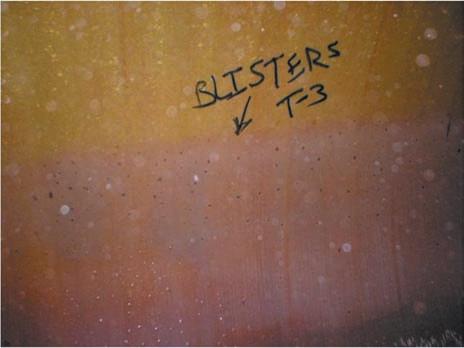
35 minute read
Press Releases
Blisters on the side walls of the tank Cracking
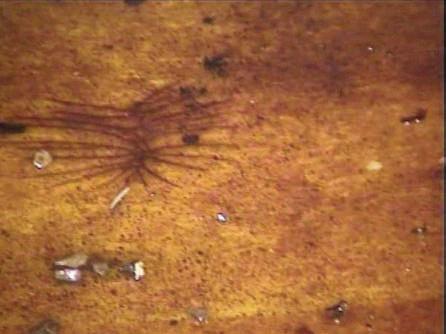
Advertisement

Wrinkling and softening of the gel-coat/primary surface Internal erosion, wicking, and delamination
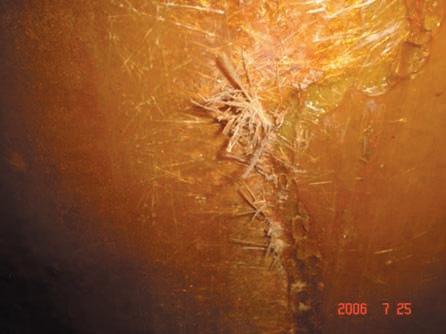
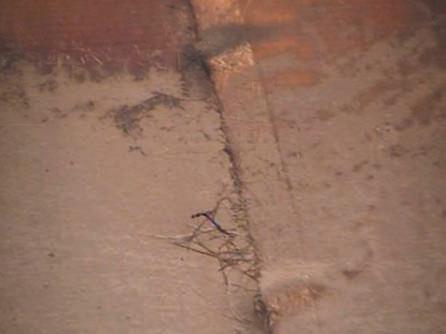
Wicking and delamination on the bulkhead seam
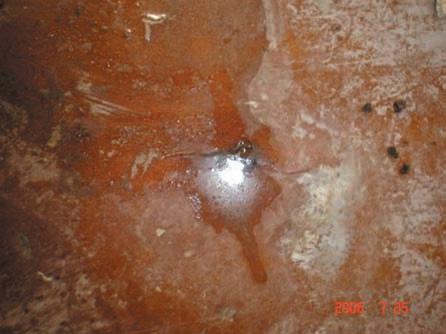
Perforation with ingress of water at the six o’clock position
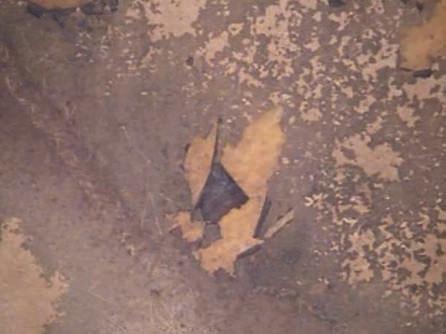
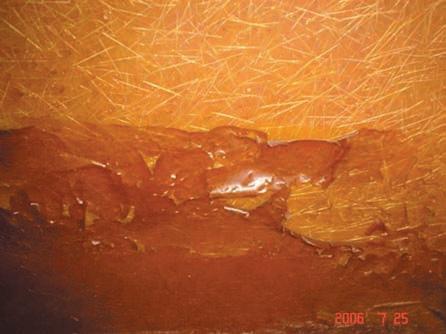
be excluded from this publication, but have allowed the publication of the photographs in the general interest of promoting improvements in industry standards and additional research.
