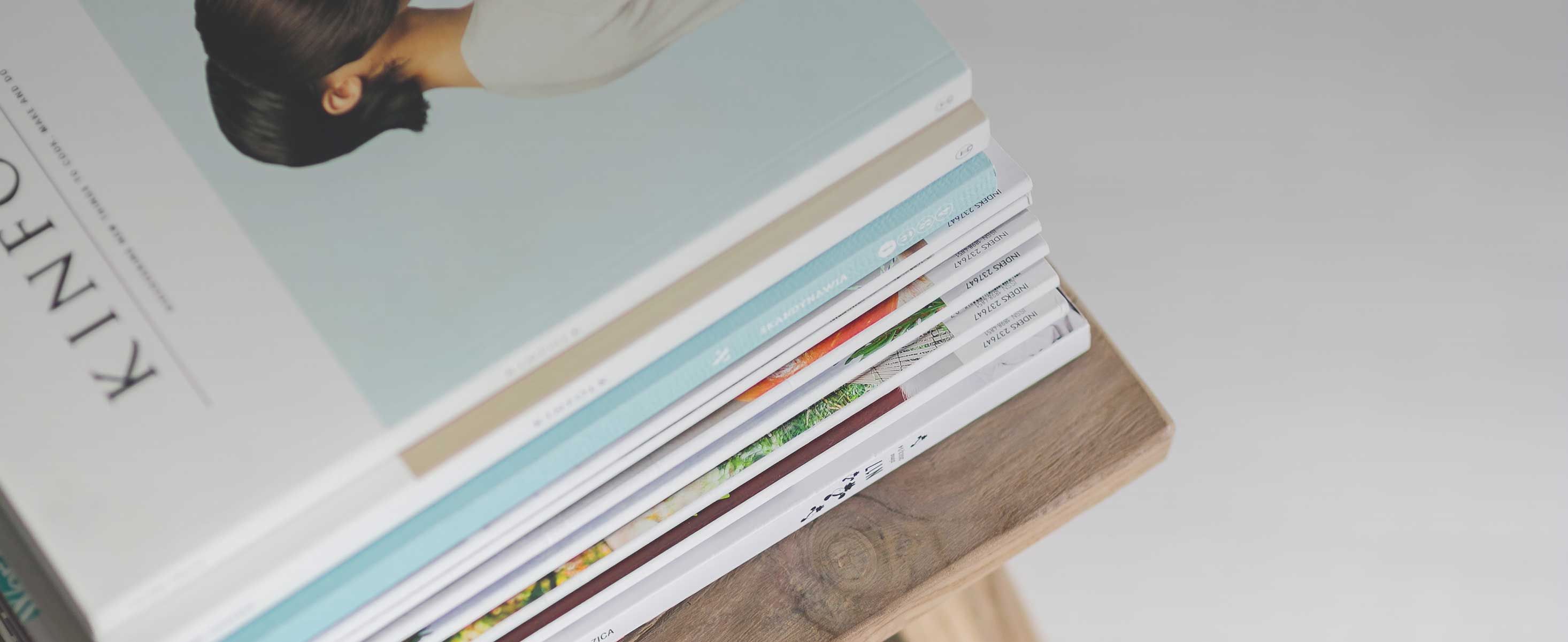
10 minute read
OPINIONS FROM ACROSS THE MANUFACTURING INDUSTRY Factory of the future
from AMT FEB/MAR 2023
by AMTIL
Empowering employees for success in the factory of the future. James McKew, Universal Robots Regional Director, APAC, and Hazel Stewart, Director of Innovate Learn, bring their skills to the table.
In an increasingly competitive global market, the Australian manufacturing sector is embracing new technology in order to thrive. Companies are investing in automation technologies, including robotics and artificial intelligence (AI), to achieve greater efficiencies and meet the demand for higher production (while keeping costs down).

The integration of new technologies does, at times, raise concerns from employees, who may fear they’ll be replaced by robots or automation.
“This is a common misconception,” says Hazel Stewart, Director of Innovate Learn, a Melbourne-based distributor of solutions from Wilson Learning Worldwide. “The Harvard Business Review puts it best: ‘technology does not purge the need for human labour but rather changes the type of labour required. Autonomous does not mean humanless.’”
