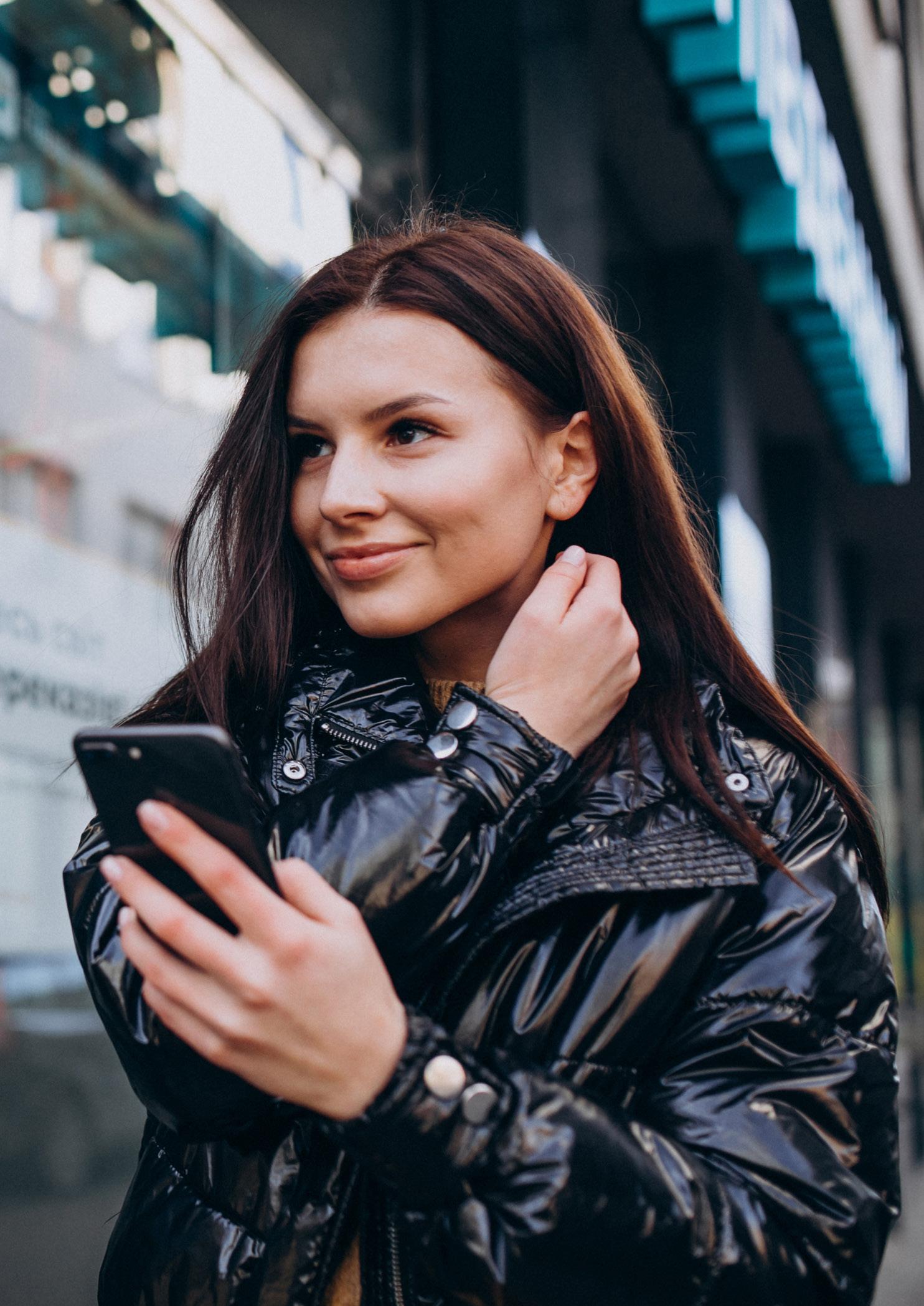
4 minute read
Literature Review
Embracing Returns Internet sales account for a fifth of total UK retail sales (ASCG, 2020:6). E-commerce has drastically altered consumer shopping behaviours; returns are now a retail normality, with ‘estimates that returns cost UK retailers £60bn a year’ (Ram, 2016). With returns an ongoing inevitability, capitalising on RL/CLSC systems from an economic perspective, could reduce fashions environmental impact.
