
9 minute read
ANCA’s Hall of Fame recognition
from AMT FEB/MAR 2023
by AMTIL
ANCA’s co-founders enter the Manufacturing Hall of Fame as recognition and celebration of their service to industry.
Pat Boland and Pat McCluskey co-founded ANCA in 1974 and their many achievements and business successes were recognised in the Victorian Government Manufacturing Hall of Fame 2022 awards. The inspiring pioneers have made significant contributions to driving new developments in CNC grinding technology, always surprising and delighting the precision cutting tool market with their latest innovation.
ANCA started in Pat Boland’s bedroom in Melbourne with the purchase of a $4000 mini- computer to turn their passion into a business venture. Considered mini or small for the time, it was in fact as tall as them at a cost in 1974 that could buy an inner-city apartment. Today, ANCA is for many a supplier of choice, employing more than 1200 people who are constantly innovating and finding better ways. The business has a long heritage of technical breakthroughs, investing over 10% in research and development each year to ensure their products exceed the needs of their customers in over 45 countries.
The Victorian Manufacturing Hall of Fame Awards celebrate the vital role of local manufacturing and exceptional manufacturers across the state. ANCA’s global headquarters remain in Melbourne, Australia and the company has gone global with offices in the UK, Germany, China, Thailand, India, Japan, Brazil and the USA as well as a comprehensive worldwide network of representatives and agents.
The two Pats are 'advanced manufacturing heroes' who continue to make an invaluable contribution to the precision cutting tool industry. Their latest product to hit the market, the MX7 Ultra instantly attracted market attention with its capabilities of manufacturing cutting tools of the highest accuracy and quality with a new nanometre control system and servo control algorithm for smooth motion. Their delivery of worldleading technology for over four decades continues to inspire many both inside of and outside of their company.
Where did ANCA start? Turning a dream into success
The enduring partnership of this dynamic duo is due to their complementary skill sets. Nuts-and-bolts practicality on one side, and academic, computational skills on the other. The result - is a recipe for success.
Pat McCluskey is an award-winning technician trained in the state-of-theart machine tools and Pat Boland is an Electrical Engineer with a First degree from renowned Melbourne University. They had a shared passion for building machines and a conviction they could do better than the numerical control (NC) equipment they were working with.
“When ANCA started we were obviously just a local company working in Melbourne, today, we are really deeply multinational,” said Pat Boland.
The importance of software, a global outlook, and supplying a highly specialised niche product have been key to ANCA’s achievements from the beginning. Targeting the field of CNC tool grinders, they decided that the future of the company lay in exporting to the world. Now, ANCA competes and wins on a global stage for the tool and cutter grinding machine market. More than anything else what has driven ANCA’s growth over the past 48 years has been a series of innovations that have revolutionised the production of cutting tools and have impacted the whole of manufacturing.
ANCA has 38 patent applications globally, from seven patent families in the fields of mechanical engineering, electrical engineering, and software. Competing internationally has created a continuing focus on innovation and to be first to market with new and better technical solutions.
As ANCA designs and manufactures its own machines, control system, and software, the company is able to provide innovative solutions for key components such as CNC controls, spindle and servo drives.
Technology is part of ANCA's DNA
“We didn’t go into business to in effect to make money,” explained Pat McCluskey. “We went into business for the excitement of it, and because of the technology – we wanted to demonstrate the technology.”
“Our grinding machines are very, very accurate machines, very reliable. And they are the machine of choice…right through America, through Europe, Asia, Japan, Korean. And it’s because of the software and the mechanics and the fine blend of the two together…they work in harmony.”
Typical of a leader able to do what nobody else in its field can do, ANCA has achieved a long list of world firsts. These include:
• First to introduce a probe for digitising tools in a CNC tool and cutter grinder
• First to introduce a modem for support and diagnostics in a CNC tool and cutter grinder
• First to introduce soft axes for significantly simplified programming of a CNC tool and cutter grinder
• First to introduce MPG Feed for safe program debugging and testing
• First to introduce Windows-style Graphical Users Interface and Real Time Operating System in a CNC tool and cutter grinder
• First to introduce a CNC tool and cutter grinder with all rotary and linear axes being directly driven
• First to introduce industry standard Statistical Process Control (SPC) in a CNC tool & cutter grinder
• First to introduce iBurr software for burr grinding, which uses Active Graphical User Interface
• First to introduce full and true 3D simulation of the grinding processCIM3D (patented in Australia and USA) On winning the award, Pat Boland added, “Pat McCluskey and I are honoured by the winning of this award. We thank all our teams who have contributed to ANCA’s success in the global marketplace.” machines.anca.com
Harrop driving lights-out
Harrop Engineering is a true Australian success story with a rich history dating back more than 65 years, and a legendary reputation in the automotive and motor sport communities.
