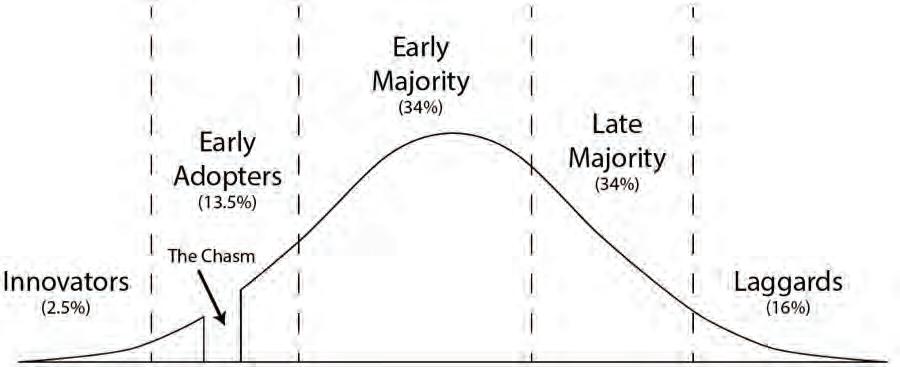
6 minute read
Are You Concerned About Equipment Uptime? You Should Be
by apeauk
By Philip Reese, Evenlode Roadside
You can have a maintenance solution that keeps your network running.
Advertisement
Every operator should have a focus on achieving the best possible uptime of their equipment. Whether this is food and drink, valeting, fuel equipment or establishing your EV footprint, reliability has been the topic of much discussion in recent months.
Customers have high expectations for equipment availability as and when they need to use it. As a society we have now become accustomed to having everything available at the touch of a button or a swipe of a screen.
Maintaining your uptime (or reducing and eliminating downtime) is important for many reasons, including:
-Revenue generation
-Inconvenience
-The expectation that after 100 years of refuelling, that your visit to site will be quick
-Ease of use
-Brand reputation
-Minimising break fix costs
Bad news travels faster than good news, and a bad reputation sticks. If a customer has a bad experience, it can take some time to re-build their belief in your offer, assuming they come back at all.
New technologies
The internal combustion vehicle and hence the forecourt model has been generally very stable for the past hundred years. Very few other types of technology have been so constant for so long. However, there is a growing possibility that the world may undergo significant and rapid change.
The quickly changing narrative for new technologies such as EV is the first really seismic change that the forecourt industry has been faced with. Growth rates for EV adoption are beginning to gather pace, for new sales at least. Whilst the overall market penetration is still around just 2% in early 2023 (volume of overall vehicles on the road), it is forecast to grow nine-fold by 2025, and that’s less than 3 years from now.

