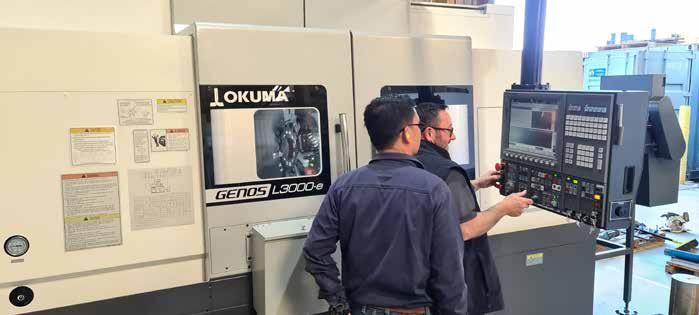
17 minute read
Upton Engineering – Performance through precision
from AMT DEC 2021
by AMTIL
Founded five years ago, the development of Upton Engineering and Manufacturing, a young Australian-owned family business based in Gladstone region of central Queensland, is soundly based on ‘Performance through Precision’.
Formed in March 2017 by Mitchell Upton, the company has made remarkable growth and now employs 25 people in a smart precision-quality engineering shop, offering the full suite of services of a modern front-line engineering and fabrication company. Upton Engineering places a strong emphasis on embracing new technologies and processes towards Industry 4.0 manufacturing, specialising in high-tolerance precision components to set them apart. The company is continually investing in the latest precision equipment. “My parents were in the precision engineering business for many years and had retired when I commenced the business, so their expertise and assistance has been an enormous help to me, particularly in the early stages, and this is on-going,” says Mitchell. “Having operated on Okuma machines during my apprenticeship and early career, I purchased second-hand machines when starting out on my own, but I have just added to these with the purchase of my very first new Okuma machine, a GENOS L3000-eMYx1000 CNC lathe with OSPP300LA-e,” advised Mitchell. According to Mitchell, his personal experience on the Okuma machines proved that they were user-friendly, solid, well setup and reliable precision machines. The back-up from the company was always professional and highly regarded in the industry. The aftermarket support even on the older machines was always excellent, and on the odd occasion when parts were required there was always a good quick turnaround on availability and service. Consequently, Okuma was a relationship he wanted to retain in the longer term. The GENOS L3000-eMY CNC horizontal lathe offers the broadest range of configurations in the GENOS lathe line. The generous Y-axis travel enhances the customer’s potential for even further productivity when machining complex parts. The GENOS lathe range also features an integral spindle for powerful, high-precision CNC machining. These onesaddle lathes are strong with a compact footprint, and are ideal for cutting a wide range of materials with ease. Built on a one-piece, cast-iron base with a horizontal way system, hand-scraped headstock and tailstock mounting surfaces, the GENOS machine provides stability, rigidity and accuracy for a variety of applications. “With the commissioning of the new machine it provides us with greatly enhanced new capability, particularly with the benefit of the longer bed length capacity,” says Mitchell. “The initial week’s training with John Baker from Okuma was fantastic, and additionally with Okuma’s 12 months bottomless training package inclusive, we look forward to taking advantage of the ongoing support from John to enhance our employee productivity with our new purchase.” The components that Upton Engineering produces on the Okuma machines are very diverse, from small items to heavy industrial components, with a constant requirement for high precision. Equally diverse is the company’s customer base, which includes clients in defence, aerospace, oil & gas, mining and resources, motorsport and energy. The advantages described by Mitchell with the commissioning of the new machine include quicker processing, increased capacity and capabilities and more processes in one operation, with timesaving benefits. 3D modelling and rapid prototyping is also integrated into the machining capabilities area of the business. “Operators on the machines are always excited with the introduction of new advanced machinery and are keen to line up to expand their knowledge and to experience the advances in technology,” Mitchell explains. “This also has positive outcomes for job security as they witness the company investing in its long-term future.” While there has been spending in the CNC machining area, investments have also been strong in the fabrication area of the business, with a heavy focus on the latest techniques, technologies and training. This enables Upton Engineering to meet a full range of Australian welding standards: AS1554:1 to 6, AS/NZS 1665, AS/NZS 3992 and ASME IX standards, with ISO in progress. Comprehensive fabrication services offered by the business include medium-to-heavy fabrication and complex assemblies, through to structural and process piping. The company’s experience covers a wide range of exotic materials, from Inconel to Bisalloy performance steels, stainless steels and higher-tensile materials – with facilities set up for largescale manufacturing and production. Now certified to ISO9001, in the final audit stages of AS9100 accreditation, and with ISO 3834 just commenced,
Commissioning the new Okuma GENOS L3000-eMYx1000 CNC lathe at Upton Engineering and Manufacturing.