Industry Research
A review of industry research supports the observations found in the internal inspection photographs. The industry research also concludes that there is still much that is unknown about the effects of ethanol on fiberglass USTs. In particular, a May, 2002 document by Simpson Gumpertz & Heger Inc. that was sponsored by the American Petroleum Institute, the Fiberglass Tank and Pipe Institute, the Steel Tank Institute, and the Western States Petroleum Association provides a concise explanation of some of the research and findings of numerous documented studies. The document was entitled “Impact of Gasoline Blended with Ethanol on the Long-Term Structural Integrity of Liquid Petroleum Storage Systems and Components”. The following are excerpts from the document and have only been edited to add the document’s page number for reference, and to remove the document’s reference numbers to accommodate the space constraints for this publication:
•The higher alcohol content in water bottoms may be locally detrimental to FRP tank walls that are qualified only for low alcohol blends; however, no such problems have been reported or evaluated in the literature. (page 3)
•Resins typically used in FRP tanks (e.g. isophthalics, terephthalics, and vinyl esters) exhibit some level of swelling (with weight gain) and softening when exposed to alcohols, including ethanol. (page 4)
•Softening can be measured as reduction in hardness and material stiffness, which can be measured by mechanical tests for Barcol surface hardness and modulus of elasticity. These physical changes are a function of permeation, which can be measured by absorption and swelling tests, and are largely reversible if the laminate is allowed to dry. After desorption of alcohol, some permanent loss of mechanical properties may occur, but the mechanism is not well defined. Reduced stiffness, along with creep, results in a lower resistance to buckling, a key design criterion for FRP tanks. This behavior may affect the adequacy of safety factors for buckling design of FRP tanks exposed to ethanol/gasoline blends. (page 4)
•However, few analytical or experimental data have been published to show how reduced properties due to ethanol exposure (e.g. softening and stiffness reduction) relate to longterm performance under sustained (creep) loads such as caused by soil and hydrostatic pressure on underground tanks. (page 5)
Most manufacturers of single-wall fiberglass USTs have had warranties in place for ethanol at 10% levels as early as 1981, and almost all UL-listed double-wall USTs are completely compatible with ethanol blends. Manufacturers had three choices of testing in accordance with UL 1316 (see Table 14.1). Manufacturers choosing to market tanks only for petroleum use (under the first column “Tanks for Petroleum Products” in Table 14.1) could forego the ethanol testing. Conversely, manufacturers wishing to market tanks for 100% ethanol or ethanol blends could have their tanks tested and listed by UL under the other two columns in Table 14.1, Type A. However, the Simpson Gumpertz & Heger literature review states that ethanol immersion testing was not required by UL 1316 before 1987. Another good source of information is provided by the State of Wisconsin’s UST Program with a “Historical Timeline for Storage Tank Ethanol Compatibility” on their website: http://commerce.wi.gov/ER/pdf/ bst/ProgramLetters_PL/ER-BST-PLHistoricalTimelineTankEthanolComp atibility.pdf
Two of the conclusions from the Simpson Gumpertz & Heger literature review state that:
•Ethanol tends to soften FRP and reduce its mechanical stiffness.
Immersion tests conducted according to the UL 1316 tank standard qualify FRP tank laminates for ethanol storage based on the retained strength, stiffness, and Izod impact resistance. Most tanks meet the requirements of UL 1316 for the storage of gasohol (10% ethanol content). There is concern that tanks that pre-date the UL testing (i.e. tanks produced prior to the early 1980s) may not be ethanol compatible; however, major tank manufacturers indicate that the tanks are constructed of similar resins and should perform satisfactorily. (page 13)
•The published literature does not adequately cover the effects of reduced material stiffness due to ethanol storage on the creep buckling strength of FRP tanks. This issue requires further research and/or evaluation of manufacturer test data, analyses, and research findings on the subject. (page 13)
Steel Tanks
The effects of ethanol on steel tanks were also investigated in the Simpson Gumpertz & Heger document, particularly with the potential for internal corrosion from phase-separation of the wateralcohol layer and the potential for microbial corrosion. There was no evidence given in the literature search with problems associated with stress corrosion cracking that sometimes occurs with large denatured ethanol ASTs at high stress areas. The personnel performing the field internal inspections for secondary containment have not encountered any unusual observations with steel tanks. They have observed some internal corrosion pitting and microbial corrosion, but nothing that is unusual or anything they did not see before the introduction of E-10.
However, they did find the following conditions at one site with an older internally-lined single-wall steel tank with delamination problems.
Recommendations
Wide-spread use of E-10 is relatively new for most of the country (within the last two to three years). While much industry and laboratory research of E-10 compatibility has been performed by UL and other national and international testing authorities, the real-world performance is still evolving. Nevertheless, one only has to consider the historical performance of early flex-pipe systems, tank bladders, and older piping and dispenser sump systems to know that design performance is not always equal to field performance. Finally, it is also possible for higher ethanol concentrations to be present in the bottom of the tank, particularly if phase separation has occurred with excess water. For owners that are not vigilant about keeping water out of the bottom of their tanks, the possibility exists that the tank surface may be periodically exposed to higher than 10% concentrations due to phase separation of ethanol.
However, this article is not intended as an indictment for manufacturers, for no manufacturer truly wants to manufacture a product that doesn’t work. Instead, this is merely an attempt to solicit reputable and qualified industry professionals to initiate a long term independent study to evaluate and measure the “real world” effects of E-10 on UST and AST storage systems, and to raise an awareness of a potential problem. This is particularly important at this time when the EPA is considering the potential effects of E-15 on UST systems in response to the Ethanol industry’s push to replace E-10 with E-15. A decision to rush to E-15 use would not be beneficial.
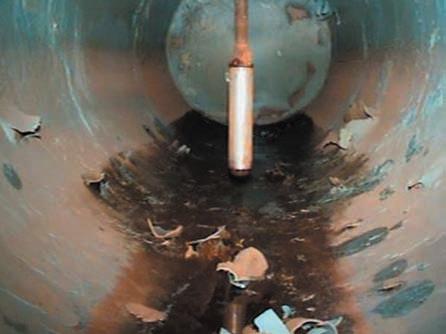
Marshall T. Mott-Smith, President Mott-Smith Consulting Group, LLC 2268-2 Wednesday Street Tallahassee, Fl 32308 mtmott-smith@comcast.net 850-391-9835 work 850-591-1434 cell www.mott-smithconsulting.com
Downstream Industry still in decline
Information recently released by Experian Catalist in the Energy Institute’s Retail Marketing Survey (March 2010) indicated that another 270 filling stations closed during 2009 and that there are now 9,013 Retail Filling Stations in the UK as at 31 December 2009.