In terms of the technology adoption curve, and despite the sudden kick start to these changes, the evolution is still very much in the first phase – “innovators” - and is only just beginning to move towards the “early adopter” phase.
This matters on a number of levels regarding:
-The uptake of EV vehicles
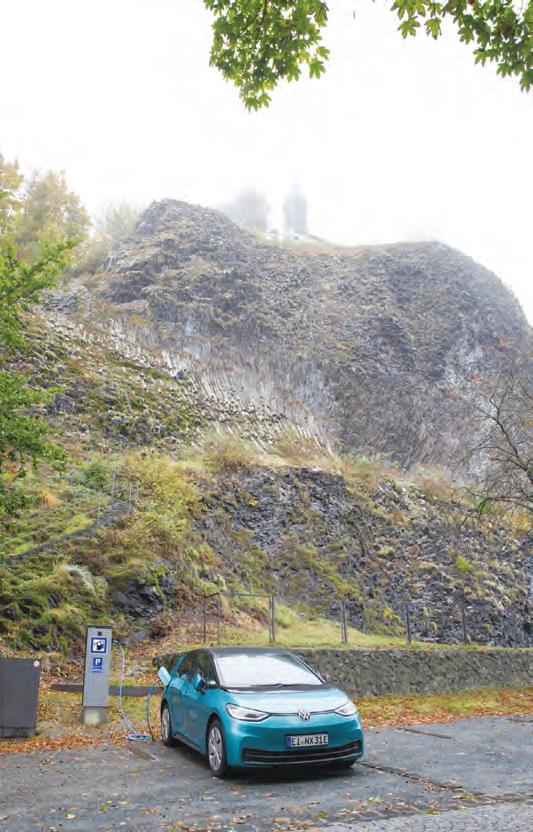
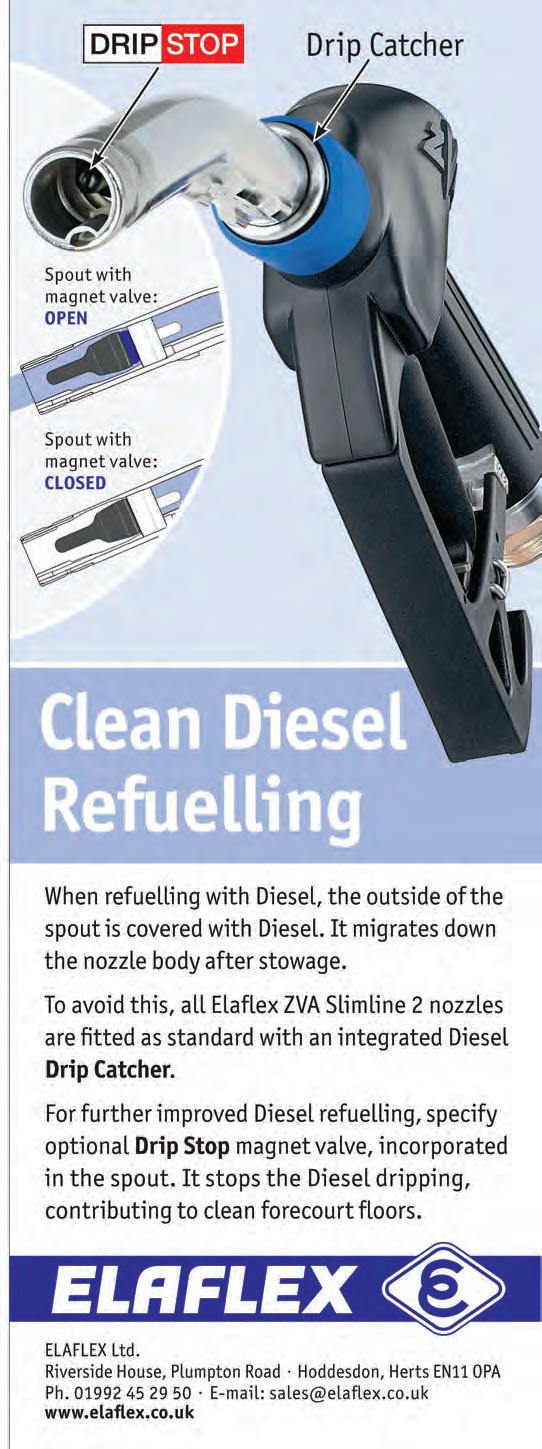
-The number of chargers actually required now, in the medium and longer terms
-What a more mature market with ageing EV’s and infrastructure might look like
Whilst the “innovators” have willingly moved readily, before the “early majority” will engage with the uptake they will need to be convinced that the new technology is right for them, and, that the infrastructure in place is reliable.
The ability to achieve best practice maintenance and maximise uptime is extremely important. It especially matters to those who wish to see cleaner technologies succeed and it also matters to the operators who wish to see a good return on investment, a strong brand image and satisfied customers. But what factors affect this uptime?
Why does equipment fail?
At some point all equipment fails, and it fails for various reasons. This can include impact damage, wear and tear, weather damage, interaction with the public, poor design, cheap components, and so on.
New technology has to contend with all of these factors, and it also has to contend with the often incalculable element of human interaction, especially where the equipment or technology is new or unfamiliar. New can also mean unproven. New can often mean a lack of real time reliability in the real world. “Innovators” are unique personalities and are always strong advocates for the new technology, and potentially more risk oriented. They often fit the mould of having a technology or engineering mindset and will be tolerant of minor mishaps. Of course, much of the general population does not fit this characteristic.