John Baker, Sales-Application Engineer (QLD) for Okuma Australia, and Mitch Upton, Managing Director of Upton Engineering, with the new machine.

Upton Engineering is actively seeking new markets with an emphasis on defence and aerospace, with the added capability of new materials. To ensure that skilled trades personnel are available in the future, Upton Engineering invests heavily in training and currently has five apprentices under training. Those interested in apprenticeships are sought through close liaison with mechanical engineering students at university, word of mouth and Facebook advertising, while at the same time establishing dialogue with high school careers advisors and the introduction of students to opportunities within manufacturing through visits to the machine shop. business in the future. “Okuma Australia is actively involved in the promotion and support of precision engineering throughout Australia and New Zealand,” said John Baker, Sales-Application Engineer (QLD) Okuma Australia. “And it is exciting to see the development and energy within a young and dynamic company such as Upton Engineering and Manufacturing. Their top priority is to continually exceed customers’ expectations on quality and performance, a philosophy dear to the heart of every Okuma employee, and we wish them continued success.”
www.okumaaustralia.com.au www.uptonengineering.com.au
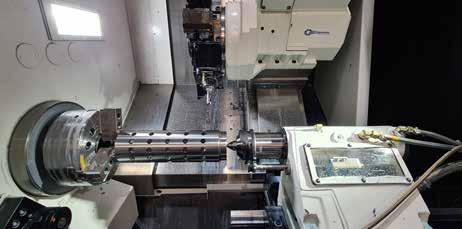
The new Okuma GENOS L3000-eMYx1000 CNC lathe in operation.
Mitchell views the current state of the economy in Queensland and across Australia as positive – especially for manufacturing in the wake of the realisation due to the COVID-19 crisis that Australia cannot and should not rely on overseas suppliers and skills. This applies in particular to heavy industry, where more and more enquiries are being received as a result of shipping delays and inconsistency of supply when relying on overseas manufactured components. Upton Engineering & Manufacturing has some exciting new projects coming up in 2022. Although it currently primarily services Queensland-based customers, there is a longer-term objective to develop export
Clearly the best Clearly the best
Industrial Door Solutions
NEW 36pp brochure now available. Contact us to get your FREE copy.
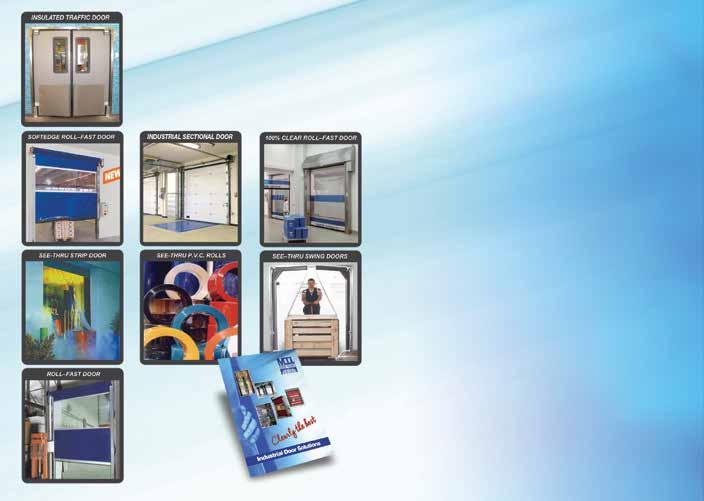
M.T.I. Qualos Pty. Ltd. are leaders in the manufacturing and service of Industrial Transparent Flexible Doors, Insulated Traffic Doors, and Roll-Fast Doors. We produce to the highest quality standard within a full range of industrial doors to suit any door application.
Contact our team today to find a solution for you.
M.T.I. Qualos Pty. Ltd. 55 Northern Road, West Heidelberg, Vic. 3081 Tel: 1300 135 539 E: sales@mtiqualos.com.au W: www.mtiqualos.com.au
Advances in modern CNC technology fuel the need for digitised tools
As advances in CNC machine tool technology continue to change the face of advanced manufacturing, the digitisation of cutting tool design is becoming more and more essential.