This reputation is built on engineering design and manufacturing excellence, which requires cutting edge technology, which is why Harrop is compelled to be driving lights-out, with a clear vision of the future.
“Ongoing investment in manufacturing and automation solutions will support our future growth,” said Tim Harrop, Harrop’s Operations Manager. “John Hart and Mazak are key contributors to our renowned manufacturing capabilities, providing world class machining equipment to provide the flexibility and agility that Harrop needs to meet our global customer needs.”
This allegiance made it natural for Harrop’s automation drive to begin with a collaborative robot machine tending solution from Agile Robotic Systems to load a Mazak Integrex j-200S and a Mazak Integrex i-200S.
Agile Robotic Systems is part of the John Hart group and draws upon a heritage of more than 70 years in machine tools and close to 40 years in automation and robotics to deliver Australian-designed and Australian-made agility to CNC automation.
A four drawer mobile Agile Robotic Systems platform equipped with a Fanuc CR-15iA collaborative robot and single three jaw gripper suitable for handing automotive parts through both Mazak machine tools, was deployed in 2019.
Each Mazak was equipped with a plug and play robot interface on a common plug allowing the robotic machine tending system to be quickly deployed to either machine. The Agile Robotic Systems platform could be pallet jack transported between both machines with simple location cones mounted in the floor for accurate repositioning.
The collaborative robot opens and closes 80kg drawers and also handles 10kg parts without compromising the collaborative safety function. The robot also manually opens and closes the CNC door eliminating the need for an expensive automated door opener.
The collaborative robot machine tending system makes for a perfect solution where floor space is limited, allowing operators to safely enter the robot’s working zone while it continues to operate.
The collaborative robot system operates on the standard Agile Robotics software platform AgileGo. With its familiar, easy to understand, state-of-the-art user interface featuring a simple to use drag-and-drop process builder system there is no need for robot programming knowledge.
These two Mazak Integrex machines feature technologies and capabilities that complement machine tool automation.

The compact size Mazak Integrex j-200S multi-tasking machine brings large workpiece capacity and makes use of two turning spindles and a milling spindle to productively process parts complete in single setups.
In addition to its cost-effective, yet high-performance turning and angular milling capabilities, the machine also offers automatic tool changing, a large machining area and convenient operation to meet a wide variety of production requirements.
The Mazak Integrex i-200S multi-tasking machine combines the capabilities of a high-powered turning center and full-function machining center to produce parts in single setups. This machine configuration features second turning spindle for Done-In-One machining and works to minimise fixtures, tools, handling and non-cut time. Additionally, the machine brings dramatic reductions in lead-time, and improves part accuracy through the elimination of multiple setups. With full 5-axis capability, the machine easily processes fully prismatic parts from solid or castings - chucked or bar fed work, round parts, or highly contoured sculptured parts.
Harrop continued their drive in 2020 and invested in a Mazak Variaxis i-700 combined with a Mazak Multi Pallet Pool (MPP). The combination offers high-speed pallet transfer and extended unmanned lights-out running.
The Mazak Variaxis i-700 features DONE-IN-ONE processing of complex 5-Axis workpieces up to Ø730 mm. It is designed for multi-surface machining delivering reduced in-process time, high accuracy and unrivalled machine ergonomics.
The Mazak Multi Pallet Pool (MPP) has an economic footprint and is controlled using the SmoothX CNC on the Mazak Variaxis i-700, which is equipped with Mazak’s Smooth MPP software application. The standard MPP stocker includes six pallets, but can be expanded at a later date with up to 18 pallets to deliver increased production capacity.