Why are new technologies hard to get right?
There are many reasons why new technologies often experience teething issues which can negatively affect their reputation for reliability for a long time:
-Over Optimism. “What can go wrong?” Everything in the testing environment worked fine but that is very different from the field.
-The overselling of “zero maintenance needed” and remote diagnostics. When this does not occur, neither the planning of resource nor the required budgets are in place.
-The speed of getting to market and fear of not “getting left behind” can mean critical issues can quickly manifest themselves across a wide portfolio of sites where equipment is installed with no remedy to resolve it readily to hand.
-Supply chains for new technologies are typically immature, and relationships have often not been forged or stress tested.
-As demand ramps up exponentially, purchase choices are often based more on what is available rather than the optimum selection process. This can lead to a non-standardised offer and complications in the supply chain process.
-Where people are striving to connect new equipment there can be an incompatibility of multi systems language or code feeding into a single software management solution.
-New technology evolves fast, meaning the rate of obsolescence is rapid. Much of what is installed today could easily be obsolete or unsupported in just a few years’ time. The demand for faster charging of EV’s is a great example of this.
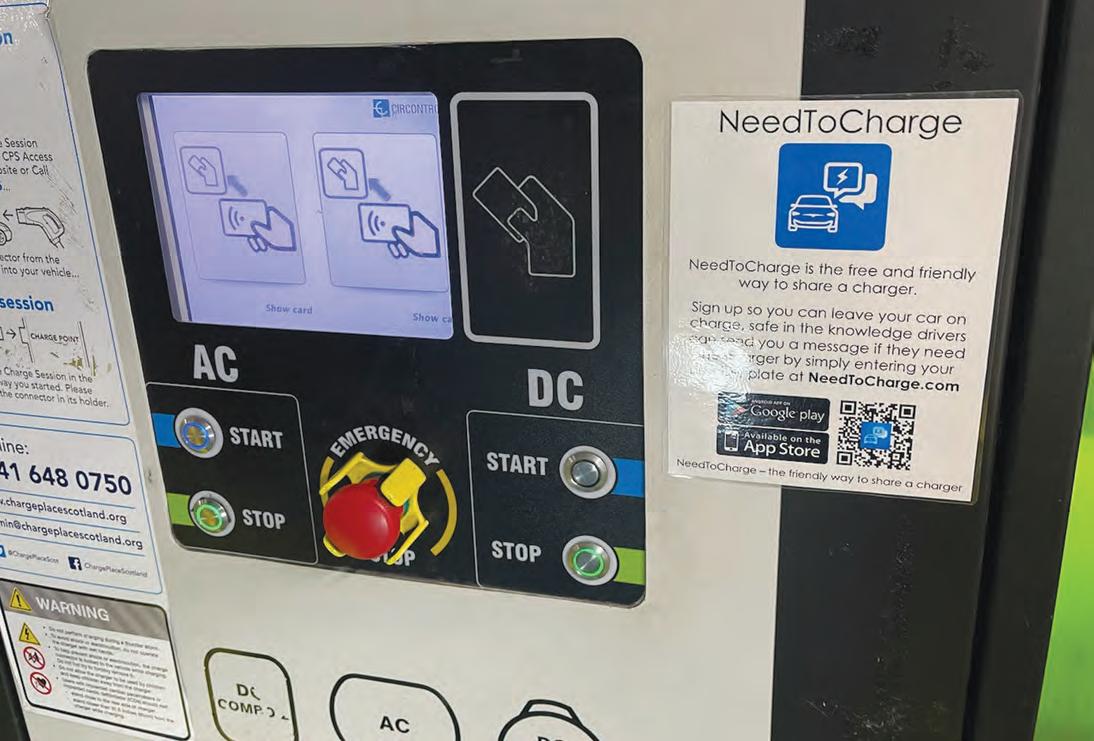
Early innovator periods typically also result in investment flooding in, as happened with technological jumps in the past, such as the dot-com bubble. Whilst ultimately the technological step change will stick in some way, many of the early companies are not the ones who ultimately survive.