Rows of computerised numerical control (CNC) machine tools sharing a workspace with industrial robots that transport machined parts, accompanied by a minimal number of machine operators, are already a common characteristic of the modern metalworking plant or machine shop. CNC machines are the catalyst that created progressive advances in computer data engineering that have enabled this new reality. Advanced multi-axis machines facilitate the production of very complicated shapes with minimal set-ups. Advanced milling and turning capabilities, combined together in multitasking machines, open new opportunities for effective process planning. Innovative CNC metal cutting systems are on the verge of single set-up, full-part production – the ultimate dream of every manufacturer. A quantum leap in CNC technology is enabling a practical understanding of machining methods that had been theoretical for a long time, such as power skiving. The progress made in the world of computerised numerical control is impressive. It has impacted related spheres such as workholding and toolholding – as well as the diverse world of cutting tools. So, what are the expectations of the machine tool producers from the cutting tool producers? What are the requirements that modern cutting tools must meet? How should tool manufacturers be driven when planning their production program for the near future? The answer is simple … the next generation of tools must be better! To cut faster, to provide higher tool life, to ensure better surface finish and more. These are obvious and undoubted demands, which every tool manufacturer needs to contend with to assure its future. However, the progress in CNC technology has highlighted one more feature in tool design – the digital component. This virtual element has turned into an integral part of the cutting tools of tomorrow. The contemporary evolution of smart manufacturing is based on network technologies. In a smart factory, CNC machines perform under real-time conditions and combine mutual information exchange from an environmental context that blends both the real and the virtual worlds. The systems interact with the context via the Internet of Things (IoT).

Recent advances in the world of CNC technology have impacted related spheres such as workholding and toolholding, as well as the world of cutting tools.
For example, the real world shows the position of a cutting tool and the acting cutting forces, while the virtual world specifies 3D tool paths during an operation combined with predetermined machine stock allowance. Subsequently, the real and virtual worlds find themselves in a cutting tool where they naturally complement each other. A digital tool component possesses vast amounts of information or data. Its elements are comprised of 3D and 2D models, estimated tool life, accumulated cutting time, possible limitations such as maximum rotational speed, optimal machining data and additional essential information. Tomorrow, the gates of a smart factory will be closed for tools without such components – consequently cutting tool manufacturers have started to prepare and adapt for changes. The virtual element is now focusing on the development of new tools and tooling solutions. For centuries, technical drawings were considered a common language for defining tool features. Computer aided engineering (CAE) and CNC systems require another means for data exchange. Co-operative efforts of world specialists from various engineering and scientific fields have resulted in the creation of the ISO 13399 standard, which specifies computer representations of information related to cutting tools and their holders, which forms the lexicon base of the language. Adherence to this standard means that the platform for a tool’s digital component remains independent, and computerised systems can utilise the data seamlessly. This new standard is merely the first sign. The smart factory will require additional smarter manufacturing systems and smarter tools for these systems. Information about tool properties – such as the remainder of its tool life period, a specific tool identification, or service limitations – necessitates uniform rules for specifying the information and its computer representation – like the ISO 13399 standard, yet much more comprehensive. These will require the intensive co-operation of companies and governmental institutions. Today, a cutting tool customer expects to receive not only a tool as the physical product, but also quick access to accompanying information such as virtual assembly options for collision checks, finding the optimal tool configuration, clear machining data, and learning how changing cutting parameters will reflect on tool life. This has already formed the virtual tool component, and its significance will only grow. Iscar is aware of the key importance of tool digital elements. The company’s latest developments relate to both cutting tools
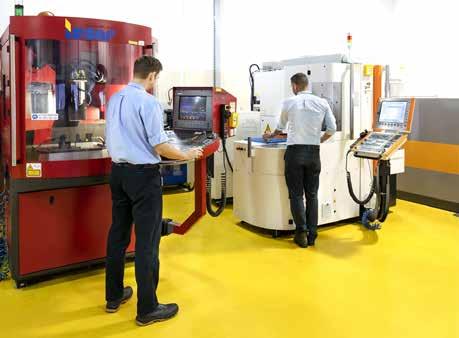
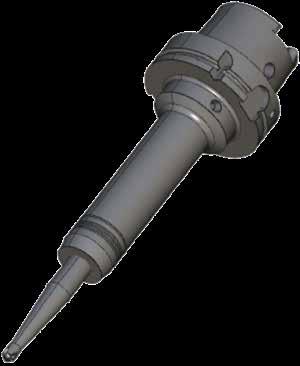
The contemporary evolution of smart manufacturing is based on network technologies, in which systems interact with the context via the Internet of Things (IoT).