Harrop’s MPP was the very first in Australia and helped them achieve up to and over 600 machining hours per month in a very short time after their system was commissioned. That is an average of at least 20 machining hours per day, achieved despite the strictest COVID-19 lockdowns in 2020.
The success of the first solution from Agile Robotic Systems convinced the team at Harrop to invest in an additional machine tending system in 2022. The aim was to provide dedicated machine tending for each of the two Mazak Integrex machines that were sharing the first Agile Robotic Systems solution, and therefore to double the machining capacity.
A four drawer Agile Modular system incorporating a standard Agile Flex drawer chest and pedestal mounted Fanuc M-20iD/35 robot was installed to handle automotive castings and billets into a Mazak Integrex i-200S machine tool.
The Agile Modular system was reconfigured from a standard Agile Flex 35D system to meet the tight floor constraints between the machine tool and a busy walkway. The Fanuc M-20iD/35 robot is equipped with dual three-jaw grippers for parts handling and also serves as door opener to the Mazak Integrex i-200S.

A simple stretch of safety fence along with a SICK area scanner create an open and free-flowing safety space in front of the machine tool for setup and the occasional manual operation of the Mazak Integrex i-200S. In full production, the four Agile drawers are replenished from outside the safety zone so as not to impede the robotic system tending the machine. Creative use of sheet metal shut out panels allow operator access to the tool change cabinet at the front of the machine without having to stop the robot.
Collectively, the Agile Robotic Systems machine tending platforms, together with in-cycle measurement and ‘sister’ tool processes, have helped Harrop Engineering to increase machine utilisation and allow staff to apply their skills to value add activities.
In September 2022, John Hart delivered a new Mazak with lightsout capability to Harrop Engineering. A Mazak HCN-4000 with a 6-pallet changer option.
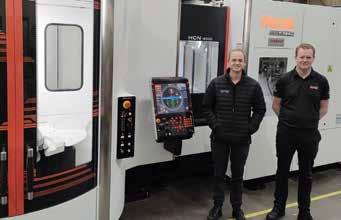
The Mazak HCN-4000 horizontal machining center features a spacious work envelope and pallet size as well as a fast rapid traverse speed and a rigid, reliable spindle. Multiple workpieces can be setup on the six pallets making unmanned operation able to be performed over extended periods of time. The pallet load capacity is 400kg (evenly distributed) with a max workpiece diameter of 630mm and workpiece height of 900mm. The pallet change time is seven seconds. Harrop have specified their HCN-4000 with a 120 tool chain magazine. The HCN’s simple, reliable automatic tool changer (ATC) performs fast tool changes over extended periods of operation and can handle tool lengths up to 420mm, tool weights up to 12kg and tool diameters up to 95mm with adjacent tools and 170mm with adjacent pockets empty.

The Australian automotive aftermarket manufacturing sector must have a bright future if Harrop Engineering is so willing to be driving lights-out!
Harrop Engineering Pty Ltd. was founded in 1955 by Len Harrop and his wife Elsa Harrop who started out producing weaving machines from a small shed in the Victorian suburb of Brunswick, Australia. As the business grew, the company expanded into other areas, including industrial food-processing equipment and heavy haulage and earthmoving accessories.
The company's current core business, the automotive performance parts business was established by Ron Harrop, the son of Len and Elsa Harrop. Ron had a strong interest in ‘making things' since his childhood, so after joining the company, he started to develop automotive performance parts with great enthusiasm. His father supported him with his technical expertise, and together they were able to evolve the new business.
Today, Len’s grandson Tim Harrop is the company’s Operations Manager overseeing the manufacturing of supercharger, differential, brake and cooling products for the automotive aftermarket globally, as well as precision components for industrial customers.
John Hart is a key player in the ongoing technology transfer to Australian manufacturers that has taken place over the past 75 years, providing the industry with the world’s most innovative and advanced manufacturing technologies including CNC Machine Tools, Automation and Robotics, CAD/CAM Software and CNC Manufacturing Accessories.
John Hart represents world leading manufacturing brands including Mazak, Fanuc, Klingelnberg, SMW Autoblok, Losma, OnRobot, hyperMILL, MazaCAM, as well as the company owned Agile Robotic Systems range of innovative CNC machine loading systems. harrop.com.au johnhart.com.au agilerobotics.com