This compares with 39,958 sites that were operating in 1967 – that is 30, 945 sites that have closed in 43 years! A closer look at the number of sites by type of operator can be summarised as follows;
Oil Companies 5,582 Main Retailers 1,083 Supermarkets 1,271 Other Retailers 1,077
Of the leading brands, they are as broken down as follows;
BP 1,179 Texaco 999 Shell 930 Esso 900 Total 818 Murco 395 Jet 361
The Supermarket brands are likewise, 2008 numbers in brackets;
Tesco 450 (+ 9) Morrison’s 292 (+ 4) Sainsbury’s 254 (+7) ASDA 179 (+6) Others 96 (- 14) The Autogas Market breakdown to the following;
Shell 226 BP 209 Texaco 73 Total 66 Unbranded/Other 62 Morrison’s 57 Jet 30 Gleaner 29 Esso 27 ASDA 14 All Others 87
Total 880 (+74)
Other Details The number of nozzles have reduced from 74, 873 to 66,537 as at 31 December 2009 The Annual Total Deliveries in Tonnes remained about the same over the last 10years at 37,002,000 for the year with diesel accounting for over 20m tonnes per year The number of sites open for 24 hours was 3,186 in 2009, BP having the largest number with 694 sites.
APEA tel/fax 0845 603 5507 www.apea.org.uk 49
History of Petrol Stations Part 14, Petrol Pumping Systems - Pressurised Pumping
By Jamie Thompson
Development of the pressurised pumping systems in European Service Stations
In the early days the petrol filling stations developed as an addition to an existing business providing added benefit for existing customers; they were generally quite small and there were many such premises. With the introduction of self-service filling stations in the 1960's the design of the petrol station layout became more important; the tanks were moved away from the dispensers, road tankers could fill without disturbing sales and for the first time engineers had to become more aware of the limitations of the suction pump which had been the preferred system for distributing petrol in Europe.
In the USA the submersible petrol pump was developed from a water pump. This became widely used in that country and it remains as popular as ever.
The main difference between the two systems was that a suction pump has the motor in the dispenser, and the pressure pump has the motor situated inside the tank.
The UK and European use had been restricted to a few sites in those early years in the 1960’s and 70’s as US trained engineers and others tried out this method of pumping in the other wise “suction orientated” Europe. It was unfortunate at the time that we all used unprotected steel pipe buried under the forecourts and while both suction and pressure systems experienced leaks from corroded steel pipe those sites with pressure lines seemed to experience the most spectacular losses which proved to be quite large and eventful.
The pressurised pumping system did not recognise the difference between a hole in a petrol pipe and a nozzle being opened and as soon as the corrosion caused a hole product would be pumped out at a high rate.
At one site in Denmark a leak caused an explosion with one death and injuries to 9 people and in the UK numerous large leaks had both operators and regulators questioning the wisdom of pressure systems.
It was clear also that many people in Europe did not fully understand the systems and in one case when a mechanical leak detector shut down a submersible pipe (for the correct reason - there was a leak!) the maintenance engineer was called out by the operator because his pump did not work, the only way he could get the pump started was to remove the mechanical leak detector and, of course, a large loss followed.
In London one pressurised system caused a 10,000 gallon loss in a very short period and following this incident in the 1980’s the petroleum section started to require the few pressurised sites that remained to change to suction systems or replace the pipes with double wall or trenched systems.
Physics and Economics are Now Driving Change
When we look at the changes within the industry in Europe at present we see a large increase in the use of the pressure pumping systems that had traditionally favoured the suction system and there are good practical, economic and indeed environmental reasons for this gradual change.
The physical limitations of the suction system can be calculated and depend upon a number of critical factors and more importantly in recent years the chemical nature of fuels we are now using are reducing those limitations further.
Let us examine these limitations
- The suction pump situated at the dispenser has limitations of pull to a depth of approx 4m, which is measured from the bottom of the tank to the level of the suction pump. With larger tanks being installed up to 3m in diameter, there is not much room to play with tanks being installed 1m below ground
- The maximum length of run for a suction pipe to operate successfully would be approximately 60m after which pumping problems will occur.
- These limitations are based on calculations at sea level and with installations at higher altitudes the limitations are much lower.
- The changing specification of the fuels that we now use has also contributed to a worsening situation regarding suction systems.

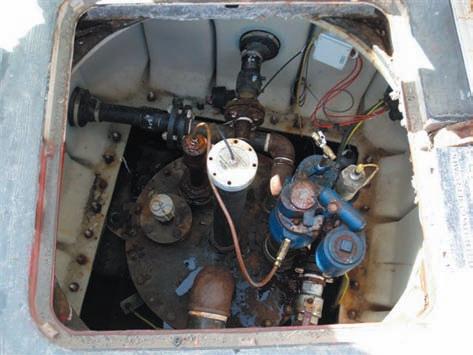
- More unleaded, higher octane fuels with increasingly more additives are making it more difficult to use suction pumps within the limits described above.
- The more gaseous nature of the fuels causes cavitation on a suction pump and causes vapour lock when the whole systems stops.
- The problems are exacerbated in the summer when warm weather heats up both the product and lines, again causing vapour lock and the subsequent dispensing problems.