Why does it take so long to get equipment fixed?
The challenge in getting equipment fixed is not just resource driven, in terms of; what is my engineer density, do I have the right skills in the field for new technology and how quickly can they drive to site? It is also driven by the availability of spare parts and a reliance on other third parties’ software to help bring the equipment back to life through remote rebooting of IOS upgrades.
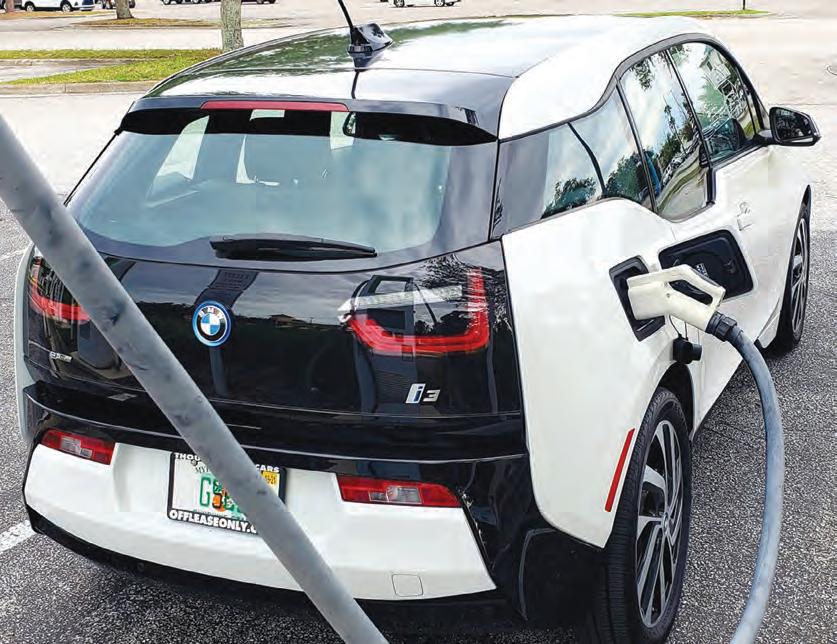
With new equipment that has a heavy reliance on software operating systems (as opposed to nuts, bolts and belts) there are more challenges:
-Arrangements for reporting the fault. How does the customer experience get relayed to the operator? Is equipment downtime monitored remotely? Are you relying on a customer to call a help line? Do the site staff report the issue centrally? Or can all four things happen at the same time?

-The workflow for arranging for repair or reinstatement – who or which system does what and when? If multiple systems are being used for managing a repair are they all connected, do they communicate together or is everything still held together by emails and phone calls?
-The supply chain is not aligned with the operator’s need for prompt rectification – this can include coordination of warranty, competence issues, parts availability, resourcing, readiness, no expectation of failure and communication.
-Commercial viability of rectifying. Who pays? If the usage of the equipment is low and input energy costs high is there misbalance between potential revenue and the cost of repair in an immature market? Is there sufficient commercial tension between operator and maintainer, not to mention enough scale, to result in efficiency? How much pain can be tolerated before the gain kicks in?
Considerations for site operators
As time progresses all of these factors will only be compounded as the expansion of new technologies continues at pace. Should the inevitable market consolidation occur (where some start-up companies rise and others fall) where will that leave the maintenance of the new equipment?
It is quite possible that as obsolescence naturally occurs, there will also emerge a need to start considering the replacement of the “new” equipment within this decade. This will present its own challenges, including availability, selection, coordination, resourcing, and disruption. It is also quite possible that if equipment needs to be replaced before the early adoption phase reaches its anticipated end (and expected volume of usage), that the initial investment and payback calculations for some of the new technology may prove to have been somewhat inaccurate.
Given the likely volatility of the emerging equipment market, there are lots of questions that operators will therefore have.
-Who’s going to be responsible for maintenance and uptime?
-What’s the impact going to be on your site if the OEMs and Charge Point Operators are not set up for maintaining their equipment?
