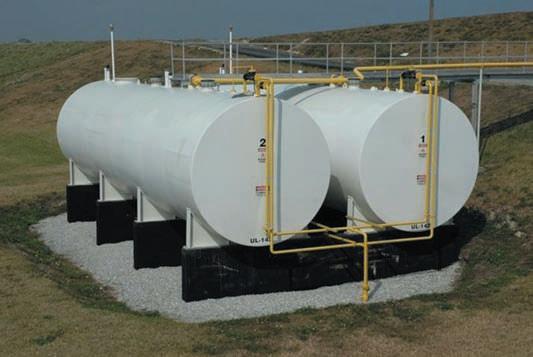
21 minute read
Press Releases
approach across the country with the Blue Book providing a good reference guide.
You know, hand on heart, all the years we have been dealing with licensing authorities I can honestly say we have never found ourselves in a corner with any licensing authority, albeit we have come close on some occasions but not, I would hasten to add, of our own making.
Advertisement
Have you worked on any jobs outside of the UK? I wonder what obstacles you found with going outside our borders.
No, we have not done anything outside of the UK since the late 1980’s when we did a little bit of work in the Middle East. I would not discount the opportunity of carrying your bags on some of the overseas ventures to bring to the table whatever we may be able!
Is everything you do nowadays based on computer assisted drawing? (CAD)
All work we carry out in the office is electronically produced and has been since probably 1995. It was Total at the time who instigated that switchover from drawing board to CAD and I guess during that 1994 –96 period we became a CAD based practice.
I guess you deal a lot with main contractors and civil engineers. Is that a particular daunting experience?
Dealing with principal contractors, both of a building and engineering discipline is a part of the everyday life and in general we are probably fortunate that the majority of whom we are involved with are well experienced in the field and have proven track records. Again, I think there has been a shift from general building contractors performing any work of a petroleum nature and this has benefited the industry enormously. This makes our life easier and also delivers far improved procedures during the construction phase and a finished product article of much higher quality. Those contractors who historically hung on to the ‘shirt-tails’ of the industry and been reluctant to change have slowly been identified and seem to have moved on to other things. This being a fast track industry, what has been for you the quickest new site you have been the architect for?
As a practice when construction times back in the early mid-90’s became what I considered crazy, we were fortunate enough never to be involved with those particular clients, but since then sense seems to have prevailed which has also been brought about by more constrained regulation and particularly with respect to health & safety and in general time-frames for construction of sites is now far more reasonable.
The ‘fast track’ effect on us as a practice is during the preconstruction phase where a client will require either planning or construction packages to be prepared in a short-time frame and you just need to be flexible in your approach in order to be able to deal with this. Once construction starts the pressure then invariably switches to the main contractor to deliver.
If you could change anything what would it be?
The planning system. Planning is a big factor in turning development sites around together with the utility and highway matters, which are a major consideration in any programme. But whilst not wishing to dwell on this aspect, where circumstances require LPA’s (Local Planning Authorities) to perform and for the record we once obtained a detailed planning permission for a Brownfield petrol filling station development site in 2-days. That must be a record, which I doubt will ever be improved upon by us. I cannot mention the LPA concerned nor the site, but needless to say there were political and other internal factors which prompted the LPA to deal with the proposal in that manner, but notwithstanding this case, the system needs to be changed.
As an architect you must have had some odd requests. Is there anything you can share with us?
I don’t recall anything in particular but asking Peter my business partner who joined me in 1983, he reminded me of an instruction we had to look at, putting a roll over wash on the first floor of a very constrained town centre site, which sadly now no longer exists but needless to say it never happened.
I guess we have seen a hard recession hitting the UK. What have you noticed about these recent times and do you see signs of any recovery?
