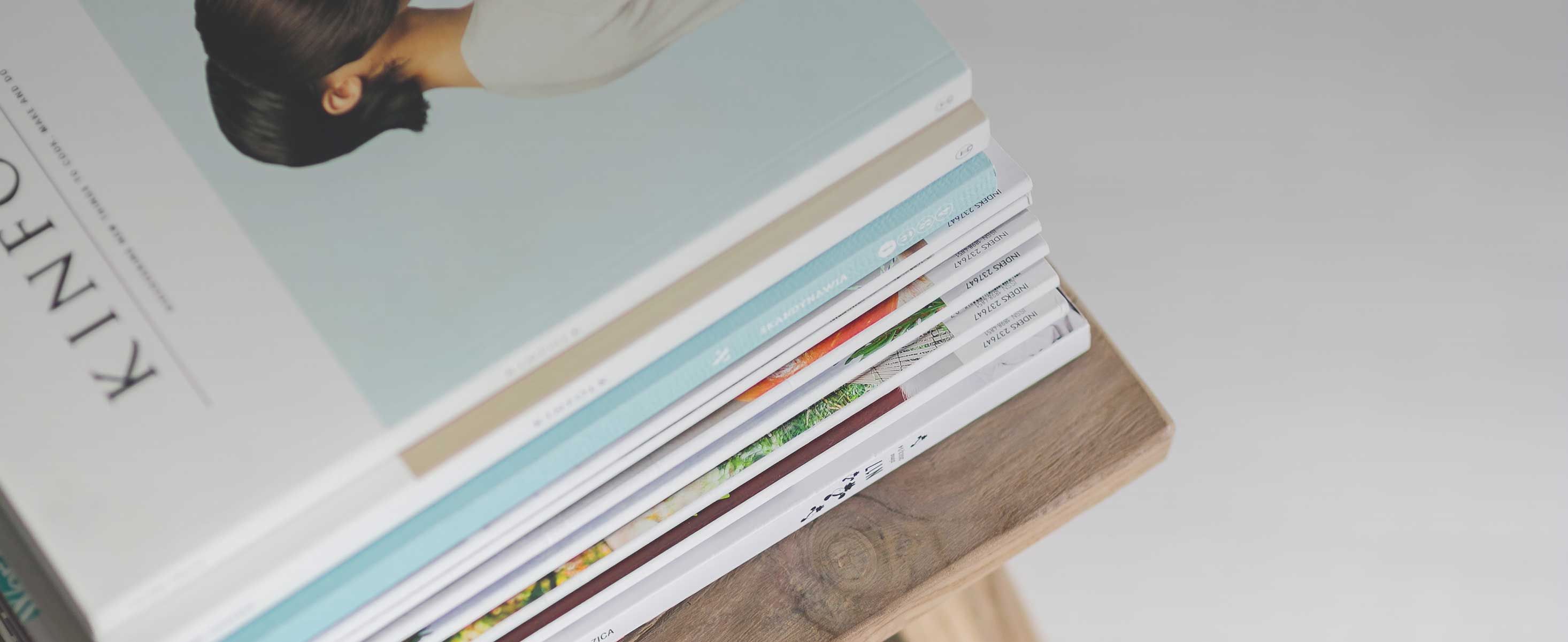
3 minute read
SYSPRO decisions
from AMT APR/MAY 2023
by AMTIL
How manufacturers can empower smart decisions that optimise operational efficiencies, increase productivity and minimise costs.

By Jaco Maritz, CEO at SYSPRO.
Manufacturers are now realising that digitalisation has the potential to fundamentally change their businesses. To ensure that Australia’s manufacturing capability is at the forefront of change and innovation in the Asia Pacific region, all manufacturing decision-makers should be moving towards Smart Manufacturing.
A Smart Manufacturing enabled organisation has all the information about the entire manufacturing process available in real-time, when and where it is needed and in the correct format to empower smart decisions.
Data analytics technologies and techniques provide a means of analysing data sets and drawing conclusions about them to empower smart decisions. Big data analytics applications integrated with an enterprise resource planning (ERP) system can enable manufacturers to analyse growing volumes of structured transaction information, plus other forms of data that are often left untapped by conventional business intelligence (BI) and analytics programs.
This encompasses a mix of semi-structured and unstructured data, for example, information from customer emails and survey responses, mobile phone records and machine analytics captured by sensors connected to the Internet of Things (IoT).
A smart ERP system provides embedded analytics that manage, analyse and process big data and provides manufacturers access to relevant and critical information from anywhere for better decisionmaking. However, to have full visibility of the whole business requires the business to be fully digitalised and interconnected.
Integrating manufacturing operations
Manufacturers must respond to demanding schedules while constantly seeking ways to lower costs, better manage inventory and streamline their processes. Add to that a constant need to innovate, as well as forecasting challenges and the ongoing pressures of supply and demand and this results in rising complexity in all areas of a manufacturing business.
For manufacturers that make-to-stock, make-to-order, engineerto-order, or employ project-centric, job shop, batch, or repetitive manufacturing approaches, they need a comprehensive ERP system to manage the entire manufacturing business that also provides them with a 360˚ view of their production.
Controlling manufacturing operations
Currently, many manufacturers are automating simple jobs and relying on people to manage the remaining processes, and this often places a heavy demand on their employees. As an alternative, a sophisticated system like Manufacturing Operations Management (MOM), implemented within an ERP solution, can help manufacturers to take control of their end-to-end manufacturing operations, without the risk of human error.
To provide more control of manufacturing operations, frontline managers need 360˚ visibility of the shop floor to prevent problems such as overruns, bottlenecks, downtime, poor employee or machine performance and excessive waste. MOM offers a unique level of delivery, cost and quality control of manufacturing operations for job shop, batch production, production line and mixed-mode environments.
With MOM, manufacturers have a single source of data and in turn, full visibility of production. Besides providing equipment status, employee performance and job status, data is digital and can be analysed to provide a predictive function to improve factory performance. Once it is adopted, manufacturers will see how quickly their manufacturing operations gain efficiency and become more streamlined, with improved quality and increased profitability.
Optimising operational efficiencies with Industry 4.0
One of the simplest ways to improve operational efficiency is to leverage automation, one of the key components of Industry 4.0. Whilst employees still need to oversee and manage production, automation can eliminate the human errors that decrease efficiency; and Artificial Intelligence (AI) and machine learning can take a manufacturing business to the next level including basic, process, advanced, and “intelligent” automation.
The key to implementing automation effectively is ensuring the free flow of data and analytics. This will encourage manufacturers to finally give up on using spreadsheets and moving to systems that automatically allow the collection, organisation, analysis and distribution of data to all departments in a business. This level of data automation allows managers to make decisions based on current information without having to worry that the latest spreadsheet is updated and correct.
When configured and used to the best of its capabilities, automation can help businesses make better quality products, improve profitability, keep workers safe and increase overall operational efficiency to help meet and exceed business goals.
A step-by-step approach
By pragmatically taking these steps and regularly iterating and improving operational efficiency does not need to be an allconsuming process. It's something that can be achieved gradually and is better-done step by step than when the business is forced to do it as a matter of urgency.
Getting buy-in from all levels of the organisation and making it everyone's job is one way to delegate responsibility during a technology transition. Keeping lines of communication open and rewarding transparency can reduce any potential problems. Once completed it will result in an improvement in product quality, increased productivity and reduced costs, which will all help businesses to retain their highly trained talent.
au.syspro.com