Service Station Design
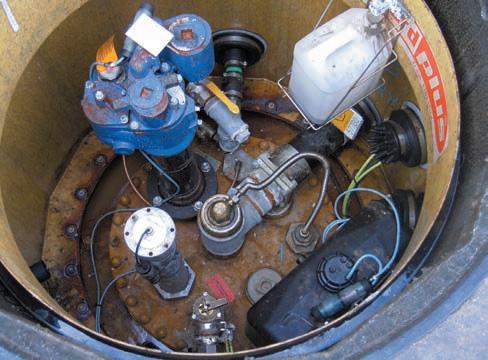
In all European countries the drive of the oil industry is for larger more efficient sites with the smaller sites closing and the larger sites with other profit centres being developed to serve the changing customer needs. This change of design ensures that the road tanker stand is situated well away from the dispensing in order to allow petrol deliveries to take place without interfering with pump sales. The size of the sites is increasing with car parking provided for the customer who also visits for non-petroleum sales.
The European engineer, traditionally used to the suction system, now has to examine the option of using submersible pumps if wishing to retain flexibility in the design of the site.
Although this move towards pressure systems has been driven by the physical nature of the site and the limitations described above, the more enlightened engineers are also praising the economic virtues of using submersible pumps in this cost conscious environment.
With new service station designs it is estimated that a pressure system uses 75% less underground pipe than a suction system, although this would be likely to be secondarily contained pipe work.
On Going Savings in Maintenance
the savings do not stop there with even greater savings being made on the maintenance of equipment. Using pressure technology means there are less motor/pumping systems working at the station. Less moving parts to break down means lower maintenance costs. Experience has shown that failure of submersible pumps is extremely rare. They have a proven track record with excellent reliability and reduced down time; one of the reasons for this is that they operate inside the tank in ideal conditions, submersed in fuel, which cools and lubricates the motor. There is the added bonus of reduced energy costs, which also contributes to increased profits.
Environmental Considerations
As an ex regulator I had major concerns as to the past performance of pressure systems in an environment where leaks frequently occurred, and with that in mind the industry has certainly responded over the years to meet those challenges offering both new materials and leak detection technology to reduce this risk considerably.
The use of unprotected single wall steel pipe work, which historically caused such horrific leak problems for service stations all over the world, is thankfully a thing of the past. Engineers constructing service stations using pressurised systems at this present time have such a wide choice of non-metallic pipe work suitable for operating at high pressure often secondarily contained with built in leak detection devices.
The sophistication of mechanical and electronic line leak detection systems supplied with the submersible pumping system can now enable lines to be automatically tested for substantial leaks (12 litres per hour) which operate each time the pump stops and the delivery cycle ends. In more sensitive environments lines can be checked to a finer test (0.38 litres per hour), at predetermined intervals. These tests only form part of the whole safety package, which would include secondarily contained lines, together with class 1 leak detection systems that recognise the smallest leak and shut down the submersible pump preventing the types of losses we experienced in those early days. These better arrangements are designed to keep the pressure pumping system operating safely and efficiently in all environments.

Misinformation about Conductive Pipes
Lars Selling, Kungsors Plast AB
From the oil well to the passenger car, products and components are conductive. Road tanker tyres and fill hoses are conductive. Fuel dispenser hoses and nozzles are conductive. Plastic fuel hoses in passenger cars are conductive. Why? Because they can be grounded to earth to increase safety margins and decrease risk (a common precaution for decades). Hence, the KPS conductive product range is not unique; it is merely providing what most other suppliers and applications have used and taken for granted over many years: a higher level of safety.
See this link for credible expert comments on the latest video: www.kpsdownload.com/videocom ments.wmv
Our conductive pipe systems have been installed for over 14 years without any electrostatic ignition incidents; unlike non-conductive systems, where a number of fires have been attributed to electrostatic discharges.
Further, safety margins in a grounded conductive systems are dramatically better than those of a non-conductive system. Therefore, the conductive system is also future proof with regards to some of the biofuels that can be expected to have more severe charging characteristics than fuels on the market today. Safety margins in a non-conductive system are at best low and will in some circumstances be non-existant.
Our products in the KPS Petrol Pipe System™ are approved to or comply with the highest standards:
•ATEX 1999/92/EC •EN 13463-1 (as only approved supplier) •EN 14125 (we were the first to be approved in 2005) •UL 971 •DIBt-approval to German regulations (as first and only approved plastic pipe supplier). •KPS is the only pipe supplier that currently allows third-party audit of products in current production under the ERA Fuelstar
Surveillance Scheme. •KPS is the inventor of and first ever supplier of CE-approved plastic
LPG-pipe. •KPS has been making plastic petrol pipes for longer than any other supplier.
We lead the development and are proud of and serious about it.
Non-conductive piping is not exempt from the laws of physics so we just cannot ignore how basic electricity works. Everyone needs to concentrate on continually improving their products as we at KPS are proud to do to ensure safety for all. Kungsors Plast ABmanufacturer and supplier of the KPS Petrol Pipe System™
The Premier Girls - Race For Life 2010
By Sadie Clark, The Premier Group
The Premier Group’s, Sadie Clarke, Penny Hughes & Heather Walls will be joining their former colleagues Joy Burgess, Melanie Thomas & Sarah Williams along with approximately 1,800 other women from North Wales, on Rhyl promenade for the Race for Life on Sunday 6th June 2010 at 11am.
