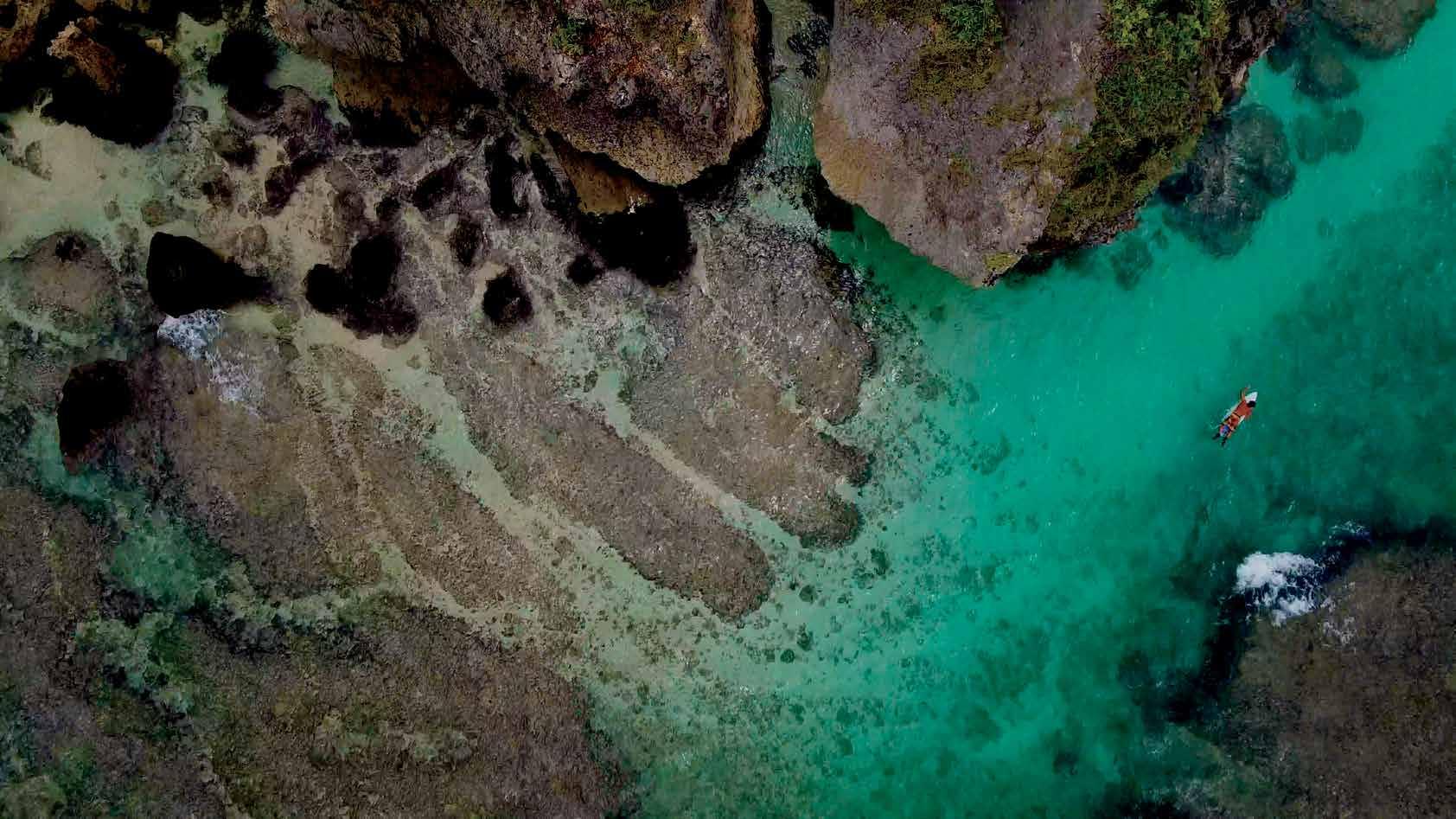
8 minute read
Lost tools lose time
from AMT APR/MAY 2023
by AMTIL
Good tool inventory management leads to more profitable, more sustainable manufacturing.
The earliest example of a vending machine dates back to the first century, when Greek engineer Hero Alexandria created a machine that accepted a coin before dispensing holy water. While vending machines have since increased in sophistication, their principal remains the same — providing streamlined, instant access to the commodity the user requires. Here, Andreas Nyberg, CoroPlus Tool Supply specialist at Sandvik Coromant, explores how tool vending machine software and hardware can enhance a shop floor’s profitability, productivity and sustainability.
In many manufacturing operations, up to 60% of stock is never used, while around 15% of jobs fall behind schedule due to missing tools. What’s more, operators can spend as much as 20% of their time looking for lost tools. These findings, based on Sandvik Coromant's own research prove one thing: inadequate analysis of tool logistics drives up business costs.
Less visibility, less productivity
A machine shop, no matter its size, should always be prepared to work quickly and cost-effectively. Machining parts for varying industries, from an ever-growing portfolio of materials, needs a wide range of tools at the ready. Another layer of complexity comes in the form of mass customization, as an increasing number of manufacturers produce unique products at larger scales. Having access to the right tools, at the right time, is essential.