While technical drawings were for a long time the common language for defining tool features, computer aided engineering (CAE) and CNC systems require more sophisticated means of data exchange.
and the tool’s informational essentials as well. Tool assembly options in 3D and 2D formats in Iscar’s electronic catalogue; Neo-Ita, the Iscar digital tool adviser; online engineering calculations; and Matrix, the automated tool dispenser that is an integral part on the shop-floors of a smart factory – these are just a few examples of the tooling virtual environment. tool assembly options, Iscar has recently introduced the turning tool assembly function, which expands the range of its electronic catalogue’s digital services. The Iscar tool adviser, which assists users in selecting the right tool, has now been rejuvenated under the brand name Neo-Ita. It features advanced analytics based on artificial intelligence and a bigdata platform. The upgraded adviser version utilises new capabilities such as new machine brands, material libraries, integrated machining calculations, and the ability to export p21 files as an integral part of tool recommendations. One more useful digital assistant is 4 PRO – an online product information and machining recommendation tool that makes tool and insert information availaible at the user’s fingertips. The 4 PRO scans the 2D data matrix barcode on an Iscar tool or insert packaging label while assuring access to the necessary data on a CNC shop floor. Diverse 4 PRO options provide product geometrical information presented in accordance with the ISO 13399 standard, and tie together inserts and tools to match up with recommended cutting speeds and feeds. The 4 PRO also bonds the insert geometry and its coating to the correct type of metal, allowing better choices at the planning stages of a given process. Intelligent CNC machines, network technologies, real-time information exchange and virtual twins of physical objects are the necessary bricks for building manufacturing in the era of Industry 4.0. Digitising cutting tools will ensure that tools will be used in smart factory environments.
www.iscar.com.au
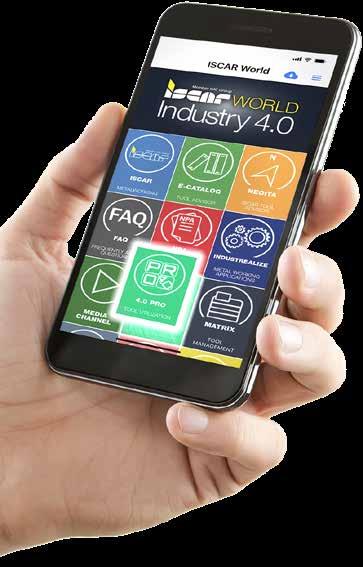
From technologists working on process planning, to engineers designing tool assemblies or preparing the tooling part of a complex key project, CNC programmers checking a tool path in a CAD/CAM environment, to application specialists optimising machining operations, and even sales managers assisting in selecting a more effective tool – all might spend hours adopting tool data from tool manufacturers to integrate with the customer’s software. Iscar’s electronic catalogue provides a digital twin representation of the tool assembly based on the ISO 13399 standard. This guarantees the successful communication between current and future software support in a digitised smart factory. The virtual assembly ensures fast, reliable simulation of the operation – as well as collision (interference) avoidance – by checking and tool path optimisation and the design of workholding fixtures. As the selected machining method affects the forces acting on workpieces, and a tool configuration influences the shape of workholding elements, simulating the operation by use of the tool assembly model may be also considered an effective instrument for jig and fixture design. In addition to milling, drilling, and threading virtual
Iscar’s 4 PRO is an online product information and machining recommendation tool that makes tool and insert information availaible at the user’s fingertips.
Keeping me up to date with our industry
AMT is one of the magazines I do actually look forward to reading, it keeps my finger on the pulse and up to date with which industries and technology streams are alive... We do receive a lot of magazines, but AMT undoubtedly is top of my reading list. The first thing that I do is write the initials of all senior management in the company to which the magazine needs to circulate to. Keep up the good work AMT.
