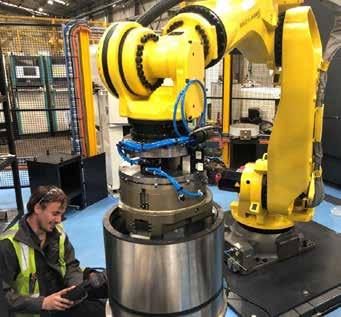
11 minute read
STATE SPOTLIGHT – WA & NT
from AMT JUN/JUL 2022
by AMTIL
Geographe shows it can machine crucial parts to rescue in real world situations.
A fully loaded live sheep transporter idles, stranded off the coast of Western Australia. The ship’s main drive coupling has failed, and to continue its passage the vessel urgently requires a splined hydraulic coupling to be made and cut in a very short space of time. Unless the repair is made quickly, a costly decision to unload the sheep will need to be made.
Cue specialist parts manufacturer, Geographe, invited to assist with the rescue of the stranded live export sheep at sea, characteristically rising to the custom manufacturing challenge to help save the day. The engineering team worked around the clock to complete the urgent work and the job was completed within five days without the need for costly unloading and reloading the ship. This professionalism, prompt response, quality of the finished product, and exceptional service is well recognised and widely regarded by Geographe’s diverse client base including in Mining, Oil & Gas, Naval, and Transport. During the 50 years since Geographe began manufacturing replacements and repairing parts in a modest backyard workshop in Busselton, WA, the company has grown to the large-scale operation it is today with multiple offices, workshops, and distribution partners across Australia. The highly skilled Geographe engineering team always strives to innovate, designing, manufacturing, and repairing parts for heavy machinery and plant equipment, reducing downtime and operating costs for a broad range of clients. Understanding that every minute of downtime costs its client’s operations, and an unwavering commitment to delivering higher quality parts at a lower price than OEMs, Geographe has earned its reputation as a trusted industry leader in the resource and industrial sectors. Geographe creates enhanced performance parts for excavators, trucks, loaders, dozers, underground drills, industrial gearboxes and more. That includes all the major OEM brands such as Caterpillar, Komatsu, Hitachi, Sandvik, Atlas Copco, and Liebherr. Because Geographe takes great pride in refining and redesigning for increased asset utilisation in many components they make, customers ultimately benefit with reduced operating costs and greater productivity across the equipment life cycle. “Innovation is key to our success, backed by 50 years of experience finding solutions that benefit our clients and the greater industry,” explains Sam Hyder, Geographe’s CEO, who is third generation family member driving the family business into the future toward a goal of saving clients $500m by 2025. This ethos is matched by the mission of Automated Solutions Australia, striving to deliver solutions. The result, a perfect union has formed, with Automated Solutions Australia partnering with Benson Machines to provide Geographe significant efficiency benefits through an automated system designed to improve throughput. Not surprisingly, in addition to a team of 140 plus highly skilled professionals, production at the South West manufacturing facility is aided by robotics. “We required a highly flexible and responsive solution to quickly and efficiently unload and load parts from two pallet locations into a DMG Mori CVG9 vertical grinding machine,” says Hyder. To meet this requirement, Benson Machines, Australia’s leading supplier of grinding machines, brought ASA and Dimac Tooling into the project to purpose build an automated cell to facilitate the grinding of a wide range of Geographe’s parts. Dimac Tooling supplied the work holding in the form of SAV magnetic chucks and zero-point locators for the chucks within the grinder, the fixture nest and around the cell at the various workstations. Benson Machines managed the automation project, but also manufactured the parts centralizing device, parts and magnet washing machine and standby stations. ASA was tasked with bringing the various items together. The solution includes rapid setup software developed by ASA that allows the handling of new parts to be setup very quickly by inputting part dimensions into the cell controller. ASA installed an automated manufacturing cell employing a Fanuc R2000iC/270F robot with a reach of 2655mm and payload of 270kg. The robot was fitted with Schunk’s Vero pallet gripper attachment to allow it to attach one of four grippers and one of eight magnetic chucks, enabling the robot to cycle parts weighing up to 150kg through the cell.


