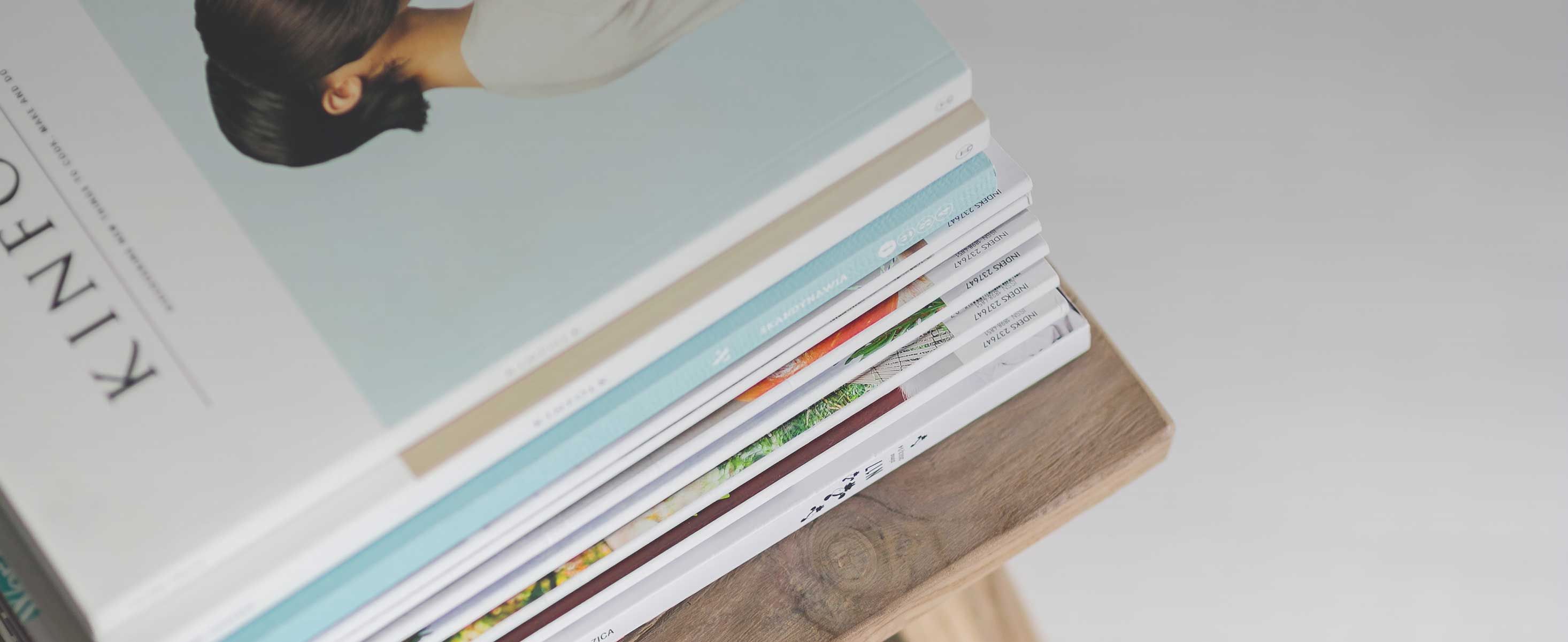
3 minute read
RMIT University
from AMT APR/MAY 2023
by AMTIL
RMIT University has outstanding research capability in Additive Manufacturing, advanced materials, industrial automation and sustainability.
Our multidisciplinary experience has been demonstrated in domains that include Defence, Transport, Medical and Energy. RMIT offers various learning and teaching opportunities in Advanced Manufacturing from online courses to short courses and industry events to Advanced Diplomas, Degree and Master’s programs. The new, expanded Advanced Manufacturing Precinct (AMP) based at RMIT's City Campus site is home to the Digital Manufacturing Facility (DMF), Micro-Nano Research Facility (MNRF) and Microscopy and Microanalysis Facility (RMMF). The newly launched precinct will provide manufacturing and characterisation from nanometre to metre length scales and digital automation technologies through collaboration with RMIT research centres and groups,
Plazmax
See the latest Plazmax CNC Controller technology.