Have too much or too little stock is largely a result of human error. If tools aren’t placed back in their correct cabinets and are left scattered across the shop floor, operators simply won’t know whether or not their tool stock is depleting. Sometimes, those working on the shop floor can create overstocks if they’re too frivolous with using new tools. If an upgraded version of their current tooling system becomes available, for example, manufacturers may automatically switch over to the new option and neglect their current stock of perfectly functioning, just slightly older, tools.
Inventory management goes digital
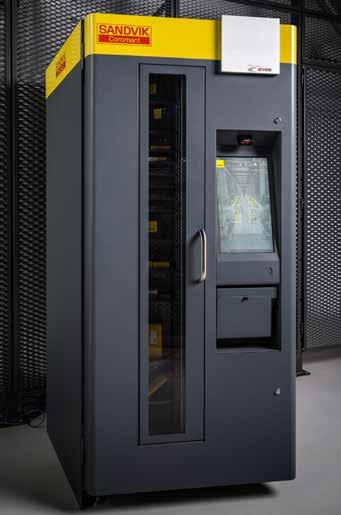
Sandvik Coromant’s CoroPlus® Tool Supply brings together tool storage hardware and software to automate many of the common headaches associated with tool management. The software keeps track of every registered tool in the inventory, shows its stock availability, high cost areas and what tools have been picked to what machine and by whom.
As well as enabling operators to pick and return their tools properly, the software can also manage restocking and maintenance of inventory, as usage of tools on the shop floor feeds data to the management and administration element of the software to support the tracking of cost, planning jobs and management of purchasing. On a practical level, tool logistics software also controls tool logistics hardware solutions, which are either open shelves, drawers with lids, or spiral–equipped vending machines depending on level of control required. The shelves and drawers can contain multiple quantities of tools for the user to pick from, whereas the spirals provide access to one tool at the time.
Leaner and greener
Automation software gives manufacturers an alternative to doing everything manually, and can avoid incurring downtime when there’s little time to spare. Because workers can track tool stocks via a tablet or other smart device, then rely on the software to automatically order and replenish that tool stock when needed, purchasing teams are no longer burdened with the unnecessary paper trail making multiple manual orders creates.
Because operators are never without the tool they need, neither do they have too much of the tools they do not need, the machines never have to stop running because they’ve run out of tools. And, besides creating a more profitable and productive working environment, good inventory management incurs a secondary benefit. It can help make the machine shop more sustainable. What’s more, automated tool supply can also account for the reconditioning and recycling of used tools. If, as an industry, we continue to consume the world’s limited resources in a nonsustainable way, we will run out of the materials we need to produce solid carbine tools. Estimated reserves of tungsten, for example, are around seven million tonnes, or 100 years of consumption. Having a workflow set up that automatically sends used tools for recycling can make taking steps towards more sustainable practice far smoother for the end user.
Like Hero’s invention, vending machines of today serve to streamline the inventory management process and get users the items they need in a more efficient manner. But today, they’re also capable of doing much more. Sandvik Coromant finds that users CoroPlus® Tool Supply software can increase their machine usage rate to 95%, compared to 50% if they aren’t using inventory management software. Having the correct hardware and software in place to manage tools isn’t just about keeping the shop floor neat and tidy. Implementing inventory management software makes the production environment leaner, greener and more cost-effective. sandvik.coromant.com
Is your business exit ready?
Do you want to increase the value of your business and achieve your desired exit outcomes?
We can work with you to ensure you achieve optimal value on the sale of your business and minimise the tax paid in proceeds.
For more information and to download our exit smart report which includes practical tips on how to plan an exit that will lead to favourable financial outcomes, scan our QR code or visit us at: williambuck.com/exitsmartsurvey
Visit us at Australian Manufacturing Week stand #MS535
Members of our friendly and knowledgeable team will be available to answer questions and give insights on how we can help you with succession planning, financial management, R&D grants and much more.
Hybrid servo CNC press brake
Fully understanding the hybrid press brake system gives clarity to its operation, but also makes it a more attractive solution to purchase. Lyndon Smith, National Sales and Marketing Manager at Complete Machine Tools, brings the details into focus.
With the steady growth in the industrial and manufacturing sectors, the expectations of the users and owners on their machinery and products have also grown exponentially. This is very true as far as sheet metal forging and manufacturing units and industries are concerned. That being said, CNC press brakes form a major constituent of the sheet metal sector. Here are the important features that you should know about your hybrid servo CNC press brake system, to help you correlate their benefits better.
Over the course of time, the simple CNC press brake system which started out as a torsion bar CNC set up has now evolved into the popular hydraulic CNC systems which are now in use in most renowned industries. The hybrid servo CNC press brake variant is the latest one in line, and we will discuss further press brakes in this article, taking this hybrid variety as the standard machine. The hybrid servo CNC press brake in simple terms is the consolidated trophy child of both electric and hydraulic press brake machines. The positive and beneficial factors pertaining to both of the mentioned counterparts are incorporated into a single system, thereby giving rise to the highly advantageous hybrid version of the conventional press brakes.