I am sure what we are seeing is no different to most other contractors, consultants and suppliers within the industry in so much as margins are squeezed, expectations are elevated and long-term forward planning is now a thing of the past. As far as recovery is concerned, I have no idea as any specialised ‘industry’ seems to follow a set pattern and I don’t think the roadside industry is any different in so much as when one is busy, all are busy, when one closes their books they all do.
I cannot believe you spend all your time at work so what do you like doing when not at the drawing board?
Over the years I really have spent most of my time working. I think it is just a consequence of the nature of this industry in so much as we have always worked countrywide and a fair amount of ‘ones’ time is spent on the road, which has tended to increase the working week. However, I cannot bemoan this fact as over the years we have been very fortunate to have maintained a healthy level of work, had some good times and been able to maintain a very stable group of people within the practice.
Outside of work I try to put a few ‘gym sessions’ in each week and stay fit and maintain my youthful looks!!
Neil, thank you for taking time out for us and for what has been an interesting interview and we wish you well for the future
Brian, it was a pleasure and I’ll never forget our first meeting which was on a site in Milton Keynes when we were proposing a re-pump for Apex during 1988, the site has since been redeveloped on a couple of occasions for different owners/Licensees etc. but it has always been a pleasure working with you, being one of those individuals with whom we have referred many a matter and issue to.
52 APEA tel/fax 0845 603 5507 www.apea.org.uk
By Marshall Mott-Smith President Mott-Smith Consulting Group
Florida’s regulatory experience with shop-fabricated storage tank systems began in 1983 when the Florida Legislature passed the Water Quality Assurance Act. Since then, thousands of these storage tank systems have been installed in Florida, particularly in the past ten years in response to homeland security issues and the need to provide fuel for emergency power generators during hurricane season. Florida’s regulatory experience with shop-fabricated tanks has been beneficial in that no other state in the United States has regulated these systems for so long and with such stringent standards, and this experience and information can be helpful to other regulatory entities, to industry, and to storage tank professionals.
Background Information
The Water Quality Assurance Act gave the Florida Department of Environmental Regulation (DER now called the Florida Department of Environmental Protection - DEP) the authority to regulate all aboveground storage tank systems (ASTs) with capacities greater than 550 gallons. The law also gave DER the authority to regulate underground storage tank systems. The DER adopted rules for storage tank systems in 1984, and these rules were amended in 1991, 1994, 1998, and 2004.
There are 186,000 registered storage tanks and approximately 54,000 registered facilities with storage tanks that are either in service or were previously in service. Only 21,000 of the 54,000 registered facilities are currently active. There are currently about 50,000 active regulated underground and aboveground storage tanks. About 23,000 of these are currently in aboveground service. Retail facilities make up 38% of the a c t i v e regulated facilities, with another 33% in a fuel-user category, and 18% in government use. However, there are approximately 35,000 reported discharges of petroleum in Florida. The large number of leaks and the fact that the state obtains about 92% of its drinking water from groundwater resources is why Florida has some of the most stringent tank rules in the United States.
Florida’s Rules for Shopfabricated Tank Systems
Florida’s AST rules reference industry standards by the American Petroleum Institute, the National Fire Prevention Association, the Steel Tank Institute, and many others. The rules include a number of exemptions such as mobile tanks, residential tanks, and heating oil tanks, but all new tanks and piping that are in contact with the soil must have secondary containment (This requirement has been in effect since 1990). Secondary containment for shop-fabricated ASTs can be either an impervious barrier like concrete or a synthetic liner, or it can be in the form of a double-wall or double-skin tank. The construction for piping secondary containment is typically doublewall. AST systems must have overfill protection, spill protection, antisiphon valves, and interstitial monitoring for leak detection. Owners must comply with regulations for registration, notification, repairs, operation, maintenance, financial responsibility, recordkeeping, closure, and must use DEPapproved equipment.