The centraliser is a three-axis device which enables a bush to be centralised on a magnetic chuck within 10 microns whilst simultaneously testing ovality limitations of the part being centralised. ASA created the centraliser function by incorporating three additional axes to the Fanuc controller, setting them up as a separate motion group independent of the robot and programming the centraliser to measure the absolute position of the part on the magnet at various points to establish both placement offset and part concentricity and to nudge the part with micron accuracy to correct the placement offset. The Fanuc R2000iC/270F robot has a payload of 270kg which means that it will handle the weight of the part, the pallet, and the gripping device. This robot can handle a mass of 175kg combined gripper/workpiece at a COG of up to 400mm in Z and X from the mounting face of the robot. ASA manufactured and supplied the overall cell controller for system. The cell controller incorporates an Allen Bradley Guardlogix safety PLC and Ignition SCADA HMI. The PLC and HMI has been programmed to provide a highly functional operator control station and diagnostic terminal for the cell. The CVG9 grinder is part of Geographe’s automation additions, and along with the FANUC robot, will play a pivotal role in supporting future customer growth alongside their recently installed heat treatment facility. The CVG9 will help sustain Geographe’s industry leading DIFOT as production demand increases. “Our talented operators have been fully trained up by Automated Solutions Australia and are currently working through grinding our current work in progress list of excavator bushes for Tier 1 miners across Australia, with great results,” adds Hyder. Geographe’s efforts haven’t gone unnoticed over the years, consistently receiving recognition through notable industry awards acknowledging business best practice, excellence in design, engineering and technology as well as being recognised for the distribution partnerships it has created. Actively servicing over 100 mine sites across Australia, Geographe works with every Tier 1 miner in the ASX Top 100 and works with a further 300+ customers in Australia and internationally. The company is well on track to meet the long-term vision of saving contracted clients a total of $500m by 2025.
geographe.com.au
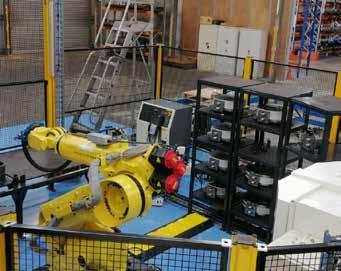
Stephanie Males and Nick Tate give a detailed opinion on the challenges of defence infrastructure in the Northern reaches of Australia in this piece reprinted from Defence Connect magazine.
Delivering infrastructure projects in the north of Australia brings an array of well-recognised challenges into play across social, economic, geographical and environmental domains. Nevertheless, ensuring that the north’s defence estate is safe, sustainable and fitfor-purpose is a critical national endeavour. PwC Australia’s Canberra managing partner and integrated infrastructure partner Stephanie Males and integrated infrastructure director Nick Tate explore what it might take to deliver adequate defence infrastructure in the region, and what success could look like. In its 2020 Defence Strategic Update underpinned by the 2022 budget, the federal government committed to strengthening Australia’s defence estate and infrastructure with significant investment over the decade, including key projects such as northern airbase resilience, upgrade of training facilities and logistics infrastructure, and new army watercraft basing. Prior to the 2020 update, much of the language about defence infrastructure had centred on consolidation of existing assets, but it will be interesting to see how this changes in the next Defence Estate Strategy update. Many of the main tenets – for defence infrastructure to be strategically aligned, affordable, safe and sustainable – will no doubt remain consistent. The 2022 federal budget papers identify that $2.6bn will be spent on infrastructure projects across the Northern Territory in coming years. From available reporting, it appears that the Department of Defence alone expects to spend at least $500m per year in the Northern Territory – amounting to close to $6bn over the next 10 years. Yet, delivering infrastructure in the Northern Territory is a very different mission compared with delivering projects of similar scale elsewhere. High transport and service delivery costs; harsh, extreme and often unpredictable weather; a sparse population; competition for skilled labour, especially highly qualified professionals; infrastructure challenges ... these are facts of life in the north. The key to success will lie in developing a collaborative, cooperative approach that responds effectively to these place-based challenges – including on-the-ground local experience and perspectives when creating plans to develop the defence estate, and engaging with the Northern Territory community as projects progress. Industry, businesses and government (both federal and state/territory) should be better aligned, use consistent data, work together more closely and seek common goals. This isn’t only about ensuring that the governance framework is right; it’s also about getting the right people in the room. An estate that is safe, secure and compliant
