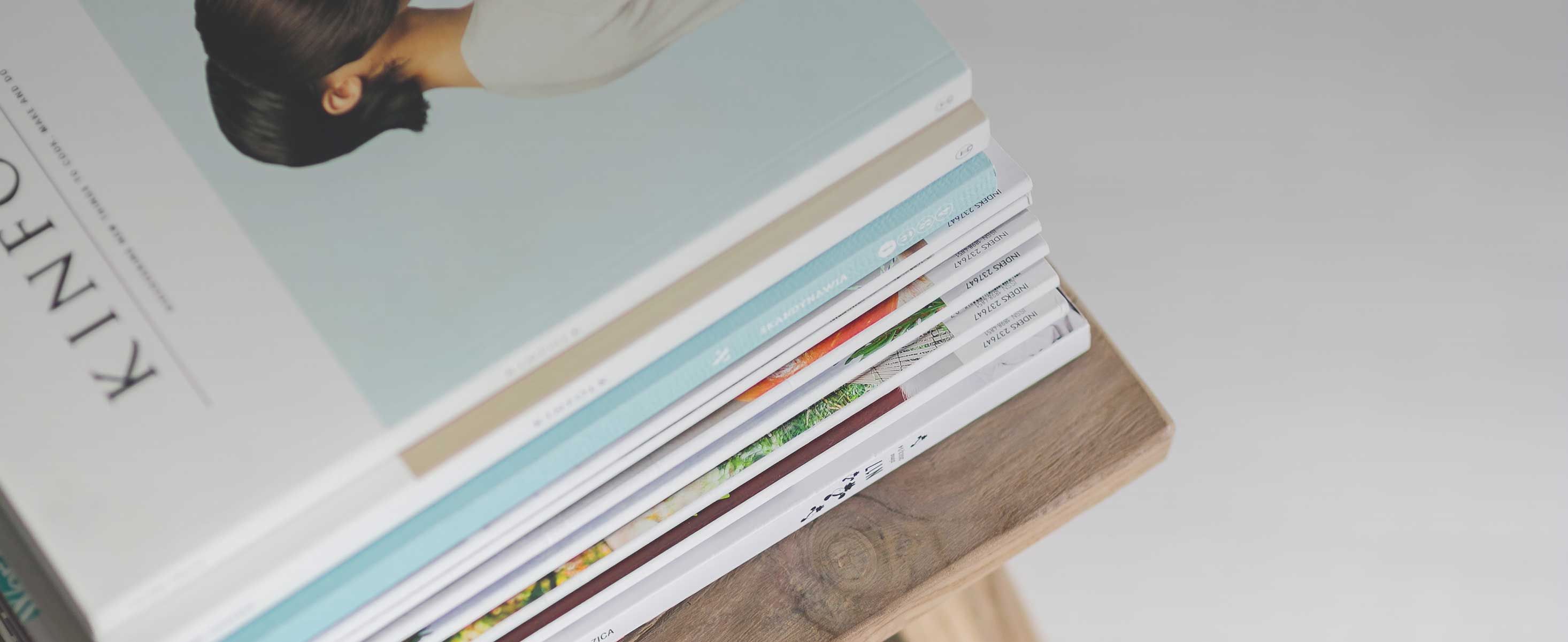
3 minute read
The benefits of optimising manufacturing inventory
from AMT FEB/MAR 2023
by AMTIL
Five ways for manufacturers to benefit from optimising inventory management systems. Rob Stummer is the Asia Pacific CEO of SYSPRO.
The rationale for inventory management is that it saves manufacturers money and allows them to fulfil customers' needs, enabling them to successfully control the cost of their operations. Therefore knowing what stock they have, what is in their warehouse and how to manage the supply chain effectively is the backbone of any manufacturing business’s operations.
Inventory management provides manufacturers with greater accuracy and visibility to inventory information throughout their business and will deliver the following four key benefits:
1. Managing the replenishment of stock
Effective replenishment is dependent on there being sufficient stock to cover demand. The inventory manager’s role is to ensure the right inventory items are ordered, in the right quantity, at the right time and to the right location.