Florida’s Compliance Verification Program
Florida’s Compliance Verification Program for storage tank systems began in 1984 and is accomplished by contracting with local governments. There are approximately 120 inspectors across the state, and these inspectors have performed over 600,000 inspections since the program began with an average of 25,000 inspections per year. The contracts require the county inspectors to perform routine inspections, non-compliance reinspections, installation inspections, closure inspections, discharge inspections, and complaint investigations. All inspections are entered into the program’s innovative data management system that was primarily developed by the inspectors. The inspection processes and work-flows were designed into the software contained in their ruggedized (toughened) field laptop computers. This paper-saving system gives owners, operators, consultants, and other interested parties the ability to view inspection results on line in real time the day after an inspection report is entered into the system by the inspector, and has
APEA tel/fax 0845 603 5507 www.apea.org.uk 53
improved the consistency of inspections.
Most owners of Florida shopfabricated ASTs comply with Florida’s rules, and there is a high rate of compliance. When facilities are out of compliance, the DEP District Offices and several Counties with DEP-authorizations are responsible for pursuing enforcement of the rules in accordance with the states rules and laws.
The Florida Leak Autopsy Study
The DEP-County inspectors participated in a Leak-Autopsy Study that was performed between January 1, 2003, and July 1, 2008. The purpose of the study was to gather data about the sources and
causes of leaks in the State from all underground and aboveground storage tank systems. The inspectors were usually on-site within three days of the discharge notification by the owner or operator. They completed a five page form that documented the conditions at the facility and captured information about the storage tank system such as leak detection equipment, tank and piping data, the success of the leak detection system, the effects of the contamination, and other important facts. Photographs and other supporting information were attached to the forms, and a comment section was provided for the inspector’s observations. If the inspector was unable to identify the source of the leak, the data was excluded from the study. The charts below show the sources and causes of discharges from shop-fabricated tank systems.
The data shows that the main source of discharges from the shopfabricated tanks in the study is the tank itself, followed by s m a l l diameter piping and dispensers. If there was an overfill, the tank was
considered the source of the discharge. The main causes of discharges from shop-fabricated systems in the study include overfill, loose components (usually associated with piping), and spills.
The study contains much more information about discharges from shop-fabricated tank systems in Florida than can be mentioned here. Although the Leak Autopsy Study was suspended by the Florida Department of Environmental Protection in July, 2008 due to budgetary constraints, it is still important in that it provides actual field data about the sources and causes of leaks. It helps support industry and owner equipment selection decisions and provides data for insurance company actuaries for risk management evaluations. Before the study, this information was only available as anecdotal evidence.
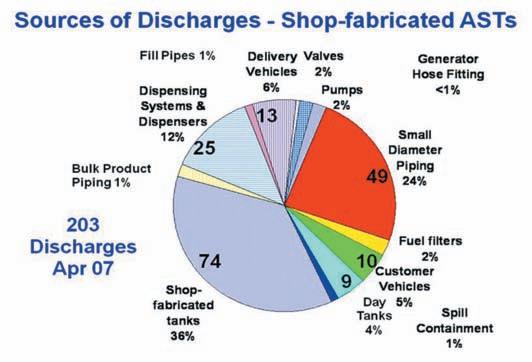
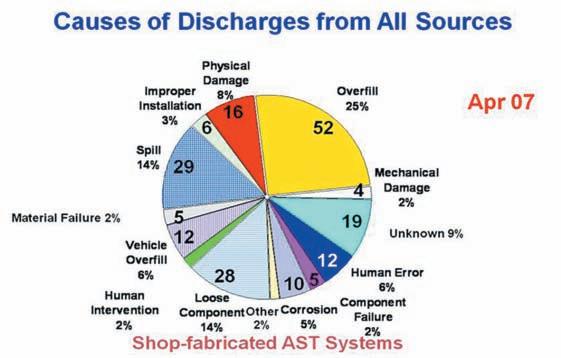
Unusual situations
There are a number of unusual systems in use (some of which are exempt from regulation) that inspectors encountered in the field. For example, the tank below could be truly characterized as an aboveground tank.