Charlie Eilbeck, Owner EILBECK HEAVY MACHINING CENTRE
APPROX 31,500
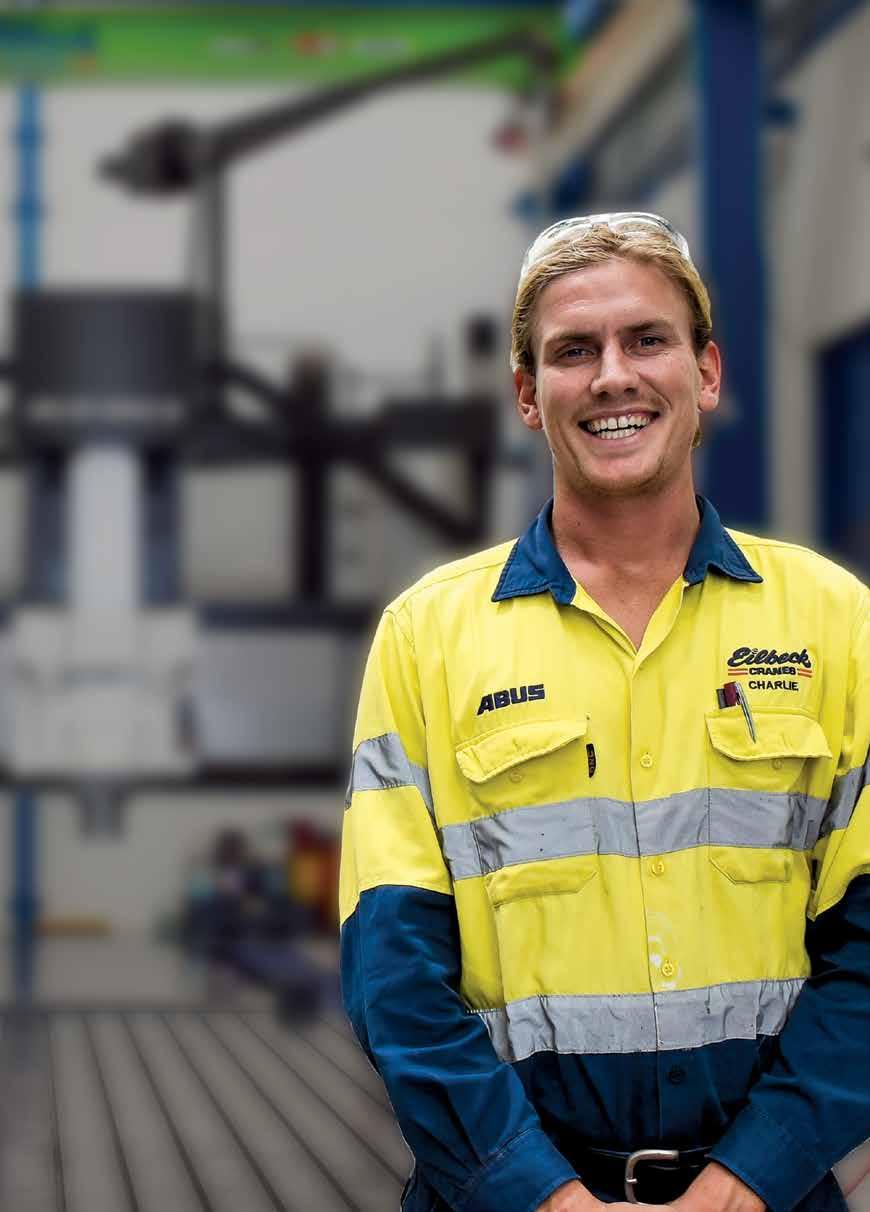
READERS
AMT the No. 1 trusted industry publication.
For information or advertising rates visit www.amtil.com.au or contact Nicholas Raftopoulos, Sales Manager on 03 9800 3666 or email nraftopoulos@amtil.com.au
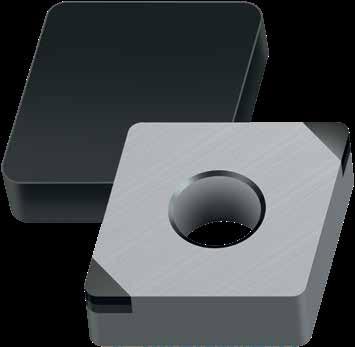
Guhring sharpens its edge
Chip jamming and swarf sticking to the cutting tool can create a major impact upon productivity and machining performance when machining soft, tough and high-alloyed materials. To eliminate this problem, Guhring has developed the new RF100 Sharp Series of solid carbide high-performance end mills.