Maintaining an appropriate inventory level is critical for both customer service and profitability. An oversupply of stock, or obsolete stock, increases business costs, and a lack of stock means customer demands will not be met.
The inventory replenishment process varies depending on the type of manufacturing business and its circumstances. Using an Enterprise Resource Planning (ERP) system to manage inventory will provide many of the necessary standard processes and rules for inventory replenishment.
2. Managing suppliers
As part of the supply chain, inventory management includes several aspects, such as controlling and overseeing supplier purchases. One of the key ways to manage this process is through the approved suppliers’ list.
Purchasing modules in an ERP system allows approved suppliers rules to be set and specific suppliers to be approved, which is a very important way to mitigate supply chain risk. The organisation knows these suppliers are compliant and will adhere to the regulations. An increased level of trust and reliability means a manufacturer can benefit in other ways, such as keeping inventory levels low. A manufacturer may have to manage many suppliers, meaning controlling spending, negotiating the best deals and mitigating risk can be time-consuming and complicated. Maintaining a preferred supplier list will help make this process efficient and straightforward.
3. Support for product traceability
There are countless examples of manufacturing businesses hitting the headlines because of problems with contamination, product malfunction and sometimes industrial sabotage.
There has never been more demand for transparency in every part of the supply chain, and increasingly it is seen as an opportunity to differentiate and grow a manufacturing business. However, having an effective traceability process takes more than updating an audit trail. Traceability is about trust, reputation, efficiency, safety, innovation, quality, staff morale and risk management. And regardless of the type of manufacturing business, effective batch traceability is cost-effective and reassuring to the wider supply chain.
A product traceability functionality enables an item to be tracked through the manufacturing process, from purchasing raw materials to manufacturing, assembly, inspection and stocking to the final dispatch stages. In the event of a recall, the organisation can identify what finished item the lot went into and who bought the items. Having traceability in place enables the manufacturer to keep track of the item being manufactured for compliance and quality assurance purposes or to view what materials were used in the production process.
4. Stock availability
Anyone who has ever shopped for a product and found it was out of stock has experienced the challenges of stock availability. For the suppliers, managing stock availability can be equally frustrating. Stock availability is a straightforward concept: It's the degree to which a business has enough inventory of each item to meet customer demand. Managing stock availability, however, is not so clear-cut. Suppliers must balance the need to fulfil orders and keep customers happy with the cost of buying and storing inventory. In addition, they must do this whilst being prepared for unexpected changes in demand and supply.
It is a tricky balance to maintain enough stock to meet customer demand without tying up too much capital in inventory, particularly when faced with supply chain issues and peaks and troughs in demand. Having an ERP system to manage inventory management will help suppliers track and manage inventory in real time, which is critical to optimising stock availability and maintaining customer satisfaction.
5. Valuation and pricing functionality
Proper valuation of inventory is important and necessary for financial reporting. Different inventory valuations or costing methods are used to calculate the cost of goods sold.
Pricing is one of the important strategic decisions a business must make, as selling goods at the correct price is important for profitability. However, there will also be a need to occasionally move stock by providing a discount through a promotion.
In addition, customers will occasionally want to negotiate a special price for a period or specified quantity. Salespeople should also be allowed to negotiate and add a discount within certain rules. An ERP system provides extensive manual and automated pricing functionality and the capability to include discount pricing terms.
The take-out
Manufacturers can utilise their ERP system to optimise their inventory management. This will help them reap many rewards by reducing their costs and increasing their profitability as a result of making their operations more streamlined and efficient.
au.syspro.com
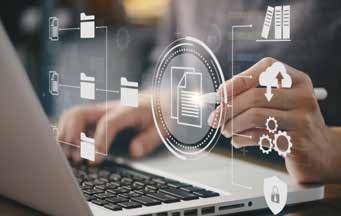