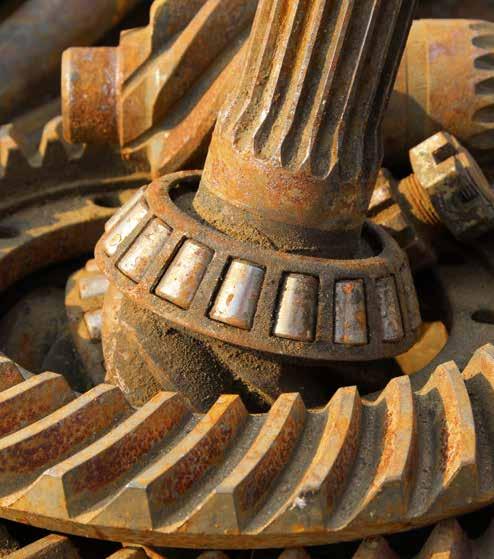
3 minute read
Investigating corrosion
from AMT APR/MAY 2023
by AMTIL
The source of corrosion in fabricated metal components is often obsure. Vyt Garnys from CETEC talks us through a case which brought up unexpected culprits.
A water authority responsible for public works submitted corroded pipe sections from their water treatment plant to CETEC Pty Ltd. They requested that CETEC investigate and identify the root cause of corrosion. CETEC was advised that soon after commissioning, the pipes developed pin holes.
Previous installations of several of these plants in the recent past, showed no evidence of corrosion. CETEC was advised that the welded pipes were made of high grade stainless steel and most pinholes were located near weld points.
The initial assumption was that ‘the fabricator had not followed the welding standard and had supplied a ‘defective product’.
It is critical when investigating problems to use an extensive methodology as possible to eliminate causes. At CETEC, the guidance used in assessing, solving and managing technical problems was one based upon appropriate and established risk management techniques and processes. This involves:
1. Context: To ensure that an understanding of the scope and parameters surrounding the problem.
2. Identification: A well-structured systematic process of identifying potential causes is critical.
3. Analysis: This next stage analyse potential causes.
4. Evaluation: Evaluate the probable causes from the analysis and align these with all the data.
Visual examination of the pipes showed that the defects were observed over the longitudinal weld sections. Corrosion was observed on the external surfaces of the pipes along with water leakage marks located near the Heat Affected Zone (HAZ). On the supplied samples, the accumulation of corrosion products was observed on the welds and weld toes. Away from the welds, there were no significant corrosion observed beside those related to the weld regions.
This supported the initial conclusion that the primary cause of failure was poor welding and fabrication.
However, on the inner surfaces of the supplied samples, where the welds and near weld regions experienced severe corrosion attack, domed morphologies (tubercles) were found. The presence of tubercles suggested the occurrence of microbiologically influenced corrosion (MIC). Material loss at the inner weld materials was also visible.
Chemical analysis using Inductively Coupled Plasma – Optical Emission spectroscopy (ICP-OES) and combustion techniques were performed on the base materials and weld to identify and confirm the grade of materials used.
The chemical analysis showed a close match and compliant to the relevant ASTM standards, but the material was at the lower end of the specifications.
Relevant specimens sampled from the supplied pipes were examined using Scanning Electron Microscopy (SEM) in conjunction with Energy Dispersive X-Ray (EDX). The analysis was performed to examine the corrosion products regarding their chemical compositions and morphology.
A fibrous morphology was also observed. In those zone, EDX analysis showed a high amount of manganese, whereas the ASTM standards indicate that there should not be a significant amount of Manganese. This elevated Manganese was an indication of presence of metal-reducing bacteria brought about during the plant operation.
Visual examination revealed that severe corrosion was mainly observed on the spiral welds for both samples. A heat tinted region was seen on some areas of the internal welds. Heat tint can cause welds to become more prone to corrosion attack because heat tint layer contains elevated chromium levels, leaving the region immediately below the heat tint layer relatively depleted in chromium, causing reduced corrosion resistance of the materials. However, the customer had not specified the grade for the weld fillers, nor provided details as to environment that the plant would be required to operate in.
SEM-EDX analysis was used to identify the elements present. The results suggested that two different bacterial types could be involved resulting in microbiologically influenced corrosion (MIC) on the piping system, which are the Sulphur reducing bacteria (SRB) and metal reducing bacteria (MRB).
Microstructure assessment for stainless steel was also performed on the samples. The structure consisted of homogeneous austenitic structure with minor amount of delta ferrite detected in the HAZ. No detrimental phases were detected. A study showed that the grain boundaries were preferred by the bacteria as their initial attachment site leading to the initiation of MIC.
Thus resolving the issues in this course of the investigation, it has been found that the corrosion failure of the submitted samples were due to the following reasons:
• Microbiologically influenced corrosion (MIC).
• The need to be aware of actual material specifications, not just compliance to standards.
• The need to be aware of the environment in which the plant operates
• The need to evaluate welding practices, including heat tint zone, weld defects and rough weld surfaces. Root cause failure analysis is a valuable tool for these complex situations. cetec.com.au