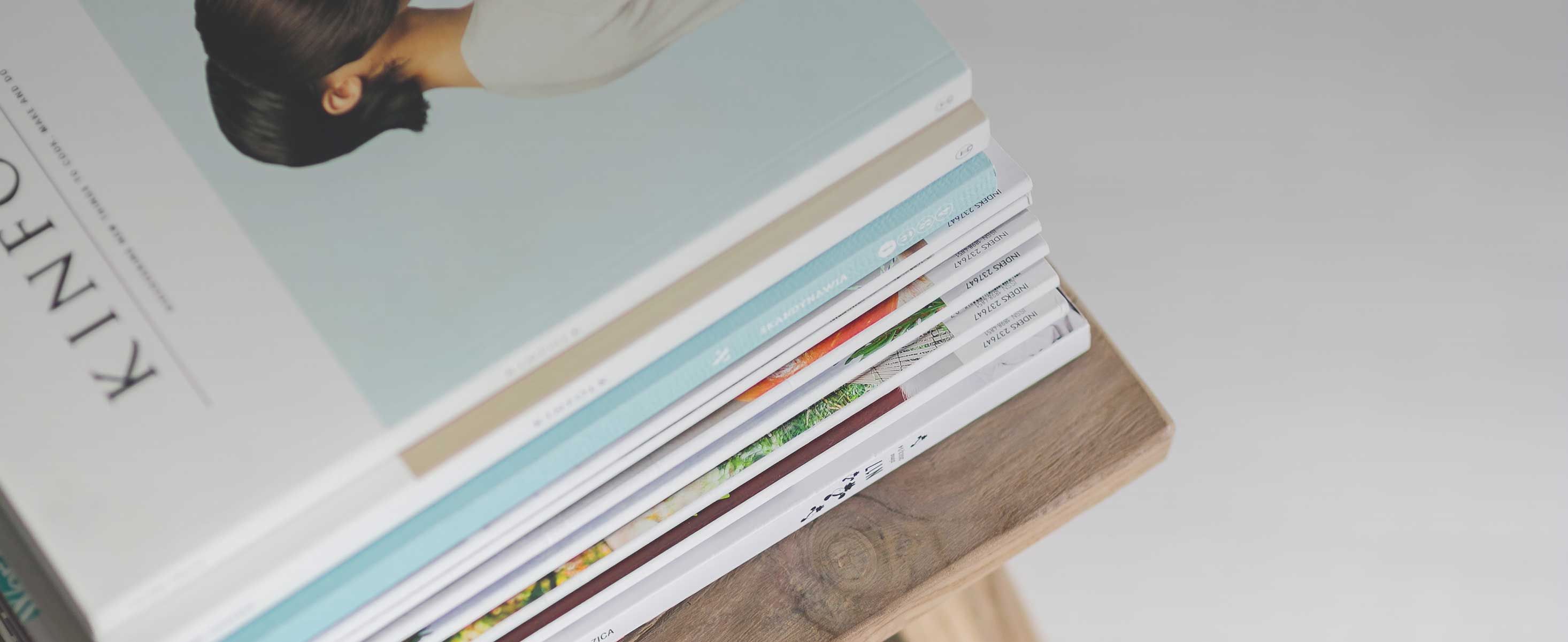
11 minute read
Councils commit to solar-driven renewable energy power plan
from AMT FEB/MAR 2023
by AMTIL
Seven New South Wales local councils have united to secure a long-term electricity purchasing agreement utilising the 115 MW Metz Solar Farm which will deliver enough renewable energy to allow the participating councils’ facilities and assets to transition to 100% renewables in a staged approach from January 2023.
All large council facilities and assets across seven New South Wales (NSW) local government regions will soon be powered by 100% renewable energy following the signing of a ten-year power purchase agreement (PPA) with Red Energy, the energy retailer owned by Snowy Hydro.
Facilitated by Melbourne-based procurements services company Procurement Australia, the agreement with Red Energy will deliver enough solar-driven renewable energy to power the electricity needs of the Wingecarribee, Albury City, Bega Valley, Camden, Penrith City, Queanbeyan-Palerang and Wollongong councils.
The renewable energy will be provided by Fotowatio Renewable Ventures’ 115 MW Metz Solar Farm near Armidale in the NSW New England region. The facility achieved commercial operation status in September and is now operating at full capacity, generating 320,000 MWh annually. The federal government-owned Snowy Hydro has a long-term supply agreement in place with the facility.