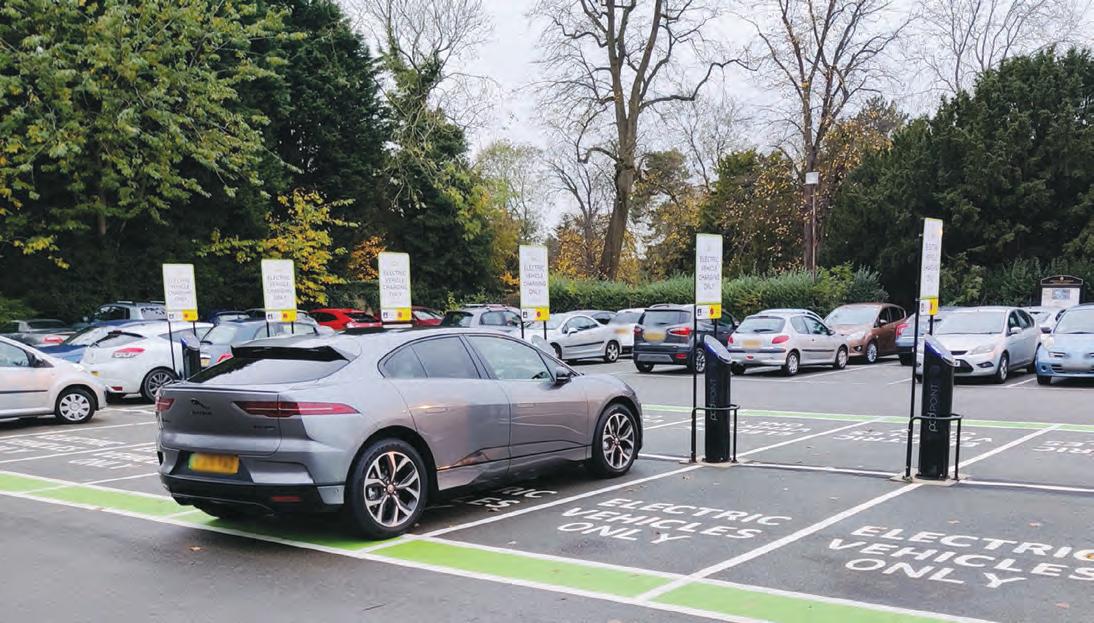
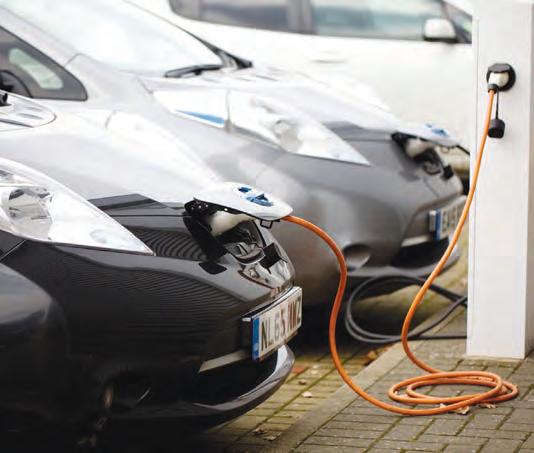
-Who suffers the consequences of downtime – is this covered in your contracts? How do you manage your customer perception? And protect your brand?
-When is the best time to enter the market in the innovation and adoption lifecycle?
Solutions
Whilst these early challenges are affecting the reliability of the networks being run by new entrants to the vehicle fuelling market, these challenges do of course offer opportunities for progressive and experienced operators and retailers, who are well versed in delivering a convenient and reliable customer offering.