The event raises funds for Cancer Research UK, with participants running, jogging or walking the course along Rhyl seafront. This is the second time the Premier Girls have taken part in the event. Whilst last year they chose to walk the 5kms, which took exactly an hour, this year they intend to jog the full distance, and are in training to do so in a reasonable time.
The event in Rhyl has a fund-raising target of £86,822.00.
The race is one of many taking place over the summer across the UK. It is hoped 700,000 women will take part nationwide to raise more than £60m for the charity.
Sadie, Penny, Heather & Joy were pleased to be able to take part in the event again, and to have recruited their former colleagues Sarah & Melanie to join them. They said “The stories of some of the women taking part last year were very moving, and the atmosphere was fantastic. The participants were of all ages and abilities, from athletes running the course, walkers at a more sedate pace, Mum’s with their baby daughters in pushchairs and elderly and disabled women in wheelchairs.”
Thanks to the generosity of their friends, family, colleagues and suppliers from within the industry, The Premier Girls raised £677.00 for Cancer Research UK last year. Their target for this year is £1,000.00.
If you wish to contribute to this worthy cause, you can donate through the Race for Life website. Please visit www.raceforlifesponsorme.org/pre mier-girls to make a donation, or alternately contact Penny or Heather at the Penmaenmawr office on 01492 623787.

The Shape of Things to Come?
By Brian Humm, LFEPA
January 2010, London Borough of Hackney.
An independent retailer has decided that enough is enough, after the losses incurred through “Drive Offs” during 2009 amounting to in excess of £10,000, Balasingham Nanthabalan, who owns and operates Mare Street Service Station, London E8 under the Texaco banner has decided to bite the bullet and start operating a Pre Pay system at all times.
“2009 was a particularly bad year for people not wanting to pay for fuel and I decided that I couldn’t carry on suffering the losses, I am an independent retailer with over 25
years invested within this business and I have decided to operate in this way.”
Following a major refurbishment in 2008, the site was equipped with Tokheim Quantium T dispensers and associated Entuitive point of sale equipment, this allows for the pre selection of an amount in £s to be allocated to an individual dispenser, the customer then fills his vehicle as normal with the dispenser cutting out once the selected limit has been reached.
Mr Nanthabalan approached the LFEPA for advice regarding the change, the Authority had no objection to the changes although the mode of operation has now been changed to pre authorisation attended self service, the forecourt is still being observed by the control staff.
An advantage of this situation from a safety point of view is that all containers would be observed before being filled and obviously anyone who could possibly be considered underage would have to enter the store and can be challenged before any transaction takes place.
The site has labelled all dispensers informing the customer that it is a
pre pay site and also has a loudspeaker message at intervals to the effect that “this is a pre pay service station, please pay in the shop before refuelling, thank you for your cooperation”, one drawback of this is that the site has now received noise complaints from neighbours!.
I have witnessed the site in operation and have noticed that in the whole it seems to be working, some people are objecting because as with any new procedure it will take some time to adapt, Mr Nanthabalan said “we have had some complaints from customers, especially long standing ones, but they all seem to understand the situation once I
explain the reasoning behind my decision.”
Will this catch on? One drawback that was thought of is that the shop sales would suffer but early indications show that the shop is trading at the same level as last year, it will take time for people to adapt to this method of purchasing fuel but as Mr Nanthabalan said what business can carry on with the size of losses that this industry seems to attract?
As a footnote, because of the poor weather being experienced within the area, Mr Nanthabalan suspended the pre pay to alleviate congestion on the forecourt, in the small period of this suspension the site suffered 2 drive offs in excess of £75 each!
Needless to say it quickly reverted back to its new image.
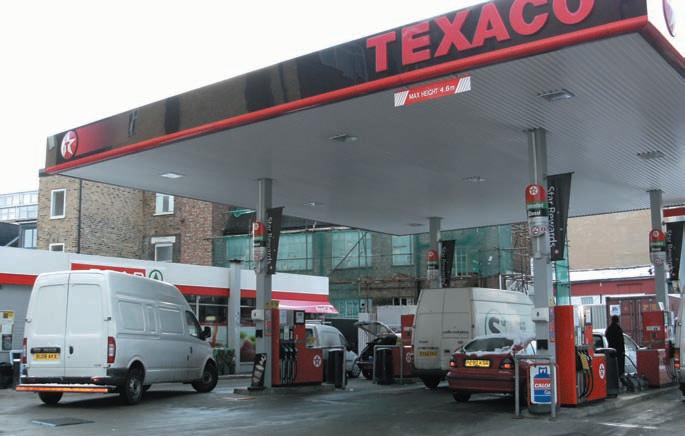
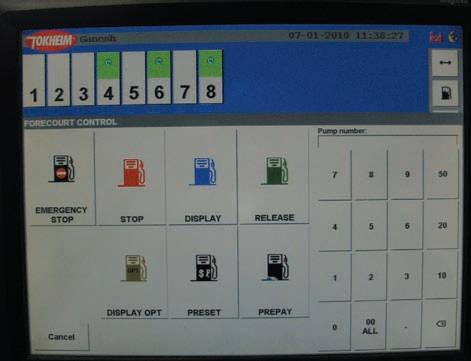
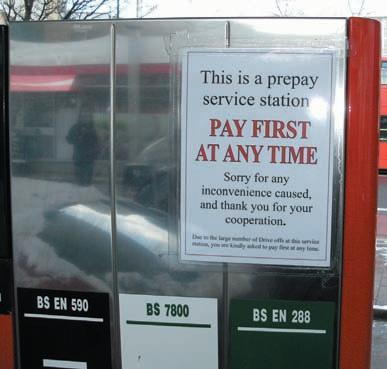
Interview with Maureen Briggs, Craigavon Borough Council
By Brian Baker
Northern Ireland has 26 Petroleum Licensing Authorities at present and have operated through some very difficult times. One Authority, Craigavon, had enormous problems a few years ago when the officer covering petroleum retired and Maureen Briggs took over by expanding her role as the Licensing Officer. I recently had the chance to speak to Maureen about the current situation in Northern Ireland. Here is what she said;
Hello Maureen, I was trying to recall how long it has been since you took over your role as the petroleum officer for Craigavon Borough Council, perhaps you could remind me and what you discovered on taking on the role?
