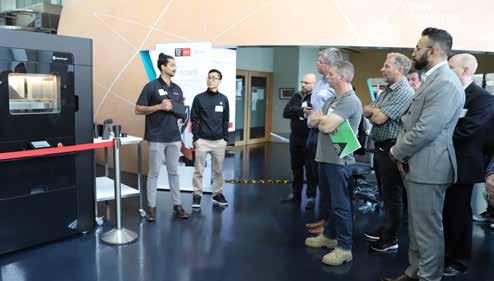
3 minute read
Markforged
from AMT APR/MAY 2023
by AMTIL
Accelerating Innovation in Australian Manufacturing with Additive Technologies.
Additive manufacturing, also known as 3D printing, is a rapidly growing technology that has revolutionized the way products are designed and manufactured. In recent years, Australian manufacturing factories have been embracing this technology and integrating it into their existing manufacturing processes to improve efficiency and reduce costs. Markforged, who recently launched its newest printer the FX20 in Australia, has already seen Australian manufacturers adopt its technology into their existing workflows on shop floors.
Six months after launching the FX20, Markforged has shipped and established a two-digit network of FX20s in Australia and New Zealand. The FX20 utilised Markforged’s Digital Forge, using the Eiger and Simulation software to develop parts quickly and easily.
One of the main advantages of additive manufacturing is its ability to produce highly customised parts and components. With traditional manufacturing methods, producing custom parts can be time-consuming and costly, requiring expensive tooling and specialised equipment. With 3D printing however, the process is much simpler and more efficient. Manufacturers can simply design the part using computer-aided design (CAD) software and then print it on a 3D printer. Many manufacturers around Australia have already recognised the contribution of Markforged 3D printers in the improvement of their production processes. An award-winning WA company Avicena prints over 100 components of the Sentinel Biosecurity Platform (molecular diagnostic instrument) in-house, speeding the time to market and enjoying freedom of design.
“In the early iterations of Sentinel, most small components were made of aluminium, and many were sourced as ready-made items. As we progressed, we redesigned many of the parts to improve functionality, and in many cases upgraded the materials we used to increase component strength,” said Avicena CEO, Tony Fitzgerald.
Over the last five years, the Formero has invested in additive technologies that print production grade materials for end use parts. For them, the FX20 allows them to build faster and more precisely with its large build platform and speed, along with its number of choices for materials to print in. As demand for local production capacity continues to grow due to supply chain issues, more customers are looking to Formero to develop high value, complex and lightweight parts. ANZ GM, James Sanders observes that, “many of our Australian customers have been rapidly transitioning to high value, complex and light weight products that we struggled to provide a solution for. The FX20 meets a market need with high strength, lightweight materials in a large format.”
In addition to producing customised parts and components, additive manufacturing is also being used to produce tooling and fixtures for existing manufacturing processes. Traditionally, producing tooling and fixtures can be a lengthy and costly process, requiring specialised skills and equipment. With 3D printing, however, manufacturers can produce these items quickly and easily using CAD software and a 3D printer. This has led to improved efficiency and reduced costs in many manufacturing processes.
SQP Engineering is another adopter of the FX20. David Miller, SQP’s owner, said “Printed parts from the FX20 look 10 times better than the ones we printed before. Customers are completely blown away when they see the surface finish.”
The FX20 will be the epicenter of SQP’s additive manufacturing workflow, accompanying the Metal X printer.
"If you're going to be competitive, you need to have a solution for all aspects of manufacturing. Not just what we've been doing yesterday. We need to evolve and embrace the manufacturing technologies of tomorrow as well,” David added. Another advantage of additive manufacturing is its ability to produce parts and components with complex geometries that would be difficult or impossible to produce using traditional manufacturing methods. This has led to the development of new products and technologies that would not have been possible otherwise.
Additive manufacturing is being implemented into existing manufacturing processes in Australian manufacturing factories with increasing frequency. As the technology continues to improve and costs come down, it is likely that 3D printing will become even more prevalent in the manufacturing industry in the coming years. Markforged, together with partners will be showcasing the FX20 at Australian Manufacturing Week. Partners include SFDesign (AM280), Emona Instruments (AM450), Konica Minolta (RA300) and Alfex (MT580).
To make the best of AMW2023, visitors are encouraged to book an exclusive meeting with the Markforged Expert by scanning the below QR code and choosing the suitable day and time for an exclusive tour. You’ll receive new insights into how you can optimise your manufacturing processes and reduce costs, to print parts at the point of need. But hurry, spots are limited. Markforged Stand AM280 markforged.com.au