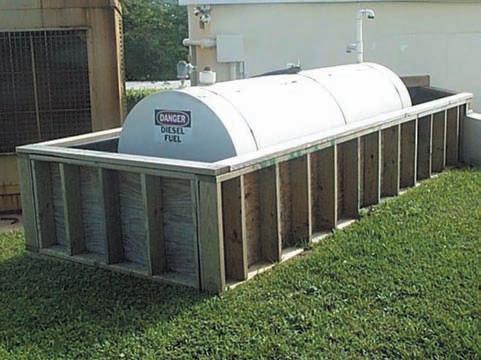
The photo, on page 54, shows a tank with improper secondary containment – (wood not exactly in accordance with the fire codes).
Florida also has a great deal of experience with hurricanes, and has learned many lessons about the types of systems that provide the most effective defence against hurricane force winds, surge, and flooding. The following photos depict some of these experiences.
In the photo above, a vaulted concrete tank manufactured by Convault survives Hurricane Ivan in 2004, in spite of a near collision from a large recreational powerboat. The next hurricane photo from the same storm shows damage to the dikewall and piping system from storm surge. Wind damage is a problem as well, particularly with vertical shopfabricated tanks. Flooding can also damage tanks and piping, and many Florida tank owners have experienced tank “float-offs” from improperly anchored systems.
After events on September 11, 2001, as well as the numerous hurricanes in the middle of this current decade, many government and private entities have decided to install shop-fabricated storage tank systems to provide fuel for emergency generator systems. There has been a significant increase in the number of the tanks,
particularly as doublewall sub-base generator tanks as shown in the photograph above. A particular lesson learned from Hurricane Wilma was that the smaller shopfabricated tanks did not provide sufficient storage capacity for power outages longer than four days. Although it was forecast to diminish in strength after landfall, Hurricane Wilma came ashore in 2005 as a Category Three Storm in Southwest Florida, and exited the Central east coast as a Category Three. Tanks with 500 to 1000 gallon capacity could not keep up with the flow-rates needed to keep the generators operating, and this led to power outages at hospitals, nursing homes, and assisted living facilities. Since then, owners have installed larger tanks to meet the additional demand.
The State of Florida has been regulating aboveground and underground storage tank systems for twenty five years. The number of shop-fabricated storage tank systems has more than doubled during this time, and are increasing in number every year, while the number of

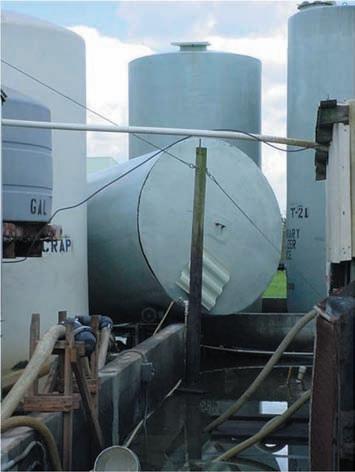
underground storage tank systems are slowly diminishing. Since most leaks begin as a small drip or weep as opposed to a spew or stream, shop-fabricated tanks are often favoured by owners because of the ability to find leaks early and correct small problems before they become large problems.
They are usually easier to maintain, and the insurance premiums for double-wall systems are much lower than their underground tank cousins. Owners need to provide sufficient security, and need to be mindful of inventory and their overfill protection system to avoid overfills. If properly constructed and maintained in accordance with fire codes and environmental rules, they can provide equal or superior service to UST systems.
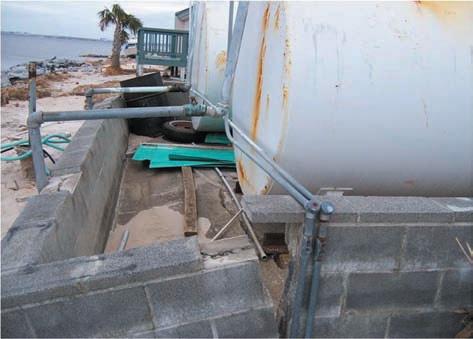

History of Petrol Stations Part 13 The Electric Petrol Dispensers
By Jamie Thompson
The next development from the hand operated petrol pump was the move towards a more mechanised powered delivery.