Hi Brian, I was given the responsibility for Petroleum Licensing early in 2007. At best the system inherited could be described as antiquated. There were no systems or procedures to follow or give guidance. In Northern Ireland D.S.E.A.R. came into force in 2003 but there did not appear to have been any attempt to either inform licensees about requirements or to enforce the requirements. It was obvious from the start that the petroleum licensing function had been a very low priority for too many years. This had permitted unscrupulous dealers to operate in the area with little legislative compliance.
It was not until I consulted you through the APEA that we began to make meaningful headway. With your assistance we put in place a two year plan for inspecting under both the Petroleum (Consolidation) Acts N 1929 & 1937 and Dangerous Substances and Explosive Atmosphere Regulations (NI) 2003. We developed workable systems, policies and procedures. We also put in place a program to ensure officers would attain the required competencies by receiving appropriate training. Additionally we revised our terms and conditions and the council agreed to formally adopt the ‘Guidance for Design, Construction, Modification, Maintenance and Decommissioning of Filling Stations’ as the standard for all new filling stations or refurbishments. This has proved very beneficial as it provided a standard which officers, licensees and architects could work towards.
So how many sites do you have that are licensed? Are they all retail filling stations or do you have workplaces as well that dispense petroleum?
When we first took over there were fifty six sites listed as requiring a petroleum licence. For the size of Craigavon (area 260 square kilometres, population 90,000 –100,000.) this number was quite high. However upon commencing inspections and enforcement we discovered a number of sites were derelict – these sites needed to be decommissioned, some other sites decided to close rather than try and comply with the new requirements. We currently have 38 sites of which two are work places.
It is well known that there has been a political divide in the Province. Has this affected you in conducting your role as an Inspecting Officer?
The political divide has not affected either me or other licensing officers. Our role is to ensure the safe storage of petroleum. We provide as much assistance and information as possible to all sections of our community.
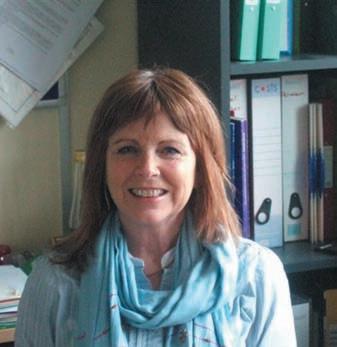
Now there are slight differences in petroleum legislation from the mainland UK. Can you share those differences as Northern Ireland tends to follow what we do over here?
While there are differences, our regulations really mirror those in England. We follow guidance issued in the rest of U.K. through H.E.L.A. (N.I.). I suppose one of the differences which I have noted is that in Northern Ireland when an application for a Petroleum Licence is refused the applicants right of appeal is to the Health and Safety Executive N.I.
I know you have some problems with a few operators. Can you outline what they have been?
When we first took over the function we were met with resistance from a minority of operators. These operators did not want to provide information relating to contact details, technical details or stock details.
A Prohibition Notice was served on one operator after discovering evidence of a large spill on the forecourt (it was suspected fuel was off loaded directly into the chambers without attaching the hose to the fill point). The site had no emergency procedures and there was no information relating to stock.
56 APEA tel/fax 0845 603 5507 www.apea.org.uk
Further to the notice being served the dispensers were ripped out at night leaving live electric wires and escaping petrol vapour from the suction lines (an attempt had been made to plug one of the lines with a small Saxa salt cellar!). The responsibility for the station then fell to the landlord of the site who worked towards having the prohibition lifted. During this work it was discovered that two tanks believed to have been decommissioned had been left in the ground empty but the chambers had been filled with concrete giving the impression of total decommissioning. Obviously a lot of work was required before the prohibition notice was lifted. As we continued our inspections we discovered another station which could not provide information relating to decommissioning of two tanks on site. Upon investigating it was discovered that the same practise of filling the chambers with concrete while leaving empty tanks in the ground had taken place. On this particular site, while driving to an appointment, our Health and Safety Officer noticed men with Kango hammers attempting to break the concrete in the chambers – yet another prohibition notice.