“The change to new technology actually brings a wide range of new employment opportunities” , says Hazel. She points to the findings of the World Economic Forum’s 2020 Future of Jobs Report, which estimate that by 2025, advanced technologies will lead to the creation of at least 12 million new jobs. They predict increased demand for jobs such as Data and Machine Learning Specialists, but also very ‘human-driven’ professions, including Digital Marketing Specialists and Business Development Professionals.
While these findings are encouraging, they will do little to assuage the concerns of manufacturing employees who may not yet be equipped with these skills. The question for manufacturers is, how to embrace advanced manufacturing without leaving employees feeling vulnerable or alienated?
Leading the change
For the transition to advanced manufacturing to be successful, it is essential that employees are educated about the new technology, as well as its benefits and goals. Employees need to support and believe in the company’s strategic goals, explains Hazel. They need to see clear advantage for both the company and for themselves.
“The majority of employees want to see the organisation they work for succeed and they understand that sometimes change is necessary in order for the company to remain competitive,” she says. “It’s not that employees are resistant to change – but rather that they need clarity on how the change stands to benefit them on both an organisational and an individual level. It’s important that employees feel that their contributions are a valued part of the overall initiative,” she adds.
Collaboration over competition
A great point of departure in a change management initiative is to highlight the benefits afforded by automation and new technology. “Automation offers manufacturers a host of benefits: it will increase productivity, improve worker safety and efficiency, and reduce errors. Pertinently, it can reduce the burden on employees, by allowing them to channel their energy and creativity into corners of the business where a human perspective is invaluable,” says Hazel. “Robots enhance the workplace for employees by taking on dull, dangerous and repetitive jobs,” says James McKew, Regional Director APAC for Universal Robots, the specialist developer of collaborative robots for industry (i.e. robots that can work safely alongside humans). According to James, the argument that robots will take jobs from humans is an argument they regularly encounter.
Yet robotic automation, he explains, has many advantages for the workforce. Collaborative robots are freeing up people to do more meaningful and fulfilling tasks, and Universal Robots has seen this repeatedly with their customers across the globe. “Robotic automation is known to create new job titles and job opportunities within a business,” says McKew.
The automation of manufacturing tasks may facilitate the reallocation of labour costs, enabling companies to invest in the professional development of employees. This is a good opportunity to up-skill personnel, equipping them with the capabilities and knowledge they will need to thrive in an altered workplace.
An unexpected but major benefit of automation is that it is reinvigorating the manufacturing sector by making it more attractive to young candidates. The implementation of robotics, programming and automation software in the manufacturing environment, presents an exciting pathway into a sector that may otherwise have limited appeal.
Advanced manufacturing requires a broad range of skills
Technical proficiencies will be in high demand as advanced manufacturing becomes more prevalent. Yet other, more ‘abstract’ skills will be required by future-thinking manufacturing businesses that wish to thrive. Hazel lists these in-demand skills as follows:
• Learning agility. “In a rapidly changing environment where new technologies are constantly coming to the fore, employees must embrace an attitude of continuous learning.”
• Collaboration. “Creativity and innovation thrive when ideas are shared.”
• Critical thinking. “I would argue that the ability to think critically, strategise and change course with agility, is the most crucial advantage that humans have over robots.”
• Communication. “Sharpening of written and verbal communication skills will increase efficiencies, improve working relationships, and improve the output.”
• Problem-solving. “This is a skill that strengthens with practice and brings significant value to an organisation, creating new opportunities for success”.
“Change is inevitable, but once teams see new technologies for the opportunities and advantages they present, they can focus on strengthening their uniquely human capabilities,” Hazel concludes. “These capabilities will always be in demand in the fourth industrial revolution and beyond – no matter how many robots are working alongside us.” innovatelearn.com.au
USA: Scientists discover material that can be made like a plastic but conducts like metal
Scientists have discovered a way to create a material that can be made like a plastic, but conducts electricity more like a metal. The research shows how to make a kind of material in which the molecular fragments are jumbled and disordered, but can still conduct electricity extremely well. This goes against all of the rules we know about for conductivity.