Traditional Supply Chains Forward supply/value chains are processes fulfilling customer requests (Burns, 2019:2), including supplying materials, manufacturing processes; distributing finished goods through a network of retailers to final consumers (Burns, 2019:113). Symbolising the value-added aspects of each stage in creating products, companies make ‘sourcing decisions around procuring materials, production systems, and distribution pipelines (Burns, Mullet & Bryant, 2016, p.256)’ (Burns, 2019:113). Sourcing decisions are influenced by internalised operations (brand ethos, equipment accessibility; capacities) and externalised factors (political, geographical, economic and outsourcing considerations). Brand ethos typically determines a framework before applying ‘vertical integration and contracting’ (Burns, 2019:114) as supply chain management (SCM) approaches.
Advertisement
RL/CLSC Govindan et al. (2015:2) classify RL as ‘planning, implementing and controlling efficient, cost-effective flows of raw materials, in-process inventory, finished goods and related information from consumption to the point of origin for recapturing’. Whilst Ronald and Dale (2002:271) define it as opposite direction product movement recapturing value, or for proper disposal. RL generally encompasses product returns, end-of-life disposal schemes; asset value recovery strategies. Appendix 1 outlines situational differences between forward and reverse logistics.
Collaborative supplier relationships operate knowing that RL/CLSC demand management, reactively responds to inconsistent flows of materials back-up the chain. Planning RL/CLSC is difficult, due to reliance on consumers returning products, hence reverse-flows are more reactive, with less visibility (Ronald and Dale S, 2002:272) (Appendix 2). Bloemhof-Ruwaard et al. (1999) mention problems of locating collection points for returned used products. Others propose combining retail activities with used product collection (Wojanowski et al., 2007) (cited through Pokharela and Mutha, 2009:177). Research highlights RL/CLSC inventory management inconsistencies, including diverse physical conditions of returned products. Pokharela and Mutha (2009:178) and Ilgin and Gupta (2009:574) discuss needs for coordination between remanufacturing and regular modes of procurement. Inconsistencies in inventory quality, usability; distribution source means consistent decision-making is important.
Asset recovery requires sufficient reverse-flow capacity, volumes, product condition, operational/logistical costs and components value. Hindrances include lack of technological systems, training or education, financial limitations; reluctance of distributors/retailers. Sustainable procurement practices regarding minimising social risk also require consideration: are suppliers’ compliant with laws/codes of conduct around wages, hiring standards, workplace safety, environmental requirements; ethical practices? (Burns, 2019:115). If not, retailers could face penalisation, damaged reputation and legal action.
RL/CLSC limitations require collaboration; ‘Large groups tend no longer to be able to act with total autonomy’ (Morana, 2013:11). Smaller retailers should consider operational flexibility and adaption for ease of collaboration between other vital players i.e. Central Return Centres send useable products off for refurbishment and unusable to disposal.
Distribution strategies are fundamental as total costs depend heavily upon transportation costs (Govindan et al, 2015:10). Efficient RL/CLSC transportation planning is vital as fashion’s freight use will triple by 2040 (Common Objective, 2018:online). ‘Emissions can be saved through more centralised…coordinated controls’ of RL/CLSC (ASCG, 2020:10) and investments in UK-based infrastructure. New products move in large, neat; efficiently stacked pallets. Reverse-flow products typically have smaller shipments, meaning less well-formed pallets; unorganized merchandise (Ronald and Dale, 2002:76).
RL/CLSC systems re-establish value out of materials already in circulation; hence ongoingly referred to simultaneously as intertwined networks.