Generally speaking, hybrid brakes make use of less hydraulic fluid and unlike the conventional hydraulic press brakes, the fluid is not in a constant fluid motion. This is what makes your hybrid machine better than its hydraulic predecessor.
Advantages of a hybrid press brake
As it was hinted earlier, the hybrid press brake system compiles the best possible features of both hydraulic and electrical press brake machines. By doing so, all the discrepancies and concerns pertaining to each of the options were eliminated one by one.
This genius hybrid was achieved through the meticulous work of the researchers of the field, who were dead set on improving the already existing patterns of hydraulic machines and electrically operated systems as individual units. Somewhere along the line, they came up with an idea to unite both these research processes, thereby framing a highly powerful and advantageous mixture of all the desirable features and eliminating undesirable ones. From a fairly general point of view, the most noteworthy advantages which were brought about by the introduction of the hybrid servo press brake system would be as follows.

1. It is highly environment friendly.
2. It helps save a significant amount of energy.
3. Functions with better efficiency.
4. It is fully automatic and does not require any manual assistance.
5. It provides great value for every dollar spent.
Environment-friendly
In the hybrid servo press brake systems, the servo pump itself acts as a functional replacement for the traditional servo proportional valve and control technology. With such developments made possible with the recent versions of the press brake machines, the hydraulic directional valves are also completely wiped off the screen entirely. By taking out this additional step in the process, users are allowed to save time that is otherwise wasted in monitoring and managing the valve shifts. With this effective replacement solution, there are additional savings made in the dimensions of space, hydraulic oil usage, and energy consumption along with the process itself. The cut in the usage of oil is mostly due to the minimizing of throttling loss. By allowing its users to save from a third to one-fifth of general hydraulic oil usage, these hybrid systems help achieve real-time energy savings, especially when you look at the process in terms of a longterm scenario.
Energy efficient
As we explained earlier in the environmental column and indirect control over the checking of energy expenditure, the direct contributions of the hybrid press brake system to the energy efficiency are also worth a mention. When compared with conventional press brake and bending systems, the energy efficiency shown by the hybrid system is at an unbeatable level. This is mainly because, in the case of a hybrid work system, the energy used by the system along most of the process is only the direct requirement of the press brake with no additional charges. Also, most pressure from the bottleneck is either reduced, offset, or both, which allows the machine to reduce even up to 75% of the energy consumption in a few cases. The feature of energy efficiency can even apply to these genius hybrid servo press brake machines in their standby mode.
High performance
By the term performance, we include various aspects and dimensions like positioning accuracy, bending accuracy, return speed, working speed, effective maintenance of a suitable internal environment, as well as internal temperature. All of these minor additions, when observed from afar add to the overall exponential increase in the productivity and efficiency of work exhibited by the machine as a complete unit. An additional shout-out is given to the oil temperature maintenance system of the unit, because of its importance in preventing unnecessary overheating. By controlling the oil temperature in the device at a desirable level of 38 degrees celsius and not letting it rise beyond 50 degrees, the hybrid machine is indirectly protecting you from the risks of oil leakage, stability issues, and unnecessary service and maintenance checks.
Automation
With the new hybrid servo CNC press brakes, all the involved processes starting from the selection of tools to recognition and detection of results are completely handled by the machine itself. It can make all the necessary calls by itself, by means of thorough processing of available data and the input you provide. This provides better work efficiency and accuracy and allows minimal space for human error.
Noise control
Apart from these key benefits, these hybrid systems also come with the perks of being very quiet. Though this might not seem like a game-changing factor, it can be quite important for industries that operate in relatively crowded areas, or shops that are looking to install a machine within or close to their store itself, in which case high levels of noise could be a major disturbance. The main feature controlling the noise production here would be the use of a twoway gear pump and a servo motor.
Conclusion
These hybrid press brake systems are the best of the press brake family, thanks to their list of benefits. By providing its users with high levels of satisfaction and quality of work, the perception of such automatic alternatives to the traditional press brake systems is only seen to be growing. All the options provided by the machine manufacturers can also improve the output and efficiency of these machines. Make sure to go through them carefully and choose one that suits every single one of your requirements before making your purchase. With such effective press brake systems available, you are assured to observe visible changes in the overall accuracy and efficiency of the work that your industry puts out as a unit, ultimately improving your quality of work and bottom line. completemachinetools.com.au
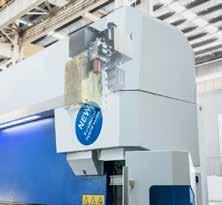
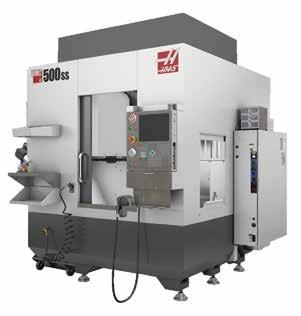