The fitting of an electric motor and pump to the existing hand operated pump started a dispensing revolution which has evolved into the pumps/dispensers that we see today.
The first design was to use an electric motor to do the work of the hand operated pump; the measuring bowls remained much as they did before but the motor had to be a safe one and sparking motors were obviously dangerous! Already within the mining industry electric motors had been developed for use in the methane atmospheres that were often found in mines and the explosion proof designs that were used in this industry soon became the safe way for the petroleum industry to proceed.
Many of these pump designs were quite unusual compared to modern dispensers; Wayne produced an Art Deco design called at the time the ‘Worlds most beautiful petrol pump’! These new designs had m e t e r s measuring the fuel dispensed and clock face displays showing the amount of fuel b e i n g delivered to the customer. Many of these dispensers have been used for over 60 years.
In the UK Sheffield

University’s mines department had been authorised to test and approve electric motors for use in h a z a r d o u s atmospheres and this was the early forerunner of the ATEX test houses that we see in the industry today.
As the industry became larger and oil companies ordered more of the same type, production lines were set up by the larger pump manufacturers and the almost universal method of display became the Veeder-Root mechanical head.
This consisted of a complicated set of cogs which moved as the fuel was dispensed indicating the
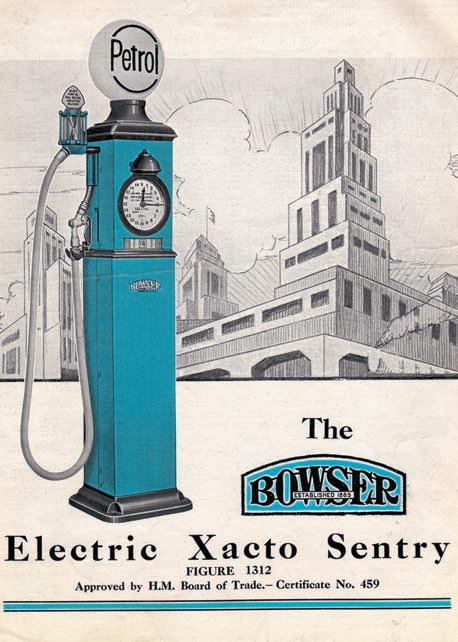
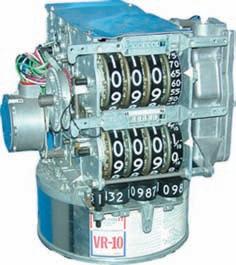
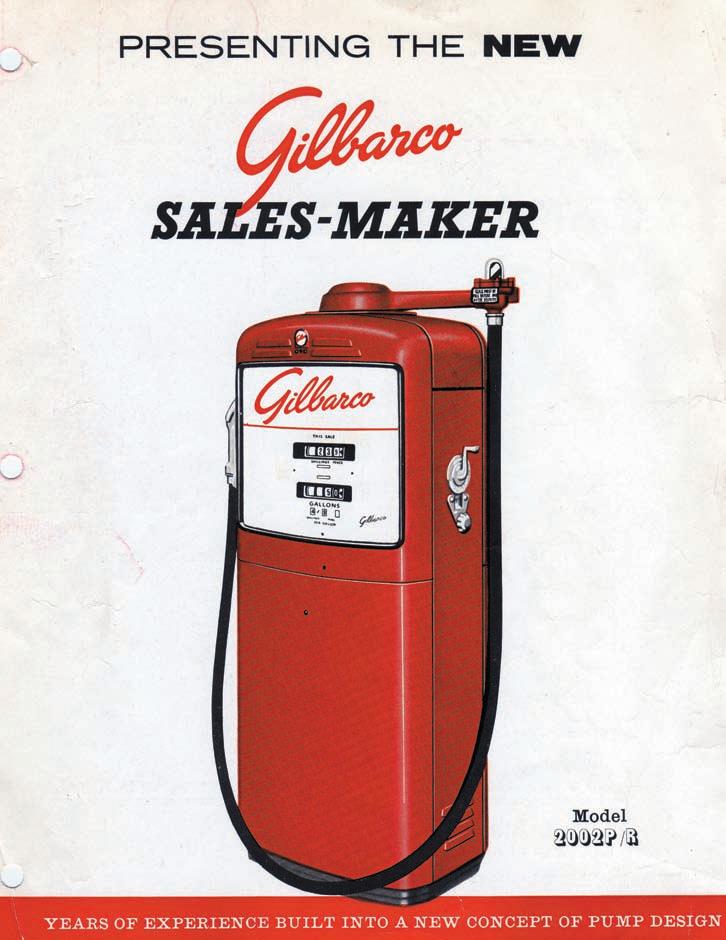
amount of fuel being sold together with the price of fuel and many of these systems are still in use in many parts of the world.
The dispenser designs eventually became smaller and more compact and the inside of the dispenser became more crowded, electric lighting was installed inside the display faces.