COLLABORATION
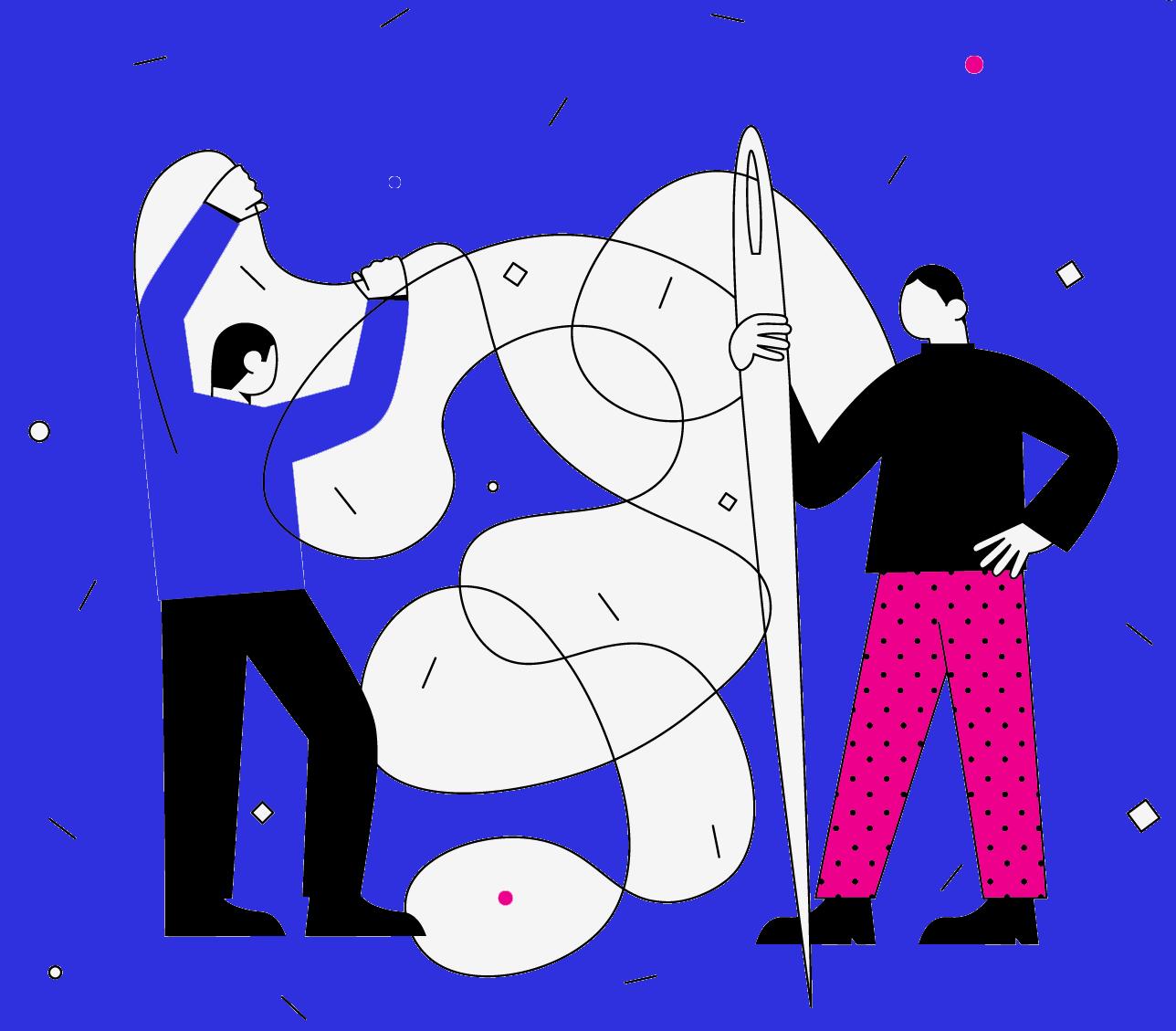
WA S T E I S O N LY WA S T E ,
IF WE WASTE IT.
