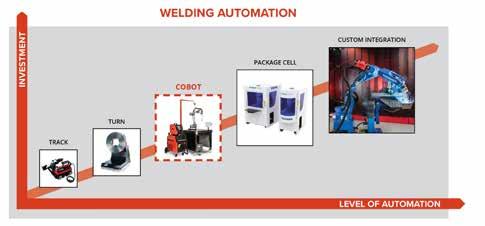
Cobot systems are typically more cost-effective than industrial robots and offer a quick return on investment.
perfect welding in all positions, removing the need for complex and expensive jigs and fixtures. • Ease of use: Fast set-up times and simple programming enable much smaller production quantities to be cost-effectively welded. • Low capital investment: Cobot systems are typically more costeffective with a quick return on investment. In contrast to a welding cobot, an industrial robot is designed for high production quantities, needs a highly trained robot technician to program, is not portable, requires extensive safety guards and barriers, and typically requires expensive jigs and fixtures. Lorch has developed a strong partnership with Universal Robots, a global leader in collaborative robot technology. What differentiates Lorch from any other manufacturer is its intelligent Cobotronic software and its advanced welding power source technology. Lorch takes the cobot and creates a purpose-built, fully integrated, ultra-safe automated welding solution. Every detail is meticulously optimised specifically for multiple forms of welding. The end result is a fast, efficient and flexible welding solution that meets the requirements of Industry 4.0 and which is ideal for small-to-medium businesses producing smaller production quantities. Lorch’s systems are simple to use and deliver dependable productivity and consistent premium-quality welding performance. Cobots are new tools that are helping to address the ongoing shortage of welders, closing the skills gap, driving productivity, efficiencies and reducing costs. Cobot welding is growing at an exponential rate across Europe. Lorch’s cobot welding solutions are now coming to Australia and New Zealand, with sales demonstration/ application and training centres set up with accredited Lorch partners across the region, as well as fully-trained Lorchcertified service infrastructure for back-+up and support. www.lorch.com.au
Magneto inspection robot wins WHS award
Perth-based robotics company Nexxis was recognised at the IFAP CGU SafeWay Awards in October, winning an award for its Magneto-EX robotic crawler technology.
The Innovation in WHS Award recognised Nexxis’ innovative technology revolutionising worker safety in industrial environments. Designed and developed by Nexxis in conjunction with CSIRO’s Data61 division, Magneto is a versatile, spider-like, climbing inspection robot able to negotiate hazardous and confined space inspections, without a human operator. The multi-limbed, spatially aware device has been created for use in high-risk settings, including the oil & gas industry – eliminating risk for humans. Nexxis Founder and Director Jason De Silveira said he was delighted with the award and paid tribute to everyone involved in the design and development of this worldleading technology: “Magneto represents a major leap in safer inspections for the oil & gas industry, as well as other sectors where there is a need for hazardous, confined-space inspections. The cuttingedge technology behind the robot enables internal visual inspection of assets and more detailed data to be gathered.” Magneto is capable of integrating intelligent autonomous control systems and is designed to carry a wide range of sensors, remote visual inspection cameras, and maintenance tools. Improved accessibility, frequency and accuracy of inspections enabled by Magneto will lead to reduced environmental and safety risks, targeted and immediate maintenance and repairs, faster decision-making and longer operational life of assets. Nexxis is focused on the commercialisation of the inspection robot, launched in August 2021 and expected to be available to the market as early as 2022. Earlier in October, Nexxis won a $675,000 Commercialisation Fund grant from the Advanced Manufacturing Growth Centre (AMGC) to assist with commercialisation of Magneto. The grant recognised the value Nexxis is bringing to resources technology and critical minerals processing, one of the Federal Government’s six National Manufacturing Priorities. Commercial production of a robot crawler that can perform complex inspections will be a breakthrough innovation in the Australian technology sector. “Our goal is to deliver leading-edge inspection, testing and measuring robots – among a range of other equipment – at fleet scale to Australia and the world across a range of industries,” said De Silveira. “The AMGC Commercialisation Fund is helping us take those next steps.”
www.nexxis.com.au
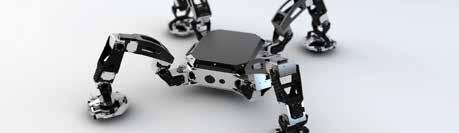