Perhaps the biggest change was dispenser design, which varied between companies. Many of the smaller companies had by this time stopped production and the largest companies relied on manufacturing larger numbers to survive for a while until eventually some mergers and closures took place within the industry.
The other large change in the development of the petrol pump came with the advent of self service and the introduction of electronic heads in dispensers. The LED/LCD displays and eventually computer screens changed the maintenance industry and the engineers dealing with the dispenser heads needed to be experts in electronics as the boards used chips rather than cogs.
The pump designs also had to meet the expectations of customers, with preset meters and limiting devices and then along came blending when fuel of different grades were blended to suit the marketing vogue at that time. Perhaps a larger revolution which did not quite make it was the use of dispensers with no hydraulics inside. The design allowed for either submersible pumps or remote pumps to serve the dispensers. The uncluttered forecourt proved to be a success but the high costs of production and installation perhaps ensured that this design did not quite make it into the modern era.
I also recall looking at proposals for robot filling stations which have been installed in Europe and USA but again it has not yet found favour in the UK.
The development of the dispenser is continuous and with card readers and TV screens on dispensers I am sure we will see many innovations in the years to come.

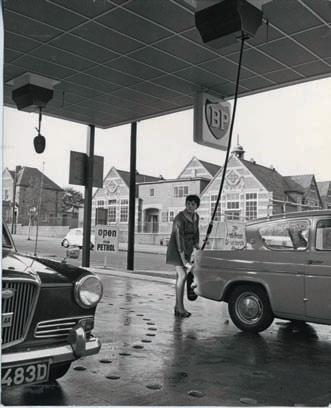
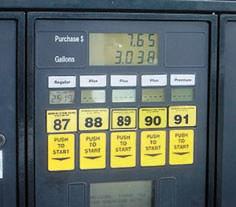
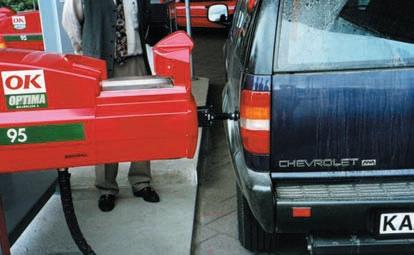
As a Petroleum Officer I was notified by an SIR company of a suspected loss of fuel from a petrol tank. To confirm the loss a precision tank test company came and put a small pressure on the tank and confirmed failure. The situation got worse when it was discovered that over 20,000 litres of fuel were lost immediately after the test. Was the action correct?
It is of course easy to be wise after the event.