Conductive materials are absolutely essential if you're making any kind of electronic device, whether it be an iPhone, a solar panel, or a television. By far the oldest and largest group of conductors is the metals: copper, gold, aluminum. Then, about 50 years ago, scientists were able to create conductors made out of organic materials, using a chemical treatment known as ‘doping’, which sprinkles in different atoms or electrons through the material. This is advantageous because these materials are more flexible and easier to process than traditional metals, but the trouble is they aren't very stable; they can lose their conductivity if exposed to moisture or if the temperature gets too high.
But fundamentally, both of these organic and traditional metallic conductors share a common characteristic. They are made up of straight, closely packed rows of atoms or molecules. This means that electrons can easily flow through the material, much like cars on a highway. In fact, scientists thought a material had to have these straight, orderly rows in order to conduct electricity efficiently.
University of Chicago
Australia: Key to success in manufacturing is differentiation through innovation in textiles
CSIRO and Textor have co-invested to conduct research into the surface treatments of textiles using plasma; understanding moisture transport via capillary action; odour reduction; and new composite web structures. This research has culminated in the invention of a novel three-dimensional fabric that is employed as a next-to-skin component of predominantly infant diapers. The fabric is highly effective in facilitating moisture movement away from the 'point of insult' and into the absorbent layer of the diaper whilst maintaining a sense of dryness, and hence comfort, to the wearer.
CSIRO's commercial engagement with Textor resulted in a new product development, in turn increasing annual gross turnover. The new material has been incorporated into the millions of nappies produced around the world by global company Kimberly-Clark.
CSIRO
France: Ukrainian professor eyes recycled concrete for the inevitable post-war build.
Viacheslav Troian has just published a scientific paper on concrete recycling alongside co-authors from ETH Zurich and Gustave Eiffel University in Paris. For some time now, building materials engineers have been crushing concrete demolition waste and using it to produce fresh concrete. This can replace up to 50% of the gravel or crushed stone required. According to Prof Troian, there is huge potential in the use of recycled concrete for the reconstruction of destroyed buildings and infrastructure in Ukraine.
As a father of four, Prof Troian was allowed to leave Ukraine as the conflict erupted. A chemical engineer specialised in concrete, he has 20 years of experience in the development of various forms of the material. Projects he has played a role in include developing the concrete mixtures for the sleepers for the Ukrainian railway, and the foundation of the safety confinement built around the damaged nuclear reactor in Chernobyl. Troian is currently working as a visiting researcher at ETH Zurich.
“Instead, what can be repaired should be repaired,” according to the professor. With this in mind, over the coming months he will be devoting his attention to the question of forecasting the remaining service life of old concrete buildings, using models developed at ETH Zurich.
GEU - Paris
USA: Medical face mask membrane that can capture, deactivate SARS-CoV-2 spike protein on contact.
The team developed the membrane, which was fabricated through an existing collaboration with a large-scale membrane manufacturer. It was then tested using SARS-CoV-2 spike proteins that were immobilized on synthetic particles. Not only could the material filter out coronavirus-sized aerosols, but it was also able to destroy the spike proteins within 30 seconds of contact.
The study reports that the membrane provided a protection factor above the Occupational Safety and Health Administration's standard for N95 masks, meaning that it could filter at least 95% of airborne particles. The new membrane builds upon the center's National Institute of Environmental Health Sciences (NIEHS) and NSF-funded activities, which have developed various functionalized membranes for environmental remediation. In contrast to passive membranes, functionalized membranes provide additional benefits by interacting with undesired particles like viruses through selective binding or deactivation.
University of Kentucky
CHINA: 3D polymers can be printed as a carbon microlattice 100 times stronger than original
Researchers recently discovered a low-cost, direct method to turn commonly used 3D printable polymers into lightweight, ultratough, biocompatible hybrid carbon microlattices, which can be in any shape or size, and are 100 times stronger than the original polymers. The research team believes that this innovative approach can be used to create sophisticated 3D parts with tailored mechanical properties for a wide range of applications, including coronary stents and bio-implants.
The team also discovered that by carefully controlling the heating rate, temperature, duration and gas environment, it is possible to simultaneously enhance the stiffness, strength and ductility of a 3D-printed polymer microlattice drastically in a single step.