When the team at Plazmax see there is a better way of doing things, they don’t just sit on their hands, they do something about it! In the same way they have revolutionised the plasma cutting industry with tables that are faster, more accurate and cheaper to run, they now are about to release the very latest in CNC controller technology after seeing other products in the market were falling well short of the mark.
After ten years of R&D and three years of in-house development, the Plazmax team are finally ready to release their new CNC controller software, MAX, at this year’s AMW show in Melbourne.
“The premise behind the need and development of this new controller was simple,” says Brad Johnston, Product Development Manager at Plazmax Technologies. “We were consistently seeing limitations in what our machines could deliver, not because of our hardware or design, but because of the software controlling them. By taking this monumental step forward in design and investment, we can now push our machines to limits no other product in the market comes close to.”
Aside from the optimisation of functionality in the vertical cutting position, the new controller also allows bevelling to move to a whole new level and allows the machine to cut bevels using any geometry whilst still producing a high-quality finish. Additionally, the user interface has been simplified by removing unnecessary steps in the job loading process. By doing this, the controller increases productivity and decreases the chance of user input errors.
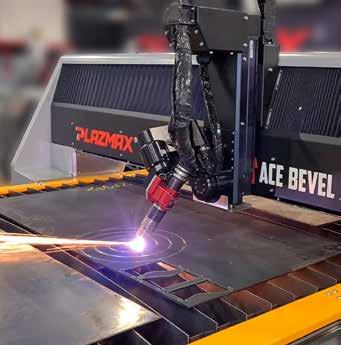
Another massive benefit is the optimisation of their system in readiness for Industry 4.0 and means the controller is ready for integration with any other Industry 4.0 applications and machines. Plazmax’s software team are also working on extensive reporting capabilities which will allow indirect supervision over machine operators by monitoring KPI’s such as uptime, productivity per shift and profitability. These reports will allow customers to really keep their finger on the pulse of their operation, even when not on site. The story behind the success of Plazmax is not just limited to their new CNC controller. For years now, this New Zealand owned and operated business has challenged themselves to excel in every product they manufacture and innovation they implement. “Take traditionally designed plasma cutting tables”, says Managing Director, Darryl Aston, “The approach to how these machines are manufactured hasn’t changed in over 20 years and as result, plasma cutting systems are commonly known as slow, cumbersome and often produce poor quality cuts. We wanted to challenge this while also pursuing further industry connections and projects. The Precinct brings together research, design and advanced manufacturing in one location, opening the doors to innovation and product development, focussing on additive manufacturing. It houses the largest concentration of additive manufacturing equipment in Australia covering both polymer and metal-based systems. A key focus of the AMP research, delivered through the Centre for Additive Manufacturing, is new products and processes based on additive manufacturing that can dramatically increase manufacturing flexibility and efficiency.
RMIT University
Stand AM460 rmit.edu.au so designed our machines from the ground up with the goal of producing a machine surpassing anything else on the market. The result of this is a product that is faster, more accurate and has less down time. Because our machines run so much more efficiently, they are cheaper to run, and this results in a much better ROI to our customers”.
In more recent years, Plazmax has also moved into the field of synchronous robotic welding and has partnered with both ABB and Robotmaster to provide industry leading robotic welding solutions. With ongoing skilled labour shortages in the steel and fabrication industries, Plazmax sees automated solutions in both cutting and welding systems continuing to be a large part of their future growth. As well as the release of their new CNC controller, Plazmax will have a fully operational CutAce plasma cutting table on display providing live demonstrations. Their team will also be able to offer information around their latest robotic automation solutions.
Plazmax Technologies
Stand RA360 plazmax.co.nz