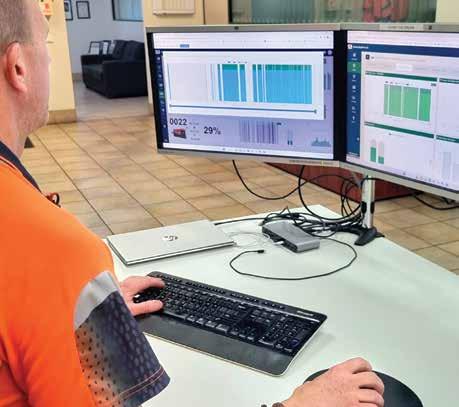
2 minute read
Sevaan Group looks to ZOOMFAB to improve production management
from AMT FEB/MAR 2023
by AMTIL
Today’s smart manufacturing firms are leveraging digital technologies and the capture of ‘big data’ via enterprise-wide software systems to aid decision-making in production and support operational efficiency, equipment utilisation, power management and ultimately organisational profitability.
The range of operational management software available to manufacturing firms is broad. They can choose to deploy Material Requirements Planning systems, Enterprise Resource Planning systems as well as specific equipment efficiency monitoring.
However, according to Ben Collins, Production Manager for Sevaan Group, for complex manufacturing operations, it is important to be able to capture enterprise-wide data processed into simple management dashboard information, as well as data about the various machine centres or individual equipment.
“Analysis of top-level data and data that focuses on individual processes and equipment is essential to understanding the overall efficiency of your operation and where adjustments can be made for improvement,” said Collins.
Sevaan Group is a Sydney-based contract manufacturing firm that specialises in precision manufacturing of metal parts for OEM customers. Sevaan’s unique and highly integrated operation consists of sheet metal fabrication, machining and finishing at scale. The plant houses a number of processes including laser cutting, bending, folding, punching, welding, machining, surface blasting and its own painting facility.
In addition to capturing data, choosing the right software solution is also critical in improving production management.
“Ensuring that the software solution you implement aligns with your business objectives is vital if you want to achieve tangible results,” said David Green, CEO of Sevaan Group.
Keen to improve their overall operational efficiency and specifically, their machine use, energy consumption and productivity, Sevaan Group implemented ZOOMFAB software.
“ZOOMFAB lets us continuously monitor and analyse our productivity levels and associated costs in real-time so that we can make shop floor decisions that improve our cost-effectiveness and profitability,” explained Green.
ZOOMFAB is an industry 4.0 productivity management application, with integrated IIoT hardware and software, advanced analytics, AI and powerful simulation tools to help manufacturers better understand and control their manufacturing operations.
At the heart of ZOOMFAB is a fully automated machine monitoring system that gathers data accurately and nonstop, 24/7. The information it captures is both comprehensive and invaluable. For instance, it can identify which machines are idling, in set- up, exceeding planned set-up, and operating or not operating due to machine fault. It measures equipment energy consumption and current, and other utilities such as gas consumption.
In the case of machine set-up, ZOOMFAB records the time actually taken to set up a machine so that it can be compared against planned parameters. This has allowed Sevaan to decrease its set-up times, while increasing output.
In addition to boosting productivity, ZOOMFAB has helped Sevaan track and reduce its energy consumption. “Energy management is becoming an important factor for all businesses. We were in the habit of leaving machines ON while they were idle, as well as overnight and over the weekend. ZOOMFAB revealed just how much energy was escaping in the process and it was considerable. We are now changing our behaviour which is helping reduce our operational energy costs.
“The software has also been very helpful when it comes to cost and pricing management as it is integrated into our main ERP system and clearly shows areas of the operation which are undercontributing to our profitability,” said Green. Impressed with the benefits derived from using the software, Sevaan is currently expanding its implementation of ZOOMFAB. “We are integrating localised iPads with the system hardware so that our operators can monitor and manage their own performance; while real-time, shop floor visibility is provided for production supervisors and managers, enhanced by regular system reporting routines,” explained Collins.
“Given the results that we’ve been able to achieve since installing ZOOMFAB, there is no doubt whatsoever that the software was the right fit for Sevaan. It has helped us streamline our processes, understand the value of each of our machines, decease our energy consumption and improve our overall efficiency and productivity,” said Green. sevaangroup.com.au