CityU
Australia: New quantum computing feat is a modern twist to a 150-year-old thought experiment on ‘Maxwell’s demon’
A team of quantum engineers at UNSW Sydney has developed a method to reset a quantum computer – that is, to prepare a quantum bit in the ‘0’ state – with very high confidence, as needed for reliable quantum computations. The method is related to the old concept of ‘Maxwell’s demon’, an omniscient being that can separate a gas into hot and cold by watching the speed of the individual molecules.
They used a fast digital voltmeter to watch the temperature of an electron drawn at random from a warm pool of electrons. "This corresponded to a high certainty of it being in the ‘0’ computational state,” says Professor Andrea Morello of UNSW, who led the team. “Quantum computers are only useful if they can reach the final result with very low probability of errors. And one can have near-perfect quantum operations, but if the calculation started from the wrong code, the final result will be wrong too. This digital ‘Maxwell’s demon’ gives a 20x improvement in how accurately the computation can begin.
UNSW
Scientists at Lawrence Livermore National Laboratory in California have announced the success of an experiment at their National Ignition Facility. With analysis of the results still underway, it would be the first net energy gain from a nuclear fusion. The news was revealed by the Financial Times with information provided by sources with knowledge of the experiment. But, the claim by researchers that nuclear fusion is ’safe and clean’ is incorrect. Laser fusion, particularly as a component of a fissionfusion hybrid reactor, can produce neutrons that can be used to produce the nuclear explosives Plutonium-239, Uranium-235 and Uranium-233. It could also produce tritium, a form of heavy hydrogen, which is used to boost the explosive power of a fission explosion, making fission bombs smaller and hence more suitable for use in missile warheads.
ITER to detach and separate the mesenchymal stem cells from microcarriers and concentrate them for downstream processing. UTS
Stem cells offer great promise in the treatment of many diseases and injuries, from arthritis and diabetes to cancer, due to their ability to replace damaged cells. However, current technology used to harvest stem cells is labour intensive, time consuming and expensive. Biomedical engineer Professor Majid Warkiani from the University of Technology Sydney led the translational research, in collaboration with industry partner Regeneus -- an Australian biotechnology company developing stem cell therapies to treat inflammatory conditions and pain. Microfluidics is the precise control of fluid at microscopic levels, which can be used to manipulate cells and particles. Advances in 3D printing have allowed for the direct construction of microfluidic equipment, and thus rapid prototyping and building of integrated systems.
The new system was developed to process mesenchymal stem cells, a type of adult stem cell that can divide and differentiate into multiple tissue cells including bone, cartilage, muscle, fat, and connective tissue. The new system combines four micromixers, one spiral microfluidic separator and one microfluidic concentrator
Growing demand for sustainable materials is driving interest in companies like MolyWorks and its newly minted commercial arm Continuum, especially considering how recycled metal scrap could become the choice feedstock for companies that are kinder to the environment.
Private equity firm Ara Partners, which specializes in industrial decarbonization, made the investment. The funds will be destined to expand Continuum’s production of 100% recycled commercial metal powder to meet the growing customer demand for sustainable, responsibly sourced materials for engineered parts. Ara’s partnership will also support the company’s international growth and continued research into adjacent technologies and customer applications.
Statista Research
UK: Rail disruption caused by leaves on the line could be obliterated with a new rail cleaning system developed by researchers from Sheffield University.
In a new Network Rail-funded project, the researchers plan to install their leaf-busting technology underneath passenger services run by train operator Northern. Developed by researchers from the University’s Department of Mechanical Engineering, the cleaning system fires dry ice pellets in a stream of air at supersonic speed at the railhead, which freezes any leaves on the line. The frozen leaves are then blasted away as the dry ice pellets turn back into a gas. Expected to be installed and ready for testing on the live rail network in 2023, it will enable passenger services to clean the track when needed, particularly in autumn and winter months when falling leaves form slippery layers and make it more difficult for trains to stop and start. In 2021, Sheffield University worked with Northern to test the technology onboard an empty passenger train on the live rail network. The trials ran throughout autumn and winter 2021/2022 at speeds of up to 60mph and found that the dry ice system is more effective at removing leaves from the line, cleaning the track and reducing stopping distances, than methods currently used by the rail industry.
Sheffield Uni.