Under the 10-year PPA, the participating councils will transfer their power supply in a staged approach to renewable electricity from January 2023. Approximately 90% of the councils’ operational electricity use will be immediately transferred to the new power supply with the remaining assets to be rolled in when possible.
Wingecarribee Shire Council General Manager Lisa Miscamble said eventually all the councils’ nominated large and small market sites will be powered by renewable electricity.
“This is the largest single-emissions reduction commitment in council’s history and one of the most significant in the Southern Highlands,” she said. “We’re absolutely thrilled to be part of this historic undertaking that will see council’s largest sites transition to renewable electricity as of January 2023.
Energy Inspectors
“It’s also one of the cornerstone actions towards achieving net zero carbon emissions and leading long-term sustainability across our shire.”
Miscamble said the PPA leveraged on the joint participation from all seven councils.
“Together this 10-year agreement will ultimately see all council assets, including public lighting, powered by renewable electricity generated from within NSW,” she said. Procurement Australia Chief Executive Joe Arena said he expects the success of the PPA will deliver more cross-council contracts with work on another agreement having already commenced on the back of intensifying interest from other councils and regulatory bodies.
“This PPA is just the beginning of the work we want to do in NSW,” he said. “We’re already fielding numerous council enquiries for the next NSW PPA, and I’m looking forward to collaborating with members and the wider energy market to make it happen as soon as possible.” pv-magazine-australia.com
Article republished with kind permission from PV magazine and David Carroll.
Specialised renewable energy inspectors introduced over next 18 months.
Energy Safe Victoria (ESV) will oversee the introduction of a new class of licensed electrical inspector (LEI) specialising in renewable energy installations, over the next 18 months.
The Victorian Government has announced the new category, which will be added to the Electricity Safety (Registration and Licensing) Regulations 2020. LEIs are responsible for inspecting and certifying a range of prescribed electrical installations, such as household wiring, solar photovoltaic systems, main earthing systems, switchboards and high-voltage installations.
In recent years, Victoria has experienced a significant increase in the number of renewable electricity installations with around 56% of Victorians expected to take up new energy technologies by 2030. While the quality of renewable electricity installations is generally high in Victoria, audits have uncovered some safety risks.
The specially trained licensing inspectors will focus on renewable energies, ensuring electrical inspections are carried out correctly and comprehensively. To be granted a renewable energy inspector licence to inspect these installations, LEIs must demonstrate they have the necessary knowledge and expertise to identify unsafe and non-compliant system installations.
ESV will work closely with industry and existing inspectors as the new licence criteria is developed and rolled out. Existing G Class LEIs will continue to carry out inspections of renewable energy installations until next April when the transition will be complete. The Department of Environment, Land, Water and Planning produced a Regulatory Impact Statement earlier this year, outlining requirements for this new LEI class with submissions received between July and August this year with feedback being overwhelmingly positive.
ESV has increased its focus on the regulation of renewable energies, highlighting it is as a key compliance and enforcement priorities for the 2022-23 financial year.
“ESV is in the process of developing new requirements for the licensing of these inspectors, which will be introduced over the next 18 months,” said ESV Chairperson and Commissioner Marnie Williams. “We will be working closely with industry and existing electrical inspectors to ensure they have all the training they need to be able to carry out renewable energy inspections.” esv.vic.gov.au
Decarbonising the globe’s roads
How advances in aluminum component machining are supporting the shift to EVs.
According to a report by the International Transport Forum, global transport activity is expected to double by 2050 compared to 2015 levels. With climate change a global concern, it’s important that we produce more efficient vehicles that run on greener fuels. Here
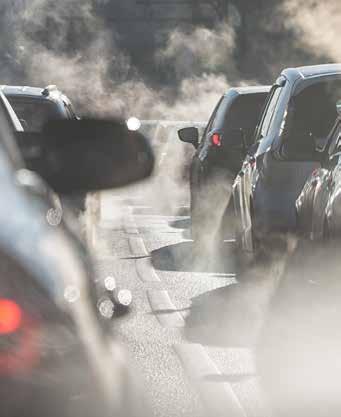
Eduardo Debone, Senior Manager for Automotive
Offer at global leader in metal cutting at Sandvik Coromant, explores how material choice and innovations in metal cutting are supporting the transition to more environmentally friendly vehicles. While COVID-19 caused a short-term reduction in transport activity, vehicle use is still set to rise over the coming decades as the global population increases and economic development continues. Producing more vehicles to meet increasing demand is inevitable — the real challenge is making them greener. The International Energy Agency (IEA) reports that transport already accounts for 24% of direct CO2 emissions from fuel combustion, with road vehicles accounting for nearly three quarters of this figure.