However, I must state that the majority of the Licensees have taken the issue very seriously, taking on board the requirements and, where necessary, putting plans in place to comply. We have had a number of major refurbishments and two new filling stations. These have been a major learning curve for us. Currently architects are developing engineered solutions on an existing station with major design concerns this is proving very interesting indeed.
In Northern Ireland you have your own Health & Safety Executive. Tell us how that works and what relationships exist between PLA’s and your HSE? The Health & Safety Executive Northern Ireland (H.S.E.N.I.) is the same as the Health & Safety Executive in G.B. in terms of set up and structure and deals with petroleum through partnership arrangements. Within our Regional Petroleum Licensing Group one of our committee members, Sean Martin, sits on the Fuel Oils Liaison Forum – a partnership forum with the Health and Safety Executive Northern Ireland.
I seem to recall that you had a successful prosecution last year. Can you explain how that came about?
We had a number of prosecutions in 2007 & 2008 for storage of petroleum without a licence. In 2008 we refused a Petroleum Licence in respect of one filling station. In Northern Ireland any appeal for refusing a Licence is made to the Health & Safety Executive. In this case the operator exercised his right to appeal. After investigating the Health & Safety Executive upheld our decision on all but one point.
I believe you multi task so what other duties on licensing are you responsible for and do they involve health and safety aspects?
The role of Licensing Officers in Northern Ireland is very much a multi task role. Our responsibilities cover petroleum licenses, entertainment licenses, amusement permits, street traders, places of marriage/civil partnership, registration of hairdressers etc. Obviously there is a health and safety aspect to many of our functions. In Northern Ireland we are currently working towards the introduction of The Fire Safety Regulations (NI) 2009 (akin to the Regulatory Reform Order in England). Licensing Officers here are currently in negotiation over the role they will have in relation to the Order. Petroleum Enforcement Liaison Group (PELG) Do you have a similar Regional Group that deals with purely petroleum matters?
We just established our Regional Group at the end of last year. This group reports to S.O.L.A.C.E. (Society of Local Authority Chief Executives) and to the Fuel Oils Liaison Group. We have developed a work plan and hope to harmonise policies and procedures throughout Northern Ireland. This would be very beneficial to licensees and enforcement officers.
Moving away from the “Day Job” do you have other interests beyond work or what do you do to relax?
My partner is a big fan of motorbike racing, so I accompany him to races. We also have friends who own hot air balloons and each year we go with them to various ballooning festivals throughout Europe. However I would say that neither is very relaxing – I think I sleep to relax!
Here is a typical cliché type question – what would be your idea of total success?
A typical cliché type question deserves nothing less than a typical cliché type answer, so my idea of total success is living a life of contentment, happiness, love, health, vitality while providing my own unique value to the world.
So where would you like to be in 5 years time?
I suppose if I am honest I would love to own a business of my own – so who knows hopefully I might be able to sell my unique value!
Thank you Maureen, a pleasure as always to talk to you and I think I am coming over soon to give some technical support to your colleagues so I look forward to that and have to say that I really like coming to Northern Ireland as it is a wonderful place.
APEA tel/fax 0845 603 5507 www.apea.org.uk 57

Q I am inspecting a Filling Station and cannot locate any records that the drainage system and site Separator has been checked or cleaned. Is there anything I can do as the Inspecting Officer to satisfy myself that the drainage system is in order?
Answer Yes there is. As a very crude test locate some tissue paper or paper hand towel. Something that is light and absorbent. Lift the separator cover lid and screw up the tissue paper and drop into the separator itself. If the paper disappears in few seconds it is likely that the separator is heavily contaminated with fuel and requires an uplift and cleaning. You can do this with a Three Stage Interceptor as well
What has happened is that hydrocarbons have soaked into the tissue paper and caused it to become heavy and it sinks below the surface of the separator liquid level. It is a simple but effective method. By the way do not forget to walk the drainage runs (AO Drainage Channels) along the Tanker Stand, Dispensing Area and Entrance/Exit points to ensure the channels are free from refuse and debris so that any spillage can flow back towards the separator
Brian Baker, Milton Keynes Council
Q I know that on a Stage 1b Vapour Recovery System there is a Pressure and Vacuum Valve Fitted at the top of the Vent Stack. Can you explain why it is there and how it works?
Jamie Thompson Chairman Technical Committee
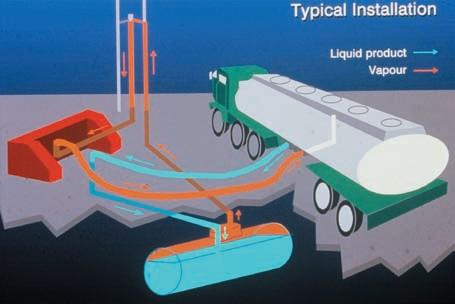
Q In the definitions of the Standard Licensing Conditions is a term called “The Approved Arrangements” can you explain what this actually means and why is important from a Petroleum Licensing point of view?
