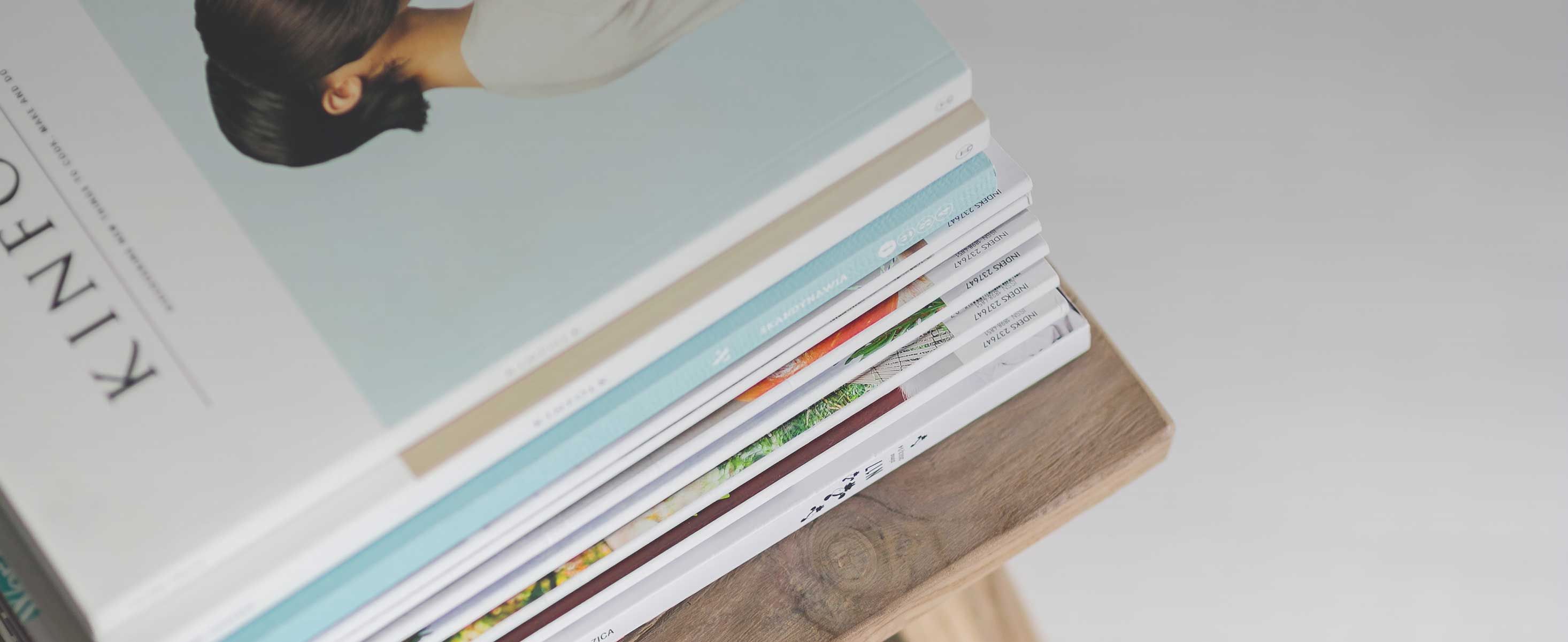
4 minute read
Road train permits extended to help resupply WA supermarkets
looks like it’s becoming more challenging than ever.
Bottom line: things probably won’t be returning to “normal” any time soon. Anticipating, monitoring, and mitigating risks may be what managing a supply chain is now all about. Sustainable operations will be ones that can pre-emptively identify a potential disruption, or at the very least respond the moment that it occurs.
Advertisement
Investment in technology key to solving business’ supply chain woes
Digital transformation is heralding the next era in supply chain management. Research by HERE and Frost & Sullivan found that a third of logistics companies in the Asia Pacific (APAC) region are considering warehouse automation (33%) and electric vehicles (32%) as key investment priorities in the next two years.
However, far more are investing in digital technologies that are designed to achieve end-to-end visibility. Today, logistics companies require fleet, logistics asset tracking, and shipment monitoring solutions that address unique logistics challenges. So there has never been a better time to digitalise and harness the power of location. With location intelligence, you can help streamline operations, reduce the costs of running a business, increase revenue channels, and gain efficiency within supply chain and fleet management. This approach also delivers a more sustainable way of doing business.
Cloud-based logistics software provider, Yojee, is one such company that is offering innovative solutions along the supply chain. As the company’s Managing Director, Ed Clarke, recently put it, “What the pandemic did to the logistics industry as a whole is basically wake everyone up and move technology and agility to the most urgent agenda item. Everyone realised we need to have visibility and control, whether we're at home or at the office.”
A significant step-up from GPS and radio-frequency identification when it comes fleet tracking and shipment monitoring, Internet of Things (IoT)-based location technologies have been gaining a great deal of traction.
Map-based services are proving even more popular and will likely be considered essential within one or two years. Ideally combined with IoT, their key benefit is better route planning and real-time notifications – helping to reduce costs and increased efficiency. A speedy, smooth, and comparatively cheap supply chain can make or break a company’s financial performance.
Consumer benefits also a critical consideration for tech investment
That said, real-time tracking doesn’t just smooth out a supply chain, it appeals to the customer who is waiting at the end of the delivery journey. Today’s consumers want, and tomorrow’s customers will demand, total visibility on every one of their orders. They will want to be able to glance at a map, and know exactly where their goods are, as they make their way through the supply chain – all the way from the factory right up to their front door; the latest trend is knowing where raw materials are sourced.
Digital investment isn’t just about minimising risk. It can also help to maximise your competitive advantage. A company that delivers a precise estimated time of arrival (ETA) – rather than a “maybe eight to 12 weeks” – will be a company that customers will return to. In fact, HERE Technologies’ latest research revealed that just 9% of Australians would be happy to wait more than five days for a delivery, with just 6% saying they will return to a retailer despite having a poor delivery experience.
Pressure on last-mile delivery is increasing as supply chains try to meet the cost and time expectation of consumers. This is where location intelligence tools such as ETA notifications, and last-mile delivery applications can help alleviate supply chain pressures and give consumers their ideal delivery experiences.
We are living in fast-moving times but there is no reason not to feel optimistic. As always, the winners will always be those that embrace change the most effectively. With the right technology in place, supply chain operators give themselves the best possible chance of success. For more information visit: www.here.com
transport industry delivering perishables to WA supermarkets and then being allowed to backload WA grown produce to SA and other Eastern States markets, particularly in light of the new flood crisis in parts of Queensland and New South Wales. "The exemptions are aimed at further assisting industry in the re-supply of WA supermarkets following the destructive floods in SA early this year and to assist local growers in getting their product out of the State swiftly.".
cabin fatigue monitoring systems.
Since February 2 Western Australia has allowed 53.5m road trains to operate from the SA border to Kalgoorlie, where they are off-loaded onto rail or broken down into 36.5m combinations, again as part of the Flood Relief Permit system. This will cease on March 13 following a decision by the National Heavy Vehicle Regulator to end these operations in SA on that date.
Early March, McGowan Government announced the establishment of a taskforce to examine the State's shipping industry and supply chains, following the disruption caused by the flooding of the east-west rail line.
WA Transport Minister Rita Saffioti said, "We have allowed these longer road trains access to Greenmount Hill eastbound for the first time after carefully considering the safety of the heavy vehicles involved and the safety of all road users. "The reasoning behind the 10am to 2pm operating period is to limit the number of lighter vehicles mixing with these road trains, which will be travelling very slowly as they climb Greenmount Hill. "It's an important step to assist the