Recognised as Guhring’s sharpest solid carbide milling tool to date, the new RF100 Sharp delivers high-quality machining results with unparalleled swarf evacuation on the most challenging of materials. Not only does the new RF100 Sharp demonstrate extremely smooth cutting action and chip removal, but it is also an extremely flexible end mill that is suitable for slotting, ramping, roughing, helical milling, finishing and trochoidal cutting. The smooth cutting action combined with the potential to be used in a wide variety of applications makes the new RF100 Sharp the end mill of choice on challenging material types. With a rake angle of 12 degrees, the end mills can be applied to materials with high ductility and tensile strength from 300 to 900N per square millimetre. This makes the four-flute end mills suitable for machining steel, stainless steel, aluminium, aluminium alloys and other challenging materials. The performance of the new RF100 Sharp is derived from a tough carbide grade that combines with an AlCrN coating to prevent tool breakages under the most demanding of conditions, while the coating technology increases the wear protection, regardless of the cutting speed. Complementing this composition is a geometry that has an optimised facet that dampens vibration, smooths the cutting action and increases tool life. This tool life improvement is further enhanced with a corner protection chamfer that increases stability and edge strength during the most difficult of machining applications. The RF 100 Sharp is available in three versions - an extra-long design long (DIN+) that is an extension on the long (DIN) version, but has an even longer cutting edge and there is also a standard length end mill. The RF100 Sharp with the standard and long (DIN) are available in diameters from 1 to 3mm in 0.5mm increments with the range including all common sizes up to 20mm diameter. Depending upon the chosen diameter, the RF100 Sharp is supplied with an overall length from 50mm to 104mm with a flute length from 3mm to 41mm. The longest tools in the range have a long neck to facilitate reaching into difficult to machine areas. With the longer series tools, the overall length ranges from 50mm to 126mm with a combined flute and neck length that ranges from 5.5mm on the 1mm diameter tool through to 75mm on the 20mm diameter variant. This increases the reach and flexibility of the series significantly, enabling end users to reach into cavities and difficult to access surfaces whilst retaining unsurpassed chip clearing. www.guhring.com.au
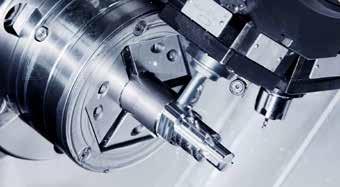
Walter presents new CBN grades
Walter has launched two new indexable insert grades for turning ISO K materials. The new WBK20 and WBK30 CBN grades have been developed specifically for the finishing of cast iron and heavy interrupted cutting.
The impressive new WBK20 grade has a grain size of just 3.0μm, which makes it perfect for the high-performance finishing of cast iron, whereas the new WBK30 with a grain size of 10.0μm makes it the perfect choice for productive turning in ISO H designated materials, especially when finishing with a heavily interrupted cut. The two new CBN grades have been manufactured from a next-generation substrate with a high CBN content that has the flexibility and durability that makes the grades suitable for rough and finish turning of sintered steels. The WBK20 indexable inserts are ‘tipped’ and this ‘CBN tip’ is securely applied to the corners of the indexable insert employing modern vacuum brazing methods. This guarantees adhesion and performance even under the most challenging of machining circumstances. In contrast, the WBK30 grade is made from a solid CBN substrate that allows manufacturers to achieve higher cutting speeds and subsequently higher productivity rates when cutting cast iron. The performance of these new arrivals far exceeds existing carbide grade indexable inserts in terms of cutting speeds and feeds as well as tool life. In addition to the high-precision manufacturing technology applied to the new grades, a strong micro-geometry on the cutting edge also contributes to the high quality, productivity and process reliability of the turning insert. This microgeometry is matched to the respective application of the Walter insert grades. Walter is offering the new WBK20 and WBK30 CBN insert grades in all of the popular ISO sizes and insert corner radii, thereby completing Walter’s extensive CBN turning range. The exciting new grades are particularly beneficial for users from the automotive industry, general mechanical engineering and the energy industry sectors.