While infrastructure resilience is often discussed in the context of climate threats, it must also be considered in terms of security or survivability against potential threats from adversaries, from the nonkinetic, such as cyber, through to kinetic. Urban encroachment is also a concern for defence bases, as surrounding developments and environmental impacts can restrict or curtail defence activities. As an example, gas/hydrogen facilities and explosive ordinance are dangerous neighbours. With collaboration between Defence Estate Planning, local planning authorities and utilities, encroachment protection plans can be developed and enacted, ensuring functional alignment of land uses in and around defence infrastructure assets. Working in partnership with traditional custodians and owners will enable appropriate access and continuing connection to the land for traditional landowners, and identification and protection of Indigenous sites and objects in and around the Defence Estate. These partnerships are the pathway to culturally informed mitigation strategies and identifying employment opportunities on country. An estate that is developed and managed to make the best use of available resources The Department of Defence appears to be bringing forward key infrastructure projects as part of a response to increasing strategic instability. Notwithstanding the joint investment between Australia, the US and Singapore through the Force Posture Initiatives, with the resulting capital budget pressures, we are likely to see an increasing appetite to implement innovative funding models. Partnering with Aboriginal landowners is critical for successful placebased approaches to infrastructure delivery in regional and remote areas. Opportunities where Defence and the private sector can contribute to reconciliation and Closing the Gap include Indigenous employment and pathway programs, culturally intelligent workplaces, and Indigenous businesses participation and empowerment through the Defence Indigenous Procurement Policy and the Australian Industry Capability program. Greater use of joint bid approaches offers opportunities to share and balance personnel availability and maximise skills development. While defence projects have some unique aspects, actively recruiting personnel with complex infrastructure project skills grown outside of the defence sector will deliver benefits. Australia’s northern bases, ports, airfields, training areas and logistics facilities will be critical to sustaining future military operations and disaster response in Australia’s national interests and in support of our neighbours and allies. The best solutions for the future of this key infrastructure will be citizen-centred and place-based, underpinned by data-driven decisions enabled through technology. Elegant and effective solutions grow better in an atmosphere of trust – which develops through collaboration. With the defence focus now squarely on operations in the north, it is time to invest in effective collaboration across all levels of government and industry to solve the big challenges ahead for northern defence infrastructure in increasingly uncertain times. About the authors
Stephanie Males is an integrated infrastructure partner and PwC Australia’s Canberra managing partner. Stephanie has over 25 years of experience in professional services, advising on the consequences of delivering a range of public policy measures. She is also responsible for delivering regulation and facilitation services on global trade, infrastructure and supply chain advisory services across the Commonwealth. Stephanie advises governments on global trade; critical, social and environment related infrastructure strategy and their role in supporting businesses build resilient supply chains. Nick Tate is an integrated infrastructure director based in Canberra. Nick has over 36 years of experience in delivering infrastructure and logistics services for the Australian government, including national strategic infrastructure planning and managing the early government approval phases for facilities and infrastructure projects. Nick is passionate about helping project owners and industry participants realise maximum value through collaborative program management.
Republished with permission from Defence Connect. defenceconnect.com.au
#1 Industry-Trusted Magazine with over 31,000* readers BOOK NOW FOR THE REST OF 2022 DON’T MISS OUT!
APR 2022
Find emerging manufacturing technologies, new products & trends and Industry news & Opportunities… plus much more industry specific news.
FEB 2022
AMW SYDNEY 2022: WHERE TECHNOLOGY MEETS INNOVATION
AMW 2022 PREVIEW
Construction & Infrastructure State Spotlight: South Australia
AMT magazine provides companies in Australia’s manufacturing and metalworking industries with vital information on: • The latest emerging manufacturing technologies • Industry news and opportunities • New products and trends.
AMT magazine represents the interests of companies specifically in the machine tool, precision engineering and ancillary equipment sectors – whether they are manufacturers, importers, distributors, or general manufacturing technology companies.
AMT magazine is produced by the industry, for the industry, specifically focused on: • Exposing your business to the right markets • Targetting the key decision-makers • Instilling effective brand awareness • Growing your business.

For further information contact Nicholas Raftopoulos, Sales Manager on 0431 753 381 or email nic@amtil.com.au
ARTIFICIAL INTELLIGENCE: SUCCEEDING IN THE GLOBAL DEFENCE WORLD AEROSPACE & DEFENCE Renewable Energy & Clean Tech State Spotlight: Tasmania