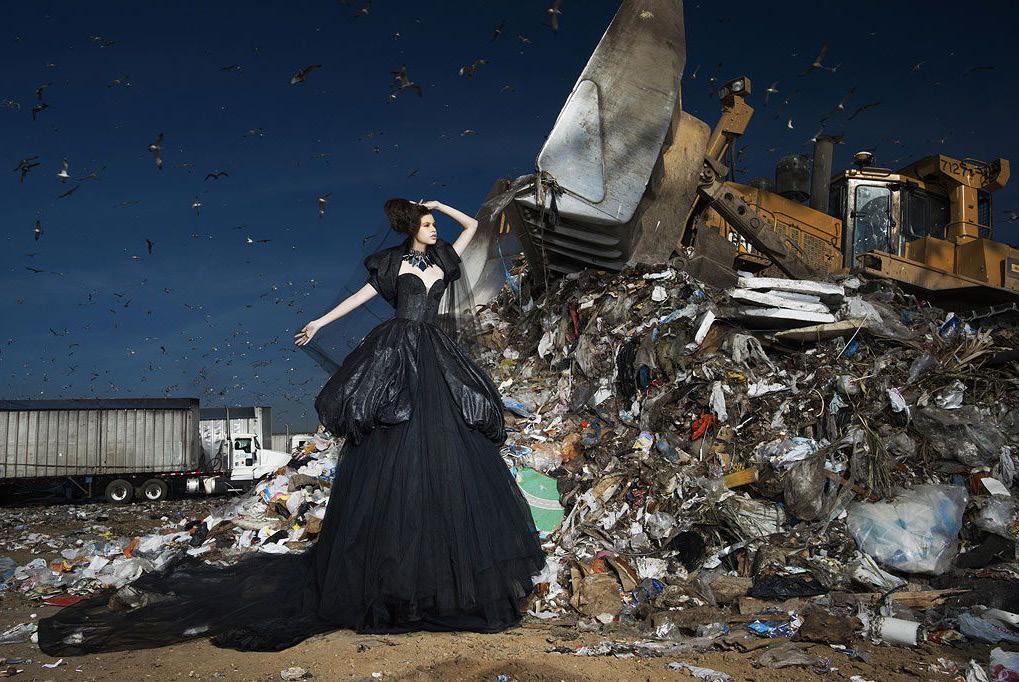
Fashion Sustainability Burns (2019:118) notes fashion’s responsibility to meet country/regional standards associated with environmental sustainability. But an industry-wide issue is defining sustainable fashion in the first place (Cheng, 2019). Without ‘common language’ or ‘shared standards’ within fashion, sustainability is hard to measure across different retailer capacities.
Projections warn that RL/CLSC dependency on return products could induce self-cannibalisation (perpetuated consumerism), whereby new products can only be produced if enough products are sold and returned in the first place.
Lifecycle Assessments (LCA) analyse ‘environmental impacts throughout product lifecycles’ (Finnveden et al., 2009). Limited data creates difficulties in LCA of textiles products. Traditional product lifecycles, post-consumer waste (Appendix 3), highlight needs to transition cradle-to-grave into cradle-to-cradle, involving product management through reuse, repair; remanufacture at product, component; material-level (Fleischmann et al., 2002:654). Although RL/CLSC has upcycling value-creation potential, logistical issues require managemental considerations to maximise effectiveness.
Waste is only waste, if we waste it. Post-electronic point of sale (EPOS) systems need operationalisation for accessible product returns. Recycling regulations are pressuring manufactures and consumers to dispose of products responsibly.
Sustainability could be embedded in design ‘with conduct codes’ (Burns, 2019:203). Sustainable design (i.e. additive manufacture, biomimicry; polymorphic clothing) for disassembly and recycling, could ease resource flow and technical manufacturing processes in value-retrieval, from post-consumer waste through RL/CLSC (Ilgin and Gupta, 2009:564). This also compromises understanding product environmental compatibility, risk management, workplace health and safety, pollution prevention, resource conservation; waste management (Morana, 2013:56).
Fleischmann et al. (2002:653) and Pokharela and Mutha (2009:175) appraise post-consumer value retention, due to forecasted scarcity of virgin resources, resulting in supplier price increases. Legislations, directives, consumer awareness and social responsibilities towards environment are also drivers for [RL].
Network designs require strategy planning of processes, locations; capacities. Ronald and Dale (2002:272) identify varied destinations for returned products and new methodologies addressing remanufacturing, forecasting, capacity planning; inventory management (Ilgin and Gupta, 2009:572). Ilgin and Gupta (2009:573) address capacity planning techniques based on maximising investment savings from remanufacturing facilities. Appendix 4 further demonstrates a recovery model for fashion CLSC.