Management
The United Nations Framework Convention on Climate Change (UNFCCC) recognises the importance of lowering the transport sector’s emissions, and thus released its Climate Action Pathway for transport earlier in 2021. The UNFCCC’s vision is that, by 2050, passenger and freight transport will be completely decarbonised following a shift to more sustainable vehicle technologies. This shift is broken down into transitioning to zero-emission modes of transport and increasing vehicle efficiency.
The EV evolution
Among zero-emission modes of transport are electric vehicles (EVs), which executive director at the IEA, Fatih Birol, says “have an indispensable role to play in reaching net-zero emissions worldwide”. By using electricity, specially from sustainable sources, from the grid to recharge batteries that power an electric motor, EVs produce zero tailpipe emissions, and are thus a more environmentally friendly option than internal combustion engine (ICE) vehicles.
According to the IEA’s Global EV Outlook 2021 report, there were ten million electric cars on the world’s roads at the end of 2020, and EV registrations increased by 41% that year. While EVs are clearly on the rise, their adoption can be accelerated further by overcoming range anxiety, the fear that the vehicle has insufficient range to reach its destination.
And range is not just the responsibility of the battery. In addition to a more robust charging infrastructure and improvements to EV battery design, every element of a vehicle needs to be made lighter. An EV with a lower weight requires less energy to travel a given distance, and can therefore go further on a single charge, increasing its range.
Aluminum plays a large role in the light-weighting of EVs, weighing just a fraction of the more traditional automotive materials of choice — steel or cast irons. In fact, aluminum is now commonly selected for a range of vehicle parts such as the chassis, internal panels, motor housing and battery enclosures. According to the Aluminum Transport Group (ATG), using aluminum to reduce an EV’s weight can result in range gains of approximately the same proportion. For instance, if the vehicle weight is reduced by 20%, the vehicle should be able to travel around 20% further on the same charge.
Mastering machining
However, components made from aluminum are notoriously more difficult to machine. Aluminum is softer than most metals, which can make it challenging to work with. What’s more, the melting point of stainless steel is 1510-degrees Celsius, whereas for aluminum it’s 660-degrees Celsius. When machining the metal, the lower melting temperature of aluminum means that chips can build up from the heat of friction at high speeds and adhere to the tool. This chip accumulation can dull the tool, making it difficult to cut through the billet. In addition, manufacturers can face issues such as timeconsuming tool setups, inconsistent tool wear, burr formation and inferior surface finishes. Burrs and need for high speeds is also a struggle.
Fortunately, these challenges can be overcome by selecting a tool with an optimised design that’s made from advanced materials. For instance, the Sandvik Coromant M5C90 face milling tool, part of its M5 cutter series, was designed for solid aluminum parts with long milling operations, as well as roughing and finishing cylinder heads, blocks and electric car components. In just one efficient operation, the M5C90 can perform the entire machining process from roughing to finishing. In many cases, this can be with a depth of cut of up to 4mm. This tool can increase tool life by fivefold and reduce cycle time by up to 200%.
In addition, the M5 cutter series features step technology, where its extremely hardwearing polycrystalline diamond (PCD) inserts are arranged in a spiral and staggered vertically to remove material from the workpiece both axially and radially. Furthermore, the last tooth has wiper geometry to further ensure a high-quality, flat surface finish. The wiper cutting edge remains in a fixed position, which eliminates the need for time-consuming setups. Other tools in the M5 series include the M5B90 face milling cutter concept for fine finishing and the M5F90 combination milling cutter for roughing and finishing in smaller dimensions.
The transition to EVs will lower transport emissions, and adoption can be accelerated by increasing their efficiency. EVs that take advantage of aluminum components can travel further per charge, helping to overcome range anxiety. Automotive manufacturers who select machining tools optimized for aluminum will be able to produce high quality aluminum EV components – helping to support the shift to greener travel. sandvik.coromant.com
Air Histories: The
industry in Australia.
Australian manufacturing. The AMT editor
Paul Hellard sits down with Fred Funnell, President of the Compressed Air Association of Australasia.
AMT: Tell me about the CAAA.
Fred Funnell: The Air and Mining Equipment Institute of Australasia (AMEI) was originally founded in 1968, and in the late 2000s, the Industrial and Commercial members merged into one and became the Compressed Air Association of Australasia (CAAA).
The CAAA is an industry specific association for businesses, companies or other entities that are actively engaged in the sale, manufacture or import and servicing of air compressors and air treatment product in Australia and New Zealand.