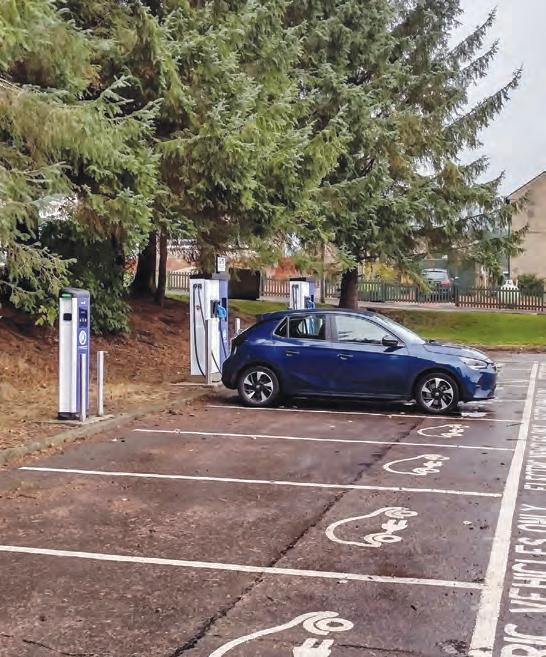
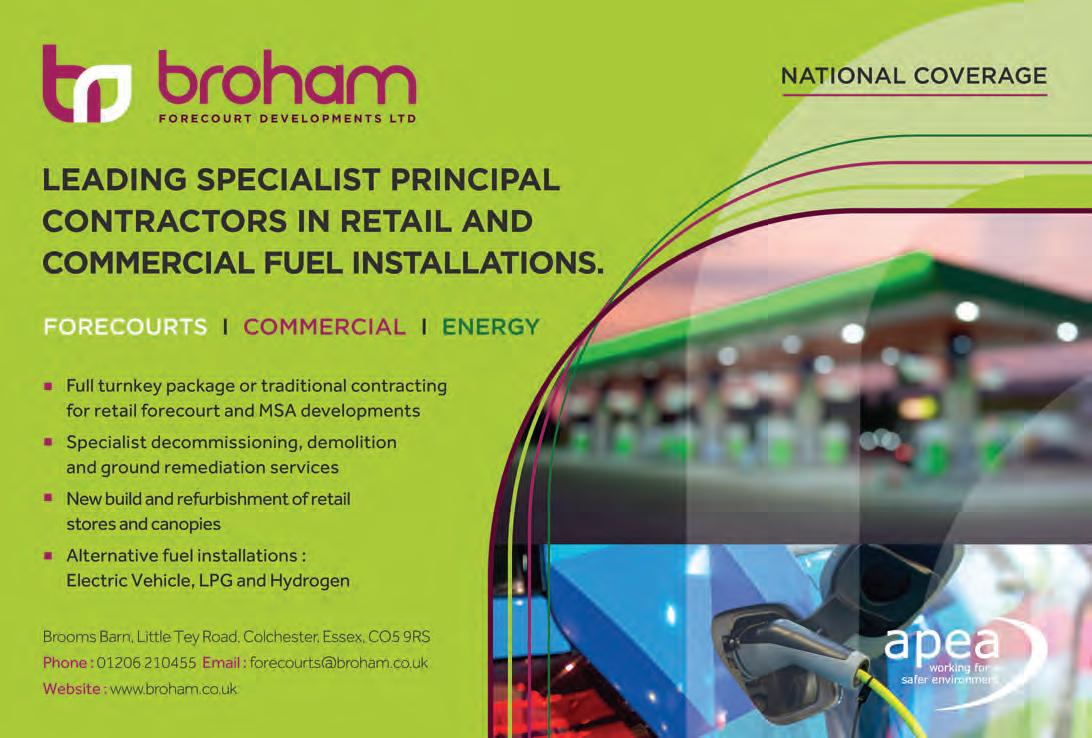
The factors that influence the success of a maintenance management regime are well versed, and Evenlode Roadside has extensive and lengthy experience of delivering for operators, including over 3,000 roadside retail sites in multiple countries. Our people are all very experienced in the roadside sector having worked directly for, and delivering bottom line value to, operators. We have a proven approach to delivering an operator focused wrap-around service, which goes beyond a reliance on systems and technology applications, to deliver excellence across multiple service lines and equipment times, including in other complex industry sectors, inclusive of:
-Workflow optimisation
-Supply chain selection & performance
-Commercial controls and sustained cost savings across capex and opex
-And a focus on delighted customers
Please see www.evenloderoadside.com for more information and examples of what we can help you to achieve. We have also produced a “How-To Guide to Maintenance” which is exclusively available to Operators.