Generally you should not put pressure on a tank with fuel inside the tank because if the tank is leaking then you risk pushing more fuel into the ground. Having said that the pressures used in precision tank testing are usually quite small but the tank testing company and the tank owner should be looking at the situation and assessing how much fuel was in the tank and the method of precision testing. It really should be risk assessed. In this case with a large amount of fuel remained in the tank an alternative precision tank test using a small vacuum may have been more appropriate.
Jamie Thompson Technical Committee
Can cable that is not MICC (Mineral Insulated copper Cable) be used in a Hazardous Area
The cable types for hazardous areas of filling stations can be either; 1.Mineral Insulated cable meeting
BSEN 60702-1 Requirements 2. Armoured cable with PVC, XLPE or equivalent insulated conductors and sheath etc.
Paragraph 14.9.10 in the “Blue Book” clarifies the types.
Although MICC is still widely used some companies do use the far less expensive steel wire armour.
However, and this must be taken into consideration, the current carrying capacity of MICC cables is far superior to a similar sized steel wire armoured cable. So the problem for the electrical designer and installer is that they would need to install physically larger sized cables when using steel wire armour hence duct requirements i.e. size of ducts may be larger than equivalent for MICC, also the size of termination glands and space available inside dispensers and in particular submersible pumps may make Steel wire armour impractical.
Gareth Bourhill, Electrical Consultant
A Developer in my area is requesting to surround the new tanks in concrete as a backfill. Is this still allowed in the UK?
Unless there is a very specific environmental or safety case supporting the use of concrete as a backfill material, then no it should not be used. The reason for this is that the European Standard that applies to the Installation of Underground Steel Storage Tanks BS EN 12285 Part 12003 specifically covers not just the manufacture of the tank itself but the installation method as well, which in Annex A of this 168 page standard calls for a “Non cohesive granular mix”, compacted sand or crushed stone to be used.
This is because the installation process allows for the easy retrieval of the tank should it fail or wish to be removed for some reason and this in itself addresses any pollution issues, bearing in mind that anti pollution laws in the UK arrived in 1990 with the introduction of the Environmental Protection Act 1990. A further point is that on completion of the installation, the installer, usually the main contractor is required to provide a Certificate of Conformity (see page 48 of the Blue Book – March 2005 edition) that includes the installation process itself and complies with the European Standard.
We should also remember that the UK was one of the only countries in the World that used concrete in the past to surround tanks. In Europe all countries use a granular backfill and that has proved most satisfactory over many years.
Brian Baker APEA Training Committee
Is the publication known as the Design, Construction, Modification, Maintenance and Decommissioning of Filling Stations APEA/IP March 2005 otherwise known as the “Blue Book” mandatory?
The publication you refer to as the “Blue Book” is a Guidance Document and is not mandatory, but it represents the best practice and by complying with this guidance you will demonstrate that you have normally done enough to conform with the current safety and environmental legislation. The guidance has been written by experienced technical and legal practitioners within the industry and this has included a wide variety of interests including all major representatives of the UK Downstream Industry including the following; Health & Safety Executive (HSE), the Association for Petroleum & Explosives Administration (APEA), UK Petroleum Industries Association (UKPIA), Association of UK Oil Independents (AUKO1), Petrol Retailers Association (PRA), the Environment Agency (EA), the Electrical Contractor Association (ECA), the Energy Institute (EI), the Forecourt Equipment Federation (FEF), LP Gas Association (LPGA), National Inspection Council for Electrical Installation Contracting (NICEIC), Petroleum Equipment Installers and Maintenance Federation (PEIMF) and Scotland’s Trade Association for the Electrical, Electronics and Communications Systems Industry (SELECT). Consequently these organisations will have contributed and been consulted on the final content of the document you refer to as the “Blue Book”. The document itself is supported by, and makes reference to, numerous European standards which the reader may have to refer to if a specific question is not answered by the Blue Book