I initally became involved in the CAAA as a member representative and there is no doubt the Association can provide an effective, credible voice for the industry to all stakeholders.
AMT: What attracted you to the industry?
FF: The compressed air industry is fascinating as it allows you to interact with an incredibly broad range of customers. Nearly every enterprise that’s building or maintaining equipment has an air compressor. When you walk into any factory, processing plant, hospital, car repair facility, or mining operation you will find one or more compressors running to support the business.
Most of our members operate service businesses which allow close ongoing relationships with customers after the initial equipment sale. Suppliers have the opportunity to understand their clients’ business challenges, and to help solve the end customer’s problems. Customers needs are always changing as their business adapts to shifts in the market and it is important that their compressed air systems are reviewed annually to ensure they remain optimised.
AMT: What is the most dynamic area of the Compressed Air Industry at the moment, either here or overseas.
FF: At a time of increasing power prices all suppliers are looking to see how we can provide more energy efficient solutions and continue to hone our service offerings to provide greater support. Everyone with a compressor should be working closely with their compressed air supplier to ensure the system remains optimised to meet their evolving requirements.
Compressors must operate in a varied range of conditions and the increased incidence of extreme weather events is making this even more challenging. Compressors may need to operate under full-load conditions in hot northern Australia where external temperatures may exceed 50-degrees C or in alpine conditions where the ambient temperature could be sub-zero. The Australian Government regulates minimum efficiency standards for most electric motors under the GEMS framework.
The Government is also considering changes to a range of regulatory standards as part of the journey to a net carbon neutral Australia by 2050. For us to meet the target of 43% by 2030 suppliers and end customers will need to work together.
The CAAA has estimated the emissions produced by the compressor fleet in Australia exceeded four million tonnes of CO2 in calander year 2021. While most of this can be offset by the use of green electricity, the Association members are alert to the need to gain a more granular view on the issue. The CAAA is looking to engage with all stakeholders to ensure we can contribute to a smooth transition.
AMT: What are the challenges hitting the market at the moment, from the CAAA point of view.
FF: Supply chain issues remain persistent although there have been improvments over the past six months. Safety remains a key focus as we seek to deliver even safer products and services to our end customers. The Association has instituted a National Safety Award for the industry to identify and promote best practices. The first award will be made in October 2023. Contributing to the efficient transition to a carbon neutral world is a priority.
Securing the best human talent to sustain the industry remains a challenge. The historically low unemployment rate is desirable on many fronts but does provide a challenge to companies seeking to grow. Compressor service technicians are the critical skill gap and the CAAA is developing an enhanced training programme specifically targeted at the compressed air industry. Many companies have apprenticeship programs in place.
AMT: Talk about the uses of compressed air in the industries.
FF: Compressed air has some unique attributes which makes it the best source of energy in a range of applications. Compressed air is extremely versatile and easily scaled, from small units supporting laboratory analytical instruments to massive units that provide continuous flow for minerals processing, glass making and so on. In the mining and water well drilling industry you will see compressed air powering reverse circulation drilling rigs. On the snow fields you will find compressed air powering snow making equipment, improving the snow cover and extending the season.
In the food and beverage sector, compressed air is used to actuate production lines or as feed air to nitrogen generators. Air is 78% nitrogen and can be used as an inert gas to keep the coffee in your pods fresh. Farmers use compressed air to blow down their headers to remove dried trash which, if left in place, can ignite and cause the loss of the equipment.
Compressed air can provide a flow of high speed air in wind tunnels to test aerospace components like aircraft wings and engines. Even the production of advanced composite material requires compressed air.
The motive power of compressed air can be distributed easily and cheaply through a pipe network and be safety used in high risk areas such as underground mines to drive dewatering pumps or in refineries to provide process air. Portable diesel compressors can deliver air power to remote locations or provide replacement air for stationary facilities undergoing routine maintenance. Looking across the wide range of industries, it's easier to ask, ‘where don’t you use the compressed air?’ compressedair.net.au
AMT: What does the future look like for the industry?
FF: The future of the Australian compressed air industry is bright. The trend to increased digitisation and the journey towards carbon neutrality will see a future compressor fleet that is more efficient and connected. Compressors will provide more data to the customer via IoT allowing them to better manage their assets. If a Compressored Air Technician can remotely review the fault logs, they can form a view of the probable issues and ensure they have the necessary spare parts when they service the equipment.
To support a carbon neutral Australia we will see a greater appetite to adopt a circular approach to the economy where compressors will be given a second and third life. The continual drive for digitisation, carbon neutrality and innovation will be hallmarks of the industry going forward.