Answer I should start by saying that the Petroleum Licence conditions to which you refer are the ‘model licence conditions’ that Petroleum Licensing Authorities (PLA’s) were advised to use from August 2006. This guidance is provided through PETEL 65/61 which can be found on the HSE Web Site -http://www.hse.gov.uk/lau/lacs/6561.htm
The full definition reads as follows:-
1.1Approved Arrangements means those arrangements relating to the design, construction and mode of operation of the licensed premises, which accord with the plans and specifications approved by the Petroleum
Licensing Authority.
Answer Stage 1b vapour recovery takes place while the road tanker is delivering fuel to the underground tanks.
The object of this is to restrict the vapour which would in the past have come out of the tank vent pipe, and return the vapour through a vapour recovery hose back in to the vapour space of the road tanker. The saturated vapour is then returned by the road tanker to the terminal and when the tanker is next loaded the vapour is sent to a vapour recovery unit in the terminal which converts it into fuel.
The Pressure Vacuum valve (P&V) is normally situated at the top of the petrol vent pipes, the vent pipes are usually joined together, at either low or high levels.
The Pressure setting of 35mbar on the P&V valve means it will not open until the pressure at the P & V valve reaches 35mbar. This encourages the vapour to return to the road tanker during delivery, but if there is a pressure build up in the system it will allow it to be relieved. It also restricts vapour losses from tanks during quiet periods.
The vacuum valve setting is 2mbar and is needed because once the delivery has taken place fuel is then sold and air comes back into the tank to replace the fuel dispensed through the pumps.
All P&V valves should be protected by an end of line flame arrestor approved to EN 12784, this is a legal requirement.
While the majority of P&V valves are fitted on top of the vent pipes some manufacturers have installed these at lower levels for ease of maintenance, but the flame arrestor in all cases should be on top of the vent pipe.
The actual Licence Condition that refers to ‘Approved Arrangements’ is:-
2.3The Licensee shall not undertake or permit to be undertaken any material alterations to the approved arrangements, unless the written consent of the
Petroleum Licensing Authority has been obtained.
The definition of ‘material alterations’ is also given within the licence:-
1.2Material Alterations means any alteration, which could affect the risks from fire and explosion at the Licensed Premises and will include: -
- the change of or cessation of use of the licensed premises;
- the removal; temporary or permanent decommissioning; repair; replacement; modification; or installation of any tank used for the storage of petroleum-spirit and any pipeline or vapour pipeline associated with the storage and dispensing of petroleumspirit;
- the change in use of a tank used to store petroleum-spirit;
- the removal without replacement or installation of any petroleum-spirit pumps/dispensers; the removal or installation of any part of the site’s leak detection, spillage or delivery control system;
- the installation a of pump/dispenser in a new location;
- a change in the Mode of Operation of the dispensing equipment;
- the removal or installation of any electrical equipment within the hazardous areas of the licensed premises; - the storage or cessation of storage of any other dangerous substances on the licensed premises.
I believe that this gives clear parameters for the approval and licensing of petrol filling stations. The PLA must ensure that a proposed new build or knock down and rebuild of a petrol filling station is designed to be constructed in compliance with current guidance i.e. Blue Book and appropriate European Standards. Once approval has been granted, and construction started, the PLA has to be satisfied that the site is constructed as per the approval. On completion of the works, and on receipt of the necessary test certificates, the PLA must collect the licence fee and issue the licence.
Once the Petroleum Licence is in force, it is the duty of the licensee to comply with Licence Conditions, including the seeking of approval for any proposed alterations.
To ascertain that unapproved alterations have not been carried out, the PLA needs to ensure that they have an audit trail of what has been approved. This is not just a bureaucratic exercise; it is to ensure that the right level of risk control is maintained. To give an example of this, I can quote a case where a licensee decided to carry out a grade change, and swap diesel and petrol between two tanks, they did this without approval, and as a consequence petrol ended up in a 50+ year old single skin steel tank, with no history of being installed to a standard suitable for petrol, with the tank venting directly above a window of neighbouring premises, and the diesel tank was vented into the Stage 1b vapour recovery system, when this was discovered during a periodic inspection, enforcement action was promptly taken. To ensure that the ‘approved arrangements’ are clear to both the licensee and the enforcing officer, some PLA’s include approved drawings and a schedule to the licence showing all equipment that has been approved, the types and ages of the tanks, the safe working capacities of the tank compartments the fuel stored and the dispensers served by those tanks. As there is another Licence condition requiring a copy of the Petroleum Licence to be kept on the licensed premises, this information is always available to both Petroleum Inspectors and site staff.
Ray Blake Head of Petroleum, London Fire & Emergency Planning Authority
Q In respect of electrical fuel pumps I have heard the term the “Zener Diode Barrier” What does this mean, what is its purpose and how does it work?
Answer Thanks very much for the question, I could of course just give a one sentence answer, that it is what’s called an “Associated” piece of apparatus for an intrinsically safe system. However this answer I do not think would mean anything to anybody other than suitably competent electrical technicians and Engineers. What I would say since you have given me the space to answer in more detail is that a Zener Barrier is an absolutely critical device where one has an Intrinsically safe system/Circuit. These devices, and I have put in some pictures (courtesy of MTL Instruments) were introduced in the late 1950’s as “Shunt – diode safety barriers” when process controlled computers were starting to be widely applied in the chemical process industry and have been used ever since. The name Zener has been used loosely when talking about these devices because one of the barriers three principle components is a Zener diode the other two being a resistor and a fuse.